In-Process Micron-Level-Accuracy Thickness Inspection Platform
ABSTRACT
Thickness, the key manufacturing parameter, directly influences the performance of the plaque. Due to lack of in-process inspection method, the current offline inspection method need to perform the destructive inspection, moreover, the cost of product changeover is about hundreds of US dollars each time. We innovated one thickness inspection platform to perform the in-process, micron-level-accuracy, contact less and dynamic inspection.
PROBLEM STATEMENT
Plaque is one kind of important product and is one fundamental component for many chip products. The plaque product consists of three layers. Two metal layers and one Positive Temperature Coefficient (PTC) layer are laminated together. Fig. 1 shows the illustration of the plaque manufacturing process. Thickness, which directly influences the performance, is the most important parameter of the plaque quality. If the thickness of final product is not within the specification, there is no rework opportunity, and we have to drop all the product.
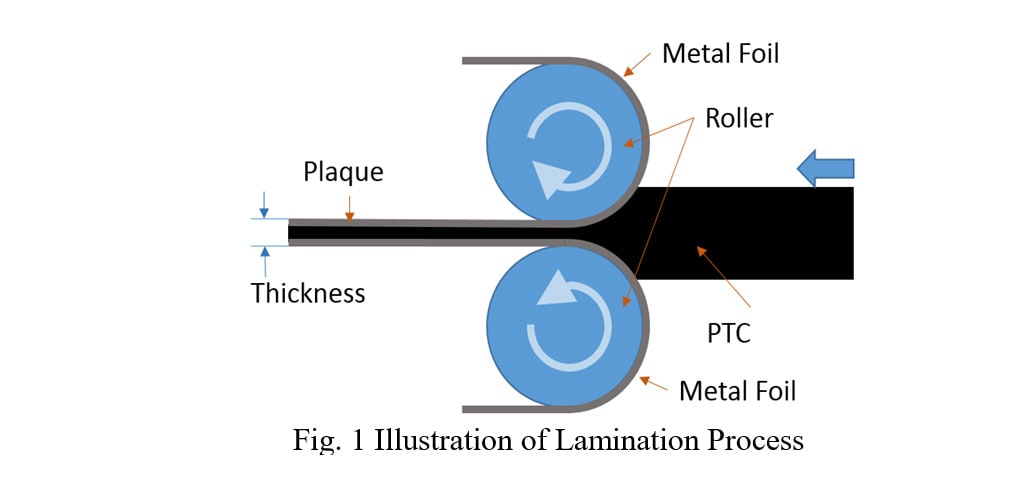
In real production, the operator needs to adjust the distance between two rollers to control the thickness. The issue occurs during changeover. There are 9 part numbers with different thicknesses in the whole product family. And normally, it’s changed frequently, twice change-over per day.
The cost of changeover is very high. Without no online thickness inspection equipment, current changeover is based on off line inspection. The operator needs to firstly produce some samples, stop the machine, cut down the samples to perform the off line destructive inspection. The operator will repeat the process until they get good result. This is micron-level adjustment by hands which is very challenging and time-consuming.
In order to develop one on-line plaque thickness inspection system, three challenges should be taken consideration:
1) Micron-level-accuracy
2) Dynamic Inspection
3) Contactless Inspection
We innovated one thickness inspection platform to perform the in-process, micron-level-accuracy, contactless and dynamic inspection. We used the laser technology to perform the contactless inspection. To achieve the accuracy requirement, we performed one DoE to understand what the key influential factor for dynamic inspection is, and how to achieve the accuracy requirement for dynamic inspection. The platform passed the GR&R qualification.
METHODS AND RESULTS
Platform Overview
Fig. 4 shows the platform overview: the purple part represents the plaque. Two laser sensors, one upward and one downward, are mounted in one C-shape sensor installation frame and work together to perform the thickness inspection. Two shafts driven by the servo motor to shifts the C-shape frame back and forth. The shafts are installed in the marble frame to improve the stability. Marble is usually used as the base for the high-precision measurement system, such as coordination measurement machine. Below the marble frame is the electrical control cabinet.
