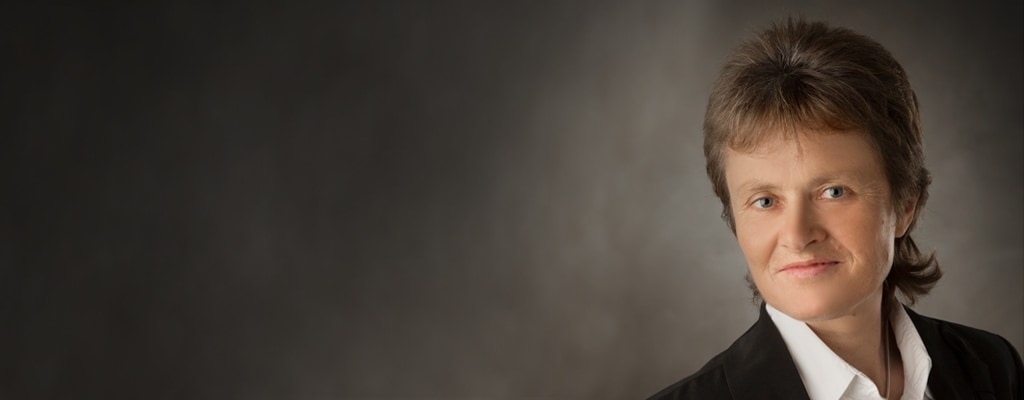
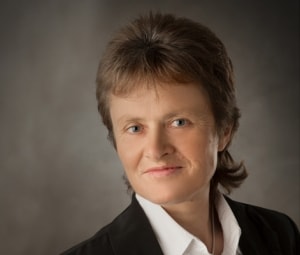
La réflexion latérale permet aux ingénieurs de résoudre des problèmes relatifs à des composants existants, en cherchant à remplacer ces derniers.
Isabell est motivée par les opportunités. Chaque problème est une opportunité d’apprendre, d’améliorer les processus et d’innover – et chaque problème appelle à la créativité. Titulaire d’un doctorat en métallurgie de l’Université de Stuttgart, Isabell passe ses journées à évaluer et à développer de nouveaux systèmes de matériaux et de revêtements qui améliorent la fiabilité des contacts et des bornes de connecteurs, ainsi que leur usage durable. Ses trente années d’expérience professionnelle dans les métaux, les surfaces et les technologies de placage lui permettent de comprendre quelles caractéristiques rendent les matériaux spéciaux et les subtilités de la production rentable des matériaux à l’aide de processus de fabrication durables. Pour Isabell, l’innovation commence par la compréhension de ce que le client veut, du fonctionnement d’une entreprise et de la façon dont elle développe un produit spécifique, jusqu’au contexte de conception, à l’historique des performances et au processus de production. Isabell aborde la résolution de problèmes par la pensée latérale, en « sortant des sentiers battus » et pas seulement en appliquant l’approche des cinq pourquoi. Cela lui permet de regarder au-delà des objets difficiles, de refuser l’ordre établi et de concevoir des manières entièrement nouvelles d’envisager un problème. Son agilité résiliente est affinée par sa passion pour les sports de compétition. Skieuse émérite ayant évolué au sein d’équipes juniors et nationales allemandes, Isabell considère que ses réussites sportives l’ont aidée à acquérir la persévérance, l’endurance et le dévouement nécessaires pour résoudre des problèmes difficiles et penser avec agilité lors du développement de solutions pour des matériaux avancés.
Quelles tendances technologiques observez-vous ?
La miniaturisation des composants électriques et électromécaniques, et l’augmentation de la puissance et des performances à moindre coût. Les forces du marché veulent plus de fonctions dans des espaces plus petits. Pour ce faire, il faut une densité de fonctionnalité ou de puissance plus élevée, des pièces miniaturisées et une réduction du poids.
En outre, la conception de matériaux et de revêtements pour des températures ambiantes et de pointe plus élevées offre une opportunité inestimable, afin d’éviter que des processus et des réactions imprévisibles des matériaux et des interfaces puissent produire des défaillances inconnues. Sur le marché actuel, ces tendances sont impossibles à suivre avec les solutions existantes en raison de la performance et de la disponibilité des matériaux et des processus ; outre de nouvelles solutions, des améliorations des matériaux et des processus standard sont nécessaires.
