視覚誘導ロボットによるシートメタル ケージの組み立て
要約
高精度なシートメタル ケージの組み立ては労働集約的です。組み立てコストの削減と組み立て効率および品質の向上を実現するうえで、速度、精度、柔軟性という利点を持つロボットは、自動組み立てシステムを構築するための最適なオプションです。ここでは、ロボットベースのシートメタル ケージ組み立て技術を提示し、マス カスタマイゼーションに対応した組み立てプロセスを自動化するための主要なソリューションを実証、検証、最適化します。
問題の説明
高精度なシートメタル ケージの組み立てプロセスは労働集約的であり、52 人を超える作業員がこのプロセスに集中的に従事しています。図 1 に示すように、まずセパレータをボトム ケージに組み付けてサブアセンブリを作成した後、このサブアセンブリとキックアウト バネおよびトップ ケージを組み合わせてケージ アセンブリを作ります。メタル ケージは外見的に歪みやすく、簡単に傷がつくため、組み立てには細心の注意が必要です。シートメタル部品の厚さは 0.25 mm、組み立て精度は 0.03 mm で、製品型番の数は 100 を超えます。図 1 に示すのは標準的な SFP+ 1X4 ケージですが、これ以外にも 1XN や 2XN のような製品があり、これらが SFP、SFP+、QSFP、ZQSFP などの製品群に分類されています。明らかに、ケージ組み立てプロセスを自動化することは多品種少量のマス カスタマイゼーション プロセスの自動化の問題に取り組むことであり、ハード ツーリングを使用した従来の自動化方法は、この事例でのマス カスタマイゼーション対応の組み立ての要件には適していません。
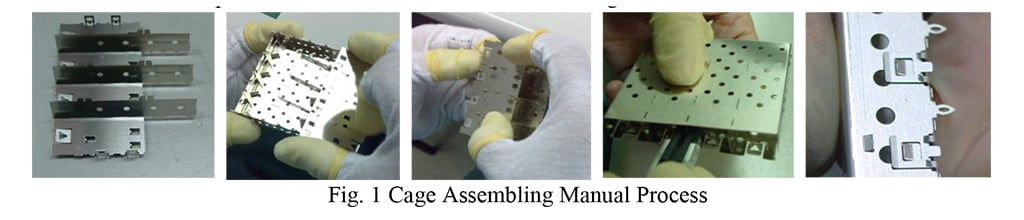
ロボットには速度、精度、柔軟性という大きな利点があり、自動化された柔軟な組み立てシステムを構築するための最適なオプションとみなされています。この研究はロボット/ロボティクスの興味深い能力を探求したものであり、マス カスタマイゼーション対応のシートメタル ケージ組み立てプロセスに対してロボットを使用したソリューションを提示します。これは TE に大きなビジネス インパクトと技術開発をもたらす可能性があります。この研究では、ロボットによるケージ組み立てシステムの信頼性と堅牢性を向上させるため、ケージ組み立てプロセスを解き明かし、2 通りの実験計画法 (DoE) を実施してセパレータおよびボトム ケージ組み立てプロセスとトップ ケージおよびキックアウト バネ組み立てプロセスを最適化します。この研究を通して開発されたロボットベースの組み立てシステムと組み立てプロセス最適化方法が TE の各事業部門で他の製品組み立てプロセスに応用され、それが組み立てコストの大幅な削減や組み立ての効率および品質の向上につながることを期待します。
方法と結果
産業用ロボットの概要
産業用ロボットには、SCARA ロボット、6 軸ロボット、デルタ ロボットなどの種類があります。SCARA ロボットは 3-DOF (自由度) 平行移動と 1-DOF 回転が可能で、一般にピックアンドプレース操作に使用されます。6 軸ロボットは 3-DOF 平行移動と 3-DOF 回転が可能で、さまざまな製造・組み立てプロセスに幅広く応用されています。デルタ ロボットは一般に 3-DOF 平行移動と 1-DOF 回転が可能な並列アーキテクチャを備えており、通常は高速なピックアンドプレース操作に利用されます。シートメタル ケージ組み立てプロセスの場合、最終組み立てへの組み立て経路に従うにはセパレータとトップ ケージの組み立て時に部品の平行移動と回転の両方が必要となるため、6 軸ロボットを採用するのが適しています。図 2 に、典型的な 6 軸ロボットと、エンドエフェクタを可動させるアーキテクチャを示します。6 軸産業用ロボットは 6-R 機構 (R: 回転関節) とも呼ばれ、アームとリストの 2 つの要素に分解できます。アームは 3-DOF 平行移動を実現し、リストは 3-DOF 回転を実現します。アームとリストを協調させることで、エンドエフェクタが作業空間内で定義された姿勢をとることができ、かなり俊敏にシートメタル ケージ組み立てプロセスをこなせると考えられます。
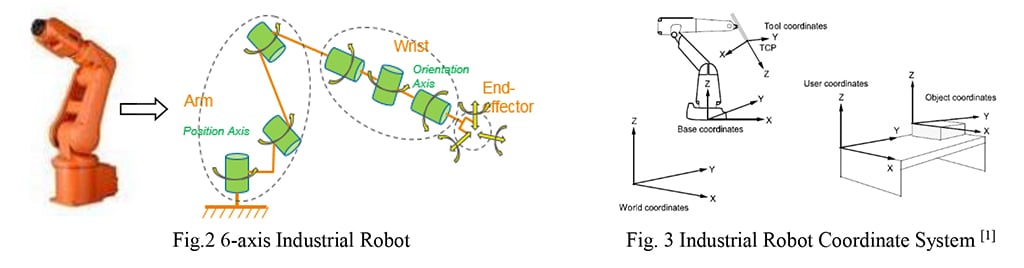
今日の産業用ロボットは、モデリング・制御方法、ロボット プログラミング言語、およびプログラミング インタフェースの発展によって大きく進化しています。エンド ユーザは、モータ制御、順運動学/逆運動学、動力学について詳しく知る必要はありません。ただし、ロボット運動と経路計画を操作するためのロボット プログラミング言語については、いくつかの手法を身につける必要があります。ロボットに搭載されたエンドエフェクタの運動と経路計画はロボット ツール座標系に基づいており、この座標系は個別に定義されて個々のエンドエフェクタに関連付けられます。図 3 に、主なロボット座標系の概念を示します。ロボット経路の精密制御とは、重要なロボット ターゲットを精密に制御することです。特にケージ組み立てプロセスにおいては、ロボット組み立て経路を構成するステップは線形平行移動、回転、またはその両方の組み合わせとなり、干渉のないスムーズな組み立て経路を構築するにはロボットのステップ サイズを正確に定義することが重要です。ターゲットごとに、エンドエフェクタの位置 (x, y, z) と向き (Ex, Ey, Ez) を正確に定義する必要があります。ここで言う x、y、z はオブジェクト座標系の座標、Ex、Ey、Ez はオブジェクト座標系のオイラー角を意味します。
視覚誘導ロボット
高精度組み立てに対する従来の自動化方法は、高精度の機械的装備を設計・製造して部品のポジショニングを行い、高精度の機構を開発して部品の装填と組み立てを行うというものであり、機械システムの精度の維持が課題となっています。それに対して、視覚誘導ロボット法では、ロボット ツールで把持された部品の姿勢を正確に識別するために視覚システムがロボット システムの一部として統合されており、ロボット/ロボット ツールが視覚的識別からのフィードバックに基づいて部品を適応的に平行移動または回転させることで、組み立て精度を確保します。
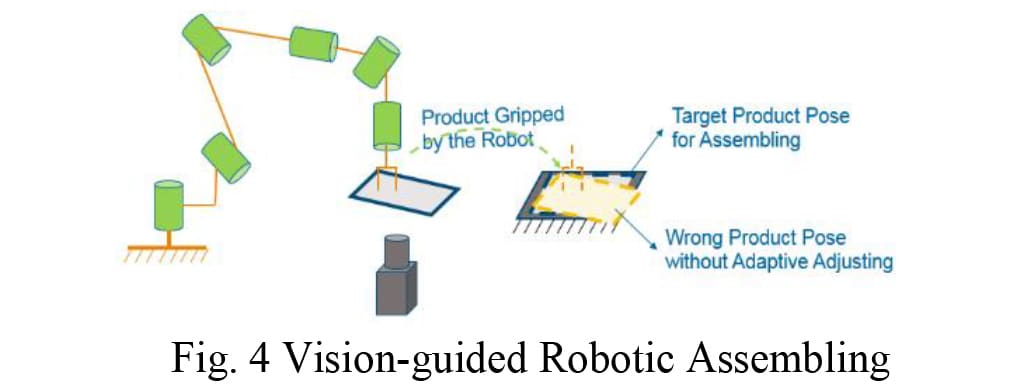
図 4 に、適応的な組み立て/ピックアンドプレース操作に使用する典型的な視覚誘導ロボット システムを示します。ロボットが製品をピックアップする際にポジショニング エラーが原因で位置または向きが違っていると、ロボット ティーチングによって生成される一定のロボット姿勢では製品の組み立てに失敗する可能性があります。視覚システムはロボットを誘導して組み立て経路を適応的に調整するのに有用であり、組み立てシステムの信頼性と堅牢性を保証します。
ロボットによる適応的組み立てアルゴリズムを開発するには、まず基準モデルとするベース モデルを作成してから、ロボットの姿勢を適応的に調整して製品を正確に組み立てるターゲット姿勢計算モデルを定式化します。ベース モデルを作成する際は、画像キャプチャのためのロボット姿勢 (XRb, YRb, ARb)、2D 視覚システムによって識別されたロボット ツールでの製品姿勢 (XCb, YCb, ACb)、および製品を正確に組み立てるためのティーチ姿勢 (XFb, YFb, AFb) を参照ベースとして、製品ターゲット姿勢 (XCFb, YCFb, ACFb) を計算します。当然ながら、製品を正確に組み立てるためには、製品ターゲット姿勢は一定になります。X/Y は位置、A は z 軸に沿った回転角度を意味します。ここでは 2D 視覚システムを使用しており、2D 平面での姿勢成分を示しています。
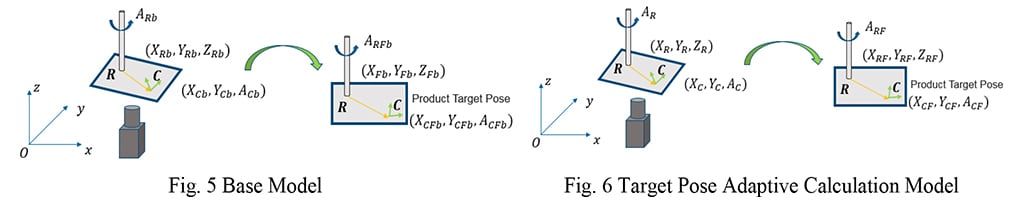
図 4 に示すように、ロボット ツールは製品をポイント R で把持します。フレーム C はロボット ツールでの製品の位置と向きを表すためのフィーチャで、製品組み立てのティーチ姿勢はすでにわかっているものとします。製品組み立て用の製品ターゲット姿勢は、画像キャプチャ姿勢から組み立て姿勢へのベクトル 𝒗𝑟𝑐 の 2 次元平行移動とティーチ姿勢に基づいて計算されます。したがって、製品ターゲット姿勢を算出する式は次のようになります。

ここで、𝒗𝑟𝑐 = (𝑋𝐶𝑏 − 𝑋𝑅𝑏, 𝑌𝐶𝑏 − 𝑌𝑅𝑏)𝑇 です。
製品組み立て用の製品ターゲット向きは、式 (2) に示すように、製品フィーチャ向きである ACb と、ロボットの回転変分を示す ∆𝐴𝑏 = 𝐴𝑅𝐹𝑏 − 𝐴𝑅𝑏 に基づいて計算されます。
𝐴𝐶𝐹𝑏 = 𝐴𝐶𝑏 + ∆𝐴𝑏 (2)
製品組み立て用のロボットの適応的ターゲット姿勢は、図 6 に示すモデルによって定式化されます。わかりやすいように、製品ターゲット姿勢は参照ベースと同じになっています。
𝑋𝐶𝐹 = 𝑋𝐶𝐹𝑏、 𝑌𝐶𝐹 = 𝑌𝐶𝐹𝑏、 𝐴𝐶𝐹 = 𝐴𝐶𝐹𝑏 (3)
画像キャプチャ用のロボット姿勢は (XR, YR, AR)、ロボット ツールで識別された製品姿勢は (XC, YC, AC) で、画像キャプチャ姿勢から組み立て姿勢までの製品回転角度の変分は式 (4) のように定式化されます。
∆A = 𝐴𝐶𝐹 − 𝐴𝐶 (4)
したがって、製品組み立て用のロボットのターゲット向きは、識別された製品フィーチャ向きを使用して式 (5) のように適応的に計算されます。
𝐴𝑅𝐹 = 𝐴𝑅 + ∆𝐴 = 𝐴𝑅 + 𝐴𝐶𝐹 − 𝐴𝐶 (5)
