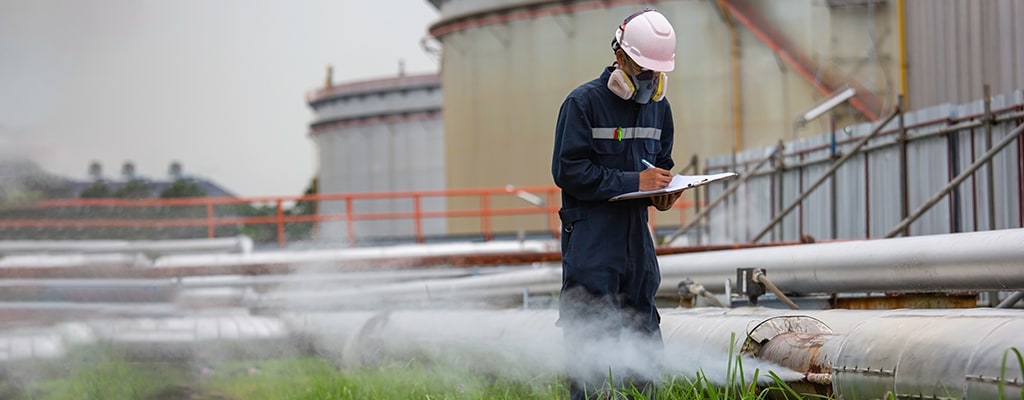
Industries
Détecter et surveiller la corrosion sous isolation dans l’industrie du pétrole et du gaz
La corrosion sous l’isolation (CUI) constitue un véritable problème important dans de nombreux secteurs, en particulier dans les industries pétrochimiques, pétrolières et gazières. Ce problème omniprésent, dissimulé sous des couches d’isolation, passe souvent inaperçu jusqu’à ce qu’un entretien de routine soit effectué. Si ce problème est négligé, il peut compromettre la sécurité, causer des dommages environnementaux, des perturbations opérationnelles, engendrer des pertes financières, une non-conformité aux réglementations, réduire la durée de vie des équipements et augmenter les problèmes de maintenance. En fin de compte, ce problème peut entraîner des risques de blessures graves, voire même des pertes de vies humaines. D’après les rapports, la CUI est responsable de 40 % à 60 % des coûts de réparation des pipelines (Dey, n.d.), ce qui représente des centaines de milliards de dollars en dépenses annuelles dans le secteur.
Ce livre blanc aborde le problème persistant de la CUI. Il explore les technologies de capteurs et les techniques de surveillance avancées qui sont essentielles pour détecter rapidement et surveiller en permanence la corrosion sous l’isolation. Cette approche permet d’atténuer proactivement les dangers potentiels et de préserver l’intégrité des équipements pour que les opérations dans l’industrie pétrolière et gazière se déroulent de manière continue et en toute sécurité.

Description de la corrosion sous isolation
La CUI est une corrosion externe qui se produit généralement dans les équipements isolés fabriqués à partir d’aciers au carbone ou faiblement alliés, tels que les pipelines. Pour que ce type de corrosion se produise, deux conditions sont nécessaires :
- La présence d’eau
- La disponibilité de l’oxygène
La CUI est plus répandue dans les usines de traitement et les raffineries qui fonctionnent sous des températures fluctuantes, ce qui contribue de manière significative au processus de corrosion. De plus, l’exposition du système à des produits corrosifs en contact avec la surface du tuyau agit également comme une source de corrosion.
Le tuyau au centre de l’isolation est généralement en acier et l’isolant est constituée de matériaux ou de combinaisons de matériaux enveloppant le conduit afin de réduire de manière significative le transfert d’énergie thermique. Cette réduction efficace des pertes d’énergie permet de réaliser des économies considérables.
Isolation thermique chaud et froid pour les pipelines
L’isolation thermique empêche le transfert d’énergie du fluide chaud. La fonction principale de cette isolation est de conserver la chaleur. Elle permet également de protéger les opérateurs contre les surfaces chaudes. Les matériaux isolants thermiques couramment utilisés comprennent la laine minérale, la laine de verre et le silicate de calcium.
Par ailleurs, l’isolation contre le froid permet de réduire le transfert de chaleur de l’environnement extérieur vers la tuyauterie et de limiter les risques de condensation. Les matériaux d’isolation contre le froid les plus utilisés sont la mousse de polyuréthane ou la mousse polyéthylène.
