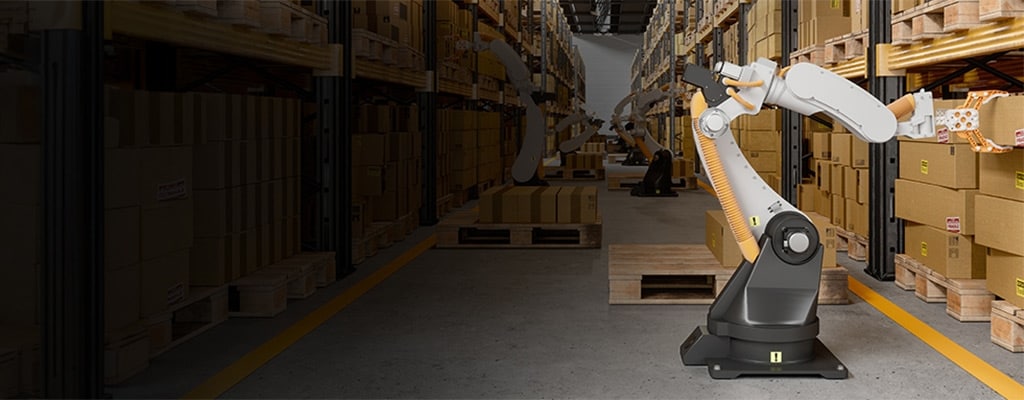
More Power and Miniaturization Demand in Warehouse Automation
Miniaturization is a key trend in industrial connectivity. TE solutions offer reliable signal, high-data, and high-power capabilities in compact, rugged designs for top performance.
Solving power density challenges as demand grows for miniaturized components
Miniaturization is a megatrend in every aspect of industrial and nonindustrial connectivity. If we look closer at this technology, it is possible to split any kind of connection into data, signal, and power for different applications and markets. Each of these areas has special requirements for the components used. For example, in warehouse automation applications, new technologies in communication and power transmission need to be combined with advancements in miniaturization. In smart warehouses, two new major applications are automated guided vehicles (AGVs) and autonomous mobile robots (AMRs). AGVs are guided by external measures like magnetic tape on the floor. AMRs have additional sensors like laser scanners integrated for navigation. Both have a similar challenge: combining high-performance features into very limited vehicle space for all the electronics. But what exactly does this mean for an application and the associated development challenges? Let us take a deeper look.
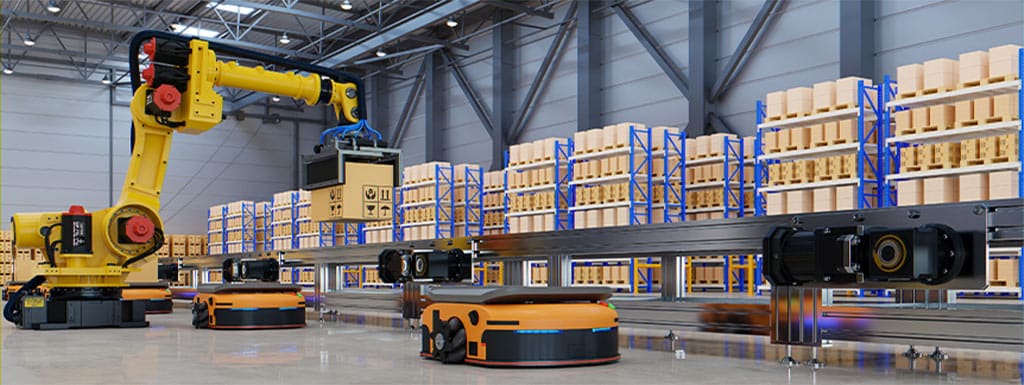
MINIATURIZATION AS A MAJOR REQUIREMENT
Manufacturers want a high-reliable signal, high data, and high-power capabilities in the smallest possible package. To meet these demands, miniaturized components are critical — and they must deliver more performance and reliability than ever before. The increasing number of AGVs and AMRs used in automated warehouses and logistics is driving the general requirement for miniaturization in addition to the demand for improvements in power density, performance, and communication reliability. These vehicles are very compact and include several subsystems with electronics, which all have to fit into a very limited space. Both mobile solutions require numerous sensors for navigation, a battery and charging management system, and internal motors and electronics, resulting in the need for hundreds of components for operation and connectivity. In order for all of these technical solutions to meet more powerful application requirements, numerous technical hurdles must be overcome. Density is one key factor to help solve these challenges. It starts with board connectors, which fulfill the internal device power needs and the signal transmission. Since equipment manufacturers look for smaller solutions that can provide more high-speed connectivity and power, engineers are turning to new
technologies to help solve the challenges of maximizing power density in a miniaturized vehicle. To help meet the need for miniaturized components that combine reliable signal and data transmission with high power possibilities, TE Connectivity offers a broad portfolio of components. The following provides insight into the TE connector portfolio, which is highly specific and detailed and therefore fits the requirement of design freedom.
