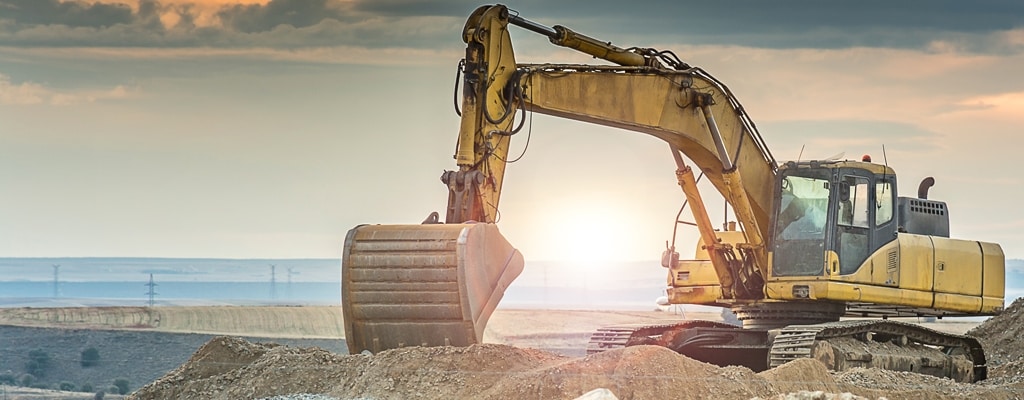
Application
LA PRESSION POUR UN BON FONCTIONNEMENT DANS LES SYSTÈMES HYDRAULIQUES ET LES CIRCUITS
Au cours des deux dernières décennies, le secteur hydraulique a bénéficié des progrès de l’électronique, de l’adoption généralisée de l’IdO (Internet des Objets), de la réduction des coûts technologiques et de la miniaturisation des composants. De plus, l’industrie hydraulique a connu un nombre croissant de défis lors de la transition des pressostats traditionnels aux capteurs de pression. Ces défis incluent des augmentations de la pression, des températures de fonctionnement plus élevées, des déploiements dans des environnements à risque et difficiles et des transitoires de pression. Ce sont des défis pour les concepteurs et les intégrateurs de systèmes et ils peuvent entraîner des retards dans le projet ou des problèmes de fiabilité sur le terrain s’ils ne sont pas traités de manière appropriée. Ces appareils de mesure de la pression ont également évolué, de l’élément de détection et du boîtier mécanique dans son ensemble à son signal de sortie électronique et au conditionnement du signal. Dans ce document, nous examinons la technologie derrière les capteurs de pression, les défis mécaniques courants auxquels ces capteurs sont confrontés et les performances du capteur de pression M9100 de TE Connectivity (TE) dans ces environnements difficiles.
Technologie de détection
Aperçu de l’intérieur de votre capteur
De l’extérieur, les capteurs de pression se ressemblent tous, mais l’élément principal de détection varie considérablement d’un fabricant à l’autre. L’une des approches économiques et technologiquement réalisables les plus courantes consiste à utiliser une jauge de contrainte comme élément de détection pour transférer la contrainte mécanique induite par la pression sur une membrane en un signal de sortie électrique précis et reproductible. TE utilise sa technologie de jauge de contrainte Microfused dans une configuration de pont de Wheatstone pour transformer la contrainte en un signal de sortie de tension. TE a conçu l’élément de détection comme un composant usiné unique intégré au port fileté. Cette conception optimisée fournit un signal robuste de l’élément de détection et offre de grands niveaux de surpression et de performances en rafale.
TE utilise un procédé de collage du verre pour fusionner les jauges de contrainte en silicium au port métallique. Les jauges sont positionnées de manière optimale pour correctement mesurer la contrainte lorsque la pression change. Des procédés de fixation des fils éprouvés du secteur sont utilisés pour établir des connexions entre les jauges et les composants électroniques de conditionnement du signal. Les technologies concurrentes sur le marché des capteurs de pression hydraulique, telles que les technologies de dépôt de film mince, de films épais et à base de céramique, utilisent des membranes séparées avec des éléments de détection à faible sensibilité. Ces technologies nécessitent des soudures supplémentaires dans les parcours des fluides, les joints toriques internes ou nécessitent des étapes de traitement supplémentaires qui peuvent entraîner de longs délais dans la chaîne d’approvisionnement. D’autres technologies peuvent nécessiter des contraintes élevées dans leur élément de détection pour compenser la faible sensibilité. Ces contraintes élevées ainsi que la construction en plusieurs pièces peuvent entraîner une réduction de la stabilité et de la durabilité à long terme. La technologie de jauge de contrainte Microfused de TE a fait ses preuves dans la production à haut volume depuis des décennies, présente un faible risque de perturbation de la chaîne d’approvisionnement et fournit une connexion fluide monobloc robuste, réduisant ainsi le risque de défaillances des capteurs internes et d’autres défis mécaniques.

