Moulage rapide de joints élastomères fonctionnels pour environnements difficiles
RÉSUMÉ
Démonstration d’un processus rapide et peu coûteux de fabrication de prototypes ou de joints élastomères à mélange élevé et faible volume (HMLV) fonctionnels à l’aide de moules en plastique ou en polymère imprimés en 3D. Nous démontrons que ce processus simple et polyvalent est capable de mouler différents silicones et fluorosilicones de qualité de production TE, produisant une variété de conceptions de joints fonctionnels complexes avec des détails fins et une précision qui répondent aux exigences de nos clients.
ÉNONCÉ DU PROBLÈME
Les joints en élastomère sont des composants essentiels qui protègent les contacts électriques des connecteurs, des capteurs et des assemblages de câbles contre la corrosion provoquée par des facteurs environnementaux difficiles tels que l’humidité, les gaz, la poussière, les fluides et d’autres produits chimiques. TE propose une large gamme de conceptions de joints, y compris des joints faciaux, des joints familiaux, des joints de câble, des joints périphériques et des joints toriques. Les joints doivent répondre aux exigences strictes des clients pour différents connecteurs et composants électriques.
L’objectif de notre travail a été de développer un processus polyvalent, rapide et peu coûteux capable de produire des prototypes fonctionnels et/ou des joints HMLV commercialisables pouvant être fabriqués dans des matériaux de qualité de production allant du caoutchouc de silicone liquide (LSR) au caoutchouc à haute consistance (HCR) ou des fluorosilicones de gomme (consistance de l’argile ou du mastic) aux caoutchoucs et autres classes d’élastomères. De plus, les joints à rotation rapide doivent pouvoir être qualifiés selon les trois critères clés de forme, d’ajustement et de fonction (c’est-à-dire être capables de répondre aux exigences d’essais dimensionnels, d’assemblage et fonctionnels). Un processus rapide permet aux ingénieurs de TE de qualifier rapidement les joints tout en comparant différentes versions d’un modèle de joint dans différents matériaux aux propriétés variables (en termes de dureté, de compression, de résistance à la déchirure et de résistance chimique). Désormais, les ingénieurs de TE seront non seulement capables de fournir rapidement des pièces aux clients finaux, mais également d’obtenir des retours d’informations plus rapides lors des tests de produits.
Ici, nous démontrons l’utilisation de moules en polymère imprimés en 3D pour le moulage de joints élastomères capables d’atteindre les critères mentionnés ci-dessus. L’avantage de ce procédé réside dans sa simplicité et sa capacité d’adaptation pour une utilisation avec un mélange liquide comme avec un mélange pure gomme. Une variété de technologies d’impression basées sur la photopolymérisation, à savoir la stéréolithographie (SLA), le jet de monomère et le traitement numérique de la lumière (DLP) ainsi que différents matériaux de moule ont été évalués, et des combinaisons imprimante/matériau appropriées ont été identifiées pour l’impression de moules en polymère capables de résister à des conditions de moulage types (par exemple, température et pression élevées). À l’exception de TE, les fournisseurs continuent de développer de nouveaux matériaux de moules polymères destinés au moulage par injection de thermoplastiques [1].
Nous avons également comparé les performances fonctionnelles des joints fabriqués à partir de moules en polymère imprimés par rapport aux moules en métal, ainsi que les économies globales en termes de temps et d’argent pour les processus associées au prototypage à l’aide de moules en polymère. En outre, nous soulignons l’importance de choisir de façon appropriée le matériau de moule en polymère et les conditions de traitement du moule, ainsi que les capacités et les limites des moules en polymère.
MÉTHODES ET RÉSULTATS
Imprimantes et matériaux
Outre divers matériaux de résine commerciaux pour les moules d’impression, les principales imprimantes utilisées dans cette étude étaient des imprimantes SLA, DLP et à jet de monomère disponibles dans le commerce. Des aspects tels que les différences de qualité/précision d’impression, la rugosité de la surface du moule et la réutilisabilité du moule seront décrits dans la section de discussion.
Notre procédé est capable de mouler des qualités commerciales de silicone et de fluorosilicone tels que les caoutchoucs à haute consistance (HCR) (également connus sous le nom de gommes ou silicones solides) et les silicones liquides (par exemple, 2 parties). Les températures de durcissement de ces matériaux sont généralement > 150 ºC. Les qualités utilisées dans cette étude vont de 20 à 70 dureté shore (par exemple, shore A 20 ou shore A 50) et conviennent à une exposition environnementale difficile.
Description du processus
Préparation de moules en polymère : les moules à cavités multiples ont été conçus à l’aide de modèles de joints. Des modèles de moule CAO 3D (format .stl) ont été utilisés pour créer des fichiers de tranche ou de couche pour l’impression 3D. Après l’impression 3D, les moules (figure 1a) ont été nettoyés dans des solvants organiques pour éliminer tout excès de résine à la surface, une opération qui a été suivie d’un dégazage/traitement UV, puis d’un traitement thermique à une température appropriée afin de s’assurer que les moules imprimés étaient complètement durcis. Nous avons constaté qu’il était crucial de durcir à la chaleur les matériaux du moule en polymère à une température appropriée, faute de quoi le silicone risquait de ne pas durcir complètement dans le moule en polymère et de rester collant au toucher.
