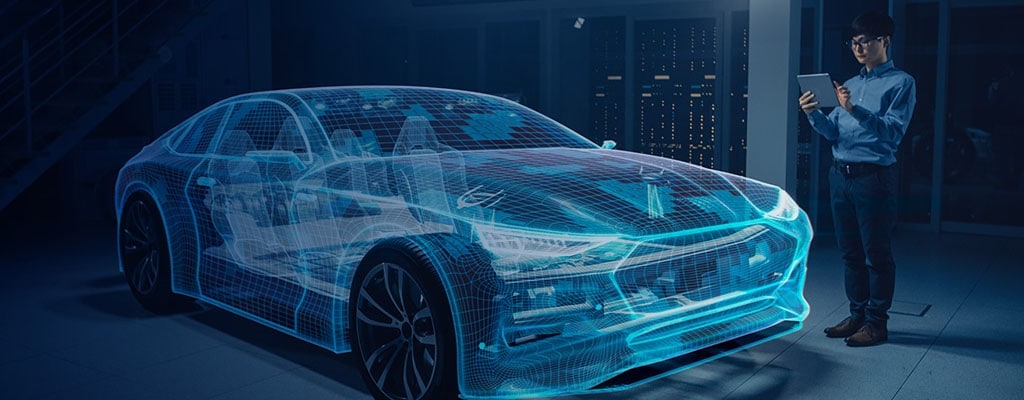
Tendance
Des solutions conçues pour les températures extrêmes
Les interconnexions permettent des gains de poids sans précédent pour les applications de sport automobile. Par : Paul Webb, Sales and Marketing Manager, Autosport
En Formule 1 et dans d’autres sports automobiles, la réduction de poids est essentielle pour devancer les concurrents. Quelques grammes de moins ici et là peuvent se traduire par un grain de poids global considérable. La tendance est également à l’embarquement de composants électroniques plus compacts. Alors que l’électronique occupe une place de plus en plus importante dans les voitures, la miniaturisation des pièces apparaît comme une évidence pour optimiser l’utilisation de l’espace. Les faisceaux électriques et les systèmes d’interconnexion permettent d’alléger ces pièces et de les rendre plus compactes. Tout d’abord, les connecteurs et les câbles doivent présenter une conception robuste, capable de résister à des températures et des vibrations extrêmes, ainsi qu’au contact avec les liquides d’une manière générale et le liquide de nettoyage des freins en particulier.
Évolution des connecteurs
L’évolution de la gamme de connecteurs DEUTSCH AS de TE Connectivity (TE) illustre bien la miniaturisation des connecteurs. Les connecteurs plus petits sont généralement plus légers, d’où l’intérêt pour le développement de connecteurs plus compacts. Les coques en acier inoxydable ont cédé la place à l’aluminium léger, voire à un composite encore plus léger. La taille de pièces telles que les bagues d’accouplement a été réduite. Plus les connecteurs sont petits, plus la question de l’ergonomie se pose, avec par exemple l’adaptation des molettes pour permettre à un technicien portant des gants de connecter et déconnecter les connecteurs de façon rapide et précise. Les connecteurs à coque composite sont une bonne solution pour réduire le poids. Lorsque l’industrie a commencé à s’intéresser aux connecteurs composites, leurs performances n’étaient pas à la hauteur des attentes du marché du sport automobile. Les composites notamment se dégradaient au contact du liquide de nettoyage des freins. Les concepteurs ont donc cessé de les utiliser. Les composites évoluent. Ils ont été considérablement améliorés, et la nouvelle génération répondra bientôt pleinement aux besoins de la course automobile. Il convient de réévaluer les gains de poids permis par les composites ainsi que les besoins mécaniques et environnementaux des sports automobiles auxquels ils répondent.
