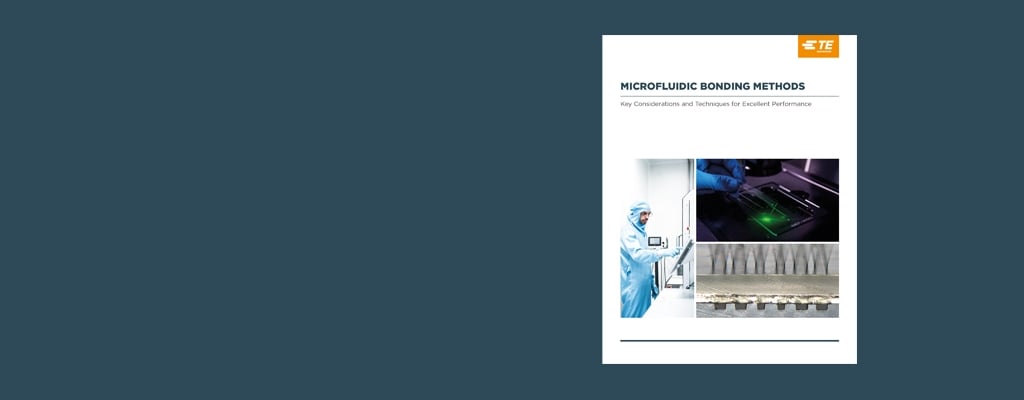
Will It Scale? Best Practices for Prototyping Thermoplastic Microfluidic IVD Devices
You can create beautiful 3D computer models and virtual simulations all day long but to get a true picture of fluid dynamics and functional performance you need to step into the physical world and create a real device. Many IVD cartridge developers run into challenges selecting the right materials and methods for creating prototypes of their microfluidic assays, and those early decisions can have a profound impact on how well your design will perform and transfer from prototype > low volume > bridge > high volume commercial production. In this article we will highlight which prototyping methods make sense in specific situations, and also discuss the pros and cons of various methods, materials and bonding techniques.
Important lessons learned from IVD microfluidic prototyping
In the very early stages, many designers start fabricating with silicone or 3D printing using commercially available pumps and valves – a typical and reasonable approach for demonstrating proof of concept and fundraising. The next step is to get to next level of reproducibility and accuracy with a more developed design that might involve producing small lots (10-100 units).
By creating small lots of prototypes with different features (e.g., geometries, channel designs and surface chemistries) the fluidic behavior of the microfluidic channel “circuits” can be tested and further refined.
Proven Expertise, From Concept to Market
Here are some important insights to be gained from making high quality microfluidic prototypes
- Are there stagnation or resistance points in the design?
- Are bubbles forming in the channels?
- What is the best material for this design based on the application and performance requirements?
- Do we need to change the design to match the preferred material?
- Are the materials, manufacturing and assembly processes the most cost-effective for commercial volumes?
Methods of thermoplastic prototyping
There is no standardized approach providing the right combination of materials and processes to use for your prototyping project. There are so many different combinations of substrate materials and methods that when the complexities of reagent properties are added, you really need an expert on your side to make sense of the options and the development path. The table below provides a summary of the basic pros and cons of different microfluidic prototyping methods. Each has its respective trade-offs, and the best choice depends on the application and stage of development. This is not a comprehensive list, but it does include the most commonly applied techniques.
Method | Appropriate Scale (units provided) | Pros | Cons |
---|---|---|---|
3D Printing | Generally, less than 20 |
|
|
Soft Lithography (aka PDMS casting) |
Generally less than 20 |
|
|
Hot Embossing | Generally 10-50 |
|
|
Micromachining(Mechanical or Laser) | Generally 10 - 100 pieces |
|
|
Micro Injection Molding (with modular tool) | Hundreds to thousands of pieces |
|
|
Choosing materials for your microfluidic disposable cartridge
The method you choose to make your prototypes is important but your chosen materials will dictate compatibility and scalability. This is an often-misunderstood area vital to the performance of your device. Several different areas need to be considered when choosing materials.
