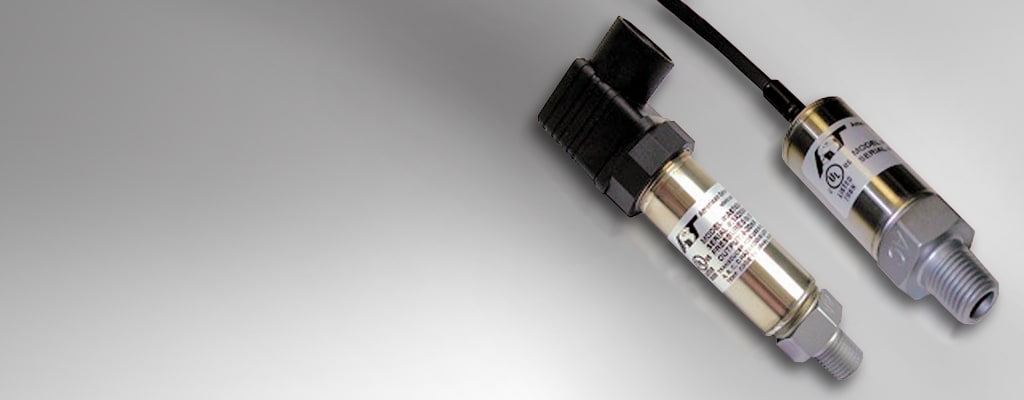
Tendance
Montée en pression
Alors que les intégrateurs de systèmes et les équipementiers s’efforcent d’accroître la fiabilité, la sécurité et les performances tout en réduisant les coûts, le besoin de capteurs intégrés dans les collecteurs, les vannes d’équilibrage, les actionneurs et les pompes est de plus en plus marqué. By: Karmjit Sidhu, Senior Director, Sensors for Oil, Gas, and Marine
Les capteurs de pression sont les deuxièmes capteurs les plus utilisés après les capteurs de température, et enregistrent une croissance notable dans les domaines de l’hydraulique, de l’eau, du médical et dans de nombreuses autres applications dans lesquelles les dimensions et les performances des produits sont des critères essentiels. Avec l’augmentation de la pression générée à l’intérieur des systèmes pour améliorer l’efficacité, ces systèmes sont de plus en plus petits. Les économies réalisées grâce à la fabrication de systèmes plus compacts obligent les fabricants de capteurs de pression à développer des solutions plus intelligentes. Les capteurs autonomes qui offrent une électronique intégrée, une protection CEM et une compensation de température sont compatibles avec les applications disposant d’un espace suffisant, mais ne conviennent pas aux systèmes compacts et miniatures.
L’isolation des composants électroniques permet d’utiliser les capteurs intégrés dans des environnements difficiles (hautes températures, vibrations, rayonnements).
Les capteurs de pression intégrés peuvent être conçus pour fournir une sortie compensée ou non compensée en fonction du prix et des performances globales visés pour le système. Certaines personnes peuvent caractériser les capteurs non compensés (en apprenant les caractéristiques de performance du capteur en matière de pression et de température) pour optimiser l’utilisation des capteurs dans leur application. Pour les capteurs non compensés, l’utilisateur a besoin de connaître certaines informations de pression et de température pour savoir précisément comment le capteur réagit, avant que les données puissent être utilisées. Les capteurs non compensés sont généralement moins coûteux et offrent davantage de flexibilité si l’utilisateur est capable de les caractériser. Les capteurs compensés sont faciles à utiliser, car les caractéristiques de pression et de température sont définies en usine. L’utilisation d’un module amplificateur est nécessaire pour obtenir la sortie souhaitée. Puisque le capteur est fourni à l’utilisateur pour fonctionner avec une précision donnée en matière de pression et de température, l’utilisateur n’a plus autant de tests ou de programmation à effectuer.
Dans la plupart des cas, l’utilisation de l’électronique à distance est généralement la plus avantageuse pour les capteurs embarqués. Selon la technologie et le milieu utilisés, l’isolation des composants électroniques permet d’utiliser les capteurs intégrés dans des environnements difficiles (hautes températures, vibrations, rayonnements). Lors de l’utilisation d’une faible impédance (jauges de contrainte piézorésistives à haut rendement en silicium inférieures à 2 kΩ), l’utilisateur peut positionner l’électronique à plusieurs mètres du capteur. Les composants en contact avec des fluides et les configurations de serrage des capteurs embarqués doivent être soigneusement vérifiés pour éviter des défaillances coûteuses. L’acier inoxydable 316L est parfaitement adapté à des applications telles que l’eau, l’oxygène, l’hydrogène et de nombreux autres milieux hostiles et critiques. Le titane et les alliages de nickel sont couramment utilisés dans le secteur médical et pour des milieux toxiques tels que les fluides corporels, le sulfure d’hydrogène et l’eau de Javel. La Figure 2 présente les configurations standard des capteurs de pression intégrés pour une utilisation dans les équipements hydrauliques et médicaux des équipementiers.
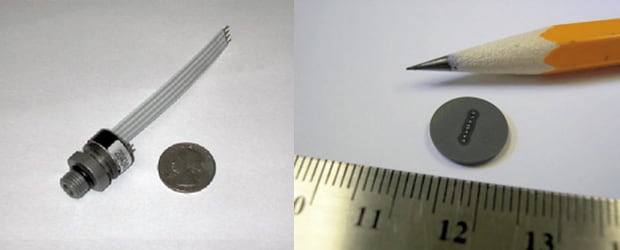
Les technologies de détection de pression jouent un rôle crucial lors de l’intégration d’un dispositif embarqué. La fiabilité et la durée de vie sont les deux facteurs clés dont dépendent les performances d’un système avec le temps. Dans certains processus du secteur médical, des semi-conducteurs ou de l’industrie, qui impliquent l’utilisation de gaz tels que l’hydrogène et l’oxygène, il est très important que le capteur de pression n’introduise pas de contamination dans le processus. La Figure 3 présente deux types de technologies de détection populaires en matière d’intégration : chaque technologie mesure la pression selon une méthode spécifique, avec différentes capacités pour contenir la pression. La principale variation est le potentiel de contamination dans le processus.