Défis mécaniques
Les capteurs de pression étant installés comme partie intégrante d’un système hydraulique, il est nécessaire de relever et de définir les divers défis mécaniques dans la conception. Vous trouverez ci-dessous les domaines typiques des systèmes hydrauliques que les concepteurs de systèmes doivent prendre en compte lors du processus de conception :
- Pression de fonctionnement
- Pics de pression
- Pression d’épreuve
- Connexions fluides
- Pression d’éclatement
- Vibration/Choc mécanique
- Fatigue de pression
- Durabilité environnementale
Chacune de ces préoccupations est prise en compte dans la conception et la validation du capteur. Les surpressions nominales, les pressions nominales d’éclatement, l’analyse de la fatigue et l’utilisation d’amortisseurs de pression font toutes partie du processus de conception chez TE et sont validées à la fois par simulation et par des tests empiriques.
Plage de pression de fonctionnement
En termes simples, il s’agit de la plage de pression qui nécessite un contrôle ou un retour d'information du système. Dans des conditions de fonctionnement typiques, le système reste toujours dans cette plage. Les pressions en dehors de cette plage ne nécessitent pas de mesure habituellement.
Pression d’épreuve
Dans la conception d'un système, il existe souvent des événements de pression qui dépassent la plage de mesures nécessaire mais qui ne devraient pas endommager le système. En règle générale, il est attendu qu’après un événement de surpression, le système revienne à son fonctionnement normal. TE spécifie la pression d’épreuve comme la pression qui peut être appliquée à l’élément de détection sans provoquer de modification permanente de la caractéristique de sortie ou de la précision du capteur de pression.
Pression d’éclatement
Des modes de défaillance potentiels au niveau du système pouvant entraîner des pressions excessives du système sont possibles, ce qui risque de provoquer une défaillance du confinement de la pression. TE conçoit et valide ses capteurs de pression à la fois théoriquement et empiriquement pour spécifier la pression minimale que le capteur peut subir sans rupture.
Fatigue de pression
La fatigue de pression typique se trouve dans les systèmes dotés d'une pompe ou d'une vanne qui entraîne continuellement des fluctuations de pression dans le système. Ces fluctuations varient en amplitude et en fréquence. Une pompe peut créer une oscillation de pression à haute fréquence avec une très faible amplitude, tandis qu’une vanne peut entraîner un changement de pression important, mais moins fréquemment. Dans certains cas, le contraire peut être vrai. Il est impossible de prévoir chaque comportement potentiel du système. Pour cette raison, le M9100 de TE est testé à une pression de 0 jusqu'à une pression maximum, allant jusqu'à 10 m de cycles. Il est aussi théoriquement validé pour confirmer que les contraintes restent inférieures à la limite de fatigue, offrant une durée de vie pratiquement illimitée dans la plage de fonctionnement, et souvent dans la plage de pression d’épreuve. Il convient de souligner que l’élément de détection de TE étant beaucoup plus sensible que les technologies concurrentes, le niveau de tension est si faible que la fatigue de pression n’est pas un problème.
Pics de pression
Le défi le moins connu dans un système hydraulique est probablement l’existence de transitoires de pression à très haute fréquence, communément appelés « pics de pression » et parfois appelés effet coup de bélier. Un pic de pression peut se produire pendant l’actionnement de la vanne, des ondes de pression imposées en raison de l’architecture du système ou de l’introduction d’air dans la pompe hydraulique. Le pic de pression est généralement caractérisé par une augmentation extrêmement rapide de la pression (le plus souvent en microsecondes) à des amplitudes très élevées (potentiellement 10 fois la pression de fonctionnement). La vitesse d’un pic de pression peut être si rapide qu’un capteur de pression typique peut ne pas être capable de détecter que l’événement s’est produit. Ce phénomène peut cependant endommager de façon permanente le capteur de pression, résultant en un décalage permanent du zéro, entraîner une défaillance du capteur à répondre à la pression ou une rupture de la membrane, provoquant une fuite du fluide dans le boîtier du capteur. Souvent, les clients ne disposent pas de l’équipement approprié pour identifier correctement les pics de pression dans leur système, mais le choix d’un capteur de pression avec la bonne technologie sera une aide. La conception robuste du M9100 de TE et son amortisseur en option réduisent les modes de défaillance potentiels causés par les pics de pression.
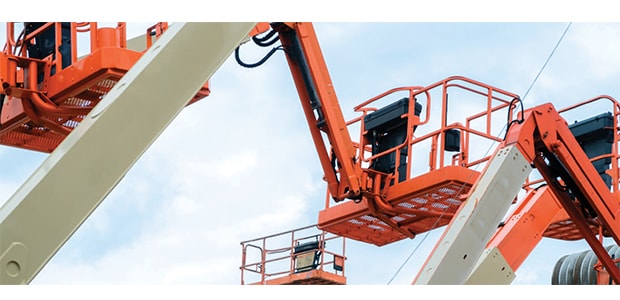
Connexions fluides
Une autre considération mécanique est la connexion au circuit hydraulique. Il existe différentes options de connexion filetée populaires dans les régions du monde, notamment SAE (Amérique du Nord), G-series (EMEA) et Metric (APAC). TE a une longue expérience en matière de normes industrielles historiques telles que SAE J1926 ou ISO 1179, et continue de suivre le rythme face aux exigences changeantes. Chaque connexion filetée possède également ses propres classes. Les pressions élevées étant de plus en plus courantes dans le secteur hydraulique, des précautions supplémentaires doivent être prises pour s’assurer que le capteur de pression est correctement classé, placé et couplé.