When production is running, the plaque goes through the inspection station continuously in the X direction, and the upward laser sensor and downward laser sensor are moving in the Y direction to form one zigzag?? inspection trajectory shown in the bottom of Fig. 4.
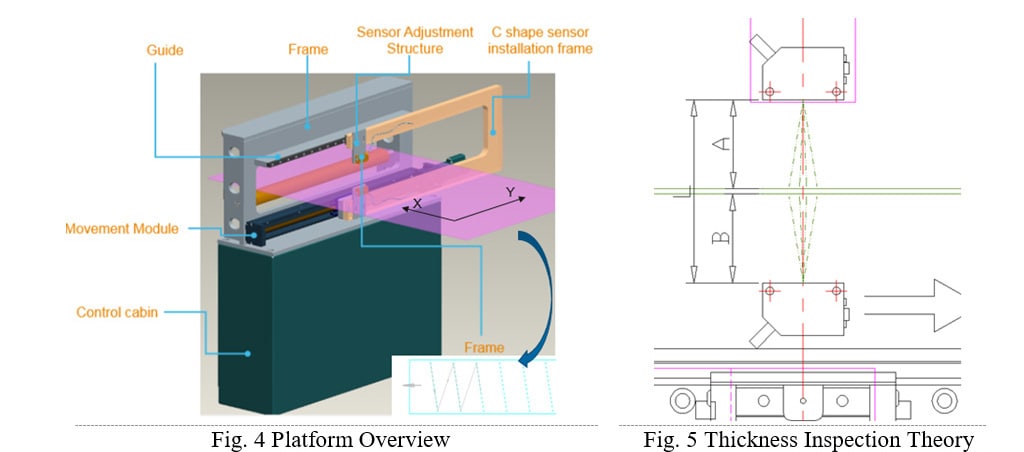
The thickness inspection theory based on two sensors is shown in Fig. 5. Two laser sensors are used to inspect the distance from the sensors to the object. Let L to be the distance between two sensors, and A is the distance measured by upward laser sensor, B is the distance measured by downward laser sensor, the thickness of the plaque is
Thickness = L-A-B (1)
DoE Platform Based on Robot
To apply equation (1) in the real production, we need to make sure the inspection environment fully satisfies the condition of equation (1) during inspection. However, the real manufacturing environment has kinds of noise resources, including the error of the laser sensor, plaque vibration, plaque rotation, sensor movement and product movement, so we can hardly directly apply equation (1).
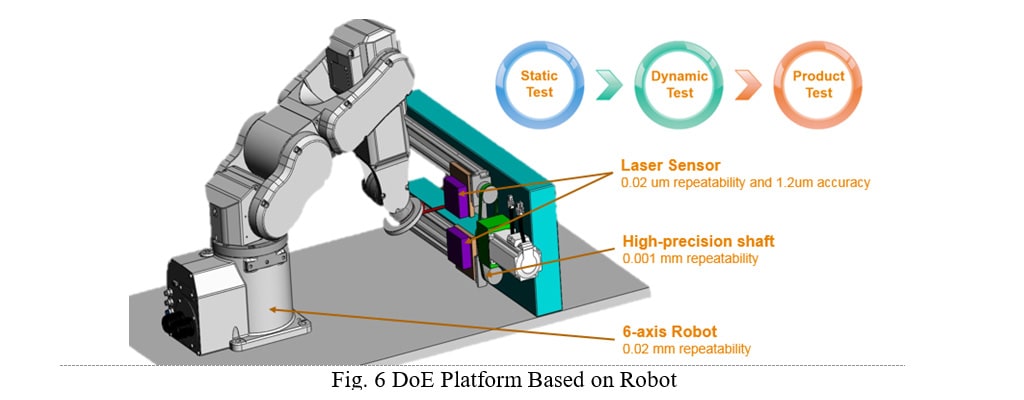
We built up one DoE platform to analyze the influence of each influential factor. The DoE platform is based on one 6-axis robot with 0.02 mm repeatability. The gripper at the end effector can manipulate the plaque sample to simulate vibration, rotation, vertical movement, and horizontal movement. Besides the robot, as one key device, the high precision laser sensor has 0.02 microns’ repeatability, and 1.2 microns’ accuracy. The shaft to horizontally shift the sensor is with 0.001 mm repeatability. The intrinsic accuracy of the system is good enough. However, the intrinsic accuracy could be decreased by the outer environment, so the purpose of this DoE is to find the way to reduce the influence and recover the intrinsic accuracy.