Une bonne compréhension de la composition et de la fonction des matériaux d’isolation, tant pour le chaud que pour le froid, permet d’acquérir une connaissance fondamentale de leur rôle dans le problème complexe de la corrosion sous isolation. Bien que le rôle principal de l’isolant soit de contrôler le transfert d’énergie, lorsqu’elle est combinée à certaines conditions environnementales et opérationnelles, elle crée par inadvertance un environnement propice à la corrosion.
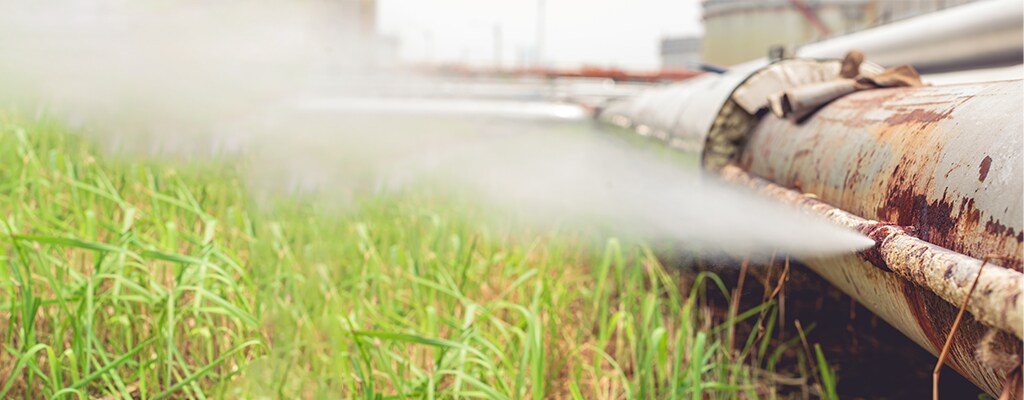
Conditions environnementales corrosives affectant une conduite isolée.
Détection traditionnelle de la CUI
Différents facteurs contribuent au développement de la CUI. L’interaction de ces éléments forme un réseau complexe de causalité qui aggrave le problème, le rendant difficile à détecter et à gérer. Examinons le fonctionnement de ces facteurs plus en détails, en mettant en évidence la façon dont leurs interactions complexes contribuent au développement de la CUI.
Tout d’abord, les conditions environnementales influencent grandement l’apparition de la CUI. L’humidité, les fluctuations de température et l’exposition au brouillard salin ou aux polluants industriels peuvent augmenter la probabilité d’intrusion d’eau dans l’isolation, condition indispensable pour développement de la CUI. Ces conditions, combinées à la température de fonctionnement de l’équipement, créent souvent les conditions parfaites pour la corrosion.
Un autre facteur critique est la qualité et le type d’isolation. Comme indiqué précédemment, les matériaux d’isolation varient considérablement, et leur efficacité ainsi que leur susceptibilité à retenir l’eau peuvent contribuer à la formation de CUI. Par exemple, les isolations poreuses (hydrophiles) ou à cellules fermées (hydrophobes) contribueront à la création de la CUI de différentes manières.
Les propriétés matérielles de l’équipement isolé, en particulier sa résistance à la corrosion, jouent un rôle central dans l’apparition de la CUI. Les aciers au carbone et faiblement alliés sont sujets à la rouille lorsqu’ils sont exposés à l’humidité, un processus qui est aggravé par les températures élevées.
De plus, les pratiques opérationnelles contribuent à ce problème. Par exemple, les équipements qui passent fréquemment d’une température élevée à une température basse peuvent provoquer de la condensation dans l’isolation, créant ainsi un environnement idéal pour la corrosion. Les méthodes d’entretien influencent également de manière significative l’apparition de CUI. Si l’isolation reste endommagée ou si l’intrusion d’humidité n’est pas traitée rapidement, le risque augmente.
Pour pouvoir formuler des stratégies efficaces de prévention et d’atténuation des dommages causés par la CUI, il est essentiel de comprendre ces interactions complexes. Avant d’aborder ces stratégies et leur efficacité, nous allons examiner plus en détail le phénomène de la CUI en présentant un cas type : la construction de conduites chaude avec isolation. Pour sécuriser physiquement l’isolation et la protéger contre les intempéries extérieures, une gaine métallique, souvent appelée « bardage », est apposée autour de l’isolation et maintenue en place par des bandes métalliques. Cette gaine est conçue pour s’enrouler autour de l’isolation, ce qui entraîne la création de joints longitudinaux ou radiaux.
