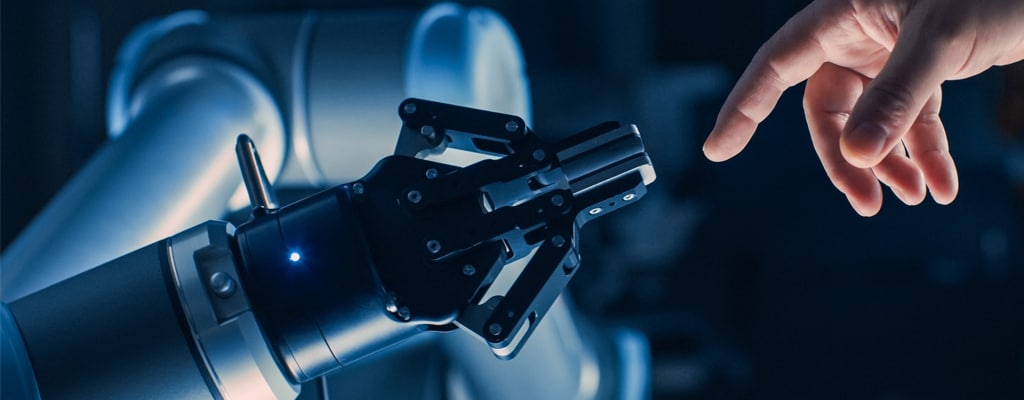
Application
Optimizing Sensing in Collaborative Robots
Sensors enable safe human to robot interactions as they collect data that enables successful and safe operation which allows an increase in efficiency, productivity, and safety. Learn about the TE sensors engineered for robotic applications.
Sensors are critical for the monitoring and control of industrial and medical robots and robotic systems. Sensors are utilized in several areas to help monitor and control the movement of the robot as well as to monitor the surrounding environment and key operational parameters to help ensure efficient, productive, and safe operation of the robot. With the evolution of robotic technologies and trends, the use of sensors to support these robots has proliferated as sensors help to increase the efficiency, productivity, and safety of these robots. As robotic technology and automation continue to advance, sensors will continue to be the basis for the critical data needed for these systems. Sensors are used in robotics for accurate monitoring of system components to help facilitate predictive and preventative maintenance, as well as, enabling the safe and efficient operation of robots. Major sensor technologies that are used to address these markets and applications include torque, force, optical, position, and temperature.
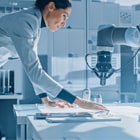

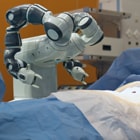
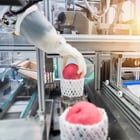

Industrial Robots
With the evolution of Industry 4.0 technologies and trends, the use of interactive robotics, their automation and control systems and the sensors used to support these industrial collaborative robots have become commonplace as businesses look to increase efficiency, productivity, and profitability. As the need for industrial robotic technology and automation continues to advance, sensing technology will continue to be the foundation for data and information that will help transform manufacturing floors into connected, cost-effective, and reliable facilities.
Sensors are an integral component of today’s sophisticated collaborative robots or cobots and are used in a variety of ways to monitor and control them and to ensure that they are operating safely, efficiently, and with the needed precision on the manufacturing floor of leading companies. Sensors are used not only to monitor and control the precise movements of the robot but, sensors are also used to monitor critical components of the robot to prevent system failures and even allow for predictive or preventative maintenance that maximizes uptime and productivity.
These cobots are intended to interact with and assist human workers as opposed to being standalone automated equipment with little to no human interaction. Cobots in manufacturing environments can also handle complex or dangerous tasks that humans either cannot complete or cannot perform safely. As safety requirements for collaborative robots have been developed and expanded, sensors have been used to help cobots achieve these functional safety requirements.
TE Connectivity offers a variety of sensors used in industrial robots and cobots, including torque, force, position, temperature, and optical sensors. These sensing technologies are used in a variety of ways to monitor and control the cobot and to ensure safe operation alongside employees. Torque sensors measure the mechanical torque at the rotational joint on a cobot that detects fault or overload conditions and prevents injuries and potential cobot failures. In addition, sensors can be used in equipment such as light curtains, which stop machines when people enter critical areas and APDs can act as artificial eyes in laser scanners. Sensors can also be used to monitor a robot's surroundings for object detection and to monitor load capacity as well as grip forces that help to ensure safe, reliable, and efficient operation in the workplace. In the modern workplace, sensors are a critical component for industrial robots and cobots because they enable humans and machines to interact safely and with greater efficiency and effectiveness.

