Plateforme d’inspection d’épaisseur de précision au niveau du micron en cours de fabrication
RÉSUMÉ
L’épaisseur, paramètre clé de la fabrication, influence directement les performances de la plaque. En raison de l’absence de méthode d’inspection en cours de fabrication, la méthode d’inspection hors ligne actuelle doit effectuer l’inspection destructive. De plus, le coût du changement de produit atteint systématiquement des centaines d’USD. Nous avons créé une plateforme d’inspection d’épaisseur pour procéder à l’inspection dynamique, sans contact, en cours de fabrication et avec une précision au niveau du micron.
ÉNONCÉ DU PROBLÈME
La plaque est un type de produit important et un composant fondamental pour de nombreux produits à puce. Elle se compose de trois couches. Deux couches métalliques et une couche à coefficient de température positif (PTC) sont laminées ensemble. La figure 1 montre l’illustration du procédé de fabrication de la plaque. L’épaisseur, qui a un impact direct sur les performances, est le paramètre le plus important de la qualité de la plaque. Si l’épaisseur du produit final n’est pas conforme aux spécifications, aucune retouche n’est possible et la plaque est mise au rebut.
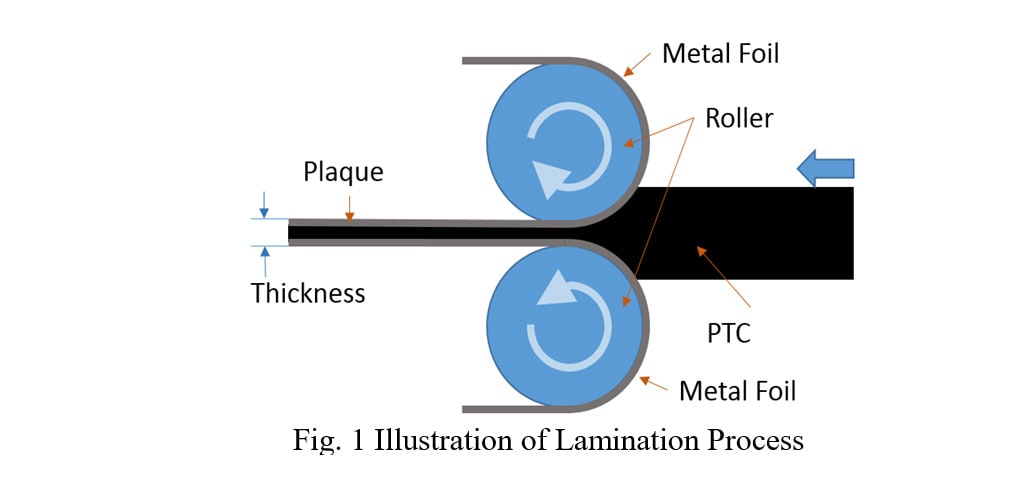
En production réelle, l’opérateur doit ajuster la distance entre deux rouleaux pour contrôler l’épaisseur. Le problème se produit lors du remplacement. Il existe 9 références de pièce avec différentes épaisseurs dans toute la famille de produits. De plus, en règle générale, le changement est fréquent, de l’ordre de deux fois par jour.
Le coût du remplacement est très élevé. Sans équipement d’inspection d’épaisseur en ligne, le remplacement actuel se décide sur la base d’une inspection hors ligne. L’opérateur doit d’abord produire des échantillons, arrêter la machine, puis couper les échantillons pour effectuer l’inspection destructive hors ligne. L’opérateur répétera le processus jusqu’à l’obtention d’un bon résultat. Il s’agit d’un ajustement au niveau du micron à la main, une opération très difficile qui prend beaucoup de temps.