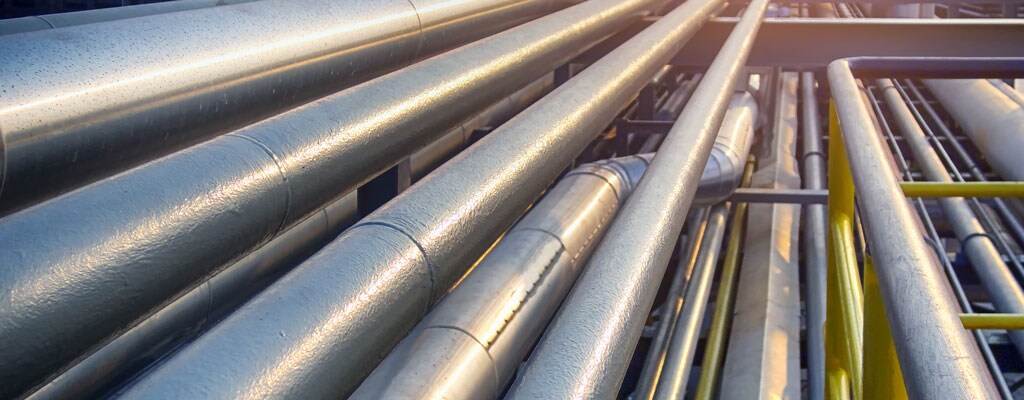
Conduite isolée avec revêtement métallique.
Les précipitations, bien qu’elles soient une cause fréquente, ne sont pas la seule source d’eau susceptible de provoquer des CUI. L’eau peut également provenir des tours de refroidissement, de la vapeur et de différents processus susceptibles d’entraîner des déversements de liquides. L’infiltration d’eau peut se produire si le revêtement est endommagé, si les joints sont défectueux ou en raison de forces externes telles que des impacts, des objets tranchants ou tombants, ou encore des personnes marchant sur le pipeline. Une fois qu’un point d’entrée d’eau existe, il n’est pas toujours immédiatement perceptible, ce qui signifie qu’en cas de pluie, l’intrusion d’eau devient inévitable.
L’interaction entre l’eau et le matériau d’isolation peut différer en fonction de la nature du matériau. Comme mentionné ci-dessus, si le matériau d’isolation est hydrophobe (une cellule fermée qui ne permet pas l’absorption d’eau), l’eau s’écoulera et restera prise en sandwich entre l’isolation et la conduite. Cette eau ne s’évapore pas toujours complètement avec le temps et certaines poches d’eau peuvent persister à certains endroits.
À l’inverse, si le matériau d’isolation est hydrophile (capable d’absorber l’humidité comme une éponge), l’eau créera une conduction thermique à travers l’éponge et la chaleur ira de la conduite au revêtement, créant un cycle d’évaporation-condensation, entraînant une augmentation de la concentration de « sel » sur le revêtement de la conduite à mesure que l’eau s’évaporera. Ce « sel », ainsi que d’autres constituants naturels de ce type de matériau d’isolation, peut dégrader la protection des conduites et entraîner de la corrosion et des fissures (connues sous le nom de fissuration par corrosion sous contrainte par chlorure CSCC) sous l’isolation.
Les contaminants, principalement les chlorures et les sulfates, sont courants sous l’isolation. Ceux-ci peuvent s’infiltrer dans les matériaux d’isolation ou provenir de sources externes. Leurs solutions aqueuses, possédant une conductivité électrique élevée, peuvent accélérer le processus de corrosion.
La température joue également un rôle central. Il est généralement admis (ou différentes sources l’indiquent) que l’acier carbone utilisé à une plage de températures de -4 °C (25 °F) à 149 °C (300 °F) présente le risque le plus élevé de CUI. Les équipements qui sont utilisés en continu à une température inférieure à -4 °C (25 °F) sont généralement exempts de corrosion. Les équipements fonctionnant à une température supérieure à 149 °C (300 °F), dépassant le point d’ébullition de l’eau, subissent une corrosion réduite car la surface de l’acier carbone reste essentiellement sèche.
