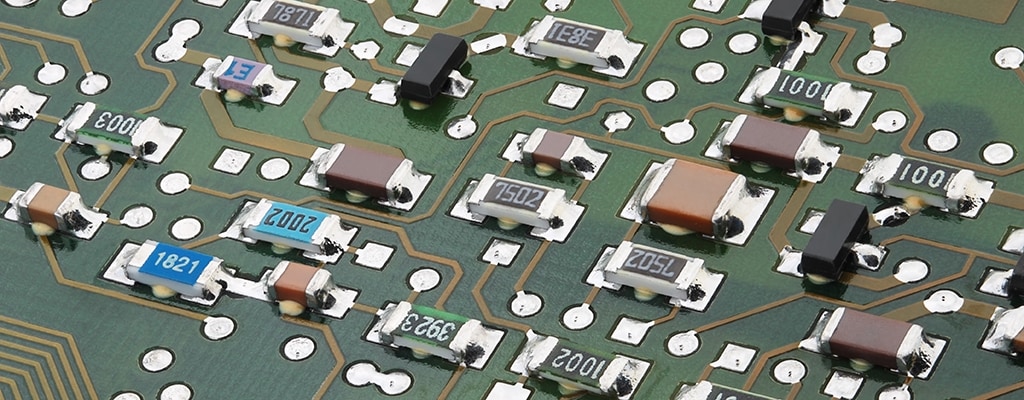
製品詳細
省スペースと軽量化の実現
現在製造されている薄膜抵抗器は、これまで以上に種類も豊富で公差が小さいため、設計時の部品点数を抑えながら、より正確な抵抗値を実現できます。当社の薄膜 SMD 抵抗器が、プリント基板上の貴重なスペース節約と、デバイスの軽量化につながる理由をご説明します。
表面実装型チップ抵抗器は、PCB (プリント基板) の設計に欠かせない部品です。 その理由の 1 つに、こうした小型のリードレス デバイスは、大量生産において取り付けが容易であることが挙げられます。製品設計にとって最適な表面実装型抵抗器 (SMD 抵抗器) を選択するには、まず、薄膜技術 (高精度を重視) と厚膜技術 (高電力を重視) の違いを理解する必要があります。
SMD 抵抗器を分類するうえで、抵抗値 (Ω) は数ある特性の一部に過ぎません。まずは、各種抵抗器の製造プロセスの違いについて、それから質量の大きな物体ほど、小さな物体よりも多くのエネルギを処理できるという熱力学の単純なルールについて、考慮する必要があります。
薄膜抵抗器の場合、導電層を真空蒸着させる、スパッタ処理という手法を使用します。この手法により、わずか 1 ミクロン以下ながらも均質な厚みの薄膜が、セラミック基板上に生成されます。生成された層には、フォト エッチングまたはレーザー エッチング プロセスを施します。これにより抵抗値の精度が決まり、公差は 0.01 % 程度と非常に小さなものになります。こうした高精度によって、薄膜抵抗器の利用価値が上がります。
一方、厚膜抵抗器は、セラミック基板上にペースト状の導電層を形成して製造します。この導電層の厚みは、薄膜抵抗器における導電層の数千倍になる場合もあります。このような厚みは、高電力用途に対応するうえで性能面での利点となり、製造コストも薄膜抵抗器に比べはるかに低くなります。しかし、電力容量における厚膜抵抗器の利点は、見方を変えれば予測可能性と精度を低下させる要因でもあり、公差は 5 % と大きめになります。
新たな素材の導入や製造プロセスの改良により、精度を損なうことなく薄膜抵抗器の容量を拡張することが可能になりつつあります。
素材における技術革新と、製造プロセスの制御性向上に伴い、精度と電力性能を両立させた薄膜抵抗器の開発が可能となり、かつてない高精度が実現されるようになりました。 抵抗器は E 系列で分類されるため、たとえば E12 系列であれば「10 個」の値 (1~10 Ω など) が 12 段階に分割されています。従来であれば、設計者は適切な抵抗値を得るため、固定抵抗器とトリマ ポテンショメータと呼ばれる小型の可変抵抗器とを組み合わせる必要がありました。
現在の薄膜抵抗器は、これまで以上に種類も豊富で公差が小さく、現在では E96 系列が標準となっています。この結果、より精度の高い抵抗値が得られるようになり、設計時にトリマが不要となりました。必要となる部品数が少なくなったことで、PCB 上の貴重なスペースを節約できるようになり、デバイスの軽量化にもつながっています。
抵抗器を選ぶ際は、温度条件が変化する状況での安定性について理解することも重要です。他のあらゆる電子回路と同じく、抵抗器の特性もまた温度に応じて変化し、あらゆる温度変化が性能に影響を及ぼします。抵抗器はいずれも、余分な電気エネルギを熱に変換するよう設計されているほか、温度変化に伴う抵抗値の変化を表す、固有の抵抗温度係数 (TCR) を持っています。薄膜製造プロセスでは、温度変化による変動がほとんど見られない、きわめて安定した抵抗値を持つ部品を作成できます。
厚膜抵抗器は薄膜抵抗器に比べて大きなエネルギを扱うため、高電力用途では優れた性能を発揮しますが、その反面、精度が損なわれることにもなります。現在の技術では、この点で妥協を余儀なくされています。しかし、状況は変化しています。新たな素材の導入や製造プロセスの改良により、精度を損なうことなく薄膜抵抗器の容量を拡張することが可能になりつつあります。たとえば、RN73 シリーズの標準的な 0805 形式抵抗器の定格電力は 0.1 W ですが、新しい RP73P シリーズでは、同サイズの抵抗器の定格電力が 0.25 W となっています。こうした性能の向上は、あらゆるサイズの抵抗器に反映されています。
さまざまな用途で活躍する、SMD 抵抗器
電力対サイズ比という形で現れる、電力容量の増加がもたらす設計上の価値を理解することは重要です。 電力対サイズ比が向上することによって、さまざまな面で設計上のメリットが得られます。たとえば、設計全体を見直してより小型の部品を採用することで、機器の小型化、軽量化を実現できます。あるいは、電力対サイズ比の向上により、より大きな電力を利用できることを活かして、既存デバイスの性能を高めることも可能です。どちらの例でも、最新の薄膜抵抗器がもたらす電力容量増加によって、設計上の新たな可能性が生まれています。
製薬産業において、過酷な環境で使用される薄膜抵抗器に関する興味深い事例を見てみましょう。製薬の現場では、各成分を正しい配合で使用するため、計量を正確に行う必要があります。こうした環境における生産速度は、精密設備にとって過酷なものともなりうるため、製薬企業では、計量機器内の抵抗器が温度変化の影響を受けて本来発揮するべき安定性を失った末に、計量の正確性が損なわれてしまうことのないよう、万全を期す必要があります。新世代の薄膜抵抗器であれば、こうした条件下においても安定性と精度の両方を実現できます。
大量生産用途や、電力容量が最優先とされる用途では今後も、厚膜抵抗器が必要とされ続けるでしょう。その一方で、薄膜技術が進歩したことによって、さらに幅広い用途で、かつてない高い精度と信頼性を実現できるようになります。
ソリューションを見る