Moules métalliques : les moules en acier à 4 cavités ont été préparés par usinage conventionnel. Les moules en acier ont été nettoyés à l’aide d’un solvant de dégraissage, puis utilisés pour le moulage en silicone.
Processus de moulage : les moules en polymère imprimés en 3D ont été pulvérisés à l’aide d’un lubrifiant de moule à base de silicone avant le moulage. Nous avons étendu l’utilisation des moules imprimés en 3D à divers processus de moulage tels que l’injection, le transfert et le moulage par compression. Nous avons développé une expertise autour de la conception de moules en polymère, du réglage du processus de moulage et de l’utilisation d’approches non conventionnelles, compte tenu de la durée de vie limitée de l’outil liée à la résistance/conductivité thermique inférieure du matériau du moule en polymère. Le moulage avec un outil en polymère nécessiterait normalement un temps de cycle plus long, ce qui est acceptable à des fins de prototypage. Il est essentiel de choisir un matériau de moule approprié, car les moules en polymère ont été soumis à une température de 180 ºC lors de notre processus de durcissement des silicones.
Après le démoulage, les joints ont été déflashés manuellement, puis post-durcis pendant 10 à 120 minutes supplémentaires à 180 ºC afin de garantir un durcissement complet. Selon la durabilité des caractéristiques de base, les moules peuvent être à usage unique ou réutilisables. À titre de comparaison, les joints ont également été fabriqués à partir de moules métalliques usinés à l’aide d’un processus de moulage standard.
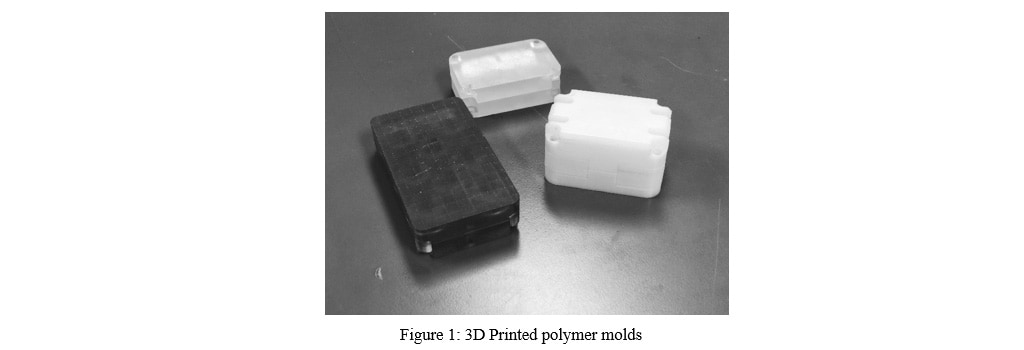
La figure 2a-g montre des exemples de joints moulés produits à l’aide de différents matériaux de moules en polymère imprimés dans une variété de formes, de tailles, de complexité et de types de matériaux en silicone. En utilisant des moules en polymère haute résolution, nous avons pu mouler de petits joints passants (figure 2b-c) avec un profil de trou complexe (diamètre du trou 1,01 mm, diamètre minimum dans le profil du trou 0,53 mm, épaisseur de paroi entre deux trous seulement 0,25 mm). La figure 2e-f montre un exemple de modèle de joint automobile dont les caractéristiques miniatures (épaisseur de paroi de 0,35 mm et trous de 0,69 mm de diamètre) ont été moulées avec succès. La figure 2g montre des exemples de joints automobiles périphériques et passants à fil unique.
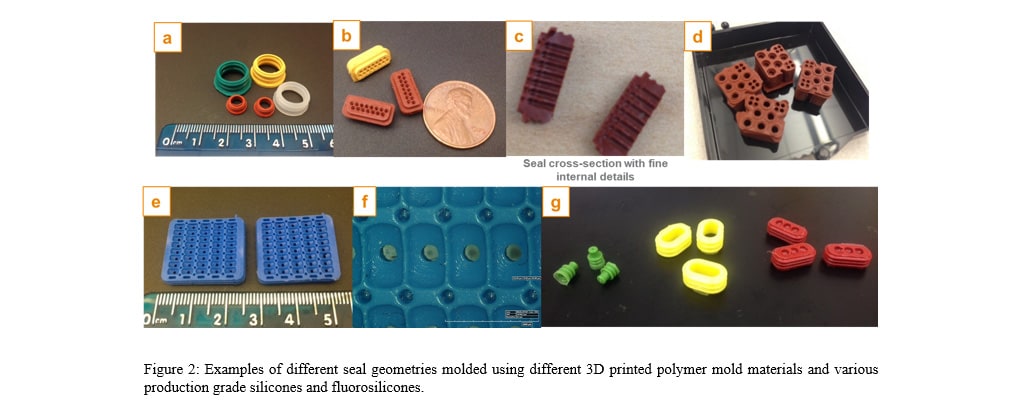
Résultats des tests fonctionnels d’étanchéité
Des joints fonctionnels (figure 2a) destinés à un client de l’aérospatiale, préparés à l’aide a) de moules en polymère imprimés en 3D et b) de moules en acier, ont été assemblés dans des bornes en aluminium, une opération suivie de l’insertion et du sertissage de fils (voir figure 3). Tous les joints ont satisfait aux exigences d’assemblage et de dimensions (les diamètres des dispositifs d’étanchéité étaient dans la tolérance autorisée de 0,1 mm). Les bornes assemblées ont été pressurisées à l’extrémité du fil et les fuites d’air testées sous l’eau à 1 bar et 2 bars. Des essais d’étanchéité ont été effectués avant et après que les pièces ont été soumises a) à 10 cycles de choc thermique (-65 ºC à 180 ºC) et b) au conditionnement de la température (180 ºC pendant 5 jours). Les exigences pour la qualification de la conception des joints du client étaient de réussir tous les tests à 1 bar sans fuite.
