Les capteurs améliorent notre capacité à observer et à décrire le monde qui nous entoure. Le point de vue d’un capteur permet de différencier l’imaginaire du possible.
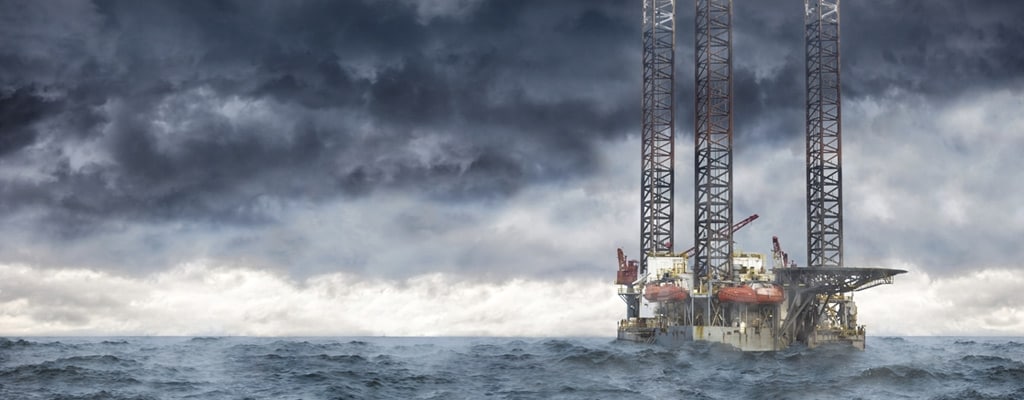
Présentation
Fiabilité extrême
La fabrication d’émetteurs capables de fonctionner à des températures extrêmes commence par le développement d’un capteur conçu pour résister aux environnements les plus difficiles.
L’environnement d’exploitation joue un rôle majeur dans le fonctionnement continu et la précision des transmetteurs de pression. S’ils ne sont pas spécifiquement conçus pour supporter des conditions environnementales telles que les régions subarctiques ou les liquides gelés, les transmetteurs de pression peuvent tomber en panne prématurément et causer de très graves défaillances d’équipement. Les fiches techniques du transmetteur de pression fournissent certes des informations sur les performances du capteur dans des conditions ambiantes, les mesures attendues dans une plage de température donnée, ainsi que divers termes et acronymes précisant les performances du transmetteur de pression dans différentes conditions, mais une compréhension approfondie de la construction du transmetteur permettra de définir le fonctionnement du capteur dans des environnements extrêmes, notamment dans des conditions de faibles températures.
Découvrez notre transducteur de pression hydraulique M9100, capable de mesurer des pressions de fluide pouvant atteindre 700 bar dans des conditions extrêmes.
Les transmetteurs de pression utilisent généralement des jauges de contrainte de forme spécifique et montées sur un diaphragme pour mesurer la pression. Pour fixer ces jauges, différentes techniques peuvent être utilisées : colle, dépôt de couche mince, bain d’huile, processus de cuisson en verre. Lorsque le diaphragme se déforme, les valeurs de résistance changent. Dans tous les cas, les effets de la température peuvent également modifier la résistance de ce signal de sortie et créer des problèmes au niveau du capteur.
La résistance des capteurs peut être testée dans des climats froids. Des températures inférieures à -20 °C (-4 °F) peuvent entraîner le gel et le durcissement des capteurs à huile. La technologie céramique peut induire le durcissement et la fragilisation du joint torique entre le port usiné et le diaphragme. Elle compromettrait donc l’intégrité de l’élément de détection et risquerait de former un trajet de fuite. Pour éviter que le capteur n’atteigne une température inférieure à sa plage de température de fonctionnement, son emplacement et son environnement doivent être modifiés. Le capteur peut être placé dans un boîtier chauffé ou une pièce chauffée afin de le protéger et d’éviter qu’il n’atteigne une température de gel. Dans certains endroits isolés, il peut être difficile de trouver une source d’alimentation pour les instruments fonctionnant à l’énergie solaire. La capacité de chauffage du capteur sera donc limitée, voire inexistante. En Alaska, en Alberta, en Colombie-Britannique, en Saskatchewan et dans le Dakota du Nord, par exemple, les systèmes de puits connaissent parfois des températures qui peuvent atteindre -50 °C (-60 °F), alors que des capteurs sont installés à l’extérieur, directement sur la tuyauterie, pour surveiller la pression hydraulique, la pression du tubage et la pression du boîtier dans la tête de puits.