We performed three kinds of experiments:
- Static Test: both product and sensor are static to test the repeatability and accuracy of the system. This is the intrinsic accuracy of the system
- Dynamic Test: test the influence of product rotation, vibration, product horizontal movement and product vertical movement and find out the relationship between each factor and accuracy
- Real Product Test: GR&R qualification on real product
DISCUSSION AND KEY POINTS
This paper introduces the innovations about one in-process micron level accuracy inspection platform, including the overview of the platform, the contactless laser technology, the calibration algorithm for dynamic inspection, the software and GR&R qualification. We in detail explained how to improve the system accuracy based on the DoE experiment and scientific analysis.
The advantages of this platform can be featured as in-process, micron-level-accuracy, dynamic and contactless. The inspection platform is directly integrated into the manufacturing production line, and the real-time inspection data are shown to the operator. The inspection accuracy of the system achieved the micron-level and passed the GR&R qualification. The dynamic inspection is able to cover a range of product. And based on laser technology, we achieved the contactless inspection.
This platform has the potential to extend to another kinds of products which needs the thickness inspection, at the same time, this platform can be improved to cover faster production line and wider product.
In-Process Micron-Level-Accuracy Thickness Inspection Platform
ABSTRACT
Thickness, the key manufacturing parameter, directly influences the performance of the plaque. Due to lack of in-process inspection method, the current offline inspection method need to perform the destructive inspection, moreover, the cost of product changeover is about hundreds of US dollars each time. We innovated one thickness inspection platform to perform the in-process, micron-level-accuracy, contact less and dynamic inspection.
PROBLEM STATEMENT
Plaque is one kind of important product and is one fundamental component for many chip products. The plaque product consists of three layers. Two metal layers and one Positive Temperature Coefficient (PTC) layer are laminated together. Fig. 1 shows the illustration of the plaque manufacturing process. Thickness, which directly influences the performance, is the most important parameter of the plaque quality. If the thickness of final product is not within the specification, there is no rework opportunity, and we have to drop all the product.
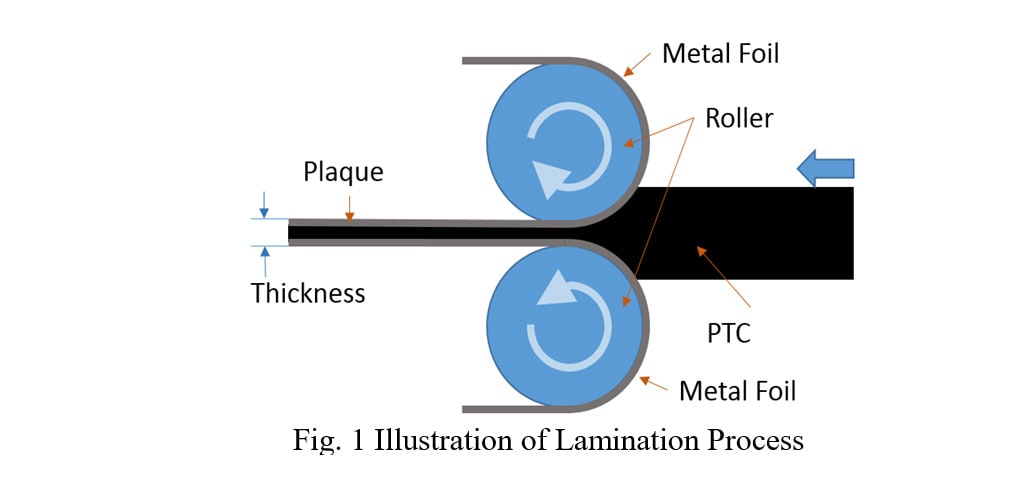
In real production, the operator needs to adjust the distance between two rollers to control the thickness. The issue occurs during changeover. There are 9 part numbers with different thicknesses in the whole product family. And normally, it’s changed frequently, twice change-over per day.