Quels sont les défis liés au développement de nouveaux matériaux pour des contacts miniaturisés ?
La miniaturisation rend les composants électroniques plus compacts et plus légers. La miniaturisation permet de réduire l’espace sur la carte ou un composant. D’autre part, cela implique des forces normales de contact réduites, des zones de contact plus petites, une augmentation de la distribution des contraintes locales lors de la formation de cette pièce, combinée à une sensibilité plus élevée aux matériaux zéro défaut. Les matériaux, surfaces et revêtements innovants, ainsi que les processus de production sont donc la clé du succès.
Pensez-y : de petits pores ou des vides – les inhomogénéités et les impuretés – dans un matériau peuvent entraîner la défaillance d’un composant, voire impliquer de graves conséquences. Pour éviter cela, vous devez vous concentrer sur les matériaux de base, en particulier les interfaces, les surfaces et les revêtements, afin de vous assurer que le matériau répond aux spécifications et à la fonctionnalité de durée de vie.
Vous devez également examiner attentivement la microstructure du matériau, en particulier sa taille de grain, ses limites de grain, ses précipitations et les interfaces entre le matériau de base et le revêtement. Ceci est crucial pour obtenir un matériau zéro défaut avec les propriétés de formage et de placage nécessaires.
Prenons un exemple : de petits vides dans l’interface, entre le matériau de base et le revêtement d’étain dans l’état initial, peuvent entraîner des problèmes plus tard à des températures élevées. Le délaminage des revêtements peut se produire dans de petites zones de contact fortement formées à mesure que le stress thermique augmente, comme dans le test de contrainte électrique. Pour éviter cela, nous utilisons des méthodes très spécifiques afin d’analyser les détails. Dans le cadre de cette enquête, nous surveillons et examinons de près les processus et les réactions chimiques dans les matériaux. Nous utilisons des équipements haute résolution tels que le FIB (= Focus Ion Beam) et la GDOES (= Glow Discharge Optical Emission Spectroskopy) pour comprendre l’interaction entre les composants individuels.
Quels sont les défis liés au développement d’entrées et de contacts de chargeur pour les applications de véhicules électriques ?
Dans la mesure où l’e-mobilité bouleverse notre cœur de métier comme jamais auparavant, nous examinons les exigences croissantes en matière de contacts de connecteurs concernant les cycles d’insertion pour les terminaux de chargeur ou les applications à haute température. Pour l’e-mobilité, nos conceptions doivent tenir compte d’exigences de cycle d’accouplement jusqu’à 10 000 à des connecteurs de charge ou des températures pouvant atteindre 180-200 °C aux points de contact.
Pour résoudre ce problème, nous développons des systèmes de revêtement et des procédés de placage capables de répondre aux nouvelles exigences. Cela nous oblige à approfondir notre recherche et à tenir compte de disciplines universitaires associées, en particulier de celles issues d’autres secteurs industriels et domaines de la science. Cela nous permet d’accélérer notre travail pendant la phase d’idéation, d’effectuer les premiers tests dans le cadre d’études de faisabilité en nous faisant une idée de ce qui pourrait – en principe – être réalisé. Nous voulons réussir dans le développement interfonctionnel, à l’aide d’innovations ouvertes et d’équipes agiles. Une infrastructure de R&D établie est très utile, en particulier lorsque les délais de mise sur le marché rapides et les pressions sur les coûts sont prioritaires.
Sur quoi travaille votre équipe pour mettre en place l’innovation technologique dans l’automobile ?
À l’heure actuelle, les marchés de l’automobile et de l’électronique sont dynamiques et en pleine transformation. Ce sont les entreprises qui s’efforcent actuellement d’optimiser la conception et les processus, de réduire les cycles de développement et de limiter les coûts qui réussiront. Il n’est pas possible de rivaliser avec les meilleurs sans adopter cette approche. Pour ce faire, il est nécessaire de renforcer la fiabilité de la chaîne d’approvisionnement, même avec de nouveaux fournisseurs, d’accélérer la mise sur le marché, de simplifier les processus et les produits, et de posséder une infrastructure de R&D axée sur la préparation de l’avenir. Ce dernier point est crucial pour de meilleures performances en termes de délai de mise sur le marché et de solidité opérationnelle.