Les opérations souffrent du gel
Le gel d’un support de traitement est la conséquence indirecte d’un climat froid. Dans certaines applications de forage de gaz naturel, un même tuyau peut transporter de l’eau et du gaz. Lorsque le système est à l’arrêt et que la température descend au-dessous de zéro, l’eau à l’intérieur du tuyau peut geler, gagner en volume et provoquer une surcharge du capteur de pression pendant une période prolongée. Cette augmentation du volume peut induire un pic de pression de 500 psi (35 bar) à 1 000 psi (70 bar). Pour un système de 100 PSI, la pression peut augmenter jusqu’à 1 500 psi (100 bar). Dans de nombreuses technologies de détection, l’application de cette contrainte sur un diaphragme à pression plus faible entraînera une défaillance de la jauge de contrainte ou une rupture du diaphragme. Pour éviter toute défaillance du capteur, la hausse de pression doit être assumée par l’élément de détection pendant un certain temps sans qu’elle affecte la précision du capteur après le dégel du support. La conception spéciale de la cavité, la capacité de résistance à la pression et l’étalonnage sont les meilleurs moyens de garantir que le capteur ne tombera pas en panne à la suite du dégel du support dans la cavité.
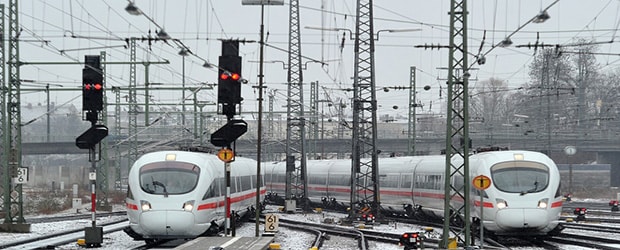
Compensation de la température
Pour compenser électriquement les variations de température, les fabricants de transmetteurs de pression testent les capteurs à différentes pressions et températures afin que ces derniers s’adaptent aux effets de la température. Puisque chaque capteur et chaque jauge de contrainte est unique, il est recommandé de tester les propriétés spécifiques de chaque capteur. La méthode classique consiste à ajuster ou à réduire le signal de sortie brut à l’aide de résistances afin d’optimiser les performances sur la plage de température testée. Ainsi, le capteur utiliserait un ensemble de cartes de circuit imprimé qui amplifie le signal millivolt au signal de sortie requis (par ex., 4-20 mA). Le réglage du zéro et de la portée sera disponible sur certains transmetteurs de pression. Cette fonction est généralement nécessaire pour les signaux de sortie dérivés en cas de fatigue du diaphragme. La diminution du coût et des dimensions de l’électronique numérique a entraîné l’augmentation de l’utilisation de la compensation numérique grâce à l’utilisation des ASIC (circuits intégrés spécifiques à l’application). L’ASIC est programmé en cas de faible température, car le capteur de pression est testé en fonction de la température. Certaines conceptions corrigent la non-linéarité ou les écarts par rapport au signal de sortie idéal. La température de l’ASIC peut être compensée au niveau des jauges à l’aide d’un capteur de température (par ex., une thermistance) ou au niveau de l’ASIC lui-même. La principale différence est la température du support. Si elle est compensée en fonction de la température de l’ASIC, la proximité avec le support affectera la précision de la mesure. Dans les climats froids, l’ASIC pourrait effectuer des relevés à une température proche de la température ambiante, et le milieu pourrait être un liquide ou un gaz chaud. La mesure de la température des jauges produit la réponse et la compensation dynamique les plus rapides, optimisant ainsi les performances.
Une autre avancée de fabrication associée aux transmetteurs de pression est la capacité de fournir un signal de sortie de température indépendant. Les intégrateurs de systèmes peuvent désormais surveiller de près les variations de température du support à partir d’un seul appareil, ce qui réduit le coût d’installation et le coût du capteur supplémentaire. Sur l’image de gauche ci-dessous, vous pouvez voir un élément de détection en acier inoxydable en une seule pièce, usiné sans soudures ni joints toriques internes. L’absence de soudures et de joints dans cette conception diminue fortement la valeur de fatigue sur une température de fonctionnement large. Fabriqués avec des diaphragmes très épais et des jauges de contrainte en silicium à la pointe de la technologie, ces transmetteurs de pression antidéflagrants offrent des résultats reproductibles même dans des environnements difficiles de forage de puits profonds, comme le montre l’image ci-dessous. L’ajout de pièces mouillées en alliage 718, 17-4 PH, alliage C-276 et 316 L SS étend encore l’utilisation de ces transmetteurs de pression dans le traitement du pétrole lourd et de la sulfuration élevée.
RÉCAPITULATIF
Comme pour la conception de l’ensemble du système, la compréhension des détails permettra d’améliorer la prise de décision. Même si les transmetteurs de pression peuvent se ressembler en termes de format et de dimensions, le mode de mesure de la pression d’un point de vue mécanique et électrique peut être très différent. Les matériaux utilisés peuvent également varier, ce qui implique une analyse approfondie. Contactez votre fabricant de transmetteurs de pression pour trouver une conception adaptée à vos besoins.