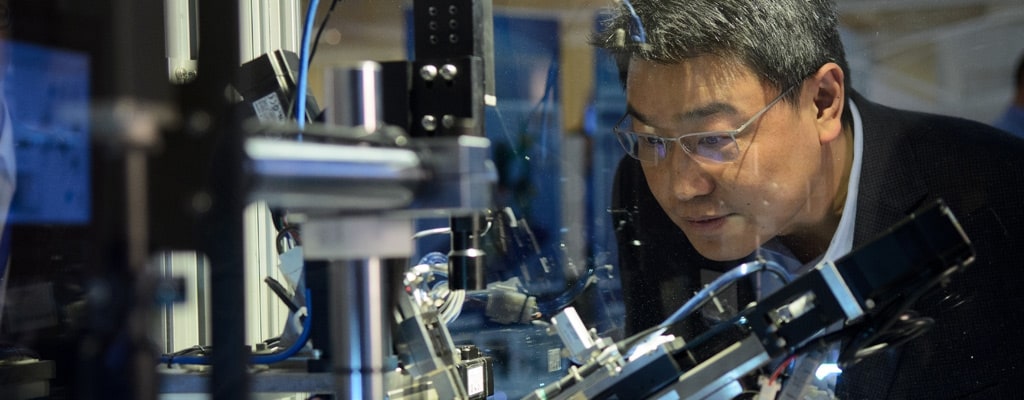
Accélérer l’innovation
Pour réussir sur le marché actuel de la technologie, vous devez développer une solution optimale, rendre le client heureux et arriver rapidement sur le marché. L’un des moyens les plus rapides d’atteindre ces résultats est l’impression 3D, une technologie cruciale pour transformer rapidement les idées en prototypes entièrement fonctionnels qui aident les équipes à tester les concepts tôt et à itérer efficacement.
Auteurs :
Gregory T. Pawlikowski, Ingénieur principal de développement, Harrisburg Research Center
Jessica H. B. Hemond, Ingénieure de développement principale, Harrisburg Research Center
Ranjan D. Deshmukh, Scientifique du personnel, Harrisburg Research Center
La fabrication de prototypes fonctionnels commence par l’utilisation de résines d’ingénierie possédant les propriétés et les cotes requises, avec un processus de fabrication similaire à celui utilisé dans la fabrication du produit final. Dans l’impression 3D actuelle, les techniques manquent principalement d’options en termes de matériaux et des performances physiques nécessaires. Cela limite la capacité d’un fabricant à imprimer directement des pièces en plastique fonctionnelles. Malgré cela, les fabricants peuvent tirer parti de l’impression 3D pour fabriquer rapidement des outils de moulage destinés à la fabrication de pièces prototypes fonctionnelles, avec le même matériau et le même processus qu’une pièce de production. Les fabricants bénéficient ainsi de quatre avantages qui leur permettent de :
- Réaliser des tests complets pour la vérification de la conception
- Qualifier les pièces pour la qualité de la production
- Fournir des pièces pour les évaluations des clients
- Accélérer le processus de développement de produits
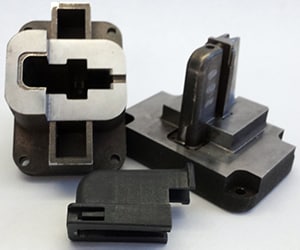
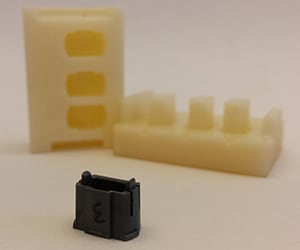
L’ALTERNATIVE : L’OUTILLAGE DE MOULE IMPRIMÉ EN 3D
L’outillage de moulage de production est généralement fabriqué à partir de plusieurs pièces, nécessitant des techniques d’usinage de haute précision pour fabriquer et assembler les outils. Cela nécessite généralement un volume de pièces élevé pour justifier le coût. La plupart du temps, ce processus ne convient pas à la fabrication de petites quantités de pièces, surtout lorsque la conception pourrait changer.
Alors que les processus soustractifs à rotation rapide permettent aux fabricants de créer un outillage de moulage simplifié, ceux-ci utilisent des fraiseuses à commande numérique par ordinateur (CNC) automatisées, qui ont souvent des problèmes avec la portée de l’outil de coupe, en particulier lorsqu’il y a une cavité profondément encastrée ainsi que des limitations géométriques, telles que les rayons d’angle intérieurs. De plus, les processus soustractifs peuvent également impliquer de longs délais et, en fin de compte, dépasser les coûts prévus.