Vibration/Choc mécanique
Les chocs mécaniques et les vibrations sont traditionnellement associés au secteur des capteurs. Les capteurs de pression sont généralement exposés aux deux conditions dans les applications sur route et hors route en raison de l’environnement mécanique spécifique des applications dans lesquelles ils sont utilisés. Des vibrations à haute fréquence d’un moteur diesel au choc d’un chariot élévateur laissant tomber une charge complète au sol, ces conditions exigent que le capteur de pression soit protégé des effets néfastes des chocs et vibrations.
Durabilité environnementale
La durabilité environnementale est essentielle pour s’assurer que tout produit peut répondre aux conditions extrêmes de l’environnement et fournir des années de service fiable. Un capteur de pression doit tenir compte de la conception mécanique et du choix des matériaux pour garantir une compatibilité et une fiabilité tout au long de la durée d’utilisation, mais doit également tenir compte de l’impact de ces conditions environnementales sur les performances à long terme du capteur. Maintenant que nous avons passé en revue les défis mécaniques courants auxquels les capteurs de pression sont confrontés, penchons-nous sur la conception renforcée du capteur de pression robuste M9100 de TE conçu pour résoudre les défis mécaniques des machines hydrauliques critiques.

Conception renforcée
La conception renforcée et les performances fiables du capteur de pression M9100 répondent aux besoins de détection de la pression des applications à usage intensif. Le capteur M9100 de TE est l’un des meilleurs de sa catégorie en matière de durabilité hydraulique. Le capteur M9100 a été conçu en prenant en compte la simplicité et la durabilité afin de satisfaire ou de dépasser les besoins des applications les plus difficiles. Les conceptions complexes qui nécessitent plusieurs cartes de circuits, un câblage interne et plusieurs interconnexions soudées sont généralement plus vulnérables, avec des défaillances précoces et des problèmes de fiabilité sur le terrain. Le M9100 est conçu pour être simple, compact et durable en éliminant autant de modes de défaillance que possible. Le capteur de pression atteint son encombrement compact avec une seule conception de circuit imprimé. Tous les joints de soudure du capteur sont bien contrôlés grâce à un équipement automatisé de transfert et à un soudage par refusion. Il n’y a pas de joints de soudure à la main ou d’interconnexions soudées à l’intérieur du capteur et les circuits ne sont pas empilés.
La structure de la membrane de détection en acier inoxydable usinée d’une seule pièce élimine les étapes d’assemblage supplémentaires telles que la soudure et le collage. La construction produit un faible degré de contrainte, ce qui se traduit par une excellente résistance à la preuve, à l’éclatement, à la fatigue et aux pics de pression, réduisant ainsi le risque de problèmes pendant le processus de conception et sur le terrain. La conception du capteur Microfused comporte une membrane extrêmement épaisse par rapport aux autres technologies. Cela permet au capteur d’être plus résistant aux dommages causés par les pics de pression et de contenir pleinement ces événements de pression. De plus, le M9100 de TE est doté d’un amortisseur intégré en option qui peut réduire davantage la vitesse et l’amplitude d’un pic de pression. La conception intégrée élimine le besoin d’un composant séparé. Le corps interne du capteur est étanche à l’environnement externe grâce à un joint torique. Cette conception protège les composants internes du capteur des brouillards salins, de l’humidité, du lavage à haute pression et de l’immersion.
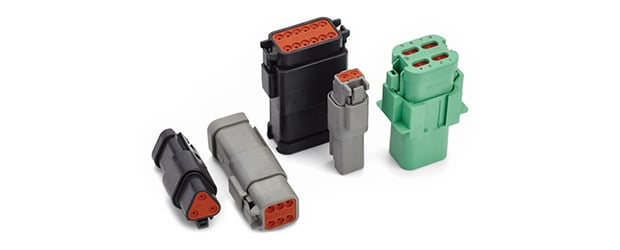
Compatibilité avec les systèmes de connexion robustes
Le capteur de pression M9100 est adapté aux systèmes de connexion durables de grande taille tels que la série de connecteurs DEUTSCH DT de TE, l’une des meilleures de sa catégorie en termes de protection contre les infiltrations. Le système de connexion DEUTSCH associé à la conception robuste du capteur permet d’obtenir dès le départ un capteur capable de résister aux diverses conditions difficiles et élimine le risque que les brouillards salins, l’humidité, la poussière ou l’eau puissent pénétrer dans le produit, ce qui entraînerait une défaillance. Les matériaux choisis pour la conception dépassent la plage de température de fonctionnement du produit. Le choix du thermoplastique, de l’adhésif et des composants électroniques (y compris un ASIC classé AEC-Q100) contribuent à la robustesse du produit à des températures extrêmes, à la lumière du soleil, à l’oxygène ou aux produits chimiques courants présents dans les applications d’équipement lourd.