Afin de développer un système d’inspection de l’épaisseur de plaque en ligne, trois facteurs doivent être pris en compte :
1) Précision au niveau du micron
2) Inspection dynamique
3) Inspection sans contact
Nous avons créé une plateforme d’inspection d’épaisseur pour procéder à l’inspection dynamique, sans contact, en cours de fabrication et avec une précision au niveau du micron. Nous avons utilisé la technologie laser pour effectuer l’inspection sans contact. Pour atteindre l’exigence de précision, nous avons effectué un DoE afin d’identifier le facteur d’influence clé pour l’inspection dynamique et de comprendre comment répondre à l’exigence de précision de l’inspection dynamique. La plateforme a obtenu la qualification GR&R.
MÉTHODES ET RÉSULTATS
Vue d’ensemble de la plateforme
La figure 4 montre la vue d’ensemble de la plateforme : la partie violette représente la plaque. Deux capteurs laser, l’un vers le haut et l’autre vers le bas, sont montés dans un cadre d’installation de capteur en forme de C et fonctionnent ensemble pour procéder à l’inspection de l’épaisseur. Deux arbres entraînés par le servomoteur permettent de déplacer le cadre en forme de C d’avant en arrière. Les arbres sont installés dans le cadre en marbre pour améliorer la stabilité. On utilise généralement du marbre comme base pour le système de mesure de haute précision, tel que la machine de mesure de coordination. Sous le cadre en marbre se trouve l’armoire de commande électrique.
En cours de production, la plaque passe par la station d’inspection en continu dans la direction X ; le capteur laser vers le haut et le capteur laser vers le bas se déplacent dans la direction Y pour former une trajectoire d’inspection en zigzag, comme illustré au bas de la figure 4.
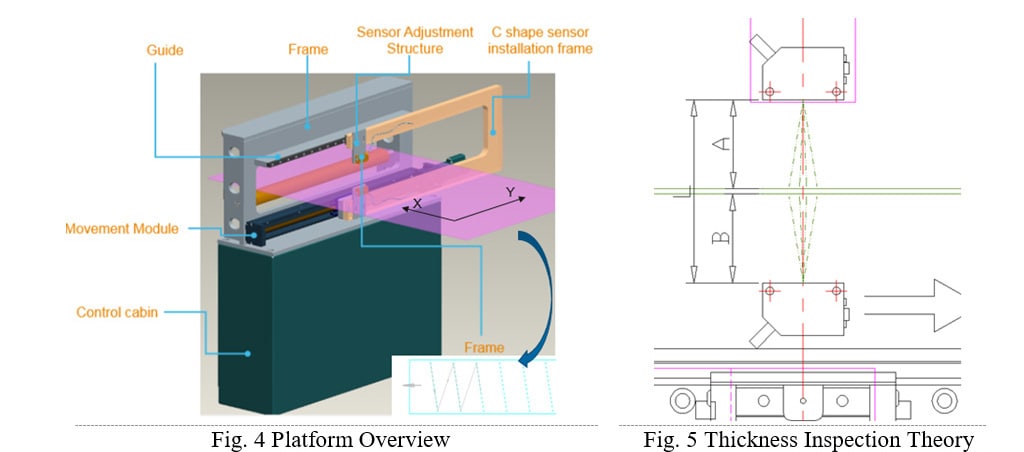
La théorie de l’inspection de l’épaisseur basée sur deux capteurs est illustrée à la figure 5. Deux capteurs laser sont utilisés pour inspecter la distance entre les capteurs et l’objet. Soit L la distance entre deux capteurs, A la distance mesurée par le capteur laser vers le haut et B la distance mesurée par le capteur laser vers le bas, la formule de calcul de l’épaisseur de la plaque est
Épaisseur = L-A-B (1)
Plateforme DoE basée sur un robot
Pour appliquer l’équation (1) en production réelle, nous devons nous assurer que l’environnement d’inspection satisfait pleinement à la condition de l’équation (1) pendant l’inspection. Cependant, l’environnement de fabrication réel occasionne du bruit, y compris l’erreur du capteur laser, la vibration de la plaque, la rotation de la plaque, le mouvement du capteur et le mouvement du produit, de sorte que nous pouvons difficilement appliquer directement l’équation (1).