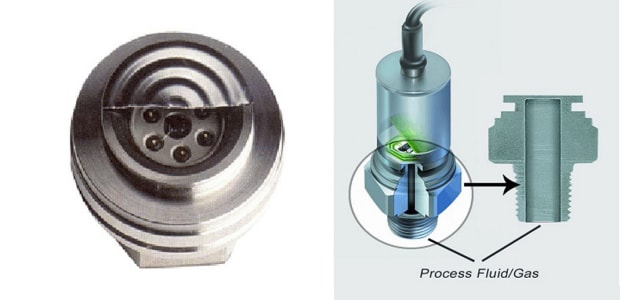
Puisque les vannes et les actionneurs sont utilisés dans des applications critiques telles que le nucléaire, l’hydraulique et l’automatisation, les capteurs de position intégrés gagnent en importance et en fréquence d’utilisation pour les retours d’information de position. La mesure de position linéaire peut aller de quelques millimètres à plusieurs mètres de long. La détection des sièges de vannes devient un domaine d’intérêt majeur en raison des normes de sécurité en vigueur dans l’industrie nucléaire et hydraulique. À l’instar de la technologie de détection de pression, le choix de la technologie appropriée pour les capteurs de position joue un rôle essentiel dans les performances et la fiabilité d’un système. Pendant des années, les capteurs de position reposaient sur une technologie de contact ou une technologie sans contact. Dans les technologies de contact comme les potentiomètres linéaires, un élément coulissant se fixe à un élément en mouvement, ce qui crée un contact direct avec le dispositif résistif. Le potentiomètre agit comme un diviseur de tension et fournit une sortie dont la tension peut varier entre 0 et 100 % de la tension appliquée lorsque l’élément coulissant se déplace d’un bout à l’autre de l’appareil. Ces appareils sont généralement moins coûteux, mais ne conviennent pas aux environnements exposés à de fortes vibrations et doivent être protégés contre la poussière et les liquides. Les technologies sans contact comme l’optique, la réluctance variable, les courants de Foucault, la magnétorestriction et les LVDT (linear variable differential transformers) ont été utilisées avec succès. Ces appareils offrent des performances et une fiabilité bien supérieures par rapport aux potentiomètres. Les capteurs optiques basés sur un interféromètre laser, sur la longueur d’onde et sur la modulation d’intensité sont utilisés uniquement dans des conditions de laboratoire et conviennent aux milieux difficiles. Les capteurs à réluctance variable sont parfaitement adaptés à des variations importantes de température, mais leur nature non linéaire ne leur permet de fonctionner que sur une plage de détection restreinte. Les dispositifs à courants de Foucault peuvent fonctionner à des fréquences plus élevées et impliquent que l’électronique de traitement du signal soit placée à proximité du capteur. La capacité de l’appareil à fonctionner sur une plage étendue de températures et de rayonnements est ainsi limitée. Les capteurs magnétorestrictifs affichent d’excellentes performances, mais sont limités à la température de fonctionnement en raison de la proximité de l’électronique de traitement du signal.
Pendant des années, les LVDT ont été utilisés dans des applications d’aviation commerciale et militaire telles que les volets hypersustentateurs, les pompes à carburant et les trains d’atterrissage, des systèmes dans lesquels la fiabilité est essentielle. Ces appareils utilisent des circuits magnétiques à basse fréquence (3 à 5 kHz) et ne génèrent aucun bruit radiofréquence par rapport aux capteurs linéaires à courant de Foucault ou à d’autres capteurs linéaires à haute fréquence. Le fonctionnement à basse fréquence permet à ces capteurs d’être placés à plusieurs mètres de l’électronique. Étant donné que le dispositif LVDT utilise un couplage magnétique entre les bobines primaires et secondaires et qu’il n’utilise aucune connexion physique, ces capteurs peuvent être étanches à l’eau, la poussière et la glace. En utilisant l’électronique moderne basée sur des circuits ASIC (application specific integrated circuits), la longueur du capteur peut être considérablement réduite sans compromis sur les performances maximales. Les ASIC permettent de traiter numériquement le signal avec une compensation complète sur une large plage de températures. Cette technologie a permis d’utiliser des capteurs linéaires sans contact dans des espaces restreints tels que les sièges de vannes et les duses sous-marines dans la détection des cylindres. La Figure 4 présente deux capteurs de position sans contact pouvant être intégrés à des vannes et des transmissions.
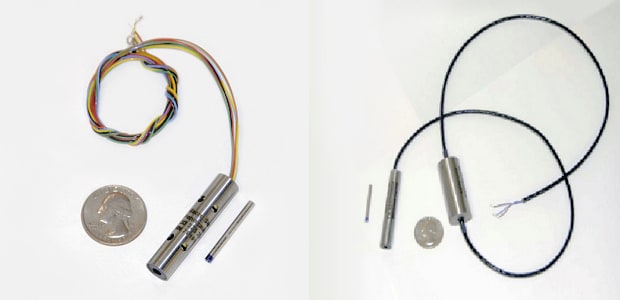