Performances du capteur de pression M9100
Les machines hydrauliques et leurs composants doivent fonctionner de manière fiable lorsqu’ils sont exposés à des conditions extrêmes. La technologie de base d’un capteur de pression est un système électromécanique très complexe. L’objectif du capteur de pression est de convertir la pression dans un système en une sortie électrique. Sur le plan physique, la stratégie consiste à convertir une contrainte dans une surface, « la membrane », en une sortie électrique directement proportionnelle et reproductible à la pression appliquée. Cependant, la complexité vient du fait que les éléments utilisés sont sensibles à presque toutes les autres influences environnementales.
Technologie de jauge de contrainte
La technologie de jauge de contrainte de TE, expliquée précédemment dans ce document, a été développée et optimisée au fil des décennies pour minimiser les sources d’erreur et fournir une sortie de pression très sensible et reproductible. Ce signal de sortie peut ensuite être corrigé et amplifié à l’aide d’un circuit intégré spécifique à l’application (ASIC). Cet ASIC corrige les erreurs induites par la sortie non linéaire, ainsi que les erreurs thermiques et les variations de tension d’alimentation. Cette correction d’erreur simplifie la définition de base des performances en un terme simple appelé bande d’erreur totale. La bande d’erreur totale est le point culminant de toutes les erreurs restantes que l’ASIC ne peut pas corriger (y compris la variation d’une pièce à l’autre et d’un lot à l’autre) et est définie comme l’erreur maximale que l’utilisateur rencontrera sur la plage de températures compensée. Le M9100 utilise un ASIC validé AEC-Q100 doté de capacités de diagnostic. Les diagnostics confirment que le capteur fonctionne correctement et réduisent le risque d’avoir un signal de sortie incorrect.
L’utilisation de la spécification de la bande d’erreur totale sur une large plage de températures (- 40 °C à + 125 °C) simplifie les attentes sur la façon dont le capteur fonctionnera dans le système. L’ASIC est également responsable du conditionnement du signal du capteur, en prenant le signal des jauges de contrainte en silicium et en le convertissant en un signal analogique amplifié. Bien que l’ASIC corrige les erreurs reproductibles, les mêmes effets environnementaux peuvent entraîner des erreurs non reproductibles, la plus fréquente étant la dérive dans le temps. La dérive est définie comme un changement basé sur le temps dans la sortie du capteur. Cette influence peut provenir d’un certain nombre de sources, y compris les changements dans la contrainte mécanique dans une membrane (fluage ou relaxation des contraintes) ; les changements physiques dans l’élément de détection dus à des effets électriques ou mécaniques, ou des changements dans la résistivité des connexions électriques ou des gels protecteurs. Les cycles de pression, les surpressions, l’exposition aux températures, le cycle de température et l’humidité peuvent tous contribuer à cette dérive à long terme. La longue expérience de TE dans la technologie des jauges de contrainte Microfused et les contributeurs connus concernant la dérive environnementale ont permis à TE d’optimiser la conception et le traitement pour fournir aux clients un produit stable. Du concept à la preuve en passant par les tests de validation, la jauge de contrainte Microfused de TE est l’une des meilleures technologies de détection de sa catégorie.
Protection élevée contre les interférences électromagnétiques
L’environnement électrique des équipements devient de plus en plus complexe à mesure que les données sont communiquées au sein et autour de l’équipement. Les capteurs sont exposés à des niveaux croissants de bruit électrique qui peuvent interférer avec le signal si le capteur n’est pas correctement protégé. Le M9100 est validé selon la norme ISO 11452-2 pour la sensibilité rayonnée, ce qui permet au produit de résister au bruit électrique à proximité et d'avoir une installation à proximité des composants émetteurs d’IEM. Le M9100 est résistant aux interférences d'injection de courant de masse jusqu’à 200 mA conformément à la norme ISO 11452-4. De plus, un niveau élevé de protection électrique de l’alimentation rend le capteur plus robuste à un contrôle insuffisant de l’alimentation et réduit le risque de problèmes an niveau du système. Bien qu’il soit recommandé de concevoir un système de câblage qui ne permet pas les connexions inverses, le M9100 peut résister à une surtension allant jusqu’à 28 VCC, à des tensions d’alimentation inversées allant jusqu’à 16 VCC et à une sortie analogique court-circuitée vers V(+) ou GND, le tout sans subir de dommages. Veuillez consulter la fiche technique du capteur M9100 pour obtenir la liste complète des spécifications de test électrique pour lesquelles le produit a été validé.

Conclusion
Les systèmes hydrauliques sont une composante essentielle des systèmes de transport industriel et commercial. L’industrie hydraulique a connu une augmentation des défis lors de la transition des pressostats traditionnels vers les capteurs et capteurs de pression, tels que les augmentations de la pression, les températures de fonctionnement plus élevées, le déploiement dans des environnements dangereux et difficiles et les transitoires de pression dans les circuits hydrauliques. La conception renforcée et les performances fiables du capteur de pression M9100 de TE Connectivity résout les problèmes et répond aux besoins de détection de la pression des applications à usage intensif.