Des prototypes de joints ont été fabriqués pour différentes tailles de fils ; différents matériaux en silicone et en fluorosilicone ont été soumis à des tests d’étanchéité. Une qualité appropriée de matériau en silicone HCR a été présélectionnée sur la base d’une performance acceptable au test d’étanchéité. Les joints de moules en polymère ont réussi le test d’étanchéité pour toutes les tailles de fils avant et après le conditionnement par choc thermique, ce qui est un résultat très encourageant. En outre, tous les joints de moule en polymère pour fils plus gros (AWG 000, 00, 0A, 1, 2, 3) ont réussi le test d’étanchéité après le conditionnement de température de cinq jours à 180 ºC. Le processus de prototypage à base de moule polymère nous a également permis de qualifier rapidement des joints AWG 8 plus petits avec une conception modifiée (paroi plus épaisse atteignant 1,99 mm) qui ont réussi tous les tests d’étanchéité. Nos résultats montrent que les prototypes de joints des moules en polymère sont capables de répondre aux exigences fonctionnelles comme les moules en métal.
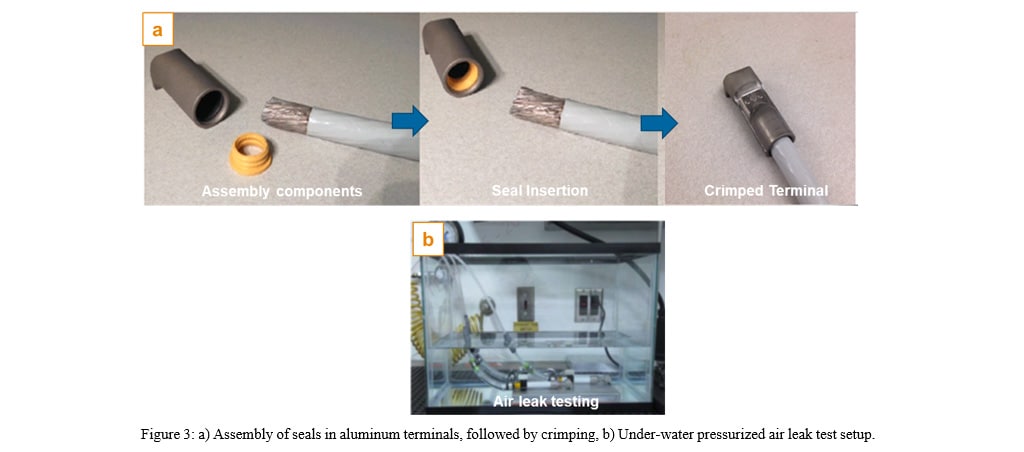
DISCUSSION ET POINTS CLÉS
Capacités et limites des moules en polymère imprimé en 3D
Le processus de moulage utilisant des moules polymères imprimés en 3D à plusieurs cavités peut produire des conceptions d’étanchéité complexes applicables à une large gamme de joints TE. Le nombre de cavités par moule en polymère peut varier de 1 pour les joints de plus grande taille à > 35 pour les joints de plus petite taille. Les imprimantes SLA utilisent généralement un laser afin de bénéficier d’une plus grande précision et d’une meilleure résolution (notez que la SLA peut également imprimer des angles ou des éléments saillants). Elles sont suivies de près par les imprimantes DLP qui utilisent la technologie de projection de lumière, puis par les imprimantes à jet monomère qui durcissent les photopolymères à l’aide de la lumière UV à large bande (notez que les coins aigus sont imprimés comme des arrondis). Le surdurcissement de la résine près des bords en raison de la pénétration de la lumière plus profondément que souhaité peut affecter la résolution et la précision de l’imprimante.
