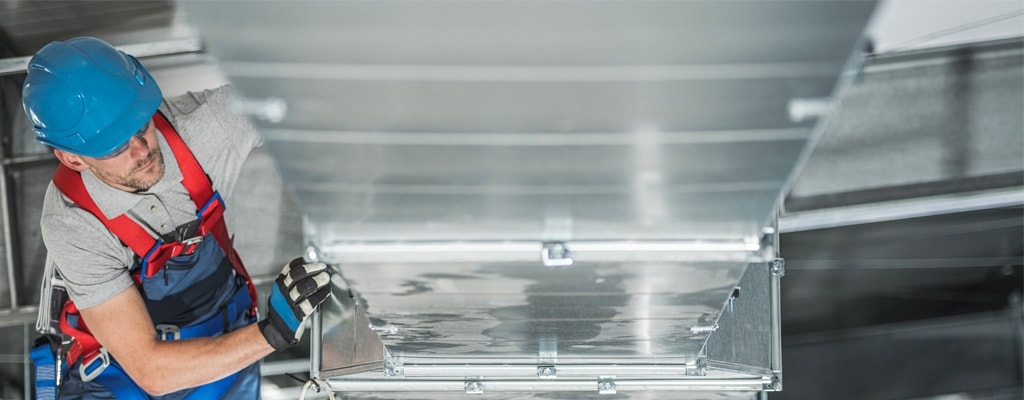
White Paper
Piezoresistive vs Advanced Thermal Sensor Technology
Sensor technology comparison for HVAC applications
Heating, ventilation, and air conditioning (HVAC) equipment designers are facing mounting challenges to create much more accurate systems that consume far less energy. These challenges are most acute in the commercial market where air handling systems play a major role in HVAC design. Variable air volume (VAV) systems are the industry standard for distributing heated and cooled air to office and commercial spaces. This equipment employs differential pressure sensors that control the air delivered through the HVAC system, plus measure pressure in the flow duct.
In HVAC environments, pressure is an important physical value, and its measurement is a critical task. The electronic sensors that perform the measurement work are extremely accurate and reliable even in the smallest pressure ranges. These differential pressure sensors operate at only a few millibars (few inches of water column) to measure volumetric air flow. Unlike relative and absolute pressure sensors, differential pressure sensors measure the delta between two pressures — and therefore have two separate pressure connections.
Sensors make HVAC systems more efficient by measuring air flow and pressure for effective air distribution. Their critical role means selecting the correct sensor is essential to ensure maximum HVAC system performance and occupant comfort.
This paper focuses on the two technologies that have proven their worth for differential pressure measurement in HVAC applications: piezoresistive (diaphragm-based) sensors and thermal (flow-based) sensors; both technologies have strengths and weaknesses.

The Role of Sensors in VAV Systems
A VAV system is a common HVAC application and provides design engineers a way to zone large areas of workspace in commercial buildings for heating and cooling. VAV systems consist of a sheet metal box with a damper and controls. An actuator connects to the box’s controller and modulates the damper position, which allows different amounts of airflow into the zone based on programmed inputs and variables such as air flow and temperature.
The air that is supplied to the VAV box is provided by a large air handler and central ductwork. When the VAV box is in cooling mode, the damper will modulate to a fully open position since air conditioning requires higher air flow. Heating requires less air flow so the damper will modulate to a minimum position.
The air handler’s blower fan must modulate to vary the air flow depending on demand. The VAV box has a sensor inside to measure air flow. The air flow and temperature variables control damper position based on temperature and cubic-feet-per-minute (CFM) demands. An additional sensor inside the main supply duct measures air pressure. There is a pressure set point inside the control program for the air handler. The air handler’s controls will ramp the blower up and down depending on the duct pressure to maintain the set point in the program.
Diaphragm vs Flow Based Technology
Piezoresistive (Diaphragm-Based) Technology
When High Linearity Is Essential
Piezoresistive differential pressure sensors consist of thin silicon diaphragms in which resistors are embedded as a Wheatstone bridge. If there are differences in pressure, the diaphragm pushes through, and distortion occurs. The semiconductor resistors arranged in the measuring bridge react to these mechanical stresses with the so-called piezoresistive effect. In other words, the resistances of the resistors change, the electrical voltages change, and a pressure proportional measuring signal is triggered.
For years, piezoresistive sensor technology has been perceived as the low-risk option for HVAC applications. Air handling systems are dusty places and piezoresistive sensors do not have a flow channel, so dust will not hinder its performance. The technology has high sensitivity and is suitable for applications requiring a measurement range of 1 millibar (0.5 inches of water column) to 10 bar. Piezoresistive sensors have high linear signal-pressure characteristics and excellent overall accuracy, and they come in very small sizes for compact applications.
Traditional Thermal (Flow-Based) Technology
Traditional thermal differential pressure sensors incorporate a heating element positioned between two temperature-sensitive resistors (one upstream, one downstream). If there is a pressure difference (differential pressure) between the two sensor connections, gas flows through the sensor and the temperature profile moves in the direction of the downstream resistor. This results in a temperature difference between the two resistors, which in turn triggers an output signal proportional to the gas flow; the measure of the underlying differential pressure.
