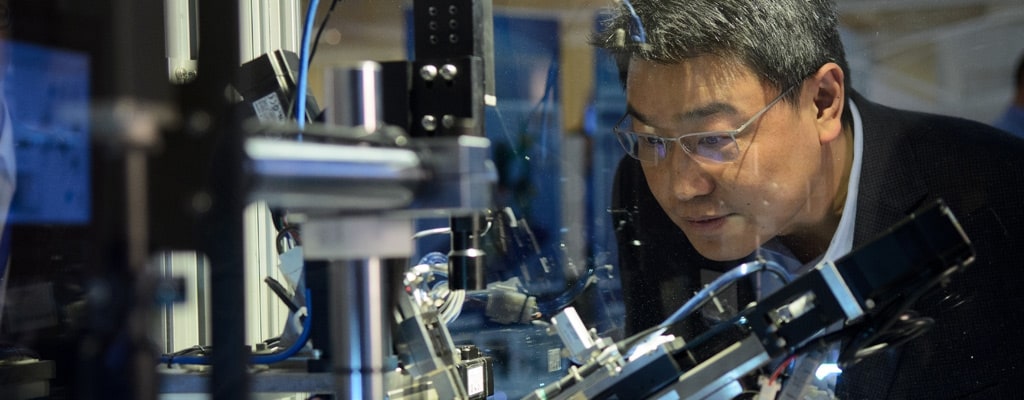
イノベーションの推進
現代の技術市場で勝ち残るには、最適なソリューションの開発、高いカストマー満足度の実現、製品の市場導入の迅速化が必要です。このような成果を迅速に上げる方法として 3D プリンティングがあります。これは、構想から短期間で完全に動作可能な試作品を製作できる重要な技術であり、早期段階で構想を試験してプロセスを効率的に標準化するうえで効果的です。
著者:
Gregory T. Pawlikowski、開発主任エンジニア、 Harrisburg Research Center
Jessica H. B. Hemond、開発主任エンジニア、 Harrisburg Research Center
Ranjan D. Deshmukh、Staff Scientist、 Harrisburg Research Center
動作可能な試作品の製作は、最終製品の製造で使用するプロセスと同等の製造プロセスで、必要な特性と定格を備えたエンジニアリング樹脂を使用することから始まります。 現時点の 3D プリンティング技術では、材料の選択肢がきわめて限られ、必要な物理性能もほとんど得られません。これによって、動作可能な樹脂部品を製造事業者が直接印刷する機能に制約が発生しています。このような制約はあるものの、生産部品と同じ材料とプロセスで、動作可能な試作部品を製作するモールド ツーリングの製作に 3D プリンティングを活用することはできます。これにより、製造事業者は次の 4 点で優位性を得ることができます。
- デザイン検証のための完全な試験
- 生産に対する部品の適性評価
- カストマーによる評価に使用する部品の供給
- 製品開発プロセスの時間短縮
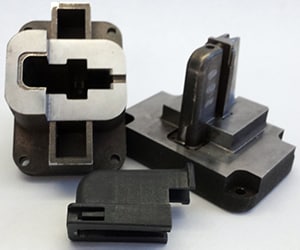
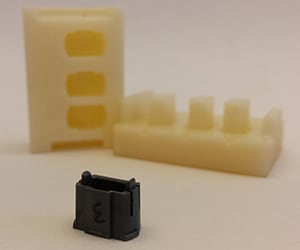
代替手段: 3D プリンティング モールド ツーリング
生産用モールド ツーリングは複数の部分で構成されていることが普通なので、各工具の製造と組み立てでは高精度な機械加工技術が要求されます。 その結果、適正なコストにするには通常は部品の大量生産が必要になります。一般的に少量生産の部品ではこのプロセスは非現実的であり、特にデザインの変更が見込まれる場合はその傾向が強くなります。
クイックターンの切削加工では簡素化したモールド ツーリングを製作できますが、そこでは自動化したコンピューター数値制御 (CNC) のフライス盤を使用します。この方法には、切削工具の到達範囲に問題があり、特に極端に深いキャビティは加工できません。また、内面にある角の曲率半径などで形状に対する制限が発生します。この点に起因して、切削加工ではリード タイムが長くなることもあり、最終的に想定コストを超過する可能性があります。
幸いなことに、3D 印刷モールド ツーリングという代替策があります。この手法では、従来の成形機で使用できるツーリングを製作できるほか、量産グレードの樹脂との互換性も得られます。さまざまな 3D プリンティング技術向けに開発されたこの手法では、モールド ツーリングで金属と樹脂を扱うことができます。機械加工した金属工具には、高い耐久性を備えたきわめて小型の基本形状を実現できる利点がありますが、3D プリンティング ツーリングでは、少量の成形部品を短時間で製作するうえで十分な分解能、熱安定性、材料強度が得られることから、機械加工にはない利点があります。