La rugosité de la surface des moules imprimés varie selon l’imprimante et le matériau imprimé. La rugosité de surface est inhérente à l’impression couche par couche (par exemple, épaisseur de couche 0,05 mm pour SLA) et à l’effet de marche d’escalier (surfaces construites en angle) qui peut être clairement vu dans l’image microscopique d’une caractéristique de moule SLA (figure 4a). La topographie de la surface du moule en polymère est clairement reproduite sur les joints moulés (figure 4b). La rugosité de la surface du joint moulé d’un moule en polymère est supérieure à celle des joints des moules métalliques (figure 4c). Une rugosité supplémentaire peut être présente dans les zones où le matériau de support est retiré de la surface du moule. La rugosité de surface supplémentaire peut ne pas être acceptable pour certaines applications d’étanchéité. Notez qu’il est également possible d’utiliser un outillage hybride, dans lequel des moules en polymère imprimés sont combinés avec des inserts de broches à noyau métallique pour les applications nécessitant des surfaces d’étanchéité de très faible rugosité.
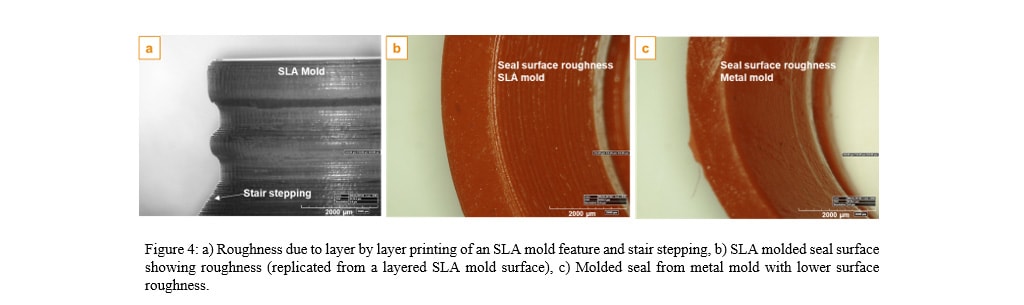
La durée de vie des moules en polymère est limitée, contrairement à celle des moules en métal. Les propriétés mécaniques des moules en polymère chutent considérablement aux températures les plus élevées, en particulier au-dessus de la température de fléchissement thermique [2]. La réutilisabilité des moules dépend fortement de la taille minimale des caractéristiques de base ainsi que des paramètres du processus de moulage tels que la température du moule, la pression, etc. Par exemple, les moules avec des caractéristiques de base plus grandes ont pu être utilisés plusieurs fois avant que le moule en polymère ne se fissure, tandis que les ruptures des moules présentant des caractéristiques de base plus petites réduisaient le nombre d’utilisations par moule. Pour les joints à géométrie extrêmement petite (impossible à réaliser par impression) et ou lorsqu’un grand nombre de pièces sont nécessaires, il peut être souhaitable d’utiliser un outillage hybride (c’est-à-dire un moule en polymère imprimé avec des inserts à broche à noyau métallique), plutôt que des moules en polymère sacrificiels ou à usage unique.
Coût/Temps
Nos coûts d’impression de moules internes étaient nettement inférieurs pour un moule à plusieurs cavités en polymère imprimé par rapport à un moule métallique usiné d’un fournisseur externe. Pour les moules imprimés, le temps total nécessaire entre la conception du moule et les joints moulés était de 2 semaines par rapport aux 8-10 semaines d’un fournisseur externe.
RÉCAPITULATIF
En résumé, nous avons développé une capacité unique de moulage rapide de joints dans différents silicones et fluorosilicones de qualité de production TE à l’aide de moules en polymère imprimés en 3D. Nous avons pu mettre en œuvre cette capacité grâce à notre expertise en conception de moules en polymère, à l’ajustement du processus de moulage et à l’utilisation d’approches non conventionnelles, compte tenu de la durée de vie limitée de l’outil liée à la résistance/conductivité thermique inférieure du matériau du moule en polymère. La capacité de passer rapidement de la conception CAO à la production de joints entièrement fonctionnels aide les ingénieurs TE à qualifier rapidement les joints en comparant différents modèles/matériaux de joints et à fournir rapidement des pièces aux clients finaux pour un retour d’information plus rapide des tests de produits. Notre processus de moulage rapide est un outil précieux qui permet de réaliser des économies considérables en termes de temps et d’argent pour la production de prototypes ou de joints HMLV entièrement fonctionnels qui répondent à toutes les exigences des clients.
REMERCIEMENTS
Les auteurs tiennent à remercier Martin Bayes, John Wasserbauer et Bob Zubrickie (Corporate Technology), Nicholas Ruffini, Kenneth Dowhower (A D et M) et Galen Martin (Automotive) pour leur précieux soutien dans le cadre de ce travail.
RÉFÉRENCES
[1] L. Zonder, N. Sella, « Precision Prototyping: The role of 3D printed molds in the injection molding industry », Stratasys.
[2] G. A. Mendible, « Applications of transient cooling simulations in injection molding », Ph.D. Thèse, Université du Massachusetts Lowell, 2015.