- Chemical compatibility and surface chemistries - Need to make sure your cartridge substrate is compatible with your chosen reagents and targets (e.g. contact angle, biocompatibility)
- Heat resistance and thermal properties
- Optical properties - transparency, auto fluorescence
- Mechanical strength and/or flexibility
- Bonding or assembly options
- Cost to scale/speed of production
Polydimethylsiloxane (PDMS) is one of the most commonly used thermoplastic substrates for making microfluidic cartridge prototypes and for limited scale production. While PDMS is affordable, easy to fabricate, able to hold tight tolerances and is compatible with many liquids, it can be somewhat limiting the technique does not provide the required draft angle in the microchannels needed separation in any scale injection molding process. PDMS is an acceptable “bridge” material but it is not suitable for high volume manufacturing – the goal is to get to the final material as quickly as possible.
Therefore, other polymers representing final commercial product material can be considered for prototype injection molding and micromachining as well. The following polymers are commonly used for injection molding, micro machining prototypes and commercial products. They tend to have good mechanical and optical properties and are easier to fabricate than materials such as silicon or glass:
- Polymethyl Methacrylate (PMMA)
- Cyclic Olefin / Copolymers (COC, COP)
- Polycarbonate (PC)
Holding it all together: selecting the right bonding
Your device design is solid. You have tested the microfluidic circuit and individual components. You have considered all material options. And you know which methods of prototyping makes the most sense for your disposable cartridge. Have you considered how it all the pieces literally come together?
Bonding is an often-underestimated discipline of microfluidic prototyping but it is vital to the performance of your device. There are several possible bonding
methods used in microfluidic cartridges including pressure-sensitive and resin adhesives, thermal fusion, ultrasonic, laser welding and solvents. We won’t go into the specifics of which ones are best for specific applications.
To be aware that the choices depends on MANY factors including
- Materials chosen (types, thickness, colors)
- Physical tolerances (deformation, flatness, warpage, adhesive incursion)
- Dimensional requirements (channel sealing, 3D features)
- Detection method (optical, electrical)
- Surface roughness (channel surface, welding / bonding surface)
- Operating conditions (temperature, pressure)
- Thermal performance (thermal conductivity, glass transition temp)
- Alignment (layer to layer, channel pattern)
- Process compatibility (reagent loading, surface treatment)
- Biocompatibility (chemical inert, medical grade, outgassing, leaching)
Test components first, then the assembly
Prototypes also offer and excellent way to test valves, switches, micromixers, reaction chambers and other features as parts of a fluidic “circuit”, using a methodology known as “couponing.” If you initially test fully integrated designs and assemblies it can be very difficult to isolate the root cause of problems identified, i.e., substrate material, bonding techniques or method used to fabricate your assay. By testing prototypes of the valves, mixers and chambers separately you can isolate the functionality of flow mixing and switching first, and then add other features such as chambers. This is less risky than assembling all components and testing them together at one time before you commit to a more advanced design. You don't want to end up creating a final prototype mold and then make small changes thereafter as this is far more costly than testing components separately and can slow your time to market.
Investing in high quality prototypes will save you money and time
It is very tempting to take shortcuts and move into production quickly to satisfy overly ambitious and optimistic timelines. However, based on 20+ years of microfluidic design and manufacturing experience, we have seen those shortcuts turn into production fiascos that significantly hamper the commercialization efforts of the company. Having a partner that understands microfluidic thermoplastic material options, surface chemistry, bonding techniques and fluid dynamics is critical. Understanding how all of those things affect your final design and transition to full scale manufacturing is even more vital.
Choosing experienced partner may seem more expensive initially but is less costly overall when you consider that fewer iterations will be needed and your time to market may be shorter.
Learn More About TE’s Microfluidic Design and Prototyping Expertise