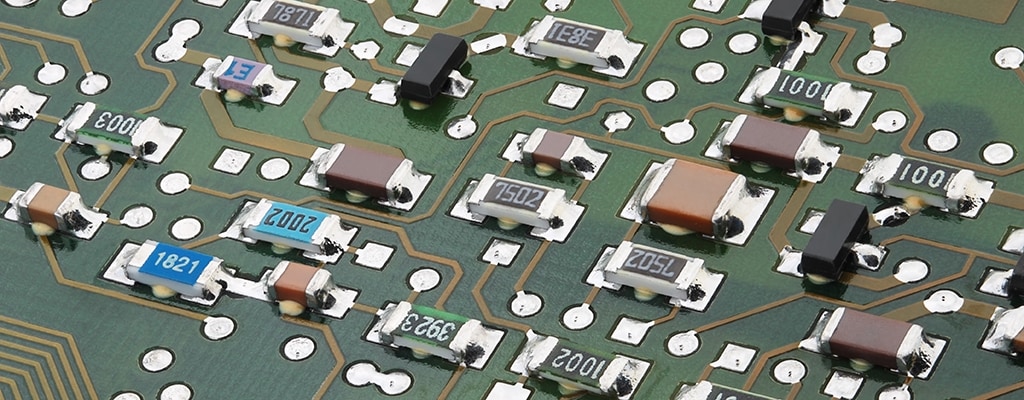
Product Insight
Save space and reduce weight
Today’s thin film resistors offer more variations and finer tolerances, enabling designers to achieve more accuracy in resistance value with fewer components. Learn how our thin film SMD resistors can help you save crucial space on the printed circuit board while reducing device weight.
The surface mount chip resistor is a crucial component in printed circuit board (PCB) design. This is partly because of the ease of installing these small, leadless devices during high-volume production. Selecting the right surface mount resistor – known also as an SMD resistor – for your product begins with understanding the differences between thin film (engineered for precision) and thick film (engineered for power) technologies.
When classifying SMD resistors, resistance in ohms tells only part of the story. The first consideration is understanding differences in the manufacturing processes and simple rules of thermodynamics – more massive objects can handle more energy than smaller ones.
In a thin film resistor, the conductive layer is deposited in a vacuum process, known as sputtering. This creates a thin but uniform layer, only fractions of a micron thick, over a ceramic substrate. Once in place, this layer is then subjected to a photo or laser etching process. This determines the accuracy of the resistance value with a very fine tolerance, which can be as low as 0.01%. This precision is what makes the thin film resistor so useful.
In contrast, the thick film resistor is manufactured with the conductive layer printed onto the ceramic substrate, in the form of a paste. This layer can be as much as a thousand times thicker than the one on a thin film resistor. This thickness offers performance advantages in handling high-power applications, and it is also significantly less expensive to manufacturer than thin film resistors. However, the advantages it gives in power capacity also make it less predictable and precise, with tolerances as high as 5%.
New materials and improved manufacturing processes are enabling manufacturers to increase the capabilities of thin film resistors without sacrificing precision.
Innovation in materials and more controllable production processes are enabling manufacturers to develop thin film resistors that deliver a combination of precision and power performance, with accuracy previously unavailable. For example, because resistors are classified using the E-series, an E12 would see every "decade" of values (for example, between 1 and 10 Ohms) divided into 12 steps. To achieve the right resistance value, designers had to combine a fixed resistor with a small variable resistor called a trimmer potentiometer.
Today’s thin film resistors offer more variations and finer tolerances, with the current norm being the E96 series. As a result, designers can achieve much more accuracy in resistance value, which means they no longer need a trimmer – and because they require fewer components, they can save crucial space on PCBs, which also helps reduce device weight.
When choosing a resistor, it is also crucial to understand stability under changing temperature conditions. As with any electrical circuit, the characteristics of a resistor will change according to temperature, and any change in temperature will affect performance. All resistors are engineered to convert unwanted electrical energy into heat; all resistors also have a Temperature Coefficient of Resistance (TCR) which describes how the resistance will vary with a change in temperature. The thin film process creates a component that offers a very stable resistance which varies little with changes in temperature.
Because thick film resistors will handle more energy than thin film resistors, these offer improved performance in high power applications – but at the cost of reduced precision. Here lies the compromise, in the current technologies. But this is changing. New materials and improved manufacturing processes are enabling manufacturers to increase the capabilities of thin film resistors without sacrificing precision. One example is the standard 0805 format resistor of the RN73 family, which has a power rating of 0.1W; a similar-sized resistor from the newer RP73P family has a power rating of 0.25W. This increase in performance is mirrored across all sizes of resistors.
SMD Resistors in Select Applications
It is important to understand the value that this increase in power capacity can bring to a design, which can be described as the power to size ratio. Improving the power to size ratio can bring benefits to the designer in different ways. For example, it might allow the entire design to use smaller components, making equipment smaller and lighter. However, as an alternative, greater power to size ratio could allow the designer to improve the performance of existing devices by employing higher power. In either example, the increased capability offered by the latest thin film resistors is offering designers new opportunities.
An interesting use of thin film resistors – in a harsh environment – can be found in the pharmaceutical industry. Manufacturing drugs requires exact measurements to ensure the correct proportions of ingredients are used. Because the velocity of production in this environment can be unforgiving for precision equipment, pharmaceutical companies need to prevent inaccuracies that can arise if the resistors within weighing machines do not exhibit the necessary stability under varying temperature. Under these conditions, the new generation of thin film resistors have been delivering both stability and precision.
While there will always be a place for thick film resistors in mass production applications, and in applications where power capacity is paramount, it is the advances in thin film technology that is enabling designers to achieve more precision and reliability in a wider variety of applications.
Find solutions now: