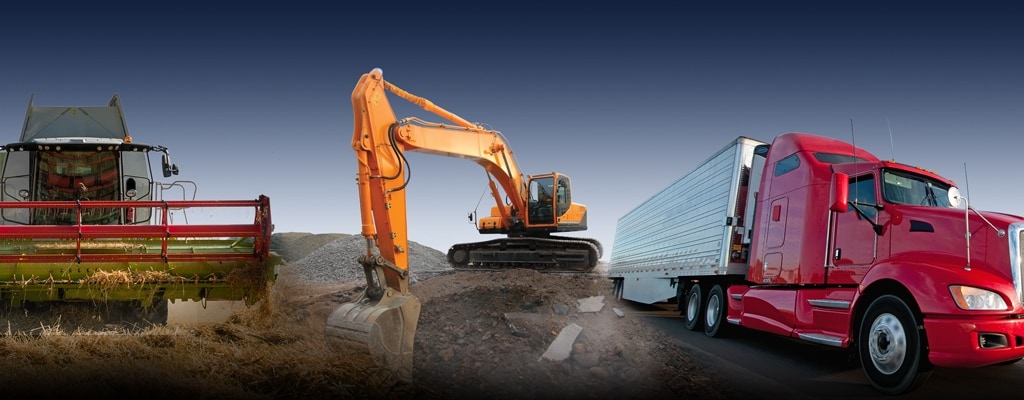
Tendance
Données à grande vitesse dans des environnements difficiles
Pour garantir la transmission de données à grande vitesse dans les véhicules commerciaux, vous ou vos concepteurs devez examiner attentivement les composants, leur emplacement et l’impact des conditions environnementales dès le début de la conception. Lisez notre article pour en savoir plus.
AUTEUR
Christian Manko, Chef de produit, Connectivité des données, TE Connectivity
La technologie progresse
Les clients exigent des fonctionnalités qui automatisent ou améliorent les tâches opérationnelles afin d’accroître la productivité et la sécurité des conducteurs et, dans de nombreux cas, elle permet aussi de réduire le coût total de possession. Les fonctionnalités telles que le freinage et la direction adaptatifs automatiques, les diagnostics embarqués, la communication de type véhicule-à-véhicule (V2V) et de type véhicule-à-infrastructure (V2I), ainsi que les caméras qui offrent au conducteur une vue à 360 degrés de son environnement deviennent des exigences de base des clients.
Ces fonctionnalités nécessitent que de grandes quantités de données soient transmises à grande vitesse. Alors que les ingénieurs conçoivent de nouveaux modèles pour répondre à ces demandes des clients, le défi consiste à assurer l’intégrité du signal et la transmission des données dans l’environnement difficile des secteurs du camionnage et du tout-terrain.
Application d’Ethernet dans une architecture mixte
Pour gérer l'augmentation des demandes de données et la connectivité à grande vitesse, une infrastructure réseau sophistiquée est nécessaire. Les architectures de bus CAN, qui gèrent généralement des vitesses allant jusqu’à 500 Kbit/s, constituent la solide structure centrale des réseaux de communication de la plupart des véhicules lourds depuis quelques décennies. Cependant, la bande passante de données requise pour les fonctionnalités avancées des véhicules et les fonctionnalités automatisées pour la sécurité et la productivité est trop importante pour être servie par l'architecture CAN seule.
Le protocole Ethernet à paire unique (100BASE-T1 à 100 Mbit/s ou 1000BASE-T1 à 1 Gbit/s) permet de transmettre des données à des vitesses élevées. L’utilisation de réseaux et de connecteurs Ethernet permet aux concepteurs OEM d’intégrer facilement davantage d’appareils sur le réseau et d’accélérer la connectivité des données dans leurs véhicules. En tant que topologie point-à-point, Ethernet modifie l’architecture électrique et électronique (E/E) du véhicule. Au fur et à mesure que les équipementiers OEM décideront d’ajouter plus de fonctionnalités et de périphériques, les concepteurs devront également prendre en compte les commutateurs Ethernet afin de diriger le signal et les passerelles pour une communication entre Ethernet et le bus CAN.