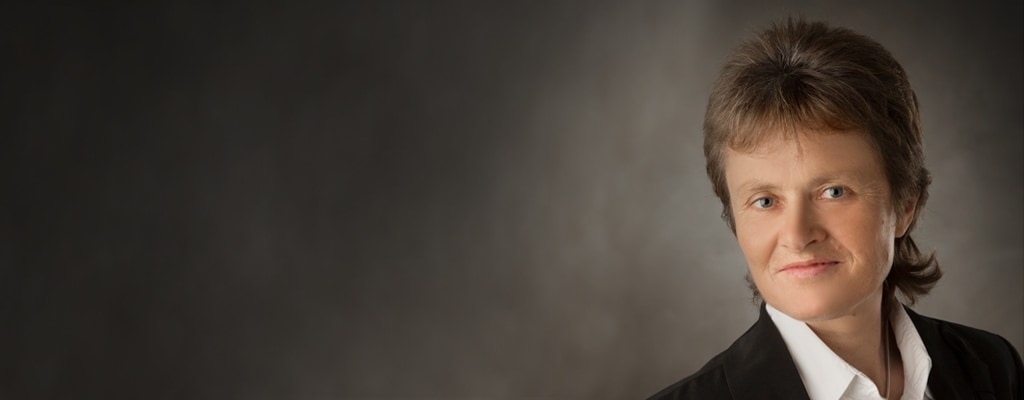
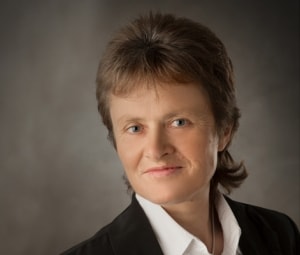
La réflexion latérale permet aux ingénieurs de résoudre des problèmes relatifs à des composants existants, en cherchant à remplacer ces derniers.
Isabell est motivée par les opportunités. Chaque problème est une opportunité d’apprendre, d’améliorer les processus et d’innover – et chaque problème appelle à la créativité. Titulaire d’un doctorat en métallurgie de l’Université de Stuttgart, Isabell passe ses journées à évaluer et à développer de nouveaux systèmes de matériaux et de revêtements qui améliorent la fiabilité des contacts et des bornes de connecteurs, ainsi que leur usage durable. Ses trente années d’expérience professionnelle dans les métaux, les surfaces et les technologies de placage lui permettent de comprendre quelles caractéristiques rendent les matériaux spéciaux et les subtilités de la production rentable des matériaux à l’aide de processus de fabrication durables. Pour Isabell, l’innovation commence par la compréhension de ce que le client veut, du fonctionnement d’une entreprise et de la façon dont elle développe un produit spécifique, jusqu’au contexte de conception, à l’historique des performances et au processus de production. Isabell aborde la résolution de problèmes par la pensée latérale, en « sortant des sentiers battus » et pas seulement en appliquant l’approche des cinq pourquoi. Cela lui permet de regarder au-delà des objets difficiles, de refuser l’ordre établi et de concevoir des manières entièrement nouvelles d’envisager un problème. Son agilité résiliente est affinée par sa passion pour les sports de compétition. Skieuse émérite ayant évolué au sein d’équipes juniors et nationales allemandes, Isabell considère que ses réussites sportives l’ont aidée à acquérir la persévérance, l’endurance et le dévouement nécessaires pour résoudre des problèmes difficiles et penser avec agilité lors du développement de solutions pour des matériaux avancés.
Quelles tendances technologiques observez-vous ?
La miniaturisation des composants électriques et électromécaniques, et l’augmentation de la puissance et des performances à moindre coût. Les forces du marché veulent plus de fonctions dans des espaces plus petits. Pour ce faire, il faut une densité de fonctionnalité ou de puissance plus élevée, des pièces miniaturisées et une réduction du poids.
En outre, la conception de matériaux et de revêtements pour des températures ambiantes et de pointe plus élevées offre une opportunité inestimable, afin d’éviter que des processus et des réactions imprévisibles des matériaux et des interfaces puissent produire des défaillances inconnues. Sur le marché actuel, ces tendances sont impossibles à suivre avec les solutions existantes en raison de la performance et de la disponibilité des matériaux et des processus ; outre de nouvelles solutions, des améliorations des matériaux et des processus standard sont nécessaires.