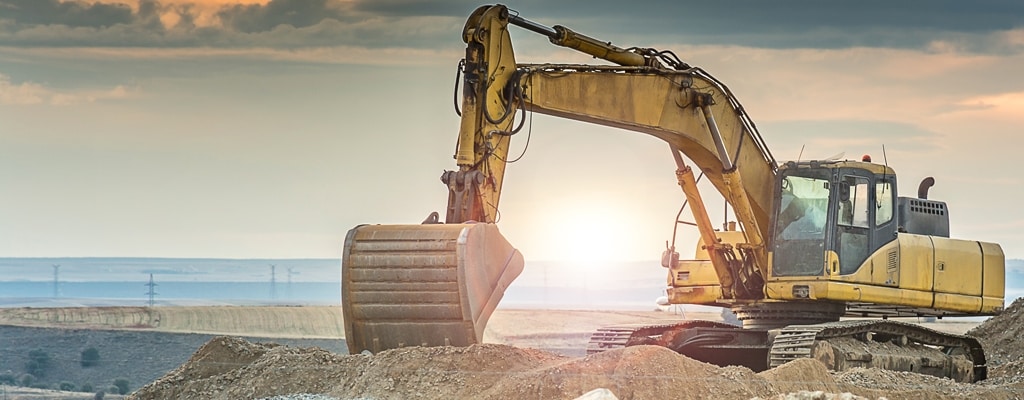
Application
LA PRESSION POUR UN BON FONCTIONNEMENT DANS LES SYSTÈMES HYDRAULIQUES ET LES CIRCUITS
Au cours des deux dernières décennies, le secteur hydraulique a bénéficié des progrès de l’électronique, de l’adoption généralisée de l’IdO (Internet des Objets), de la réduction des coûts technologiques et de la miniaturisation des composants. De plus, l’industrie hydraulique a connu un nombre croissant de défis lors de la transition des pressostats traditionnels aux capteurs de pression. Ces défis incluent des augmentations de la pression, des températures de fonctionnement plus élevées, des déploiements dans des environnements à risque et difficiles et des transitoires de pression. Ce sont des défis pour les concepteurs et les intégrateurs de systèmes et ils peuvent entraîner des retards dans le projet ou des problèmes de fiabilité sur le terrain s’ils ne sont pas traités de manière appropriée. Ces appareils de mesure de la pression ont également évolué, de l’élément de détection et du boîtier mécanique dans son ensemble à son signal de sortie électronique et au conditionnement du signal. Dans ce document, nous examinons la technologie derrière les capteurs de pression, les défis mécaniques courants auxquels ces capteurs sont confrontés et les performances du capteur de pression M9100 de TE Connectivity (TE) dans ces environnements difficiles.
Technologie de détection
Aperçu de l’intérieur de votre capteur
De l’extérieur, les capteurs de pression se ressemblent tous, mais l’élément principal de détection varie considérablement d’un fabricant à l’autre. L’une des approches économiques et technologiquement réalisables les plus courantes consiste à utiliser une jauge de contrainte comme élément de détection pour transférer la contrainte mécanique induite par la pression sur une membrane en un signal de sortie électrique précis et reproductible. TE utilise sa technologie de jauge de contrainte Microfused dans une configuration de pont de Wheatstone pour transformer la contrainte en un signal de sortie de tension. TE a conçu l’élément de détection comme un composant usiné unique intégré au port fileté. Cette conception optimisée fournit un signal robuste de l’élément de détection et offre de grands niveaux de surpression et de performances en rafale.
TE utilise un procédé de collage du verre pour fusionner les jauges de contrainte en silicium au port métallique. Les jauges sont positionnées de manière optimale pour correctement mesurer la contrainte lorsque la pression change. Des procédés de fixation des fils éprouvés du secteur sont utilisés pour établir des connexions entre les jauges et les composants électroniques de conditionnement du signal. Les technologies concurrentes sur le marché des capteurs de pression hydraulique, telles que les technologies de dépôt de film mince, de films épais et à base de céramique, utilisent des membranes séparées avec des éléments de détection à faible sensibilité. Ces technologies nécessitent des soudures supplémentaires dans les parcours des fluides, les joints toriques internes ou nécessitent des étapes de traitement supplémentaires qui peuvent entraîner de longs délais dans la chaîne d’approvisionnement. D’autres technologies peuvent nécessiter des contraintes élevées dans leur élément de détection pour compenser la faible sensibilité. Ces contraintes élevées ainsi que la construction en plusieurs pièces peuvent entraîner une réduction de la stabilité et de la durabilité à long terme. La technologie de jauge de contrainte Microfused de TE a fait ses preuves dans la production à haut volume depuis des décennies, présente un faible risque de perturbation de la chaîne d’approvisionnement et fournit une connexion fluide monobloc robuste, réduisant ainsi le risque de défaillances des capteurs internes et d’autres défis mécaniques.