Pour optimiser l’espace, le poids et les performances dans des conditions difficiles, les concepteurs doivent prendre en compte, dès les premières étapes de la conception, comment ils intégreront Ethernet là où cela est nécessaire pour les fonctionnalités avancées. Des décisions telles que le nombre de câbles à placer à l’intérieur du véhicule et leur emplacement, l'emplacement des commutateurs Ethernet et s'ils doivent être dans une unité de commande électronique (ECU) existante ou dans une nouvelle ECU dédiée, doivent être prises pour chaque fonctionnalité qui requiert Ethernet. Ceci est crucial pour éviter ou atténuer les problèmes d’interférences électromagnétiques (IEM) ou d’autres perturbations mécaniques.
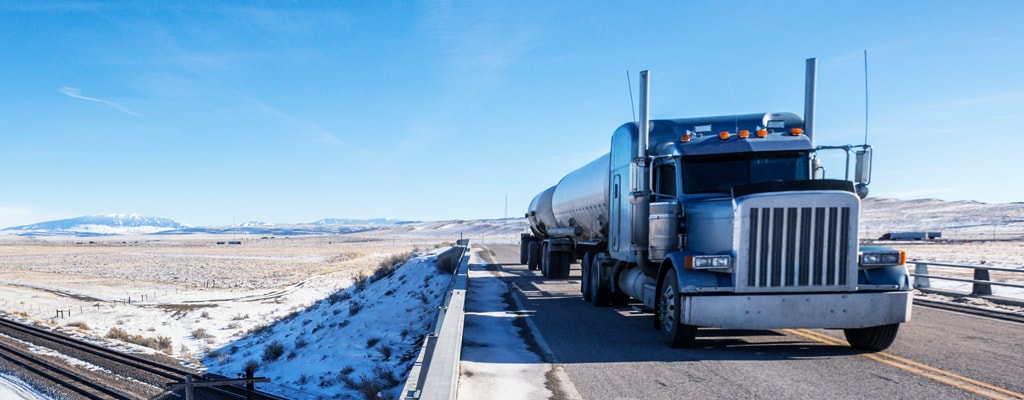
Par exemple, Les caméras à 360 degrés d’un véhicule lourd transmettent des données à grande vitesse de l’extérieur du véhicule à l’écran de l’habitacle pour que le conducteur puisse les voir. Quatre caméras (une de chaque côté du véhicule) envoient des signaux à une ECU. Les concepteurs doivent planifier l'emplacement d'un commutateur pour combiner les données des quatre caméras et envoyer ces données en un seul signal à l’ECU. Le commutateur peut se trouver dans le véhicule ou dans l’une des caméras, qui aurait quatre ports pour faire entrer les données des trois autres caméras, puis envoyer des données. Une autre option consiste à intégrer le commutateur dans le moniteur d’affichage vidéo.
Avec des fonctions automatisées actives telles que le freinage adaptatif automatique et d’autres systèmes avancés d’aide à la conduite (ADAS) qui incluent un réseau multicapteur, réfléchir à la conception à un stade précoce est encore plus essentiel. Chaque capteur aura une liaison de communication dédiée à une ECU. Plus le véhicule dispose de capteurs, plus il faut de câbles et de liaisons de communication. Un véhicule lourd autonome du futur aurait besoin d’un large réseau de capteurs pour environ 16 radars, 10 lidars et 10 caméras tout autour du véhicule. Cela représente plus de 30 câbles et liaisons qui doivent être résistants aux interférences électromagnétiques et acheminés intelligemment tout en tenant compte de l’espace, du poids et des interférences électromagnétiques afin de maintenir l’intégrité du signal à l’intérieur et à l’extérieur du châssis et lorsque les liaisons arrivent dans une ECU. Plus de données signifie plus de besoins en bande passante et par conséquent, des connecteurs et des câbles qui peuvent également gérer une plus grande vitesse.