Quels sont les défis liés au développement de nouveaux matériaux pour des contacts miniaturisés ?
La miniaturisation rend les composants électroniques plus compacts et plus légers. La miniaturisation permet de réduire l’espace sur la carte ou un composant. D’autre part, cela implique des forces normales de contact réduites, des zones de contact plus petites, une augmentation de la distribution des contraintes locales lors de la formation de cette pièce, combinée à une sensibilité plus élevée aux matériaux zéro défaut. Les matériaux, surfaces et revêtements innovants, ainsi que les processus de production sont donc la clé du succès.
Pensez-y : de petits pores ou des vides – les inhomogénéités et les impuretés – dans un matériau peuvent entraîner la défaillance d’un composant, voire impliquer de graves conséquences. Pour éviter cela, vous devez vous concentrer sur les matériaux de base, en particulier les interfaces, les surfaces et les revêtements, afin de vous assurer que le matériau répond aux spécifications et à la fonctionnalité de durée de vie.
Vous devez également examiner attentivement la microstructure du matériau, en particulier sa taille de grain, ses limites de grain, ses précipitations et les interfaces entre le matériau de base et le revêtement. Ceci est crucial pour obtenir un matériau zéro défaut avec les propriétés de formage et de placage nécessaires.
Prenons un exemple : de petits vides dans l’interface, entre le matériau de base et le revêtement d’étain dans l’état initial, peuvent entraîner des problèmes plus tard à des températures élevées. Le délaminage des revêtements peut se produire dans de petites zones de contact fortement formées à mesure que le stress thermique augmente, comme dans le test de contrainte électrique. Pour éviter cela, nous utilisons des méthodes très spécifiques afin d’analyser les détails. Dans le cadre de cette enquête, nous surveillons et examinons de près les processus et les réactions chimiques dans les matériaux. Nous utilisons des équipements haute résolution tels que le FIB (= Focus Ion Beam) et la GDOES (= Glow Discharge Optical Emission Spectroskopy) pour comprendre l’interaction entre les composants individuels.
Quels sont les défis liés au développement d’entrées et de contacts de chargeur pour les applications de véhicules électriques ?
Dans la mesure où l’e-mobilité bouleverse notre cœur de métier comme jamais auparavant, nous examinons les exigences croissantes en matière de contacts de connecteurs concernant les cycles d’insertion pour les terminaux de chargeur ou les applications à haute température. Pour l’e-mobilité, nos conceptions doivent tenir compte d’exigences de cycle d’accouplement jusqu’à 10 000 à des connecteurs de charge ou des températures pouvant atteindre 180-200 °C aux points de contact.
Pour résoudre ce problème, nous développons des systèmes de revêtement et des procédés de placage capables de répondre aux nouvelles exigences. Cela nous oblige à approfondir notre recherche et à tenir compte de disciplines universitaires associées, en particulier de celles issues d’autres secteurs industriels et domaines de la science. Cela nous permet d’accélérer notre travail pendant la phase d’idéation, d’effectuer les premiers tests dans le cadre d’études de faisabilité en nous faisant une idée de ce qui pourrait – en principe – être réalisé. Nous voulons réussir dans le développement interfonctionnel, à l’aide d’innovations ouvertes et d’équipes agiles. Une infrastructure de R&D établie est très utile, en particulier lorsque les délais de mise sur le marché rapides et les pressions sur les coûts sont prioritaires.
Sur quoi travaille votre équipe pour mettre en place l’innovation technologique dans l’automobile ?
À l’heure actuelle, les marchés de l’automobile et de l’électronique sont dynamiques et en pleine transformation. Ce sont les entreprises qui s’efforcent actuellement d’optimiser la conception et les processus, de réduire les cycles de développement et de limiter les coûts qui réussiront. Il n’est pas possible de rivaliser avec les meilleurs sans adopter cette approche. Pour ce faire, il est nécessaire de renforcer la fiabilité de la chaîne d’approvisionnement, même avec de nouveaux fournisseurs, d’accélérer la mise sur le marché, de simplifier les processus et les produits, et de posséder une infrastructure de R&D axée sur la préparation de l’avenir. Ce dernier point est crucial pour de meilleures performances en termes de délai de mise sur le marché et de solidité opérationnelle.