Surgical Robots
As medical technology advances, the use of surgical robots has become more prevalent due to the many benefits that robotic surgery offers. Robot-assisted surgery is the use of surgical robots to help perform minimally invasive medical procedures which offer patients shorter hospital stays, reduced pain, faster recovery time, and smaller incision sites.
Surgical robots aid with surgeon fatigue during long and complex operations. In comparison to traditional surgery methods where surgeons needed to make large incisions to accommodate larger tools and their hands, robotic surgery allows surgeons to accomplish the same complex tasks using very precise and reliable robotic technology.
Robotic surgery works by utilizing a surgeon console where the surgeon can control and manipulate the mechanical arms of the surgical robot by looking through a camera that magnifies the surgical site. The surgeon’s hand, wrist, and finger movements are mimicked through the console controls and carried over to the robotic arms to perform the surgery in a very concise manner, with smaller incisions while still offering the surgeon full control. The highly precise functionality and repeatability needed for robotic surgery would not be possible without the use of high-performing sensors.
Sensors are the foundation of robot-assisted surgery since they collect the data needed to perform the precise robotic arm movements needed to carry out successful surgeries. Surgical robots use torque, force, and position sensors to accomplish these data measurements. Torque sensors in surgical robots are used for safety and to improve the manual arm positioning of the surgical robot. Additionally, force sensors are used in surgical robots for haptic feedback to improve a sense of touch for controls to the surgeon while position sensors are used in surgical robots for table and console positioning. As robotic surgery becomes more commonplace in hospitals around the world, sensors will continue to be the foundational components needed for robotic surgical systems.

AMR & AGV
As the need to increase the efficiency of operations within industrial factory applications grows, warehouses and other industrial facilities have been using mobile robots to improve efficiency, productivity, and profitability while also maintaining safety standards for employees. Autonomous mobile robots (AMRs) and automated guided vehicles (AGVs) are used to help transport loads or goods to support manufacturing production lines and are ideal for facilities with well-defined and relatively fixed operations.
AGVs are used to help transport loads of materials to support the manufacturing production line and are ideal for facilities needing more fixed operations. The sensors that are used in AGVs are optical sensing for LIDAR navigation to confirm personnel safety and avoid collisions. Force and tilt sensing are required to prevent material overloading of the mobile robot, and cable-actuated position sensor for forklift height.
More recently, AMRs, or autonomous mobile robots, have been introduced into the industry. AMRs, like AGVs, follow along a predefined, designated path. However, AMRs can sense an obstacle and move around it to complete their designated task while AGVs, on the other hand, can sense an obstacle but just stop and wait until the obstacle is removed, requiring user intervention. AGVs and AMRs can both be used for dynamic activities such as transporting materials, loading, or unloading goods as well as shelving or de-shelving inventory.
To enable this more intelligent and complex functionality, the sensors used for AMRs may include:
- Position sensing to confirm distance for nearby workers and objects and for navigating the surrounding environment
- Optical sensing for learning their environments to choose the most effective path
- Force and tilt sensing for interacting with the material loads.
Whether an AGV or AMR is deployed within your facility, sensors for mobile robots provide the foundational data to confirm these technologies are working correctly, safely, and as efficiently as possible.

LEARN MORE
Robotics Solutions
TOPICS | RESOURCES |
---|---|
Improving Safety Performance in Cobots | Trend Page |
The Role of Sensors in the Evolution of Robotics | Trend Page |
Five Ways Torque Sensors Help Improve Safety Performance in Cobots | Infographic |
Sensors for Surgical Robots | Solution Sheet |
Sensors for Industrial Collaborative Robots | Solution Sheet |
Sensors for AGVs & AMRs | Solution Sheet |
Improving Safety and Functionality in Cobots | Podcast |