Moulage rapide de joints élastomères fonctionnels pour environnements difficiles
RÉSUMÉ
Démonstration d’un processus rapide et peu coûteux de fabrication de prototypes ou de joints élastomères à mélange élevé et faible volume (HMLV) fonctionnels à l’aide de moules en plastique ou en polymère imprimés en 3D. Nous démontrons que ce processus simple et polyvalent est capable de mouler différents silicones et fluorosilicones de qualité de production TE, produisant une variété de conceptions de joints fonctionnels complexes avec des détails fins et une précision qui répondent aux exigences de nos clients.
ÉNONCÉ DU PROBLÈME
Les joints en élastomère sont des composants essentiels qui protègent les contacts électriques des connecteurs, des capteurs et des assemblages de câbles contre la corrosion provoquée par des facteurs environnementaux difficiles tels que l’humidité, les gaz, la poussière, les fluides et d’autres produits chimiques. TE propose une large gamme de conceptions de joints, y compris des joints faciaux, des joints familiaux, des joints de câble, des joints périphériques et des joints toriques. Les joints doivent répondre aux exigences strictes des clients pour différents connecteurs et composants électriques.
L’objectif de notre travail a été de développer un processus polyvalent, rapide et peu coûteux capable de produire des prototypes fonctionnels et/ou des joints HMLV commercialisables pouvant être fabriqués dans des matériaux de qualité de production allant du caoutchouc de silicone liquide (LSR) au caoutchouc à haute consistance (HCR) ou des fluorosilicones de gomme (consistance de l’argile ou du mastic) aux caoutchoucs et autres classes d’élastomères. De plus, les joints à rotation rapide doivent pouvoir être qualifiés selon les trois critères clés de forme, d’ajustement et de fonction (c’est-à-dire être capables de répondre aux exigences d’essais dimensionnels, d’assemblage et fonctionnels). Un processus rapide permet aux ingénieurs de TE de qualifier rapidement les joints tout en comparant différentes versions d’un modèle de joint dans différents matériaux aux propriétés variables (en termes de dureté, de compression, de résistance à la déchirure et de résistance chimique). Désormais, les ingénieurs de TE seront non seulement capables de fournir rapidement des pièces aux clients finaux, mais également d’obtenir des retours d’informations plus rapides lors des tests de produits.
Ici, nous démontrons l’utilisation de moules en polymère imprimés en 3D pour le moulage de joints élastomères capables d’atteindre les critères mentionnés ci-dessus. L’avantage de ce procédé réside dans sa simplicité et sa capacité d’adaptation pour une utilisation avec un mélange liquide comme avec un mélange pure gomme. Une variété de technologies d’impression basées sur la photopolymérisation, à savoir la stéréolithographie (SLA), le jet de monomère et le traitement numérique de la lumière (DLP) ainsi que différents matériaux de moule ont été évalués, et des combinaisons imprimante/matériau appropriées ont été identifiées pour l’impression de moules en polymère capables de résister à des conditions de moulage types (par exemple, température et pression élevées). À l’exception de TE, les fournisseurs continuent de développer de nouveaux matériaux de moules polymères destinés au moulage par injection de thermoplastiques [1].
Nous avons également comparé les performances fonctionnelles des joints fabriqués à partir de moules en polymère imprimés par rapport aux moules en métal, ainsi que les économies globales en termes de temps et d’argent pour les processus associées au prototypage à l’aide de moules en polymère. En outre, nous soulignons l’importance de choisir de façon appropriée le matériau de moule en polymère et les conditions de traitement du moule, ainsi que les capacités et les limites des moules en polymère.
MÉTHODES ET RÉSULTATS
Imprimantes et matériaux
Outre divers matériaux de résine commerciaux pour les moules d’impression, les principales imprimantes utilisées dans cette étude étaient des imprimantes SLA, DLP et à jet de monomère disponibles dans le commerce. Des aspects tels que les différences de qualité/précision d’impression, la rugosité de la surface du moule et la réutilisabilité du moule seront décrits dans la section de discussion.
Notre procédé est capable de mouler des qualités commerciales de silicone et de fluorosilicone tels que les caoutchoucs à haute consistance (HCR) (également connus sous le nom de gommes ou silicones solides) et les silicones liquides (par exemple, 2 parties). Les températures de durcissement de ces matériaux sont généralement > 150 ºC. Les qualités utilisées dans cette étude vont de 20 à 70 dureté shore (par exemple, shore A 20 ou shore A 50) et conviennent à une exposition environnementale difficile.
Description du processus
Préparation de moules en polymère : les moules à cavités multiples ont été conçus à l’aide de modèles de joints. Des modèles de moule CAO 3D (format .stl) ont été utilisés pour créer des fichiers de tranche ou de couche pour l’impression 3D. Après l’impression 3D, les moules (figure 1a) ont été nettoyés dans des solvants organiques pour éliminer tout excès de résine à la surface, une opération qui a été suivie d’un dégazage/traitement UV, puis d’un traitement thermique à une température appropriée afin de s’assurer que les moules imprimés étaient complètement durcis. Nous avons constaté qu’il était crucial de durcir à la chaleur les matériaux du moule en polymère à une température appropriée, faute de quoi le silicone risquait de ne pas durcir complètement dans le moule en polymère et de rester collant au toucher.