The cost of changeover is very high. Without no online thickness inspection equipment, current changeover is based on off line inspection. The operator needs to firstly produce some samples, stop the machine, cut down the samples to perform the off line destructive inspection. The operator will repeat the process until they get good result. This is micron-level adjustment by hands which is very challenging and time-consuming.
In order to develop one on-line plaque thickness inspection system, three challenges should be taken consideration:
1) Micron-level-accuracy
2) Dynamic Inspection
3) Contactless Inspection
We innovated one thickness inspection platform to perform the in-process, micron-level-accuracy, contactless and dynamic inspection. We used the laser technology to perform the contactless inspection. To achieve the accuracy requirement, we performed one DoE to understand what the key influential factor for dynamic inspection is, and how to achieve the accuracy requirement for dynamic inspection. The platform passed the GR&R qualification.
METHODS AND RESULTS
Platform Overview
Fig. 4 shows the platform overview: the purple part represents the plaque. Two laser sensors, one upward and one downward, are mounted in one C-shape sensor installation frame and work together to perform the thickness inspection. Two shafts driven by the servo motor to shifts the C-shape frame back and forth. The shafts are installed in the marble frame to improve the stability. Marble is usually used as the base for the high-precision measurement system, such as coordination measurement machine. Below the marble frame is the electrical control cabinet.
When production is running, the plaque goes through the inspection station continuously in the X direction, and the upward laser sensor and downward laser sensor are moving in the Y direction to form one zigzag?? inspection trajectory shown in the bottom of Fig. 4.
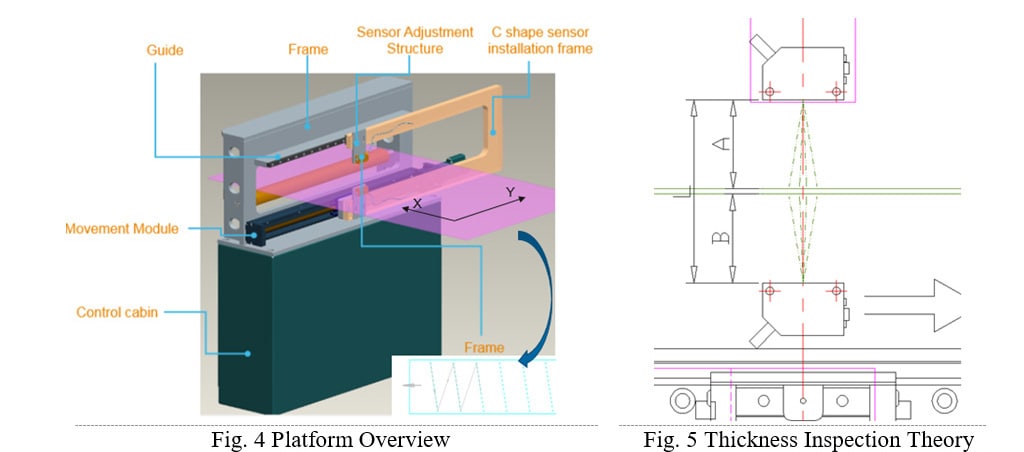
The thickness inspection theory based on two sensors is shown in Fig. 5. Two laser sensors are used to inspect the distance from the sensors to the object. Let L to be the distance between two sensors, and A is the distance measured by upward laser sensor, B is the distance measured by downward laser sensor, the thickness of the plaque is
Thickness = L-A-B (1)
DoE Platform Based on Robot
To apply equation (1) in the real production, we need to make sure the inspection environment fully satisfies the condition of equation (1) during inspection. However, the real manufacturing environment has kinds of noise resources, including the error of the laser sensor, plaque vibration, plaque rotation, sensor movement and product movement, so we can hardly directly apply equation (1).