Il est indispensable de comprendre l’interaction entre les matériaux d’isolation, les infiltrations d’eau, les contaminants et les variations de température pour comprendre l’apparition de la CUI. Cependant, ces connaissances ne sont pas complètes si l’on ne prend pas en compte les conséquences potentielles d’un problème non résolu. Les conséquences s’étendent au-delà de la corrosion elle-même et ont un impact non seulement sur l’aspect financier de l’industrie pétrolière et gazière, mais aussi sur les aspects liés à la santé, à la sécurité et à l’environnement.
Les répercussions de la CUI font écho à celles de la corrosion de manière plus générale. La corrosion peut provoquer des fissures qui peuvent à terme entraîner des ruptures et des fuites de produits pétroliers le long des pipelines. Cela constitue non seulement une menace importante pour le milieu environnant en raison de la pollution potentielle, mais crée également des risques pour la santé des personnes vivant à proximité des fuites. De plus, le risque d’incendie et d’explosion vient s’ajouter à une situation déjà critique.
De tels dommages sont non seulement dangereux, mais également coûteux. La réparation de ces dommages peut être à la fois financièrement lourde, en termes de dépenses d’investissement et d’exploitation (CAPEX et OPEX), et périlleuse pour les techniciens effectuant les réparations. Dans les sections suivantes, nous explorons des stratégies permettant de prévenir et d’atténuer la CUI afin de contrôler efficacement ces risques.
Il est difficile de découvrir une CUI en raison de sa nature cachée sous l’isolation et elle n’est souvent révélée que lorsqu’il est trop tard. Les méthodes traditionnelles de détection des CUI vont des techniques simples aux techniques avancées, toutes visant à découvrir la corrosion avant qu’elle ne cause des dommages importants.
L’approche la plus répandue et la plus directe de l’inspection d’une CUI consiste à couper des parties de l’isolation afin de permettre des essais non destructifs ou des inspections visuelles.
Les méthodes ci-dessous, avec leurs avantages et inconvénients respectifs, sont couramment utilisées pour détecter la CUI :
- Inspection visuelle : la méthode la plus simple et la plus couramment utilisée consiste à retirer l’isolation, à vérifier l’état de la surface du conduit et à réinstaller l’isolation. Des études indiquent que la plupart du temps, la CUI n’est pas détectée après le retrait de l’isolant. D’autres défis peuvent être le risque associé à la manipulation de l’isolation en présence d’amiante ou l’impact sur l’isolation thermique si le pipeline est en service.
- Inspection sans retrait de l’isolation : cette technique réduit considérablement le coût des inspections, car elle évite la nécessité de retirer et de réinstaller l’isolation. Des méthodes d’évaluation non destructive (NDE) sont généralement utilisées pour cette approche.
- Évaluation non destructive (NDE) : la NDE englobe diverses techniques d’inspection non invasives utilisées pour évaluer les propriétés des matériaux , des composants ou des unités de traitement entières. Diverses méthodes, telles que les courants de Foucault pulsés (PEC) et la radiographie numérique, sont utilisées pour inspecter les CUI. En règle générale, aucune méthode n’est utilisée séparément, plusieurs méthodes sont utilisées conjointement afin d’obtenir des résultats optimaux .
- Courants de Foucault pulsés (PEC) : les équipements PEC fonctionnent sur l’électromagnétisme afin de déterminer efficacement l’épaisseur moyenne de la paroi de la conduite à travers l’isolation. Cela permet la détection et la localisation des CUI. Le principal avantage du PEC est sa capacité à discerner l’amincissement général de la paroi des objets isolés sans retirer l’isolation ni préparer la surface de l’objet.
- Ondes guidées (GW) : technologie alternative pour l’évaluation des CUI sur de grandes longueurs de pipeline. Cette technologie utilise des ondes ultrasonores guidées à basse fréquence qui se propagent le long de la conduite. La corrosion interne et externe peut être détectée, mais le capteur d’ondes guidées doit être en contact direct avec la conduite, c’est pourquoi il est nécessaire de retirer une partie de l’isolation pour installer le capteur.
- Radiographie numérique en temps réel : des rayons sont émis d’un côté de la conduite isolée, ils traversent la conduite, le revêtement et l’isolation, et un capteur reçoit les rayons X de l’autre côté. Les rayons reçus par le capteur sont convertis en images en temps réel et mettent en évidence des anomalies telles que la corrosion interne ou externe, ou des défauts sur la conduite. Cette méthode peut être appliquée sans enlever le revêtement et fournit des informations en temps réel.