Moules métalliques : les moules en acier à 4 cavités ont été préparés par usinage conventionnel. Les moules en acier ont été nettoyés à l’aide d’un solvant de dégraissage, puis utilisés pour le moulage en silicone.
Processus de moulage : les moules en polymère imprimés en 3D ont été pulvérisés à l’aide d’un lubrifiant de moule à base de silicone avant le moulage. Nous avons étendu l’utilisation des moules imprimés en 3D à divers processus de moulage tels que l’injection, le transfert et le moulage par compression. Nous avons développé une expertise autour de la conception de moules en polymère, du réglage du processus de moulage et de l’utilisation d’approches non conventionnelles, compte tenu de la durée de vie limitée de l’outil liée à la résistance/conductivité thermique inférieure du matériau du moule en polymère. Le moulage avec un outil en polymère nécessiterait normalement un temps de cycle plus long, ce qui est acceptable à des fins de prototypage. Il est essentiel de choisir un matériau de moule approprié, car les moules en polymère ont été soumis à une température de 180 ºC lors de notre processus de durcissement des silicones.
Après le démoulage, les joints ont été déflashés manuellement, puis post-durcis pendant 10 à 120 minutes supplémentaires à 180 ºC afin de garantir un durcissement complet. Selon la durabilité des caractéristiques de base, les moules peuvent être à usage unique ou réutilisables. À titre de comparaison, les joints ont également été fabriqués à partir de moules métalliques usinés à l’aide d’un processus de moulage standard.
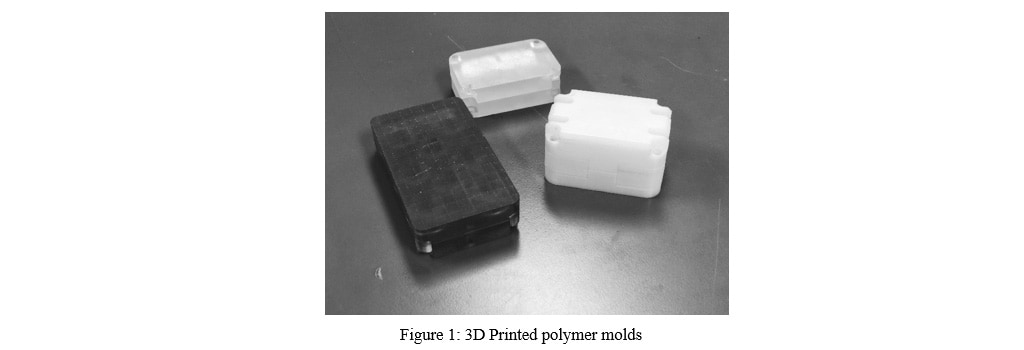
La figure 2a-g montre des exemples de joints moulés produits à l’aide de différents matériaux de moules en polymère imprimés dans une variété de formes, de tailles, de complexité et de types de matériaux en silicone. En utilisant des moules en polymère haute résolution, nous avons pu mouler de petits joints passants (figure 2b-c) avec un profil de trou complexe (diamètre du trou 1,01 mm, diamètre minimum dans le profil du trou 0,53 mm, épaisseur de paroi entre deux trous seulement 0,25 mm). La figure 2e-f montre un exemple de modèle de joint automobile dont les caractéristiques miniatures (épaisseur de paroi de 0,35 mm et trous de 0,69 mm de diamètre) ont été moulées avec succès. La figure 2g montre des exemples de joints automobiles périphériques et passants à fil unique.
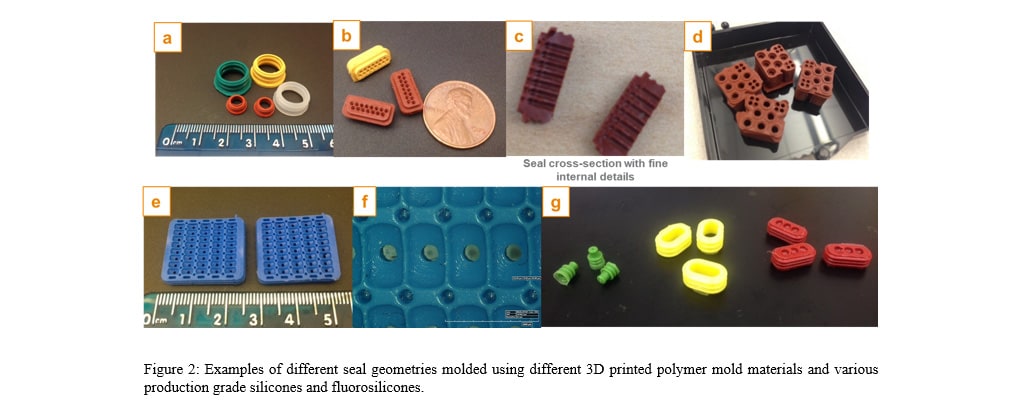
Résultats des tests fonctionnels d’étanchéité
Des joints fonctionnels (figure 2a) destinés à un client de l’aérospatiale, préparés à l’aide a) de moules en polymère imprimés en 3D et b) de moules en acier, ont été assemblés dans des bornes en aluminium, une opération suivie de l’insertion et du sertissage de fils (voir figure 3). Tous les joints ont satisfait aux exigences d’assemblage et de dimensions (les diamètres des dispositifs d’étanchéité étaient dans la tolérance autorisée de 0,1 mm). Les bornes assemblées ont été pressurisées à l’extrémité du fil et les fuites d’air testées sous l’eau à 1 bar et 2 bars. Des essais d’étanchéité ont été effectués avant et après que les pièces ont été soumises a) à 10 cycles de choc thermique (-65 ºC à 180 ºC) et b) au conditionnement de la température (180 ºC pendant 5 jours). Les exigences pour la qualification de la conception des joints du client étaient de réussir tous les tests à 1 bar sans fuite.