Défis mécaniques
Les capteurs de pression étant installés comme partie intégrante d’un système hydraulique, il est nécessaire de relever et de définir les divers défis mécaniques dans la conception. Vous trouverez ci-dessous les domaines typiques des systèmes hydrauliques que les concepteurs de systèmes doivent prendre en compte lors du processus de conception :
- Pression de fonctionnement
- Pics de pression
- Pression d’épreuve
- Connexions fluides
- Pression d’éclatement
- Vibration/Choc mécanique
- Fatigue de pression
- Durabilité environnementale
Chacune de ces préoccupations est prise en compte dans la conception et la validation du capteur. Les surpressions nominales, les pressions nominales d’éclatement, l’analyse de la fatigue et l’utilisation d’amortisseurs de pression font toutes partie du processus de conception chez TE et sont validées à la fois par simulation et par des tests empiriques.
Plage de pression de fonctionnement
En termes simples, il s’agit de la plage de pression qui nécessite un contrôle ou un retour d'information du système. Dans des conditions de fonctionnement typiques, le système reste toujours dans cette plage. Les pressions en dehors de cette plage ne nécessitent pas de mesure habituellement.
Pression d’épreuve
Dans la conception d'un système, il existe souvent des événements de pression qui dépassent la plage de mesures nécessaire mais qui ne devraient pas endommager le système. En règle générale, il est attendu qu’après un événement de surpression, le système revienne à son fonctionnement normal. TE spécifie la pression d’épreuve comme la pression qui peut être appliquée à l’élément de détection sans provoquer de modification permanente de la caractéristique de sortie ou de la précision du capteur de pression.
Pression d’éclatement
Des modes de défaillance potentiels au niveau du système pouvant entraîner des pressions excessives du système sont possibles, ce qui risque de provoquer une défaillance du confinement de la pression. TE conçoit et valide ses capteurs de pression à la fois théoriquement et empiriquement pour spécifier la pression minimale que le capteur peut subir sans rupture.
Fatigue de pression
La fatigue de pression typique se trouve dans les systèmes dotés d'une pompe ou d'une vanne qui entraîne continuellement des fluctuations de pression dans le système. Ces fluctuations varient en amplitude et en fréquence. Une pompe peut créer une oscillation de pression à haute fréquence avec une très faible amplitude, tandis qu’une vanne peut entraîner un changement de pression important, mais moins fréquemment. Dans certains cas, le contraire peut être vrai. Il est impossible de prévoir chaque comportement potentiel du système. Pour cette raison, le M9100 de TE est testé à une pression de 0 jusqu'à une pression maximum, allant jusqu'à 10 m de cycles. Il est aussi théoriquement validé pour confirmer que les contraintes restent inférieures à la limite de fatigue, offrant une durée de vie pratiquement illimitée dans la plage de fonctionnement, et souvent dans la plage de pression d’épreuve. Il convient de souligner que l’élément de détection de TE étant beaucoup plus sensible que les technologies concurrentes, le niveau de tension est si faible que la fatigue de pression n’est pas un problème.
Pics de pression
Le défi le moins connu dans un système hydraulique est probablement l’existence de transitoires de pression à très haute fréquence, communément appelés « pics de pression » et parfois appelés effet coup de bélier. Un pic de pression peut se produire pendant l’actionnement de la vanne, des ondes de pression imposées en raison de l’architecture du système ou de l’introduction d’air dans la pompe hydraulique. Le pic de pression est généralement caractérisé par une augmentation extrêmement rapide de la pression (le plus souvent en microsecondes) à des amplitudes très élevées (potentiellement 10 fois la pression de fonctionnement). La vitesse d’un pic de pression peut être si rapide qu’un capteur de pression typique peut ne pas être capable de détecter que l’événement s’est produit. Ce phénomène peut cependant endommager de façon permanente le capteur de pression, résultant en un décalage permanent du zéro, entraîner une défaillance du capteur à répondre à la pression ou une rupture de la membrane, provoquant une fuite du fluide dans le boîtier du capteur. Souvent, les clients ne disposent pas de l’équipement approprié pour identifier correctement les pics de pression dans leur système, mais le choix d’un capteur de pression avec la bonne technologie sera une aide. La conception robuste du M9100 de TE et son amortisseur en option réduisent les modes de défaillance potentiels causés par les pics de pression.
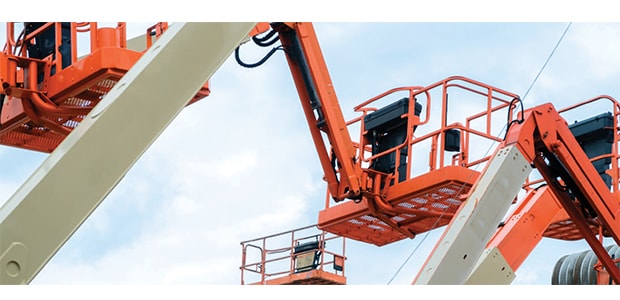
Connexions fluides
Une autre considération mécanique est la connexion au circuit hydraulique. Il existe différentes options de connexion filetée populaires dans les régions du monde, notamment SAE (Amérique du Nord), G-series (EMEA) et Metric (APAC). TE a une longue expérience en matière de normes industrielles historiques telles que SAE J1926 ou ISO 1179, et continue de suivre le rythme face aux exigences changeantes. Chaque connexion filetée possède également ses propres classes. Les pressions élevées étant de plus en plus courantes dans le secteur hydraulique, des précautions supplémentaires doivent être prises pour s’assurer que le capteur de pression est correctement classé, placé et couplé.