製品組み立て用のロボットのターゲット位置は、ベクトル 𝒗𝑟𝑐 の 2 次元平行移動と製品ターゲット姿勢に基づいて式 (6) のように定式化されます。

ここで、𝒗𝑟𝑐 = (𝑋C − 𝑋R, 𝑌C − 𝑌R)T
です。
図 5 および 6 に示す製品フィーチャを正確に識別する視覚システムのおかげで、製品組み立て時のロボット姿勢は一定でなくなり、式 (5) と (6) によって算出される適応的な姿勢になります。
シートメタル ケージ組み立てプロセスの場合、セパレータとキックアウト バネの機械的ポジショニング精度は約 0.3 mm で、トップ ケージの機械的ポジショニング精度は、位置については約 0.1 mm、向きについては約 0.25 度です。0.03 mm の組み立て精度を満たすため、ポジショニング精度が +/-0.003 mm の視覚システムを統合して、図 8 に示すようにロボットを適応的に誘導します。ロボットの繰り返し精度が +/-0.01 mm であることを考慮すると、このロボット システムの全体的な組み立て精度は約 0.02 mm となり、シートメタル ケージ組み立てプロセスを実行するのに十分な精度があります。
ロボット シートメタル ケージ組み立てシステム
多品種少量のケージ製品の高精度組み立てをカバーするマス カスタマイゼーション対応の自動化システムを開発するため、シートメタル ケージ組み立てシステム (図 7-a を参照) は、部品の装填と組み立てを行う 6 軸ロボットと、ロボット ツールおよび組み立て治具で把持された部品の姿勢を正確に識別する視覚システムで構成されています。このロボットは、2 種類のロボット ツールを備えています。1 つはセパレータとキックアウト バネの装填と組み立てを行う空気圧グリッパで、もう 1 つはボトム ケージとトップ ケージの装填と組み立てを行う空気圧サッカーです。組み立て治具はリニア スクリューによってセパレータ組み立てステーションとトップ ケージ & キックアウト バネ組み立てステーションの間を搬送されます。
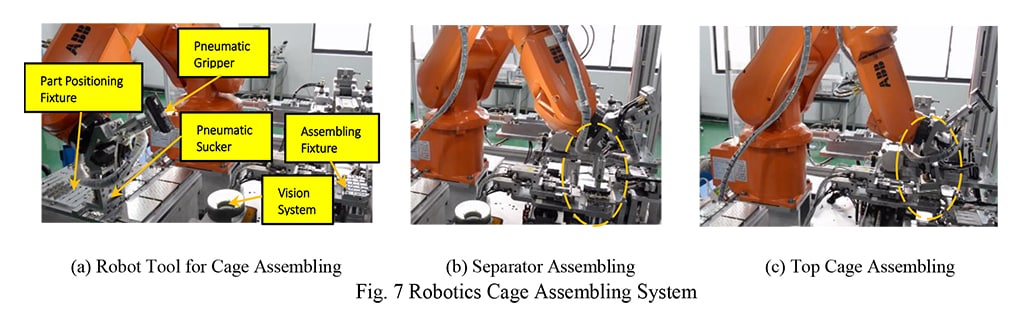
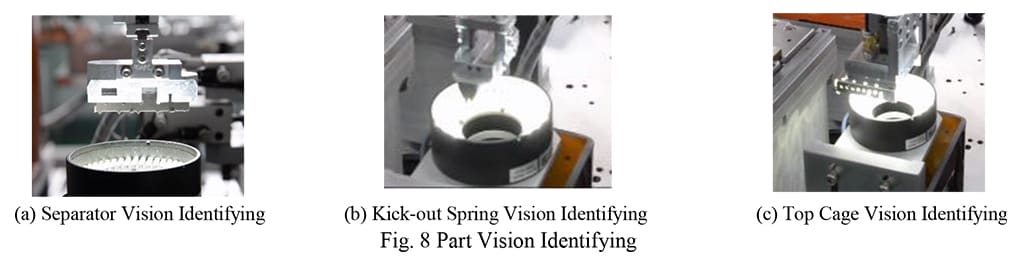
このロボットは、まずボトム ケージをセパレータ組み立てステーションで組み立て治具に装填してから、個々のセパレータをボトム ケージと組み合わせてサブアセンブリを作成します (図 7-b を参照)。次に、リニア スクリューが組み立て治具とサブアセンブリをキックアウト バネ & トップ ケージ組み立てステーションに搬送します。そこで組み立て治具が正確にポジショニングされ、セパレータがキックアウト バネおよびトップ ケージ組み立て用のセパレータ保持機構によって正確に保持されます (図 7-c を参照)。視覚システムによってロボット ツールで把持された部品の姿勢が正確に識別され、セパレータ、キックアウト バネ、およびトップ ケージが式 (5) と (6) に基づく定式に従って適応的に組み立てられます。
ロボット組み立てプロセスの最適化
ロボットによるシートメタル ケージ組み立てシステムの信頼性を向上させてその能力を最大限に高めるため、2 通りの実験計画法 (DoE) を実施して組み立てプロセスの最適化を図りました。一方の DoE はセパレータおよびボトム ケージ組み立てを対象とし、もう一方はキックアウト バネおよびトップ ケージ組み立てを対象とします。高精度組み立てプロセスの鍵となる重要な要素は一般に、組み立て治具の部品ポジショニング機構とロボット組み立て経路です。
セパレータおよびボトム ケージ組み立てプロセスの最適化については、組み立て治具のポジショニング機構によってボトム ケージのポジショニングと固定を向上させました。セパレータ組み立て用の組み立て治具には大きな問題がないことが確かめられたので、歩留まりを最適化するために他の 2 つの要因 (組み立て速度と組み立て経路) を選択しました。図 9-a に示すパレート図から、組み立て歩留まりに大きな影響を及ぼす影響係数は組み立て経路であることがわかります。図 10-a と 10-b に示す最適なセパレータ組み立て経路を使用して最適化されたセパレータ組み立ての歩留まりは、97% に達しました。セパレータ構造の違いにより、ボトム ケージとの干渉を避けるためにセパレータ #1 の組み立て経路はセパレータ #2 および #3 と異なっています。
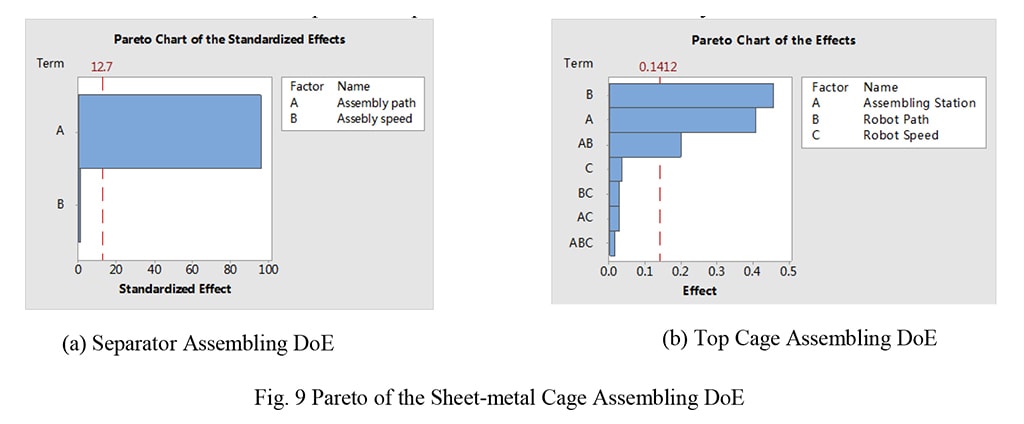
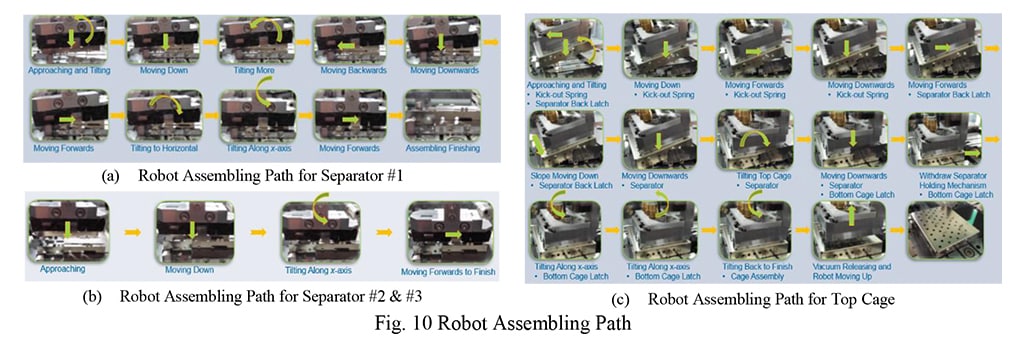
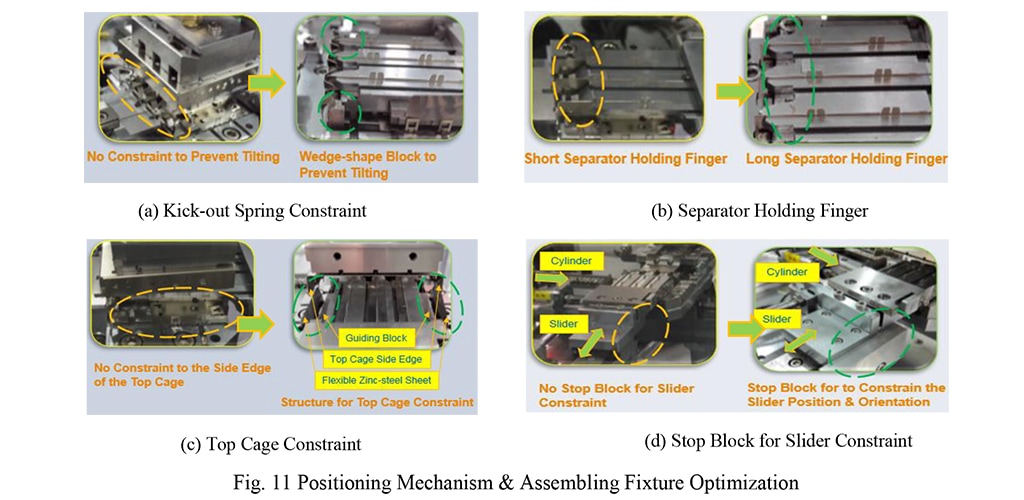
トップ ケージ組み立ての最適化については、DoE の実施に際して 3 つの要因を選択しました。図 9-b のパレート図は、ロボット経路、組み立て治具とポジショニング機構、および両者の相互作用が影響係数であることを示しています。図 10-c に示す最適なトップ ケージ組み立て経路、および図 11 に示す最適なポジショニング機構と組み立て治具を使用して最適化されたトップ ケージ組み立ての歩留まりは、97% に達しました。組み立てを成功させるには、トップ ケージをキックアウト バネ、セパレータ、ボトム ケージに狂いなく合わせる必要があるため、重要な要素を考慮に入れてそれぞれの最適な組み立てステップを設計しました。ポジショニング機構と組み立て治具の最適化については、ロボット組み立て経路と協調させて組み立て歩留まりを向上させるため、くさび状のブロックのペアによってキックアウト バネに制約をかけ、トップ ケージによる軽微な力によってバネが傾斜しないようにしました。バネが傾斜すると、トップ ケージの組み立てがうまくいかない場合があります (図 11-a を参照)。また、セパレータをしっかり正確に保持できるようにセパレータ保持フィンガを長くして、高速でもセパレータが振動しないように改良しました (図 11-b を参照)。トップ ケージについては、ガイド ブロックによって側端に制約をかけ、柔軟な亜鉛鋼板によってトップ ケージの側端間距離の大きな公差 (-0.1 ~ 0.7 mm) の適合性を確保しました (図 11-c を参照)。さらに、空気圧シリンダがセパレータ保持フィンガを押してセパレータを保持する際、セパレータ保持フィンガの供給・引き出し用のスライダとガイド トラックの間にある隙間が原因で、セパレータとボトム ケージの位置エラーや回転エラーが発生することがありました。これを避けるため、ストップ ブロックを追加してスライダの位置と向きに制約をかけ、組み立てステーションでのセパレータとボトム ケージのポジショニング精度を保証しました。これは組み立ての信頼性と堅牢性を確保するうえで非常に重要です (図 11-d を参照)。
組み立て歩留まりを損失させずにロボット速度を最適化することで、組み立て効率も向上しました。表 1 は、ロボット移動速度を 2000 mm/秒、セパレータおよびキックアウト バネ組み立てのロボット速度を 50 mm/秒、トップ ケージ組み立てのロボット速度を 30 mm/秒にそれぞれ最適化した場合の、各部品の組み立てに要する最適なサイクル タイムを示します。この最適なサイクル タイムは、ケージ組み立てプロセスの産業化に関する要件を満たしています。
表 1
組み立て品 | ボトム ケージ | セパレータ #1 | セパレータ #2 | セパレータ #3 | キックアウト バネ | トップ ケージ |
サイクル タイム (秒/個) | 2.2 | 4.6 | 3.2 | 3.4 | 4.0 | 7.0 |
考察および要点
シートメタル ケージ組み立て用の生産機械の開発
この研究では、ロボットベースのシートメタル ケージ組み立てシステムの実現可能性を検証し、組み立てプロセスの最適化と組み立て歩留まりおよび組み立てサイクル タイムの向上を図るために 2 通りの DoE を実施しました。この技術は明らかに産業化の目標を達成可能なことが判明したため、この DoE プラットフォームは現在 D&D 珠海工場に導入されて大量生産に使用されています。最新の生産データによると、このプラットフォームの歩留まりは 98% で、労務費は 4 人の作業員分に削減されました (年間 48,000 ドルの節約)。次のステップは、シートメタル ケージ組み立て用の生産機械を製作することです。この技術を搭載した生産機械を導入すれば、TE D&D 事業部門の労務費は年間 52 万ドル削減されると見込まれます。さらに、ここで開発したロボットベースのシートメタル ケージ組み立て技術は、TE のマス カスタマイゼーションに対応した高精度な組み立て能力を大幅に向上させ、自動車、インダストリアル、CPD、センサなどの他の事業部門でマス カスタマイゼーション対応の組み立て自動化ソリューションを開発するための足掛かりになります。これは間違いなく、TE 全体に大きなビジネス インパクトを生み出します。
謝辞
ロボットベースのシートメタル ケージ組み立て技術の開発に取り組むことは胸躍る経験でした。この取り組みを支持および後援していただいた TE Global Operations および D&D 事業部門のリーダーの方々、特に有益な提案や指導をいただいた Philip Gilchrist 氏、Darel Callis 氏、Rolando Saavedra 氏、Marshall Chen 氏に感謝の意を表します。
参考文献
[1] 技術参考文献 – RAPID Instructions, Functions and Data types, ABB Robot documentation M2004, rev H, RW5.15
視覚誘導ロボットによるシートメタル ケージの組み立て
要約
高精度なシートメタル ケージの組み立ては労働集約的です。組み立てコストの削減と組み立て効率および品質の向上を実現するうえで、速度、精度、柔軟性という利点を持つロボットは、自動組み立てシステムを構築するための最適なオプションです。ここでは、ロボットベースのシートメタル ケージ組み立て技術を提示し、マス カスタマイゼーションに対応した組み立てプロセスを自動化するための主要なソリューションを実証、検証、最適化します。
問題の説明
高精度なシートメタル ケージの組み立てプロセスは労働集約的であり、52 人を超える作業員がこのプロセスに集中的に従事しています。図 1 に示すように、まずセパレータをボトム ケージに組み付けてサブアセンブリを作成した後、このサブアセンブリとキックアウト バネおよびトップ ケージを組み合わせてケージ アセンブリを作ります。メタル ケージは外見的に歪みやすく、簡単に傷がつくため、組み立てには細心の注意が必要です。シートメタル部品の厚さは 0.25 mm、組み立て精度は 0.03 mm で、製品型番の数は 100 を超えます。図 1 に示すのは標準的な SFP+ 1X4 ケージですが、これ以外にも 1XN や 2XN のような製品があり、これらが SFP、SFP+、QSFP、ZQSFP などの製品群に分類されています。明らかに、ケージ組み立てプロセスを自動化することは多品種少量のマス カスタマイゼーション プロセスの自動化の問題に取り組むことであり、ハード ツーリングを使用した従来の自動化方法は、この事例でのマス カスタマイゼーション対応の組み立ての要件には適していません。
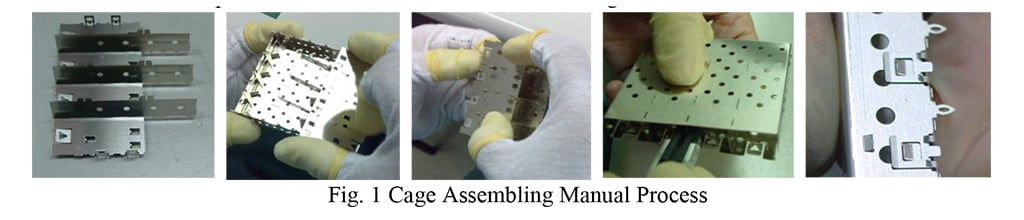
ロボットには速度、精度、柔軟性という大きな利点があり、自動化された柔軟な組み立てシステムを構築するための最適なオプションとみなされています。この研究はロボット/ロボティクスの興味深い能力を探求したものであり、マス カスタマイゼーション対応のシートメタル ケージ組み立てプロセスに対してロボットを使用したソリューションを提示します。これは TE に大きなビジネス インパクトと技術開発をもたらす可能性があります。この研究では、ロボットによるケージ組み立てシステムの信頼性と堅牢性を向上させるため、ケージ組み立てプロセスを解き明かし、2 通りの実験計画法 (DoE) を実施してセパレータおよびボトム ケージ組み立てプロセスとトップ ケージおよびキックアウト バネ組み立てプロセスを最適化します。この研究を通して開発されたロボットベースの組み立てシステムと組み立てプロセス最適化方法が TE の各事業部門で他の製品組み立てプロセスに応用され、それが組み立てコストの大幅な削減や組み立ての効率および品質の向上につながることを期待します。
方法と結果
産業用ロボットの概要
産業用ロボットには、SCARA ロボット、6 軸ロボット、デルタ ロボットなどの種類があります。SCARA ロボットは 3-DOF (自由度) 平行移動と 1-DOF 回転が可能で、一般にピックアンドプレース操作に使用されます。6 軸ロボットは 3-DOF 平行移動と 3-DOF 回転が可能で、さまざまな製造・組み立てプロセスに幅広く応用されています。デルタ ロボットは一般に 3-DOF 平行移動と 1-DOF 回転が可能な並列アーキテクチャを備えており、通常は高速なピックアンドプレース操作に利用されます。シートメタル ケージ組み立てプロセスの場合、最終組み立てへの組み立て経路に従うにはセパレータとトップ ケージの組み立て時に部品の平行移動と回転の両方が必要となるため、6 軸ロボットを採用するのが適しています。図 2 に、典型的な 6 軸ロボットと、エンドエフェクタを可動させるアーキテクチャを示します。6 軸産業用ロボットは 6-R 機構 (R: 回転関節) とも呼ばれ、アームとリストの 2 つの要素に分解できます。アームは 3-DOF 平行移動を実現し、リストは 3-DOF 回転を実現します。アームとリストを協調させることで、エンドエフェクタが作業空間内で定義された姿勢をとることができ、かなり俊敏にシートメタル ケージ組み立てプロセスをこなせると考えられます。
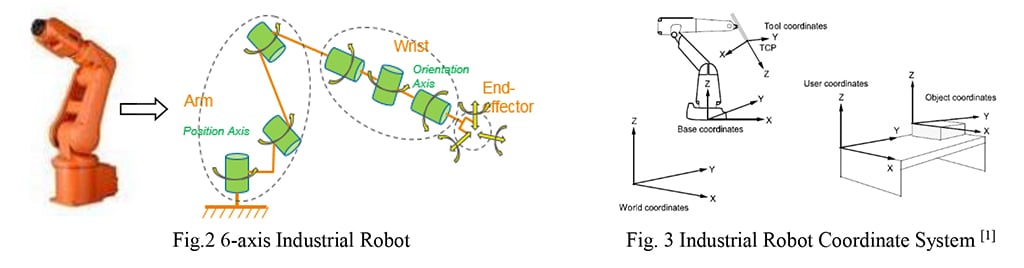