Heureusement, il existe une alternative : l’outillage de moule imprimé en 3D. Cette approche produit un outillage utilisable dans une machine de moulage traditionnelle et compatible avec les résines de qualité production. Développée pour une variété de techniques d’impression 3D, cette approche peut inclure des matériaux métalliques et plastiques pour l’outillage de moulage. Alors que les outils métalliques usinés ont l’avantage de fournir de très petits éléments avec une grande durabilité, l’outillage imprimé en 3D est complémentaire en ce sens qu’il offre suffisamment de résolution, de stabilité thermique et de résistance des matériaux pour générer de petits volumes et des pièces moulées à rotation rapide.
Par exemple, il existe de nombreuses applications qui nécessitent des pièces capables de résister à des conditions environnementales difficiles. La fabrication de ces pièces implique l’utilisation de résines à haute température de qualité technique et nécessite des attributs tels que des éléments fins, des parois minces et un haut niveau de complexité combiné à des tolérances serrées. Le moulage des pièces précises à partir d’outils de moulage imprimés en 3D présente quelques complexités. Notre équipe chez TE en a identifié et résolu plusieurs, notamment :
- Résolution et précision d’impression
- Finition secondaire de l’outillage de moule imprimé
- Durabilité de l’insert de moule
- Type de résine d’ingénierie et conditions de traitement
- Remaniement de pièces moulées
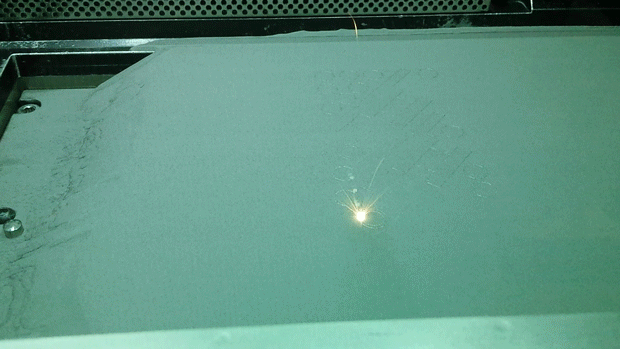
Les technologies d’impression 3D – y compris le frittage laser direct des métaux (DMLS) – sont essentielles pour permettre à TE de produire des outils rapides avec une bonne précision et une bonne résolution.
CHOISIR LA BONNE IMPRIMANTE ET LES BONS MATÉRIAUX
Nous avons appris que pour surmonter ces difficultés, nous devions commencer par choisir le bon type d’imprimante 3D et de matériaux de moulage. La résolution et la précision d’impression des moules imprimés sont limitées et peuvent varier en fonction de l’imprimante et du matériau de moule utilisé. Nous avons constaté que les imprimantes stéréolithographiques (SLA) – qui durcissent généralement un matériau en résine liquide à l’aide d’un laser – offrent à la fois la plus grande précision (~ 0,02-0,05 mm) et la meilleure résolution de fonctionnalité (jusqu’à 0,125 mm). Cela peut également produire de l’outillage avec des éléments et des coins précis et nets.
D’autres technologies importantes comprennent l’impression numérique de traitement de la lumière (DLP), qui utilise la technologie de projection de lumière, et les imprimantes à jet de monomère, qui peuvent durcir les gouttelettes de résine photopolymère distribuées en utilisant la lumière UV à large bande. Les technologies d’impression 3D sur lit de poudre, telles que le frittage laser direct du métal (DMLS), peuvent atteindre une bonne précision et une bonne résolution, mais produire une finition de surface rugueuse.
Une considération importante est la finition secondaire des moules et des inserts imprimés, car elle peut augmenter le coût et le temps globaux du processus. Une finition de surface rugueuse réduit non seulement la qualité de surface de la pièce moulée, mais peut également nuire à la libération de la pièce lors de l’éjection du moule. Les technologies de durcissement par photopolymère (telles que la SLA et le jet de monomères) fournissent des surfaces relativement lisses qui nécessitent des opérations de post-finition faibles ou négligeables.
En raison de la rugosité de surface inhérente aux outils métalliques imprimés DMLS, un certain degré d’usinage secondaire est souvent nécessaire. Cependant, si une surface plus rugueuse est autorisée, des opérations moins complexes telles que le sablage de billes ou la finition à la main sont parfois suffisantes. Certains effets de rugosité de surface et de pas d’escalier (sur des surfaces construites en angle) sont inévitables – même pour l’outillage de moules en polymère – lors de l’utilisation de l’impression couche par couche (par exemple, épaisseur de couche 0,05 mm pour la SLA).