La taille immense des véhicules industriels et commerciales représente un défi pour maintenir l’intégrité du signal et transmettre les données de manière fiable. Pour la transmission d’un signal Ethernet dans les voitures, la norme Ethernet spécifie des exigences techniques jusqu’à 15 m (49 pieds). Mais dans les camions, les bus et les véhicules tout-terrain, l’intégrité du signal doit être maintenue sur de plus grandes longueurs, jusqu’à 40 m (131 pieds), tout en résistant aux fortes vibrations, aux températures et aux chocs extrêmes, aux conditions avec de la poussière épaisse, etc.
La norme Ethernet spécifie actuellement jusqu’à quatre connexions en ligne le long de ces 40 mètres ; il revient aux concepteurs d'évaluer la longueur de chaque segment pour maintenir l'intégrité optimale du signal. L'exposition à des éléments extérieurs ou à des températures élevées ou le placement près d’une antenne ou d’autres composants susceptibles de causer des interférences électromagnétiques sont des facteurs affectant l'intégrité du signal. L'acheminement est un élément clé de la conception et l’ensemble de la couche physique doit être mis à l’échelle pour obtenir les performances attendues.
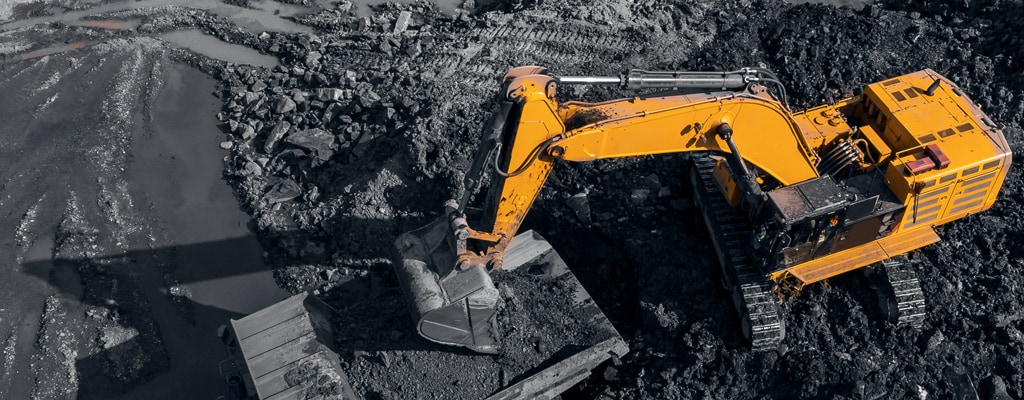
Achetez nos solutions pour les véhicules commerciaux lourds connectés
Choisir les bons composants
« Lors de la conception d’une architecture mixte avec un bus CAN et Ethernet, les ingénieurs doivent réfléchir à l’avance à l’ensemble de l’infrastructure de connectivité en termes de fonctions avancées et gourmandes en données qu’ils intégreront » explique Abbas Alwishah, responsable de l’ingénierie, Connectivité des données, chez TE Connectivity. « Plus la technologie est avancée, plus la collaboration entre les équipementiers OEM et les fournisseurs est importante. Si un client me dit qu’il a besoin d’une caméra haute définition ou d’un système de détection de proximité qui fonctionne avec une latence très faible, je peux expliquer tous les composants individuels nécessaires à cette fonction ou à ce système (capteurs, connecteurs, câbles préassemblés, antennes, processeurs, écran, etc.) et faire des recommandations sur la topologie pour optimiser les performances, l’espace, le poids et les coûts.
Le choix de composants compatibles Ethernet capables de résister à des conditions difficiles est essentiel pour une transmission fiable des données dans les véhicules lourds qui ont une longue durée de vie. Les connecteurs Ethernet automobiles (ceux conçus à l’origine pour les véhicules de tourisme) peuvent être utilisés dans l’habitacle ou dans d’autres parties du véhicule non exposées à des chocs extrêmes, à la température ou à d’autres éléments, où des connecteurs plus robustes et des câbles de plus grande longueur ne sont pas nécessaires. Un câble à paire torsadée non blindée de haute qualité convient à Ethernet dans la plupart des parties du véhicule, avec des câbles à paire torsadée blindés utilisés uniquement lorsque cela est nécessaire. Les choix du concepteur permettent également de contrôler les coûts, d’économiser de l’espace et de réduire le poids.