Vibration/Choc mécanique
Les chocs mécaniques et les vibrations sont traditionnellement associés au secteur des capteurs. Les capteurs de pression sont généralement exposés aux deux conditions dans les applications sur route et hors route en raison de l’environnement mécanique spécifique des applications dans lesquelles ils sont utilisés. Des vibrations à haute fréquence d’un moteur diesel au choc d’un chariot élévateur laissant tomber une charge complète au sol, ces conditions exigent que le capteur de pression soit protégé des effets néfastes des chocs et vibrations.
Durabilité environnementale
La durabilité environnementale est essentielle pour s’assurer que tout produit peut répondre aux conditions extrêmes de l’environnement et fournir des années de service fiable. Un capteur de pression doit tenir compte de la conception mécanique et du choix des matériaux pour garantir une compatibilité et une fiabilité tout au long de la durée d’utilisation, mais doit également tenir compte de l’impact de ces conditions environnementales sur les performances à long terme du capteur. Maintenant que nous avons passé en revue les défis mécaniques courants auxquels les capteurs de pression sont confrontés, penchons-nous sur la conception renforcée du capteur de pression robuste M9100 de TE conçu pour résoudre les défis mécaniques des machines hydrauliques critiques.

Conception renforcée
La conception renforcée et les performances fiables du capteur de pression M9100 répondent aux besoins de détection de la pression des applications à usage intensif. Le capteur M9100 de TE est l’un des meilleurs de sa catégorie en matière de durabilité hydraulique. Le capteur M9100 a été conçu en prenant en compte la simplicité et la durabilité afin de satisfaire ou de dépasser les besoins des applications les plus difficiles. Les conceptions complexes qui nécessitent plusieurs cartes de circuits, un câblage interne et plusieurs interconnexions soudées sont généralement plus vulnérables, avec des défaillances précoces et des problèmes de fiabilité sur le terrain. Le M9100 est conçu pour être simple, compact et durable en éliminant autant de modes de défaillance que possible. Le capteur de pression atteint son encombrement compact avec une seule conception de circuit imprimé. Tous les joints de soudure du capteur sont bien contrôlés grâce à un équipement automatisé de transfert et à un soudage par refusion. Il n’y a pas de joints de soudure à la main ou d’interconnexions soudées à l’intérieur du capteur et les circuits ne sont pas empilés.
La structure de la membrane de détection en acier inoxydable usinée d’une seule pièce élimine les étapes d’assemblage supplémentaires telles que la soudure et le collage. La construction produit un faible degré de contrainte, ce qui se traduit par une excellente résistance à la preuve, à l’éclatement, à la fatigue et aux pics de pression, réduisant ainsi le risque de problèmes pendant le processus de conception et sur le terrain. La conception du capteur Microfused comporte une membrane extrêmement épaisse par rapport aux autres technologies. Cela permet au capteur d’être plus résistant aux dommages causés par les pics de pression et de contenir pleinement ces événements de pression. De plus, le M9100 de TE est doté d’un amortisseur intégré en option qui peut réduire davantage la vitesse et l’amplitude d’un pic de pression. La conception intégrée élimine le besoin d’un composant séparé. Le corps interne du capteur est étanche à l’environnement externe grâce à un joint torique. Cette conception protège les composants internes du capteur des brouillards salins, de l’humidité, du lavage à haute pression et de l’immersion.
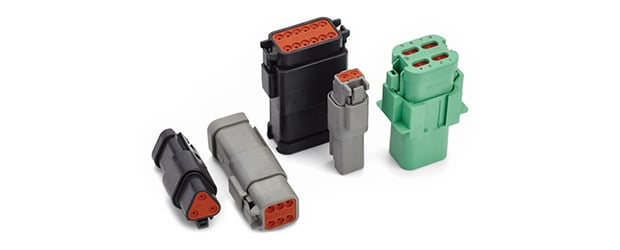
Compatibilité avec les systèmes de connexion robustes
Le capteur de pression M9100 est adapté aux systèmes de connexion durables de grande taille tels que la série de connecteurs DEUTSCH DT de TE, l’une des meilleures de sa catégorie en termes de protection contre les infiltrations. Le système de connexion DEUTSCH associé à la conception robuste du capteur permet d’obtenir dès le départ un capteur capable de résister aux diverses conditions difficiles et élimine le risque que les brouillards salins, l’humidité, la poussière ou l’eau puissent pénétrer dans le produit, ce qui entraînerait une défaillance. Les matériaux choisis pour la conception dépassent la plage de température de fonctionnement du produit. Le choix du thermoplastique, de l’adhésif et des composants électroniques (y compris un ASIC classé AEC-Q100) contribuent à la robustesse du produit à des températures extrêmes, à la lumière du soleil, à l’oxygène ou aux produits chimiques courants présents dans les applications d’équipement lourd.