今日の産業用ロボットは、モデリング・制御方法、ロボット プログラミング言語、およびプログラミング インタフェースの発展によって大きく進化しています。エンド ユーザは、モータ制御、順運動学/逆運動学、動力学について詳しく知る必要はありません。ただし、ロボット運動と経路計画を操作するためのロボット プログラミング言語については、いくつかの手法を身につける必要があります。ロボットに搭載されたエンドエフェクタの運動と経路計画はロボット ツール座標系に基づいており、この座標系は個別に定義されて個々のエンドエフェクタに関連付けられます。図 3 に、主なロボット座標系の概念を示します。ロボット経路の精密制御とは、重要なロボット ターゲットを精密に制御することです。特にケージ組み立てプロセスにおいては、ロボット組み立て経路を構成するステップは線形平行移動、回転、またはその両方の組み合わせとなり、干渉のないスムーズな組み立て経路を構築するにはロボットのステップ サイズを正確に定義することが重要です。ターゲットごとに、エンドエフェクタの位置 (x, y, z) と向き (Ex, Ey, Ez) を正確に定義する必要があります。ここで言う x、y、z はオブジェクト座標系の座標、Ex、Ey、Ez はオブジェクト座標系のオイラー角を意味します。
視覚誘導ロボット
高精度組み立てに対する従来の自動化方法は、高精度の機械的装備を設計・製造して部品のポジショニングを行い、高精度の機構を開発して部品の装填と組み立てを行うというものであり、機械システムの精度の維持が課題となっています。それに対して、視覚誘導ロボット法では、ロボット ツールで把持された部品の姿勢を正確に識別するために視覚システムがロボット システムの一部として統合されており、ロボット/ロボット ツールが視覚的識別からのフィードバックに基づいて部品を適応的に平行移動または回転させることで、組み立て精度を確保します。
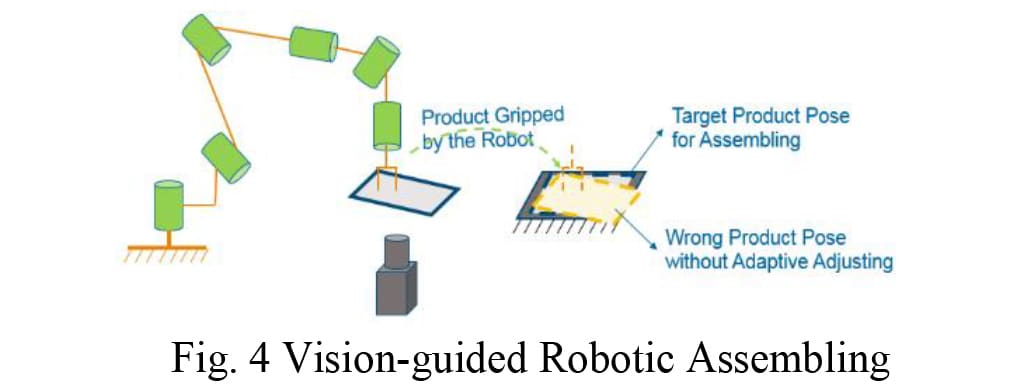
図 4 に、適応的な組み立て/ピックアンドプレース操作に使用する典型的な視覚誘導ロボット システムを示します。ロボットが製品をピックアップする際にポジショニング エラーが原因で位置または向きが違っていると、ロボット ティーチングによって生成される一定のロボット姿勢では製品の組み立てに失敗する可能性があります。視覚システムはロボットを誘導して組み立て経路を適応的に調整するのに有用であり、組み立てシステムの信頼性と堅牢性を保証します。
ロボットによる適応的組み立てアルゴリズムを開発するには、まず基準モデルとするベース モデルを作成してから、ロボットの姿勢を適応的に調整して製品を正確に組み立てるターゲット姿勢計算モデルを定式化します。ベース モデルを作成する際は、画像キャプチャのためのロボット姿勢 (XRb, YRb, ARb)、2D 視覚システムによって識別されたロボット ツールでの製品姿勢 (XCb, YCb, ACb)、および製品を正確に組み立てるためのティーチ姿勢 (XFb, YFb, AFb) を参照ベースとして、製品ターゲット姿勢 (XCFb, YCFb, ACFb) を計算します。当然ながら、製品を正確に組み立てるためには、製品ターゲット姿勢は一定になります。X/Y は位置、A は z 軸に沿った回転角度を意味します。ここでは 2D 視覚システムを使用しており、2D 平面での姿勢成分を示しています。
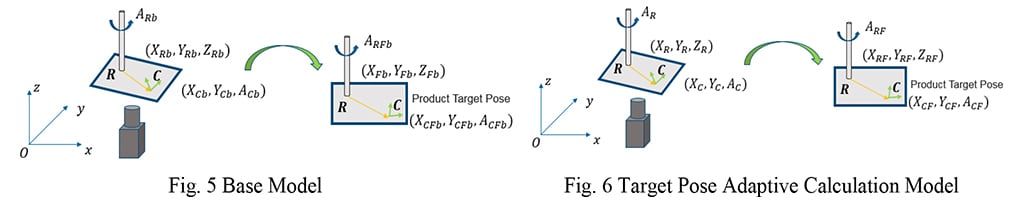
図 4 に示すように、ロボット ツールは製品をポイント R で把持します。フレーム C はロボット ツールでの製品の位置と向きを表すためのフィーチャで、製品組み立てのティーチ姿勢はすでにわかっているものとします。製品組み立て用の製品ターゲット姿勢は、画像キャプチャ姿勢から組み立て姿勢へのベクトル 𝒗𝑟𝑐 の 2 次元平行移動とティーチ姿勢に基づいて計算されます。したがって、製品ターゲット姿勢を算出する式は次のようになります。

ここで、𝒗𝑟𝑐 = (𝑋𝐶𝑏 − 𝑋𝑅𝑏, 𝑌𝐶𝑏 − 𝑌𝑅𝑏)𝑇 です。
製品組み立て用の製品ターゲット向きは、式 (2) に示すように、製品フィーチャ向きである ACb と、ロボットの回転変分を示す ∆𝐴𝑏 = 𝐴𝑅𝐹𝑏 − 𝐴𝑅𝑏 に基づいて計算されます。
𝐴𝐶𝐹𝑏 = 𝐴𝐶𝑏 + ∆𝐴𝑏 (2)
製品組み立て用のロボットの適応的ターゲット姿勢は、図 6 に示すモデルによって定式化されます。わかりやすいように、製品ターゲット姿勢は参照ベースと同じになっています。
𝑋𝐶𝐹 = 𝑋𝐶𝐹𝑏、 𝑌𝐶𝐹 = 𝑌𝐶𝐹𝑏、 𝐴𝐶𝐹 = 𝐴𝐶𝐹𝑏 (3)
画像キャプチャ用のロボット姿勢は (XR, YR, AR)、ロボット ツールで識別された製品姿勢は (XC, YC, AC) で、画像キャプチャ姿勢から組み立て姿勢までの製品回転角度の変分は式 (4) のように定式化されます。
∆A = 𝐴𝐶𝐹 − 𝐴𝐶 (4)
したがって、製品組み立て用のロボットのターゲット向きは、識別された製品フィーチャ向きを使用して式 (5) のように適応的に計算されます。
𝐴𝑅𝐹 = 𝐴𝑅 + ∆𝐴 = 𝐴𝑅 + 𝐴𝐶𝐹 − 𝐴𝐶 (5)