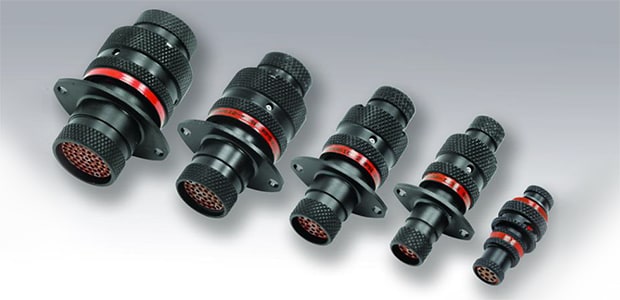
L’utilisation de composites a permis de réduire le poids des connecteurs d’environ 40 %. En optimisant le matériau de renforcement et en introduisant de la mousse dans les matrices polymères, il est possible de réduire encore le poids de 10 à 20 %. Le matériau fibreux et la longueur des fibres de renforcement jouent un rôle important dans la détermination de la résistance de la pièce finie. Des matériaux plus résistants permettent d’obtenir une paroi plus mince et donc de réduire le poids. L’introduction d’agents moussants ou de microsphères dans un composite polymère, même si elle est plus difficile lorsque le volume de fibres de renforcement augmente, est désormais possible. Les câbles à paroi mince haute performance sont déjà la norme pour la course automobile. Un câble standard, tel que le câble SPEC 55 de TE, utilise une isolation et une gaine ETFE réticulées capables de résister à des températures allant jusqu’à 150 °C ou 200 °C et présente une excellente résistance aux liquides. La construction à paroi mince allège le câble sans compromettre ses performances. L’industrie automobile commerciale et l’armée commencent à utiliser des câbles en aluminium pour alléger les composants, mais cette utilisation n’est pas encore généralisée dans le sport automobile.
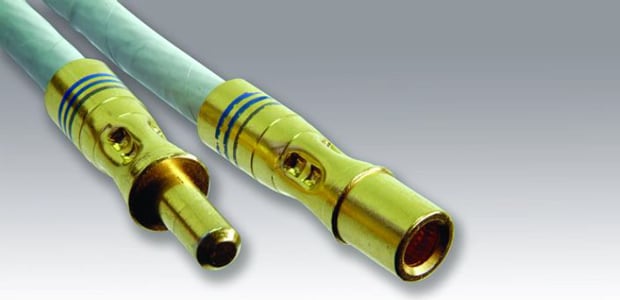
Le fil d’aluminium est considéré comme difficile à travailler. Son rayon de courbure n’est pas aussi étroit que celui du cuivre et la fiabilité de sa terminaison reste problématique en raison du fluage à froid. Certains contacts résistent toutefois au fluage à froid et assurent une connexion fiable et étanche aux gaz. La conductivité de l’aluminium étant 40 % inférieure à celle du cuivre, un conducteur plus grand est nécessaire pour obtenir la même intensité de courant admissible. Même en tenant compte de cela, l’aluminium est environ 50 % plus léger que le cuivre.
Bruit électrique
Trois approches pour remédier aux IEM
Le blindage est rarement utilisé dans les voitures de course, mais les nouvelles technologies génèrent de nouveaux niveaux de bruit électrique auxquels il convient de trouver une solution. Les systèmes de récupération d’énergie à courant élevé, par exemple, sont source d’interférences électromagnétiques (IEM).
1
Éloignement
Éloigner la source d’IEM des fils et des composants électroniques sensibles. Compte tenu de l’espace limité dans une voiture, cette approche est inapplicable dans la majorité des cas.
2
Blindage
Le blindage augmente le poids, c’est pourquoi les câbles blindés ne sont utilisés que ponctuellement. Une gaine tressée en cuivre peut être glissée sur le câble et raccordée au capot d’un connecteur. La tresse forme un chemin à faible impédance de la terre aux IEM. TE a récemment développé un système de tresse jusqu’à 50 % plus léger qu’une tresse traditionnelle.