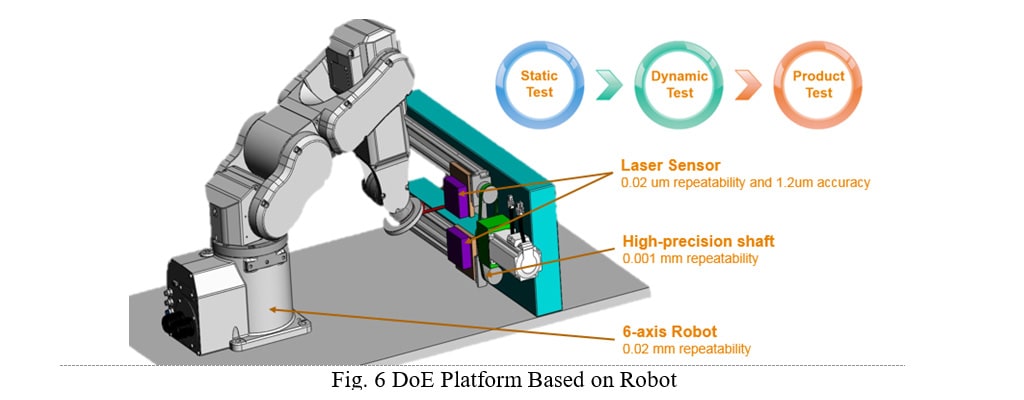
Nous avons construit une plateforme DoE pour analyser l’influence de chaque facteur influent. La plateforme DoE est basée sur un robot à 6 axes avec une répétabilité de 0,02 mm. La pince au niveau de l’effecteur final peut manipuler l’échantillon de plaque pour simuler les vibrations, la rotation, le mouvement vertical et le mouvement horizontal. Outre le robot, en tant que dispositif clé, le capteur laser de haute précision a une répétabilité de 0,02 micron et une précision de 1,2 micron. L’arbre pour déplacer horizontalement le capteur a une répétabilité de 0,001 mm. La précision intrinsèque du système est suffisante. Cependant, la précision intrinsèque pourrait être diminuée par l’environnement extérieur, de sorte que le but de ce DoE est de trouver le moyen de réduire l’influence et de récupérer la précision intrinsèque.
Nous avons effectué trois types d’expériences :
- Test statique : le produit et le capteur sont statiques pour tester la répétabilité et la précision du système. C’est la précision intrinsèque du système.
- Test dynamique : tester l’influence de la rotation du produit, des vibrations, du mouvement horizontal du produit et du mouvement vertical du produit, et découvrir la relation entre chaque facteur et la précision.
- Test de produit réel : qualification GR&R sur un produit réel.
DISCUSSION ET POINTS CLÉS
Ce document présente les innovations apportées à une plateforme d’inspection de précision au niveau du micron en cours de fabrication. Il contient également une vue d’ensemble de la plateforme, la technologie laser sans contact, l’algorithme d’étalonnage pour l’inspection dynamique, le logiciel et la qualification GR&R. Nous avons expliqué en détail comment améliorer la précision du système sur la base de l’expérience DoE et de l’analyse scientifique.
Les avantages de cette plateforme sont les suivants : en cours de fabrication, précision au niveau du micron, dynamique et sans contact. La plateforme d’inspection est directement intégrée dans la chaîne de fabrication et les données d’inspection en temps réel sont montrées à l’opérateur. La précision de l’inspection du système a atteint le niveau du micron et a obtenu la qualification GR&R. L’inspection dynamique est capable de couvrir une gamme de produits. Grâce à la technologie laser, nous avons réalisé l’inspection sans contact.
Cette plateforme a le potentiel de s’étendre à d’autres types de produits qui nécessitent une inspection d’épaisseur. De plus, cette plateforme peut être améliorée pour couvrir une chaîne de production plus rapide et une gamme de produits plus large.