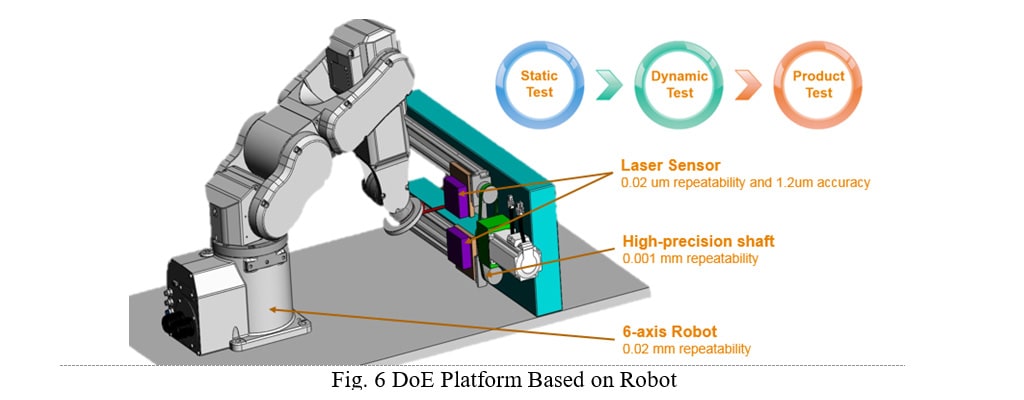
We built up one DoE platform to analyze the influence of each influential factor. The DoE platform is based on one 6-axis robot with 0.02 mm repeatability. The gripper at the end effector can manipulate the plaque sample to simulate vibration, rotation, vertical movement, and horizontal movement. Besides the robot, as one key device, the high precision laser sensor has 0.02 microns’ repeatability, and 1.2 microns’ accuracy. The shaft to horizontally shift the sensor is with 0.001 mm repeatability. The intrinsic accuracy of the system is good enough. However, the intrinsic accuracy could be decreased by the outer environment, so the purpose of this DoE is to find the way to reduce the influence and recover the intrinsic accuracy.
We performed three kinds of experiments:
- Static Test: both product and sensor are static to test the repeatability and accuracy of the system. This is the intrinsic accuracy of the system
- Dynamic Test: test the influence of product rotation, vibration, product horizontal movement and product vertical movement and find out the relationship between each factor and accuracy
- Real Product Test: GR&R qualification on real product
DISCUSSION AND KEY POINTS
This paper introduces the innovations about one in-process micron level accuracy inspection platform, including the overview of the platform, the contactless laser technology, the calibration algorithm for dynamic inspection, the software and GR&R qualification. We in detail explained how to improve the system accuracy based on the DoE experiment and scientific analysis.
The advantages of this platform can be featured as in-process, micron-level-accuracy, dynamic and contactless. The inspection platform is directly integrated into the manufacturing production line, and the real-time inspection data are shown to the operator. The inspection accuracy of the system achieved the micron-level and passed the GR&R qualification. The dynamic inspection is able to cover a range of product. And based on laser technology, we achieved the contactless inspection.
This platform has the potential to extend to another kinds of products which needs the thickness inspection, at the same time, this platform can be improved to cover faster production line and wider product.