Des prototypes de joints ont été fabriqués pour différentes tailles de fils ; différents matériaux en silicone et en fluorosilicone ont été soumis à des tests d’étanchéité. Une qualité appropriée de matériau en silicone HCR a été présélectionnée sur la base d’une performance acceptable au test d’étanchéité. Les joints de moules en polymère ont réussi le test d’étanchéité pour toutes les tailles de fils avant et après le conditionnement par choc thermique, ce qui est un résultat très encourageant. En outre, tous les joints de moule en polymère pour fils plus gros (AWG 000, 00, 0A, 1, 2, 3) ont réussi le test d’étanchéité après le conditionnement de température de cinq jours à 180 ºC. Le processus de prototypage à base de moule polymère nous a également permis de qualifier rapidement des joints AWG 8 plus petits avec une conception modifiée (paroi plus épaisse atteignant 1,99 mm) qui ont réussi tous les tests d’étanchéité. Nos résultats montrent que les prototypes de joints des moules en polymère sont capables de répondre aux exigences fonctionnelles comme les moules en métal.
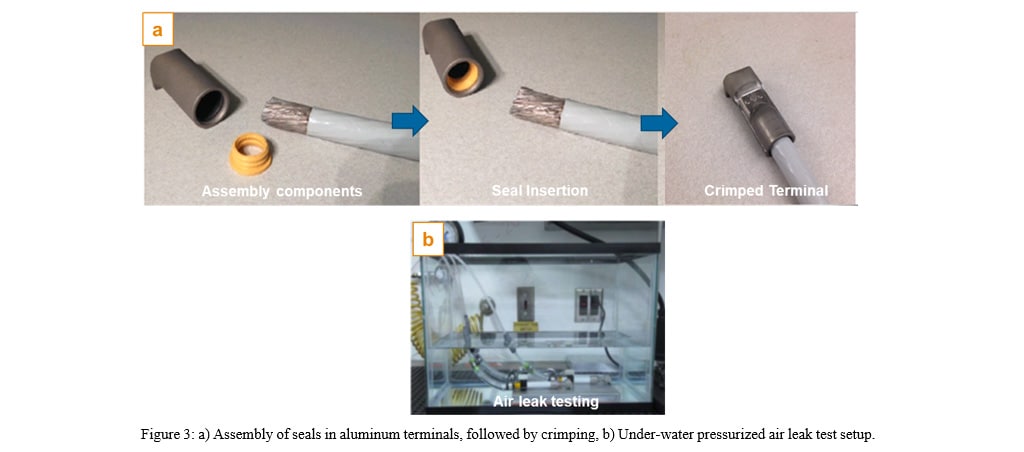
DISCUSSION ET POINTS CLÉS
Capacités et limites des moules en polymère imprimé en 3D
Le processus de moulage utilisant des moules polymères imprimés en 3D à plusieurs cavités peut produire des conceptions d’étanchéité complexes applicables à une large gamme de joints TE. Le nombre de cavités par moule en polymère peut varier de 1 pour les joints de plus grande taille à > 35 pour les joints de plus petite taille. Les imprimantes SLA utilisent généralement un laser afin de bénéficier d’une plus grande précision et d’une meilleure résolution (notez que la SLA peut également imprimer des angles ou des éléments saillants). Elles sont suivies de près par les imprimantes DLP qui utilisent la technologie de projection de lumière, puis par les imprimantes à jet monomère qui durcissent les photopolymères à l’aide de la lumière UV à large bande (notez que les coins aigus sont imprimés comme des arrondis). Le surdurcissement de la résine près des bords en raison de la pénétration de la lumière plus profondément que souhaité peut affecter la résolution et la précision de l’imprimante.