- Thermographie : utilisée dans l’industrie pétrochimique. Cette méthode donne une imagerie thermique d’un objet et détecte le gaspillage d’énergie qui peut être causé, par exemple, par des défauts d’isolation, des infiltrations d’eau, des fuites de gaz ou de liquide qui ont un impact sur la température de la conduite isolée.
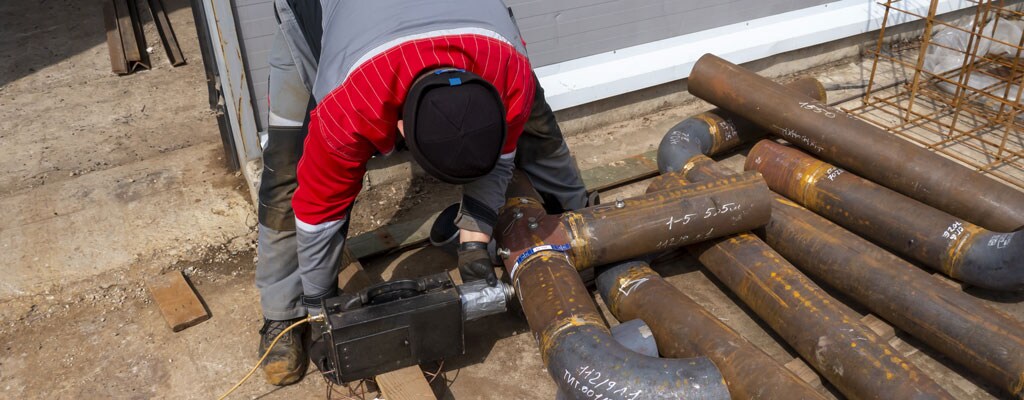
Un spécialiste installant un appareil à rayons X pour l’évaluation non destructive des joints soudés.
Bien que chacune des méthodes décrites ait des points forts uniques, elles partagent toutes des limitations inhérentes qui peuvent les rendre inefficaces pour révéler les CUI cachées sous l’isolation. Les inspections visuelles, même si elles sont simples, n’exposent que les conditions de surface, négligeant potentiellement la corrosion qui se trouve plus en profondeur. Le retrait et la réinstallation de l’isolant lors de ces inspections ajoutent des coûts importants et des problèmes logistiques, tels que la gestion de l’amiante. (Texas Nondestructive Testing Academy & Level III Services, n.d.)
Les méthodes d’évaluation non destructive (NDE), qui évaluent les propriétés des matériaux sans endommager l’isolation, sont limitées en raison de leur nature respective. Par exemple, les systèmes à courants de Foucault pulsés (PEC) offrent des informations précieuses sur l’amincissement des parois, mais peuvent ne pas détecter avec précision la corrosion localisée ni les petits points de corrosion. (Texas Nondestructive Testing Academy & Level III Services, n.d.)
La technologie des ondes guidées requiert le retrait de l’isolant à des points spécifiques, ce qui signifie qu’une corrosion se produisant ailleurs pourrait être ignorée. De plus, des facteurs tels que les revêtements à pertes élevées ou les réflexions de signaux provenant de caractéristiques telles que les soudures et les colliers peuvent avoir un impact sur l’atténuation du signal, limitant ainsi la longueur du pipeline pouvant être inspecté. (Chukwuemeka, et al., 2021)
La radiographie numérique en temps réel fournit des images des anomalies potentielles sous l’isolation, mais elle n’est pas toujours suffisamment sensible pour détecter la corrosion à un stade précoce. De plus, elle n’est utile que pour les densités de matériaux et peut ne pas révéler efficacement la corrosion de certains matériaux de conduites. (Nanan, 2020)
Les examens visuels et la thermographie, bien qu’efficaces pour identifier les dangers potentiels d’une CUI dus à une imperméabilisation ou à un revêtement endommagé, n’offrent qu’une analyse au niveau de la surface et peuvent passer à côté d’une corrosion cachée plus profondément sous l’isolation. (Fujifilm, 2022)
Le principal défi réside essentiellement dans l’incapacité de ces méthodes à fournir une évaluation complète et exhaustive de la corrosion cachée, en particulier lorsqu’elle est localisée ou à un stade précoce. En raison des limites de chaque méthode, certaines zones importantes risquent de ne pas être contrôlées et des CUI négligées peuvent continuer d’évoluer sous l’isolation.