3
Fibre optique
La fibre optique est naturellement insensible aux IEM. De plus, les câbles à fibre optique sont nettement plus légers que les câbles en cuivre. Les fibres optiques en verre et en plastique peuvent être utilisées en sport automobile. Les fibres de verre ont l’avantage d’offrir une bande passante et une plage de températures de fonctionnement plus élevées (certaines fibres spéciales sont conçues pour résister à des températures atteignant 700 °C), mais elles sont plus difficiles à travailler. Bien que les câbles en fibre de verre soient robustes et qu’il existe des modèles renforcés, il convient de les acheminer avec précaution et de respecter les rayons de courbure. La structure d’un câble peut remédier à bon nombre de ces inconvénients et permettre aux câbles en fibre de verre de résister aux conditions extrêmes de la construction, de l’entretien et de la conduite d’une voiture de course. Les fibres optiques en plastique sont moins coûteuses, qu’il s’agisse du câble lui-même ou des émetteurs-récepteurs électroniques associés. Largement utilisées aujourd’hui dans les réseaux automobiles commerciaux, elles résistent également mieux aux fortes contraintes mécaniques et aux rayons de courbure étroits. Leur principal inconvénient est leur plage de température : un câble POF standard est conçu pour résister à une température maximale de 85 °C tandis que d’autres modèles peuvent supporter jusqu’à 125 °C.
Solutions intégrées
Si la conception des connecteurs composites doit être repensée, il en va de même pour les boîtiers composites en tant qu’alternative viable à l’aluminium pour les unités de commande électroniques et d’autres systèmes. Le principal atout des boîtiers composites est leur légèreté : un boîtier composite en polysulfure de phénylène avec un remplissage carbone peut être 40 % plus léger qu’un boîtier en aluminium. Les matériaux composites sont solides et peuvent être adaptés pour offrir une résistance exceptionnelle aux chocs, à la traction, à la flexion, etc. Leur résistance au bosselage et aux déformations les rend plus robustes que les modèles en aluminium. Les boîtiers composites offrent tous les avantages mécaniques et électriques du métal, tout en étant plus légers, plus résistants à la corrosion et moins coûteux.
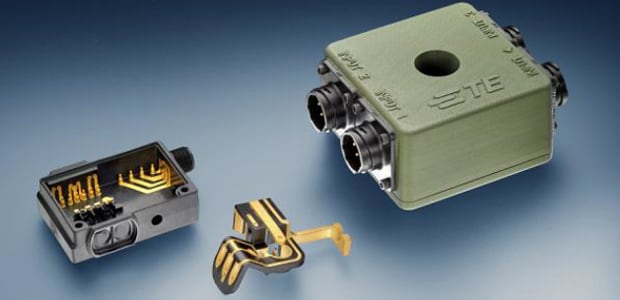
Nos innovations en matière de technologies et de matériaux vous offrent de nouvelles possibilités. Les matériaux de remplissage, allant de la fibre de carbone traditionnelle aux microsphères et aux nanotubes de carbone, permettent de créer un boîtier sur mesure pour obtenir le meilleur équilibre entre le poids et les performances électriques, mécaniques et environnementales. Le moulage avancé permet de créer des entretoises, des coques de connecteurs intégrées, des séparations et d’autres éléments tridimensionnels. La métallisation sélective permet une intégration économique des pistes de circuit imprimé, du blindage et même des antennes incorporées. Le moulage tridimensionnel et la métallisation sélective permettent une plus grande diminution du poids que la simple utilisation de composites.
Conclusion
La technologie d’interconnexion continue de progresser, permettant des gains de poids sans précédent dans le domaine du sport automobile. Plus important encore, d’anciens procédés font leur retour. Des technologies jugées limitées à certains égards ont évolué. Ne vous fiez pas aux idées reçues. Les connecteurs et boîtiers composites, la fibre optique, les tresses de blindage et le fil d’aluminium méritent tous que l’on s’y intéresse à nouveau. L’un des avantages de la collaboration avec TE est que nous adoptons une approche systémique des interconnexions. En ajoutant quelques grammes à un endroit, on peut alléger l’ensemble de plusieurs kilos. Car c’est le produit final qui gagne la course, pas les composants individuels.