The package or envelope needs to get smaller, but it can’t lack power or functionality. In fact, designers want it to perform even better than the bigger version.
- Manuel Rüter,
- Senior Principal of Standardization and Consortia for Industrial Solutions at TE Connectivity

WHAT IS DRIVING THIS DEMAND AND HOW ARE POWER DENSITY CHALLENGES SOLVED?
Miniaturization is not a new trend in the power supply world, but demand for miniaturized components is growing as operations look for ways to improve efficiency, reduce costs, and streamline warehouse operations. AGVs and AMRs are built on different platforms from small to large. They require scalable components that still provide the necessary power and connectivity across a wide range — often with even more functionality and better performance and reliability.
Engineers have worked for years to improve power density. The limits on power density depend on the specific product involved. In addition to material limitations and approbation specifications, there are physical limitations, such as contact technology and thickness to meet transmission requirements, clearance and creepage distances, printed circuit board (PCB) workability, and different
manufacturing options.
The material choice depends on air and creepage distances, with optimal contact technology realized using smaller future-ready board connectivity for reliable applications and robust environments. In AGVs and AMRs, high-volume loading, wireless data transmission for fleet control, and sensor/actuator supply all require power transmissions of more than 10 A. Precise movement of heavy weights with intelligent transactions in smaller vehicles is the trend. In this environment, temperature resistance, mechanical robustness, and electrical shielding functionality are critical. A good example is the impact of environmental influences on data and signal transmission and how shielding helps solve this problem. Higher data rates of several thousand megabits need a high transmission frequency. The higher the transmission frequency, the more susceptible the data connection is to interference. Shielding helps deliver reliable integrity, reflecting a successful example of engineering expertise.

What is power density?
Power density is the measure of how much power can be processed within a given space. It is quantified as the amount of power processed per unit of volume in units of watts per cubic meter (W/m3). Reducing the size of components in a robot or AGV is an important consideration to help improve power density.
RELIABILITY REQUIREMENTS FOR MINIATURIZED SOLUTIONS
As more components are miniaturized in automated warehouses, another challenge to keep in mind is the issue of maintenance and repairs. As parts become smaller and components become packaged more closely together, it can be difficult to access the connection or component that requires maintenance or repair inside AMRs and AGVs. One failed connector may require the disassembly of the entire warehouse system — and warehouses cannot afford any prolonged downtime for maintenance. Products are tested against standards generally applied when products are used in harsh environments. Engineer requirements are based on customer and market requirements, standards, and the physical demands of the materials and the environment. Sometimes customer requirements above the market standards (such as VW75174, formerly LV214 for automotive applications) are necessary. In those cases, higher expectations for robustness or material durability must be met to avoid failures. This makes it especially important for manufacturers to invest in miniaturized components that are not only high-performing but also extremely reliable and durable. Examples of TE solutions that meet these demands for industrial applications include ERNI MaxiBridge, MicroBridge, MiniBridge, and SMC connectors. Original equipment manufacturers (OEMs) can count on TE for product consistency, quality, precision, and reliability, and can depend on TE’s team of experts for engineering know-how and support.