Capteurs pour détecter les CUI
Issue de la transformation numérique de l’industrie, la prolifération rapide des dispositifs relevant de l’Internet des objets (IoT) et des systèmes interconnectés a ouvert la voie à des technologies innovantes en matière de détection des CUI, notamment par le biais de capteurs sans fil alimentés par des batteries. L’accélération de cette révolution technologique est en grande partie due à l’émergence de capteurs sans fil alimentés par batterie qui capitalisent sur les progrès de l’électronique à faible consommation d’énergie, ainsi qu’à l’introduction de protocoles de communication sans fil peu énergivores, tels que LoRaWAN, NB-IoT, LTE M et Bluetooth.
Différents principes de détection sont en cours d’évaluation, y compris des capteurs qui détectent l’hygrométrie (à la fois l’humidité et la température) entre la conduite et le revêtement extérieur, ou bien à l’intérieur ou autour d’un matériau d’isolation, par exemple une fibre optique ou un EMGR. Cependant, des défis existent, tels que les difficultés associées à l’adaptation des infrastructures existantes à la fibre optique ou à l’intégration de fils (câbles) « sacrifiés » dans l’isolation.
Ces fils « sacrifiés » sont utilisés en conjonction avec le radar à guidage électromagnétique (EMGR), où le câble se corrode en tant que préindicateur de CUI, tandis que le câble non corrosif transmet des signaux à un module sans fil placé à l’extérieur du revêtement. Cette intégration permet une connexion transparente entre les méthodes de détection innovantes et les contraintes pratiques de mise en œuvre, reflétant les complexités inhérentes à la fusion des nouvelles technologies avec les infrastructures établies.
TE Connectivity excelle dans la résolution de ces problèmes grâce à son expertise unique en matière de capteurs, en particulier sa technologie de détection d’humidité relative et ses transmetteurs sans fil. Ces capteurs, placés stratégiquement sur des conduites isolées, permettent de cartographier efficacement des infrastructures entières. Ils peuvent détecter les infiltrations d’eau et, grâce à des analyses intelligentes, simplifier la tâche consistant à repérer les zones qui nécessitent une inspection plus approfondie à l’aide de méthodes d’évaluation non destructives (END). De plus amples détails sur l’application de cette technologie dans le monde réel sont présentés dans la section consacrée aux études de cas ci-dessous.
Les efforts de collaboration dans l’industrie offrent des possibilités d’amélioration de la surveillance en temps réel. Cependant, l’efficacité de ces solutions est considérablement amplifiée lorsqu’elles sont associées aux technologies de capteurs avancées de TE Connectivity.
L’approche traditionnelle nécessite souvent des inspections coûteuses et exigeantes en ressources. Cependant, les capteurs de TE Connectivity visent à renforcer l’efficacité de ce processus et à le rendre moins exigeant, ce qui permet d’économiser du temps et de l’argent. Plus de 90 % des inspections visuelles, effectuées après le retrait du revêtement, n’aboutissent à aucune trace de corrosion. Des inspections ciblées facilitées par notre technologie de capteurs avancée peuvent ainsi permettre de réaliser des économies importantes.
Différentes entreprises peuvent avoir leurs propres stratégies d’inspection basées sur les risques. Les équipements stratégiques continueront probablement à faire l’objet d’une maintenance programmée et de méthodes d’inspection non destructive, mais les équipements moins importants pourraient voir leurs coûts de maintenance considérablement
réduits s’ils étaient équipés des capteurs sans fil à distance de TE Connectivity.
L’objectif reste de concevoir et de déployer un capteur robuste, précis, rentable et durable, capable de surveiller tous les pipelines et surfaces isolés dans les raffineries. Les capteurs de TE Connectivity, qui répondent déjà à ces critères, sont également entièrement certifiés ATEX FCE, ce qui permet un fonctionnement sûr dans des environnements potentiellement dangereux.
Progrès de la technologie des capteurs et leurs avantages
L’utilisation de technologies telles que LoRaWAN permet de récupérer les données des capteurs situés à des distances allant de quelques mètres à plusieurs kilomètres. Les opérateurs et les sociétés de maintenance peuvent détecter la corrosion de manière proactive en travaillant avec des passerelles, des analyses avancées, des stratégies de gestion centrées sur les CUI et une expertise spécialisée en matière de corrosion. Cela permet des interventions rapides et ciblées pour réparer les zones où la corrosion se produit, dans le but de gagner du temps et de réduire les dépenses, tout en garantissant la sécurité et la longévité des infrastructures.