Performances du capteur de pression M9100
Les machines hydrauliques et leurs composants doivent fonctionner de manière fiable lorsqu’ils sont exposés à des conditions extrêmes. La technologie de base d’un capteur de pression est un système électromécanique très complexe. L’objectif du capteur de pression est de convertir la pression dans un système en une sortie électrique. Sur le plan physique, la stratégie consiste à convertir une contrainte dans une surface, « la membrane », en une sortie électrique directement proportionnelle et reproductible à la pression appliquée. Cependant, la complexité vient du fait que les éléments utilisés sont sensibles à presque toutes les autres influences environnementales.
Technologie de jauge de contrainte
La technologie de jauge de contrainte de TE, expliquée précédemment dans ce document, a été développée et optimisée au fil des décennies pour minimiser les sources d’erreur et fournir une sortie de pression très sensible et reproductible. Ce signal de sortie peut ensuite être corrigé et amplifié à l’aide d’un circuit intégré spécifique à l’application (ASIC). Cet ASIC corrige les erreurs induites par la sortie non linéaire, ainsi que les erreurs thermiques et les variations de tension d’alimentation. Cette correction d’erreur simplifie la définition de base des performances en un terme simple appelé bande d’erreur totale. La bande d’erreur totale est le point culminant de toutes les erreurs restantes que l’ASIC ne peut pas corriger (y compris la variation d’une pièce à l’autre et d’un lot à l’autre) et est définie comme l’erreur maximale que l’utilisateur rencontrera sur la plage de températures compensée. Le M9100 utilise un ASIC validé AEC-Q100 doté de capacités de diagnostic. Les diagnostics confirment que le capteur fonctionne correctement et réduisent le risque d’avoir un signal de sortie incorrect.
L’utilisation de la spécification de la bande d’erreur totale sur une large plage de températures (- 40 °C à + 125 °C) simplifie les attentes sur la façon dont le capteur fonctionnera dans le système. L’ASIC est également responsable du conditionnement du signal du capteur, en prenant le signal des jauges de contrainte en silicium et en le convertissant en un signal analogique amplifié. Bien que l’ASIC corrige les erreurs reproductibles, les mêmes effets environnementaux peuvent entraîner des erreurs non reproductibles, la plus fréquente étant la dérive dans le temps. La dérive est définie comme un changement basé sur le temps dans la sortie du capteur. Cette influence peut provenir d’un certain nombre de sources, y compris les changements dans la contrainte mécanique dans une membrane (fluage ou relaxation des contraintes) ; les changements physiques dans l’élément de détection dus à des effets électriques ou mécaniques, ou des changements dans la résistivité des connexions électriques ou des gels protecteurs. Les cycles de pression, les surpressions, l’exposition aux températures, le cycle de température et l’humidité peuvent tous contribuer à cette dérive à long terme. La longue expérience de TE dans la technologie des jauges de contrainte Microfused et les contributeurs connus concernant la dérive environnementale ont permis à TE d’optimiser la conception et le traitement pour fournir aux clients un produit stable. Du concept à la preuve en passant par les tests de validation, la jauge de contrainte Microfused de TE est l’une des meilleures technologies de détection de sa catégorie.
Protection élevée contre les interférences électromagnétiques
L’environnement électrique des équipements devient de plus en plus complexe à mesure que les données sont communiquées au sein et autour de l’équipement. Les capteurs sont exposés à des niveaux croissants de bruit électrique qui peuvent interférer avec le signal si le capteur n’est pas correctement protégé. Le M9100 est validé selon la norme ISO 11452-2 pour la sensibilité rayonnée, ce qui permet au produit de résister au bruit électrique à proximité et d'avoir une installation à proximité des composants émetteurs d’IEM. Le M9100 est résistant aux interférences d'injection de courant de masse jusqu’à 200 mA conformément à la norme ISO 11452-4. De plus, un niveau élevé de protection électrique de l’alimentation rend le capteur plus robuste à un contrôle insuffisant de l’alimentation et réduit le risque de problèmes an niveau du système. Bien qu’il soit recommandé de concevoir un système de câblage qui ne permet pas les connexions inverses, le M9100 peut résister à une surtension allant jusqu’à 28 VCC, à des tensions d’alimentation inversées allant jusqu’à 16 VCC et à une sortie analogique court-circuitée vers V(+) ou GND, le tout sans subir de dommages. Veuillez consulter la fiche technique du capteur M9100 pour obtenir la liste complète des spécifications de test électrique pour lesquelles le produit a été validé.

Conclusion
Les systèmes hydrauliques sont une composante essentielle des systèmes de transport industriel et commercial. L’industrie hydraulique a connu une augmentation des défis lors de la transition des pressostats traditionnels vers les capteurs et capteurs de pression, tels que les augmentations de la pression, les températures de fonctionnement plus élevées, le déploiement dans des environnements dangereux et difficiles et les transitoires de pression dans les circuits hydrauliques. La conception renforcée et les performances fiables du capteur de pression M9100 de TE Connectivity résout les problèmes et répond aux besoins de détection de la pression des applications à usage intensif.