Alors que la rugosité de surface est le plus gros problème avec les moules métalliques imprimés DMLS, la durabilité des outils est le principal défi pour les moules en polymère. Cela est dû à la résistance intrinsèquement plus faible des polymères par rapport aux métaux, en particulier lorsque différentes propriétés thermiques et mécaniques sont impliquées aux températures et pressions de moulage élevées. Les propriétés mécaniques et thermiques de l’outillage polymère déterminent en fin de compte le nombre de pièces moulées correctement ou le nombre de tirs.
Ces propriétés influencent directement la survie des éléments du noyau (en particulier pour les noyaux de petite taille et/ou à rapport d’aspect élevé) et peuvent entraîner une fissuration ou une déformation prématurée de l’insertion de moule. La fissuration et la déformation de l’insert sont plus particulièrement déterminées par des facteurs tels que la résistance du matériau du moule à des températures plus élevées, la dégradation du matériau du moule au contact du polymère chaud fondu, le coefficient de dilatation thermique/les différences de conductivité thermique et le choc thermique.
Notre équipe a identifié les éléments permettant de choisir le bon matériau d’imprimante et de moule :
- Géométrie de la pièce, plus petit élément
- Matériel de production à mouler
- Nombre de pièces nécessaires
Il existe d’autres facteurs qui ont un impact sur la réussite : il est crucial d’établir les bonnes conditions pour le processus de moulage et de déterminer les règles de conception de moules modifiées qui conviennent aux moules en polymère.
N’oubliez pas que la durabilité – et les performances ultérieures – de l’outillage de moule en polymère est déterminée de manière significative par la résine d’ingénierie utilisée pour la pièce moulée, le type de charge (par exemple, les fibres de verre abrasives ont tendance à causer une usure sévère du moule, par rapport à la résine non remplie), la viscosité fondue et les paramètres de traitement du moule. Cela peut nécessiter des ajustements du processus d’impression, du modèle ou des deux, afin de garantir des dimensions de pièce précises.
En utilisant un outil métallique imprimé, les fabricants peuvent appliquer des valeurs standard de traitement et de retrait des polymères. Pour que cela fonctionne avec les moules en polymère, les fabricants peuvent avoir besoin d’effectuer des ajustements des processus et de la conception des moules. Comprendre pleinement le processus et les adaptations de conception vous aidera à optimiser l’utilisation de cette technologie.
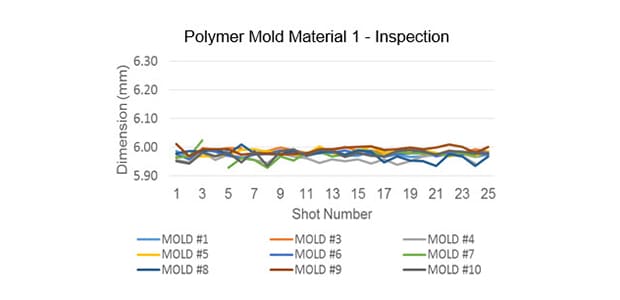
Tous les moules en polymère ne sont pas égaux en performance. Choisir le bon matériau de moule est la clé d’une mise en œuvre réussie.
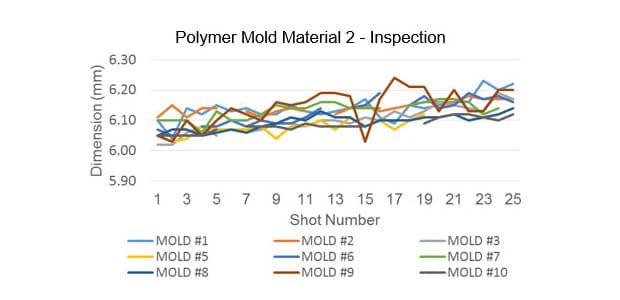
Chez TE, nous développons et améliorons continuellement nos processus de fabrication de moules en polymère, en vue de les déployer dans l’ensemble de notre portefeuille de produits. Cela inclut la plupart des matériaux de la pyramide de résine et les machines de moulage existantes. En utilisant des avancées uniques en matière de conception et de processus, nous pouvons surmonter les limites traditionnelles imposées à l’outillage imprimé. Avec les bons processus, nous n’imprimons pas seulement des éléments fins, mais nous les reproduisons également dans les pièces moulées. Cela inclut le moulage avec des matériaux à haute température tels que les polymères à cristaux liquides (LCP) dans des moules en polymère imprimés. Les allocations qui peuvent être nécessaires dépendent de la technologie utilisée.
Gardez à l’esprit que les performances des matériaux de moule en polymère varient considérablement. Lorsque l’on compare différents matériaux de moules en polymère, il existe des avantages évidents en termes de durabilité et d’usure par rapport aux cycles de moulage répétés. Il existe également une certaine variation – basée sur le matériau du moule en polymère – dans les ajustements de conception nécessaires pour amener le moule aux dimensions nominales et dans les limites de la tolérance.