製品組み立て用のロボットのターゲット位置は、ベクトル 𝒗𝑟𝑐 の 2 次元平行移動と製品ターゲット姿勢に基づいて式 (6) のように定式化されます。

ここで、𝒗𝑟𝑐 = (𝑋C − 𝑋R, 𝑌C − 𝑌R)T
です。
図 5 および 6 に示す製品フィーチャを正確に識別する視覚システムのおかげで、製品組み立て時のロボット姿勢は一定でなくなり、式 (5) と (6) によって算出される適応的な姿勢になります。
シートメタル ケージ組み立てプロセスの場合、セパレータとキックアウト バネの機械的ポジショニング精度は約 0.3 mm で、トップ ケージの機械的ポジショニング精度は、位置については約 0.1 mm、向きについては約 0.25 度です。0.03 mm の組み立て精度を満たすため、ポジショニング精度が +/-0.003 mm の視覚システムを統合して、図 8 に示すようにロボットを適応的に誘導します。ロボットの繰り返し精度が +/-0.01 mm であることを考慮すると、このロボット システムの全体的な組み立て精度は約 0.02 mm となり、シートメタル ケージ組み立てプロセスを実行するのに十分な精度があります。
ロボット シートメタル ケージ組み立てシステム
多品種少量のケージ製品の高精度組み立てをカバーするマス カスタマイゼーション対応の自動化システムを開発するため、シートメタル ケージ組み立てシステム (図 7-a を参照) は、部品の装填と組み立てを行う 6 軸ロボットと、ロボット ツールおよび組み立て治具で把持された部品の姿勢を正確に識別する視覚システムで構成されています。このロボットは、2 種類のロボット ツールを備えています。1 つはセパレータとキックアウト バネの装填と組み立てを行う空気圧グリッパで、もう 1 つはボトム ケージとトップ ケージの装填と組み立てを行う空気圧サッカーです。組み立て治具はリニア スクリューによってセパレータ組み立てステーションとトップ ケージ & キックアウト バネ組み立てステーションの間を搬送されます。
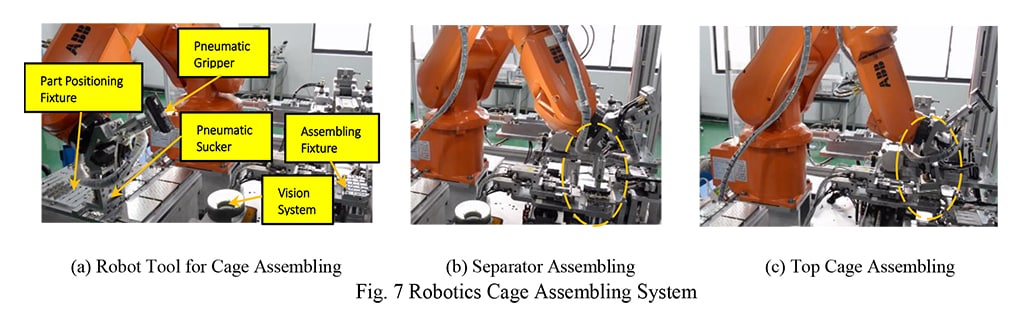
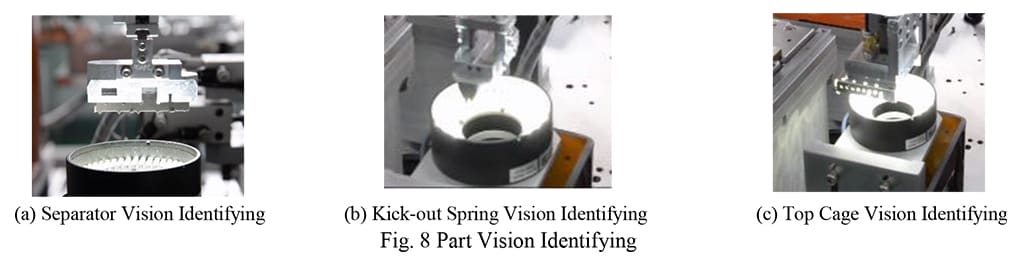
このロボットは、まずボトム ケージをセパレータ組み立てステーションで組み立て治具に装填してから、個々のセパレータをボトム ケージと組み合わせてサブアセンブリを作成します (図 7-b を参照)。次に、リニア スクリューが組み立て治具とサブアセンブリをキックアウト バネ & トップ ケージ組み立てステーションに搬送します。そこで組み立て治具が正確にポジショニングされ、セパレータがキックアウト バネおよびトップ ケージ組み立て用のセパレータ保持機構によって正確に保持されます (図 7-c を参照)。視覚システムによってロボット ツールで把持された部品の姿勢が正確に識別され、セパレータ、キックアウト バネ、およびトップ ケージが式 (5) と (6) に基づく定式に従って適応的に組み立てられます。
ロボット組み立てプロセスの最適化
ロボットによるシートメタル ケージ組み立てシステムの信頼性を向上させてその能力を最大限に高めるため、2 通りの実験計画法 (DoE) を実施して組み立てプロセスの最適化を図りました。一方の DoE はセパレータおよびボトム ケージ組み立てを対象とし、もう一方はキックアウト バネおよびトップ ケージ組み立てを対象とします。高精度組み立てプロセスの鍵となる重要な要素は一般に、組み立て治具の部品ポジショニング機構とロボット組み立て経路です。
セパレータおよびボトム ケージ組み立てプロセスの最適化については、組み立て治具のポジショニング機構によってボトム ケージのポジショニングと固定を向上させました。セパレータ組み立て用の組み立て治具には大きな問題がないことが確かめられたので、歩留まりを最適化するために他の 2 つの要因 (組み立て速度と組み立て経路) を選択しました。図 9-a に示すパレート図から、組み立て歩留まりに大きな影響を及ぼす影響係数は組み立て経路であることがわかります。図 10-a と 10-b に示す最適なセパレータ組み立て経路を使用して最適化されたセパレータ組み立ての歩留まりは、97% に達しました。セパレータ構造の違いにより、ボトム ケージとの干渉を避けるためにセパレータ #1 の組み立て経路はセパレータ #2 および #3 と異なっています。
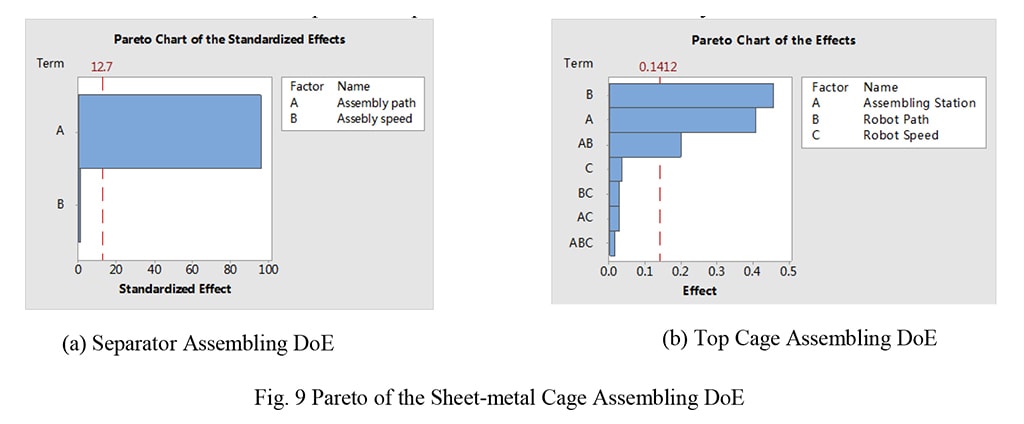
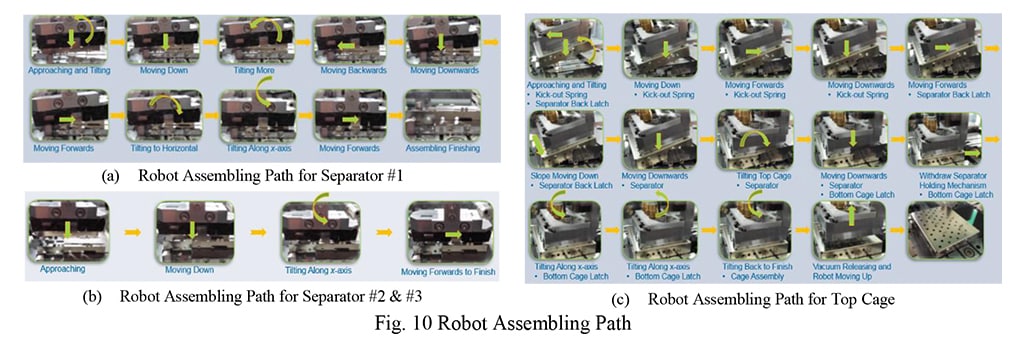
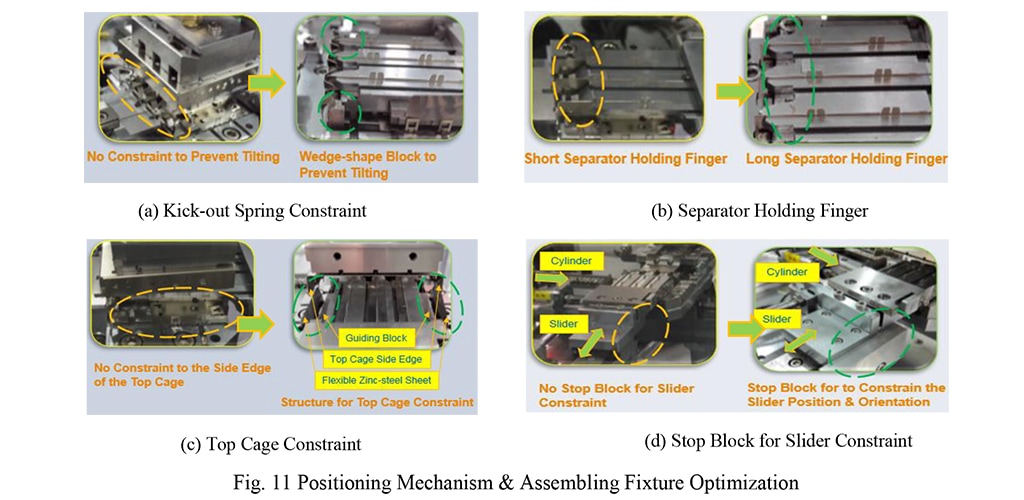