L’intégration de tels systèmes offre de profonds avantages dans la gestion proactive de la corrosion sous isolation. Ces dernières années, de nombreuses simulations et expériences en laboratoire impliquant des capteurs d’humidité ont été menées. Celles-ci ont donné des résultats prometteurs, démontrant que les mesures d’humidité et de température pourraient en effet être efficaces pour détecter les CUI avant qu’elles ne se produisent. Chez TE Connectivity, nous sommes fiers de notre expertise en matière de technologie des capteurs, qui a joué un rôle clé dans ces avancées. Cependant, des avancées comme celles-ci ne doivent pas rester dans les laboratoires, elles doivent trouver leur place dans des applications pratiques grâce à des partenariats stratégiques solides, comme nous allons maintenant l’explorer plus en détail.
Étude de cas KAEFER
Reconnaître les graves préoccupations de l’industrie
Au cours des ces dernières années, le Groupe KAEFER, leader dans le domaine des solutions intégrées de services industriels, a mené une enquête auprès d’un large éventail de sociétés pétrolières et gazières dans le monde entier. Toutes ces entreprises avaient un point en commun : la corrosion sous isolation (CUI) était leur priorité absolue. Cette préoccupation n’était pas seulement d’ordre technique, mais avait des implications d’une grande portée, comme nous l’avons vu plus haut dans le présent document. C’est dans ce contexte qu’a pris forme notre collaboration avec KAEFER, afin de répondre à ces besoins urgents.
Solutions complètes via KIT®
Blu Empowered by KAEFER a présenté KIT® (KAEFER Integrity Technology) en tant que service global de bout en bout pour la gestion des CUI. KIT met en valeur l’expertise de KAEFER dans la gestion efficace de projets de CUI de différentes envergures. De l’optimisation complexe du placement et de l’installation des capteurs à la configuration du système, KIT se présente comme une solution complète. Mais ce qui amplifie ses capacités, c’est la technologie des capteurs de TE Connectivity.
La synergie entre les services intégrés de KAEFER et les solutions de détection avancées de TE constitue le fondement de ce partenariat innovant. La technologie de capteur sans fil de TE, dotée de caractéristiques telles qu’une longue durée de vie de la batterie et la capacité de résister à des environnements difficiles, représente un progrès significatif dans la détection des CUI. Certifiés pour répondre aux normes de sécurité les plus strictes, ces capteurs sans fil permettent de communiquer sur de grandes distances à l’aide de protocoles avancés tels que LoRaWAN™ et sont équipés de Bluetooth® Low Energy pour une configuration à distance polyvalente.
De plus, la possibilité de personnaliser les temps de mesure et la gestion intelligente des seuils illustrent l’approche avant-gardiste de ce partenariat, qui améliore la fiabilité et la précision des données tout en optimisant la durée de vie de la batterie. Avec des capteurs capables d’adapter de manière autonome leur mesure et leur transmission de données en fonction de seuils configurés, ainsi que des notifications automatiques pour la gestion de la batterie, ce partenariat s’annonce d’une grande efficacité.
Les éléments de détection de cette technologie sont méticuleusement conçus, souvent en s’appuyant sur des technologies éprouvées de capteurs d’humidité MEMS et d’ASIC, qui ont été largement utilisées dans diverses industries, notamment dans les secteurs de l’automobile, des véhicules tout-terrain et des camions. Cette application multi-industrielle met en évidence le potentiel de développement à grande échelle dans des secteurs tels que le pétrole et le gaz, permettant d’atteindre des niveaux de qualité indispensables telles que trouvé dans l’industrie automobile, et servant d’épine dorsale pour une acquisition de données efficace et une surveillance en temps réel.
KIT® : Une technologie sophistiquée
KIT propose un système de surveillance de CUI entièrement numérisé. S’il est vrai que les zones problématiques identifiées requièrent toujours des inspections traditionnelles, il est possible d’automatiser les activités sur le terrain, de réduire l’intervention humaine et par conséquent d’atténuer les risques. De plus, le système est en cours de développement afin d’inclure diverses fonctionnalités telles qu’un service de conseil et même des possibilités d’installation robotisée et autonome, grâce aux capteurs sans fil de TE fonctionnant sur batterie.