Par exemple, les connecteurs MATEnet modulaires et évolutifs développés par TE pour Ethernet automobile peuvent également être utilisés dans les véhicules commerciaux lourds pour des applications nécessitant des volumes de données de taille moyenne à grande et à faibles latences, comme les diagnostics embarqués (technologies V2X), la télématique, l’info-divertissement de tableau de bord, ADAS, etc. Les connecteurs peuvent transmettre des données à une vitesse de 100 Mbit/s à 1 Gbit/s (selon les protocoles IEEE 100BASE-T1/1000BASE-T1) et peuvent être utilisés avec des câbles à paires torsadées blindés ou non blindés.
Les composants sur châssis nécessitent plus que de la robustesse. Ils doivent faire preuve de fiabilité mécanique, pouvoir être réparés, résister aux températures extrêmes et fonctionner efficacement avec des canaux de plus grande longueur. En cas de fréquences plus élevées, la qualité du câble/du connecteur et la conception peuvent avoir un impact significatif sur les performances du canal, ce qui affecte les performances du système et en retour, les performances de l'application. En particulier pour les composants sur le châssis, les ingénieurs doivent opter pour des câbles et des connecteurs spécifiquement conçus pour une transmission des données à grande vitesse dans des environnements difficiles.
« Lorsqu'ils essaient de répondre à des besoins en résilience mécanique, certains ingénieurs peuvent aussitôt penser à ajouter un boîtier plus grand et plus robuste, mais des parois plus épaisses peuvent avoir un impact négatif sur les performances électriques, » déclare Mark Brubaker, Chef de projet, Connectivité des données, chez TE. « Il est important de regarder ce qui a marché dans le passé, mais également d'aller plus loin afin de comprendre cette nouvelle génération de besoins électriques pour transmettre des données à grande vitesse et tester les performances des connexions étant donné les fréquences plus élevées impliquées. »
Le choix et le placement du produit ne peut pas être une réflexion après coup lors de la conception de fonctionnalités automatisées et avancées qui nécessitent une transmission des données à grande vitesse. En ajoutant Ethernet à des architectures de véhicules lourds, les concepteurs doivent réfléchir aux complexités impliquées et à leur planification bien avant et bien plus en profondeur qu'avant pour obtenir un bon équilibre entre fiabilité et résilience mécanique avec des exigences électriques pour les données à grande vitesse et de plus grandes longueurs de canaux, ainsi que pour les besoins d'entretien.
Pour en savoir plus sur nos solutions pour véhicules connectés
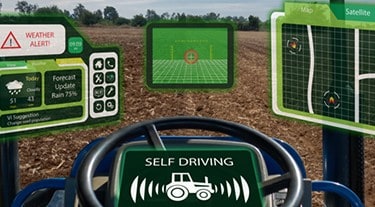
Conduite autonome
Solutions Ethernet
Découvrez en plus sur les exigences de connectivité pour permettre la conduite autonome des véhicules commerciaux et industriels.
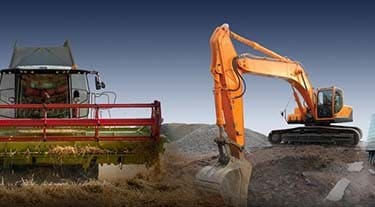
Connectivité des données
Solutions pour véhicules lourds
Découvrez pourquoi les ingénieurs concepteurs doivent envisager d’intégrer des systèmes Ethernet dans leurs véhicules et machines industriels et commerciaux pour répondre aux besoins des futurs clients.
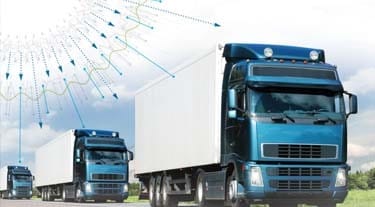
Connectivité Ethernet
Exigences pour véhicules lourds
Découvrez les considérations que nous avons prises pour concevoir nos connecteurs Ethernet pour les véhicules lourds.
Publié à l’origine dans Truck et Off-Highway Engineering