Plateforme d’inspection d’épaisseur de précision au niveau du micron en cours de fabrication
RÉSUMÉ
L’épaisseur, paramètre clé de la fabrication, influence directement les performances de la plaque. En raison de l’absence de méthode d’inspection en cours de fabrication, la méthode d’inspection hors ligne actuelle doit effectuer l’inspection destructive. De plus, le coût du changement de produit atteint systématiquement des centaines d’USD. Nous avons créé une plateforme d’inspection d’épaisseur pour procéder à l’inspection dynamique, sans contact, en cours de fabrication et avec une précision au niveau du micron.
ÉNONCÉ DU PROBLÈME
La plaque est un type de produit important et un composant fondamental pour de nombreux produits à puce. Elle se compose de trois couches. Deux couches métalliques et une couche à coefficient de température positif (PTC) sont laminées ensemble. La figure 1 montre l’illustration du procédé de fabrication de la plaque. L’épaisseur, qui a un impact direct sur les performances, est le paramètre le plus important de la qualité de la plaque. Si l’épaisseur du produit final n’est pas conforme aux spécifications, aucune retouche n’est possible et la plaque est mise au rebut.
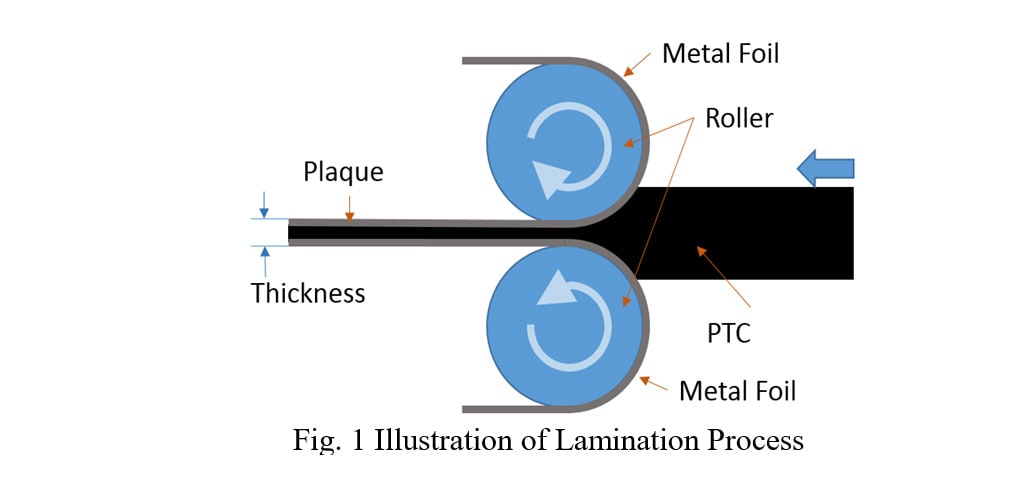
En production réelle, l’opérateur doit ajuster la distance entre deux rouleaux pour contrôler l’épaisseur. Le problème se produit lors du remplacement. Il existe 9 références de pièce avec différentes épaisseurs dans toute la famille de produits. De plus, en règle générale, le changement est fréquent, de l’ordre de deux fois par jour.
Le coût du remplacement est très élevé. Sans équipement d’inspection d’épaisseur en ligne, le remplacement actuel se décide sur la base d’une inspection hors ligne. L’opérateur doit d’abord produire des échantillons, arrêter la machine, puis couper les échantillons pour effectuer l’inspection destructive hors ligne. L’opérateur répétera le processus jusqu’à l’obtention d’un bon résultat. Il s’agit d’un ajustement au niveau du micron à la main, une opération très difficile qui prend beaucoup de temps.