En termes de visualisation des données, KIT offre des options allant des tableaux de bord modernes aux représentations de jumeaux numériques. Ceux-ci sont enrichis par des analyses sophistiquées qui permettent de prédire la corrosion sous l’isolation ainsi que de recommander des actions de maintenance.
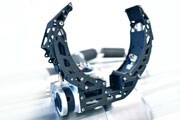
Monkeybot pour l’installation de capteurs robotiques
L’intégration de la technologie de capteurs de TE Connectivity dans KIT® n’offre pas seulement une sophistication technologique, mais également des avantages tangibles. Des études de cas ont démontré des économies significatives en termes de maintenance et d’amélioration de l’intégrité de l’installation Tous ces éléments ont pour conséquence d’augmenter les avantages pour le client, ce que KAEFER et TE Connectivity s’efforcent tous deux de réaliser.
Conclusion
Pour faire face au défi omniprésent de la corrosion sous isolation, un dilemme qui a des conséquences importantes sur l’efficacité opérationnelle, la sécurité environnementale et le bien-être de la communauté, le rôle que joue les dernières technologies ne peut pas être ignoré. Ce livre blanc a illustré les vastes impacts de la corrosion sur le secteur pétrolier et gazier, affectant non seulement les résultats financiers (dépenses d’investissement et d’exploitation [CAPEX et OPEX]), mais également les facteurs de santé, de sécurité et d’environnement (HSE).
Notre collaboration avec KAEFER constitue un point de départ, reconnaissant les besoins urgents de l’industrie en matière de solutions robustes pour gérer les CUI. KIT® de KAEFER, qui intègre la technologie de capteur innovante de TE Connectivity, offre un service global de bout en bout pour la gestion des CUI. Cet effort de collaboration illustre une approche interdisciplinaire de la résolution de problèmes, unissant diverses expertises dans un écosystème engagé à relever les défis complexes de la détection et de la gestion des CUI. Le déploiement à grande échelle de nos capteurs sans fil alimentés par batterie va au-delà de la simple prouesse technologique, il a également un impact transformateur sur l’industrie. La possibilité de réduire à la fois l’entretien programmé et les inspections visuelles inutiles amplifie la sécurité et permet de réaliser des économies importantes.
La numérisation des équipements, y compris le développement de « jumeaux numériques », nous permet de faire un bond en avant en matière de précision et de prévisibilité. Nos capteurs, soutenus par des outils d’analyse, s’alignent bien sur les systèmes et les normes existants, ce qui témoigne de notre engagement envers les avancées en matière de détection et de prévention des CUI. Cela témoigne de notre dévouement envers l’évolution continue de la technologie des capteurs et les partenariats industriels qui rendent ces avancées possibles.
Pour l’avenir, l’objectif de TE Connectivity reste clair : être le pionnier de solutions plus sûres et plus durables en tirant parti d’une technologie de pointe. Les outils de visualisation alimentés par nos capteurs intelligents sans fil offrent une vue complète de l’état des équipements, ce qui permet une transition judicieuse de la maintenance généralisée basée sur les risques vers une approche plus ciblée et axée sur les données.

Les capteurs sans fil de TE Connectivity ont été déployés et sont actuellement utilisés dans des applications de maintenance conditionnelle qui permettent la maintenance prédictive des équipements rotatifs et des têtes de puits pétroliers et gaziers.
Une plateforme intelligente complète est disponible, comprenant des capteurs de vibrations piézoélectriques simples et triaxiaux avec une gamme de fréquences allant jusqu’à 15 KHz (FFT et traitement du signal intégrés), des capteurs de température qui peuvent être insallés sur des conduites et sont capables de résister à une température externe allant jusqu’à 260 °C, ainsi que des capteurs de pression qui peuvent mesurer la pression absolue ou relative.
Ces capteurs intelligents sont entièrement configurables via la TE Sensor Toolbox ou à l’aide de votre smartphone et de l’application TE SensorConnect disponible sur l’App Store d’Apple ou le Google Play Store. Alors que nous nous tournons vers l’avenir, nous restons convaincus que notre leadership en matière de solutions de surveillance des CUI est à l’avant-garde de la transformation de l’industrie, conduisant à la fois l’efficacité et la sécurité vers de nouveaux sommets.
En associant une technologie de pointe à une expertise solide et à des partenariats collaboratifs, nous ne nous contentons pas de relever les défis d’aujourd’hui, nous façonnons les solutions de demain.