La rugosité de la surface des moules imprimés varie selon l’imprimante et le matériau imprimé. La rugosité de surface est inhérente à l’impression couche par couche (par exemple, épaisseur de couche 0,05 mm pour SLA) et à l’effet de marche d’escalier (surfaces construites en angle) qui peut être clairement vu dans l’image microscopique d’une caractéristique de moule SLA (figure 4a). La topographie de la surface du moule en polymère est clairement reproduite sur les joints moulés (figure 4b). La rugosité de la surface du joint moulé d’un moule en polymère est supérieure à celle des joints des moules métalliques (figure 4c). Une rugosité supplémentaire peut être présente dans les zones où le matériau de support est retiré de la surface du moule. La rugosité de surface supplémentaire peut ne pas être acceptable pour certaines applications d’étanchéité. Notez qu’il est également possible d’utiliser un outillage hybride, dans lequel des moules en polymère imprimés sont combinés avec des inserts de broches à noyau métallique pour les applications nécessitant des surfaces d’étanchéité de très faible rugosité.
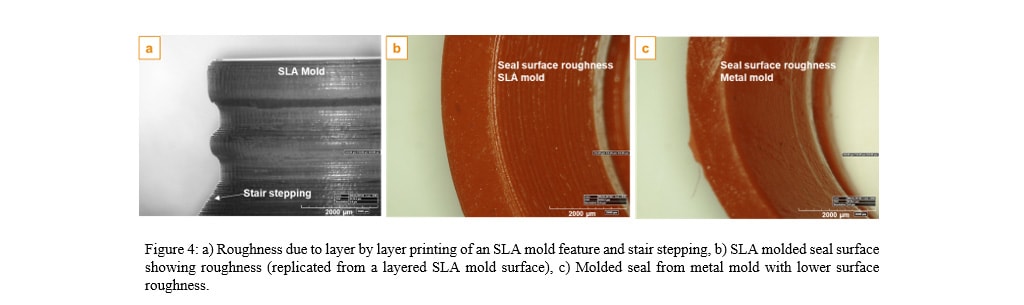
La durée de vie des moules en polymère est limitée, contrairement à celle des moules en métal. Les propriétés mécaniques des moules en polymère chutent considérablement aux températures les plus élevées, en particulier au-dessus de la température de fléchissement thermique [2]. La réutilisabilité des moules dépend fortement de la taille minimale des caractéristiques de base ainsi que des paramètres du processus de moulage tels que la température du moule, la pression, etc. Par exemple, les moules avec des caractéristiques de base plus grandes ont pu être utilisés plusieurs fois avant que le moule en polymère ne se fissure, tandis que les ruptures des moules présentant des caractéristiques de base plus petites réduisaient le nombre d’utilisations par moule. Pour les joints à géométrie extrêmement petite (impossible à réaliser par impression) et ou lorsqu’un grand nombre de pièces sont nécessaires, il peut être souhaitable d’utiliser un outillage hybride (c’est-à-dire un moule en polymère imprimé avec des inserts à broche à noyau métallique), plutôt que des moules en polymère sacrificiels ou à usage unique.
Coût/Temps
Nos coûts d’impression de moules internes étaient nettement inférieurs pour un moule à plusieurs cavités en polymère imprimé par rapport à un moule métallique usiné d’un fournisseur externe. Pour les moules imprimés, le temps total nécessaire entre la conception du moule et les joints moulés était de 2 semaines par rapport aux 8-10 semaines d’un fournisseur externe.
RÉCAPITULATIF
En résumé, nous avons développé une capacité unique de moulage rapide de joints dans différents silicones et fluorosilicones de qualité de production TE à l’aide de moules en polymère imprimés en 3D. Nous avons pu mettre en œuvre cette capacité grâce à notre expertise en conception de moules en polymère, à l’ajustement du processus de moulage et à l’utilisation d’approches non conventionnelles, compte tenu de la durée de vie limitée de l’outil liée à la résistance/conductivité thermique inférieure du matériau du moule en polymère. La capacité de passer rapidement de la conception CAO à la production de joints entièrement fonctionnels aide les ingénieurs TE à qualifier rapidement les joints en comparant différents modèles/matériaux de joints et à fournir rapidement des pièces aux clients finaux pour un retour d’information plus rapide des tests de produits. Notre processus de moulage rapide est un outil précieux qui permet de réaliser des économies considérables en termes de temps et d’argent pour la production de prototypes ou de joints HMLV entièrement fonctionnels qui répondent à toutes les exigences des clients.
REMERCIEMENTS
Les auteurs tiennent à remercier Martin Bayes, John Wasserbauer et Bob Zubrickie (Corporate Technology), Nicholas Ruffini, Kenneth Dowhower (A D et M) et Galen Martin (Automotive) pour leur précieux soutien dans le cadre de ce travail.
RÉFÉRENCES
[1] L. Zonder, N. Sella, « Precision Prototyping: The role of 3D printed molds in the injection molding industry », Stratasys.
[2] G. A. Mendible, « Applications of transient cooling simulations in injection molding », Ph.D. Thèse, Université du Massachusetts Lowell, 2015.