Afin de développer un système d’inspection de l’épaisseur de plaque en ligne, trois facteurs doivent être pris en compte :
1) Précision au niveau du micron
2) Inspection dynamique
3) Inspection sans contact
Nous avons créé une plateforme d’inspection d’épaisseur pour procéder à l’inspection dynamique, sans contact, en cours de fabrication et avec une précision au niveau du micron. Nous avons utilisé la technologie laser pour effectuer l’inspection sans contact. Pour atteindre l’exigence de précision, nous avons effectué un DoE afin d’identifier le facteur d’influence clé pour l’inspection dynamique et de comprendre comment répondre à l’exigence de précision de l’inspection dynamique. La plateforme a obtenu la qualification GR&R.
MÉTHODES ET RÉSULTATS
Vue d’ensemble de la plateforme
La figure 4 montre la vue d’ensemble de la plateforme : la partie violette représente la plaque. Deux capteurs laser, l’un vers le haut et l’autre vers le bas, sont montés dans un cadre d’installation de capteur en forme de C et fonctionnent ensemble pour procéder à l’inspection de l’épaisseur. Deux arbres entraînés par le servomoteur permettent de déplacer le cadre en forme de C d’avant en arrière. Les arbres sont installés dans le cadre en marbre pour améliorer la stabilité. On utilise généralement du marbre comme base pour le système de mesure de haute précision, tel que la machine de mesure de coordination. Sous le cadre en marbre se trouve l’armoire de commande électrique.
En cours de production, la plaque passe par la station d’inspection en continu dans la direction X ; le capteur laser vers le haut et le capteur laser vers le bas se déplacent dans la direction Y pour former une trajectoire d’inspection en zigzag, comme illustré au bas de la figure 4.
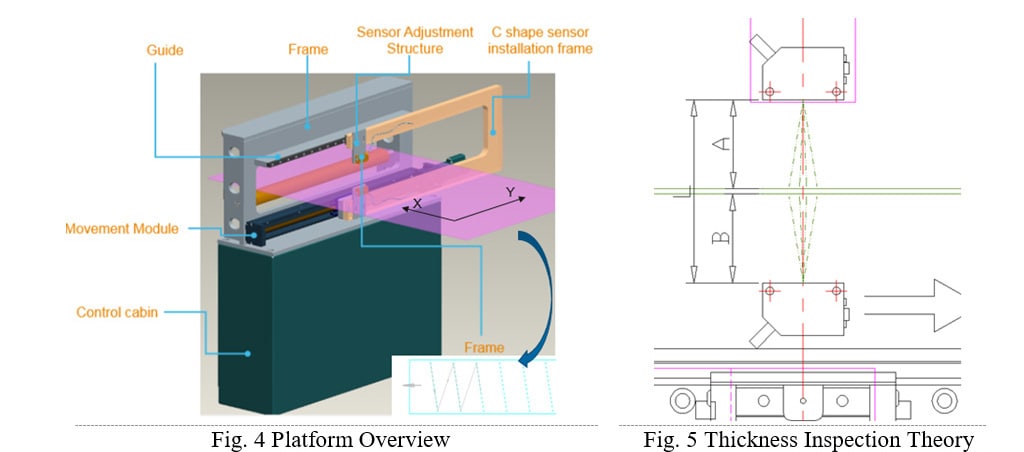
La théorie de l’inspection de l’épaisseur basée sur deux capteurs est illustrée à la figure 5. Deux capteurs laser sont utilisés pour inspecter la distance entre les capteurs et l’objet. Soit L la distance entre deux capteurs, A la distance mesurée par le capteur laser vers le haut et B la distance mesurée par le capteur laser vers le bas, la formule de calcul de l’épaisseur de la plaque est
Épaisseur = L-A-B (1)
Plateforme DoE basée sur un robot
Pour appliquer l’équation (1) en production réelle, nous devons nous assurer que l’environnement d’inspection satisfait pleinement à la condition de l’équation (1) pendant l’inspection. Cependant, l’environnement de fabrication réel occasionne du bruit, y compris l’erreur du capteur laser, la vibration de la plaque, la rotation de la plaque, le mouvement du capteur et le mouvement du produit, de sorte que nous pouvons difficilement appliquer directement l’équation (1).