トップ ケージ組み立ての最適化については、DoE の実施に際して 3 つの要因を選択しました。図 9-b のパレート図は、ロボット経路、組み立て治具とポジショニング機構、および両者の相互作用が影響係数であることを示しています。図 10-c に示す最適なトップ ケージ組み立て経路、および図 11 に示す最適なポジショニング機構と組み立て治具を使用して最適化されたトップ ケージ組み立ての歩留まりは、97% に達しました。組み立てを成功させるには、トップ ケージをキックアウト バネ、セパレータ、ボトム ケージに狂いなく合わせる必要があるため、重要な要素を考慮に入れてそれぞれの最適な組み立てステップを設計しました。ポジショニング機構と組み立て治具の最適化については、ロボット組み立て経路と協調させて組み立て歩留まりを向上させるため、くさび状のブロックのペアによってキックアウト バネに制約をかけ、トップ ケージによる軽微な力によってバネが傾斜しないようにしました。バネが傾斜すると、トップ ケージの組み立てがうまくいかない場合があります (図 11-a を参照)。また、セパレータをしっかり正確に保持できるようにセパレータ保持フィンガを長くして、高速でもセパレータが振動しないように改良しました (図 11-b を参照)。トップ ケージについては、ガイド ブロックによって側端に制約をかけ、柔軟な亜鉛鋼板によってトップ ケージの側端間距離の大きな公差 (-0.1 ~ 0.7 mm) の適合性を確保しました (図 11-c を参照)。さらに、空気圧シリンダがセパレータ保持フィンガを押してセパレータを保持する際、セパレータ保持フィンガの供給・引き出し用のスライダとガイド トラックの間にある隙間が原因で、セパレータとボトム ケージの位置エラーや回転エラーが発生することがありました。これを避けるため、ストップ ブロックを追加してスライダの位置と向きに制約をかけ、組み立てステーションでのセパレータとボトム ケージのポジショニング精度を保証しました。これは組み立ての信頼性と堅牢性を確保するうえで非常に重要です (図 11-d を参照)。
組み立て歩留まりを損失させずにロボット速度を最適化することで、組み立て効率も向上しました。表 1 は、ロボット移動速度を 2000 mm/秒、セパレータおよびキックアウト バネ組み立てのロボット速度を 50 mm/秒、トップ ケージ組み立てのロボット速度を 30 mm/秒にそれぞれ最適化した場合の、各部品の組み立てに要する最適なサイクル タイムを示します。この最適なサイクル タイムは、ケージ組み立てプロセスの産業化に関する要件を満たしています。
表 1
組み立て品 | ボトム ケージ | セパレータ #1 | セパレータ #2 | セパレータ #3 | キックアウト バネ | トップ ケージ |
サイクル タイム (秒/個) | 2.2 | 4.6 | 3.2 | 3.4 | 4.0 | 7.0 |
考察および要点
シートメタル ケージ組み立て用の生産機械の開発
この研究では、ロボットベースのシートメタル ケージ組み立てシステムの実現可能性を検証し、組み立てプロセスの最適化と組み立て歩留まりおよび組み立てサイクル タイムの向上を図るために 2 通りの DoE を実施しました。この技術は明らかに産業化の目標を達成可能なことが判明したため、この DoE プラットフォームは現在 D&D 珠海工場に導入されて大量生産に使用されています。最新の生産データによると、このプラットフォームの歩留まりは 98% で、労務費は 4 人の作業員分に削減されました (年間 48,000 ドルの節約)。次のステップは、シートメタル ケージ組み立て用の生産機械を製作することです。この技術を搭載した生産機械を導入すれば、TE D&D 事業部門の労務費は年間 52 万ドル削減されると見込まれます。さらに、ここで開発したロボットベースのシートメタル ケージ組み立て技術は、TE のマス カスタマイゼーションに対応した高精度な組み立て能力を大幅に向上させ、自動車、インダストリアル、CPD、センサなどの他の事業部門でマス カスタマイゼーション対応の組み立て自動化ソリューションを開発するための足掛かりになります。これは間違いなく、TE 全体に大きなビジネス インパクトを生み出します。
謝辞
ロボットベースのシートメタル ケージ組み立て技術の開発に取り組むことは胸躍る経験でした。この取り組みを支持および後援していただいた TE Global Operations および D&D 事業部門のリーダーの方々、特に有益な提案や指導をいただいた Philip Gilchrist 氏、Darel Callis 氏、Rolando Saavedra 氏、Marshall Chen 氏に感謝の意を表します。
参考文献
[1] 技術参考文献 – RAPID Instructions, Functions and Data types, ABB Robot documentation M2004, rev H, RW5.15