To measure volumetric flow, the flow-based sensor must be connected to the main flow channel via tubes. Sometimes, additional filters are used in the bypass channel to protect the sensor against dust, humidity, or bacterial contamination. However, any pneumatic element between the main flow channel and the bypass represents additional flow resistance that leads to a pressure drop. The pressure sensor will therefore measure a differential pressure which is lower than the one caused by the flow restricting element in the main channel. The result is an inaccurate measurement of the volumetric flow rate in the main flow channel. The higher the flow impedance of the connecting tubes and additional filters compared to the sensor, the more dominant is this effect.
For conventional flow-based differential pressure sensors, a maximum allowed tube length to the sensor is recommended, or respectively, a correction formula is given to compensate for the pressure drop in the bypass. Traditionally, tube lengths were kept short to prevent adding pneumatic impedance that would alter the sensor’s calibration and cause it to return an incorrect value.
In the past, these issues have caused concern among OEM designers about the construction of thermal flow-through technology. However, an advanced generation of thermal sensors is quickly alleviating those concerns.
Advanced Thermal Technology
An Excellent Choice for Ultra-Low Pressure Measurement
Advanced thermal differential pressure sensors are based on a silicon chip only about 4 mm2 (0.006 in2) in size. The sensors incorporate innovative MEMS technology that integrates a micro-flow channel within the silicon sensor chip. Advanced thermal sensors can measure ultra-low air or gas pressures from 0.25 millibar (0.1 inches of water column) full scale (FS).
Advanced thermal technology features high dynamic ranges and high sensitivities for very low pressures, especially around zero. The sensors offer digital signal conditioning for calibration, temperature compensation, and amplification. They can be optimized to different application requirements depending on whether a high sensitivity, high dynamic range, or linear output signal is needed. Probably the most significant advantage of advanced thermal technology it’s zero-offset accuracy.
Typically, differential pressure is created in the system by an air velocity probe that converts air velocity into delta-P. These probes use the physical principle of a classic Pitot tube. The probe may be constructed in the shape of a stick with multiple orifices or as a bent metal tube distributed across the duct cross section (also with multiple orifices).
The integration of the miniaturized flow channel with the sensor chip enables the advanced thermal pressure sensor to achieve very high pneumatic impedances up to 20,000 to 50,000 Pa/(ml/s). This performance is up to 100 times higher than comparable traditional thermal (flow-based) sensors. The miniaturized flow channel reduces the gas flow through the sensor to an absolute minimum and offers unique application advantages in dusty and humid environments as well as when using long connection tubes or filters.
With TE’s advanced thermal technology, the bypass flow is almost exclusively determined by the very high flow impedance of the sensor device. The influences of additional components with resistance to flow can be neglected. That means advanced thermal differential pressure sensors can be used with long tubing, filters, or other pneumatic elements without losing their calibration. Even if these elements change their resistance over time, there will be no negative influence on the measurement accuracy. This capability gives the engineer more flexibility in designing the air handling system.
The Problem of Dust
In the past, when traditional thermal pressure sensors were used for volumetric flow measurement in dirty HVAC environments, dust particles might reach the inside of the sensor and the walls of the inner flow channel. This condition would increase the sensor’s pneumatic impedance, decrease the output signal, and cause a loss of calibration. In a worst-case scenario, the flow channel might be completely blocked, resulting in sensor failure.
TE’s advanced thermal pressure sensors are highly immune to the issues noted above for applications in dusty environments. Due to the very high pneumatic impedance, the air flow through the sensor is extremely small. This means that the total amount of dust-laden gas that streams through the bypass channel for volumetric flow measurement is reduced to an absolute minimum compared to traditional thermal pressure sensors. Additionally, the flow velocity is greatly reduced so the remaining dust quantity will settle in the bypass before it reaches the sensor input.
As a result, the sensor does not require a dust filter. Its ability to eliminate the ingress of dust provides highly accurate measurements and very long sensor lifetimes.
Traditional thermal sensors must be installed in a specific orientation while the advanced thermal sensors eliminate this problem of position dependency by allowing device installation in any desired orientation. Now, the air handling system designer can place the device in any position, greatly improving design flexibility. The advanced thermal sensor also enhances design flexibility through the accuracy of its flow channel. In traditional thermal sensors, the flow channel and gas flow are determined by the geometry of their plastic housings. These housings are not manufactured as accurately as semiconductor technology, resulting in lower stability. In contrast, the advanced sensor’s micro-flow channel is defined at the die level. This permits construction of the sensor housing for high design flexibility, extremely low production tolerances, much smaller and more stable packaging, and reduced manufacturing costs.

Conclusion
In selecting a differential pressure sensor, the decision comes down to the application’s requirements. One sensor may have to function under changing temperatures, another will be exposed to strong vibration, while a third must cope with dusty air. No matter how demanding the conditions, there is always a pressure sensor that will meet the application requirements for accuracy and reliability over a long period of time. Both sensor technologies behave quite similarly in practice due to their high degree of sensitivity and accuracy. Each technology has its own strengths and advantages. The piezoresistive sensor is impressive thanks to its high linearity. The advanced thermal sensor eliminates the drawbacks of traditional flow technology and reacts particularly sensitively around the zero point of the measurement. Choosing the correct technology will result in an HVAC air handling system that delivers maximum occupant comfort at the lowest possible energy cost.