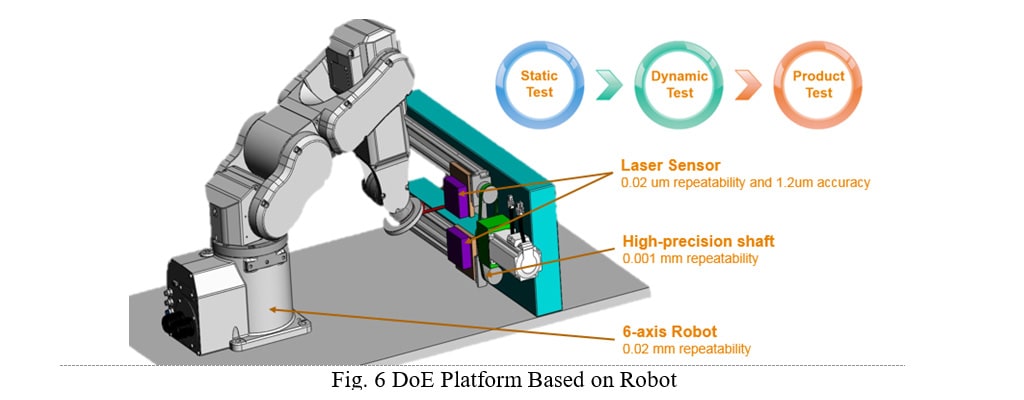
Nous avons construit une plateforme DoE pour analyser l’influence de chaque facteur influent. La plateforme DoE est basée sur un robot à 6 axes avec une répétabilité de 0,02 mm. La pince au niveau de l’effecteur final peut manipuler l’échantillon de plaque pour simuler les vibrations, la rotation, le mouvement vertical et le mouvement horizontal. Outre le robot, en tant que dispositif clé, le capteur laser de haute précision a une répétabilité de 0,02 micron et une précision de 1,2 micron. L’arbre pour déplacer horizontalement le capteur a une répétabilité de 0,001 mm. La précision intrinsèque du système est suffisante. Cependant, la précision intrinsèque pourrait être diminuée par l’environnement extérieur, de sorte que le but de ce DoE est de trouver le moyen de réduire l’influence et de récupérer la précision intrinsèque.
Nous avons effectué trois types d’expériences :
- Test statique : le produit et le capteur sont statiques pour tester la répétabilité et la précision du système. C’est la précision intrinsèque du système.
- Test dynamique : tester l’influence de la rotation du produit, des vibrations, du mouvement horizontal du produit et du mouvement vertical du produit, et découvrir la relation entre chaque facteur et la précision.
- Test de produit réel : qualification GR&R sur un produit réel.
DISCUSSION ET POINTS CLÉS
Ce document présente les innovations apportées à une plateforme d’inspection de précision au niveau du micron en cours de fabrication. Il contient également une vue d’ensemble de la plateforme, la technologie laser sans contact, l’algorithme d’étalonnage pour l’inspection dynamique, le logiciel et la qualification GR&R. Nous avons expliqué en détail comment améliorer la précision du système sur la base de l’expérience DoE et de l’analyse scientifique.
Les avantages de cette plateforme sont les suivants : en cours de fabrication, précision au niveau du micron, dynamique et sans contact. La plateforme d’inspection est directement intégrée dans la chaîne de fabrication et les données d’inspection en temps réel sont montrées à l’opérateur. La précision de l’inspection du système a atteint le niveau du micron et a obtenu la qualification GR&R. L’inspection dynamique est capable de couvrir une gamme de produits. Grâce à la technologie laser, nous avons réalisé l’inspection sans contact.
Cette plateforme a le potentiel de s’étendre à d’autres types de produits qui nécessitent une inspection d’épaisseur. De plus, cette plateforme peut être améliorée pour couvrir une chaîne de production plus rapide et une gamme de produits plus large.