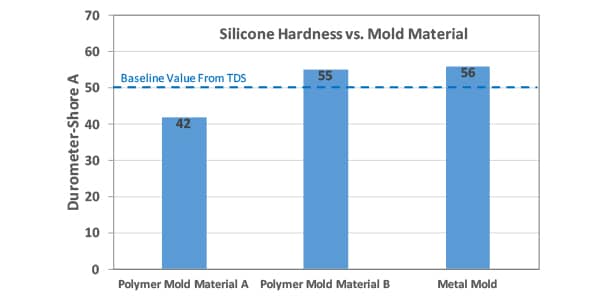
Cette technologie ne se limite pas aux résines thermoplastiques. Nous l’utilisons également pour mouler des résines thermodurcissables, telles que des silicones, des fluorosilicones et d’autres élastomères. Compte tenu du coût et de la complexité des moules en silicone traditionnels, il y a un avantage évident à adapter une approche à faible coût et à rotation rapide. Comme on le voit lors du moulage de résines thermoplastiques dans des moules en polymère, les fabricants peuvent avoir besoin d’ajuster la conception et le processus de l’outil. Bien qu’il soit également important de sélectionner le matériau de moule approprié, l’objectif est de fabriquer un outil qui offre les performances d’un moule traditionnel.
Il y a un avantage dans le délai d’exécution, qui est souvent plus court que les méthodes d’usinage conventionnelles. Non seulement le processus d’impression est capable de produire des résultats rapidement (seulement quelques heures dans certains cas), mais il peut également produire un outillage de moule imprimé utilisable avec peu ou pas de finition secondaire. Pour minimiser les coûts et réduire les temps de production, les fabricants peuvent mettre en place des stratégies pour rendre les moules imprimés aussi petits que possible.
Alors que les moules en polymère imprimés en 3D ne produisent souvent qu’un nombre limité de pièces moulées, la nouvelle technologie utilise des moules imprimés supplémentaires pour multiplier le nombre total possible. En cas de besoin, les fabricants peuvent utiliser des moules métalliques imprimés en 3D pour créer un plus grand nombre de pièces moulées, dans des conditions de traitement de production.
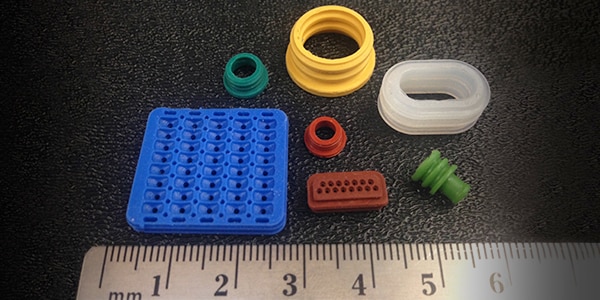
NOTRE ENGAGEMENT ENVERS L’INNOVATION
Chez TE, nous pouvons appliquer cette technologie à la plupart des résines de production utilisées. Mais il y a encore des défis à surmonter. Aujourd’hui, nous nous efforçons d’améliorer la durabilité des éléments plus fins et à adapter le processus pour fabriquer des produits à plus grande échelle, pour nos portefeuilles d’énergie ou de transport. Actuellement, nous travaillons avec des technologies qui nous permettent de respecter des tolérances serrées et des caractéristiques de tangage fin, <0,4 mm.
Dans le même temps, nous effectuons des ajustements dans la conception et le traitement lors de la fabrication de pièces de plus de 12 cm. En affinant la conception du moule et les paramètres du processus, nous pouvons envisager de déployer davantage cette technologie sur l’ensemble de notre portefeuille.
Aujourd’hui, il n’existe pas de solution d’impression 3D unique adaptée à la production de toutes les nombreuses gammes de géométries et de volumes de produits. En ce qui concerne l’impression 3D, nous exploitons une suite diversifiée de technologies d’impression en interne. La diversité de nos technologies d’impression 3D est le résultat de notre engagement continu et à long terme – qui remonte à la fin des années 1980 – envers l’investissement dans des technologies qui tirent parti de nos vastes capacités et de notre savoir-faire en matière d’outillage et de moulage de moules, de manière à nous permettre de développer et de tester de nouvelles solutions pour produire de faibles volumes de prototypes fonctionnels. Chaque jour au sein de notre entreprise, nous utilisons ces technologies pour faire progresser notre expertise interne et collaborer au sein d’un réseau mondial d’ingénieurs diversifiés engagés à accélérer l’innovation et à adopter une technologie d’outillage rapide.