たとえば、過酷な環境条件に耐えることができる部品を必要とする用途が数多く存在します。 このような部品を製作するには、耐熱性のエンジニアリンググレード樹脂を使用する必要があるほか、厳しい公差を設定した精密な基本形状、薄肉構造、高度な複雑さなどの属性が要求されます。3D プリンティング モールド ツーリングから正確な部品を問題なく成形するにはいくつかの課題があります。TE の担当チームでは、次のような問題を特定して解決しています。
- 印刷の分解能と精度
- 印刷モールド ツーリングの二次仕上げ
- モールド インサートの耐久性
- エンジニアリング樹脂の種類と処理条件
- 成形部品の補修
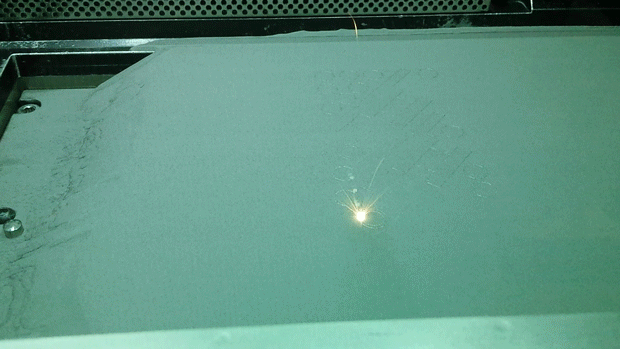
適切なプリンタと適切な材料の選択
これらの課題を解決するには、適切な種類の 3D プリンタと適切な種類のモールド材料の選択から着手する必要があることがわかっています。 印刷モールドの分解能と印刷精度には制限があり、使用するプリンタとモールド材料によっても変化します。当社では、光造形 (SLA) プリンタであれば最高の精度 (0.02 ~ 0.05 mm 以下) および基本形状に対する最高の分解能 (最高で 0.125 mm) の両方を実現できることを見いだしました。このプリンタでは、レーザーを使用して液状樹脂材料を硬化処理します。鋭利ではっきりした輪郭の基本形状や角を持つツーリングも製作できます。
このほかにも重要な技術として、光投影技術を使用する光デジタル処理 (DLP) プリンタや、分注した感光性樹脂の小滴を広帯域紫外光で硬化処理できるモノマー ジェット プリンタなどがあります。直接金属レーザー焼結法 (DMLS) などの粉体層 3D 印刷技術でも優れた精度と分解能を達成できますが、表面仕上げが粗くなります。
検討が必要となる重要な点として、印刷モールドとインサートの二次仕上げがあります。この仕上げによってプロセスの総合的なコストと時間が増大するからです。表面仕上げが粗いと、成形部品表面の品質を損なうだけでなく、モールドから取り出す際に部品に悪影響を及ぼす可能性があります。SLA やモノマー ジェットなどの感光性樹脂硬化技術を使用すれば、比較的滑らかな表面が得られ、後仕上げ処理を最低限にするか、省略できます。
その性質上、DMLS 印刷した金属工具ではどうしても表面が粗くなるので、ある程度の二次機械加工が必要になることが普通です。表面の粗さを許容できるのであれば、ビード ブラスティングや手作業による仕上げなどの軽作業で十分なこともあります。層単位の印刷を採用する場合 (SLA で層の厚みを 0.05 mm とした場合など) は、ポリマ モールド ツーリングでも、ある程度の粗い表面や角の位置に構成する表面の階段状効果の発生は避けられません。
直接金属レーザー焼結法 (DMLS) などの 3D プリンティング技術は、優れた精度と分解能でツーリングの迅速な製作を可能にするうえで TE にとって重要です。
DMLS 印刷金属モールドでは表面の粗さが最大の問題になりますが、ポリマ モールドでは工具の耐久性が大きな課題です。 これは、金属と比較してポリマは本質的に強度が低いことに起因しています。特に、成形温度と成形圧力が高い条件下でさまざまな熱特性と機械特性が介在する場合にこの傾向が強くなります。最終的には、ポリマ ツーリングの機械特性と熱特性によって、正常な成形部品の数やショット数が決まります。
これらの特性はコアの基本形状を保持できるかどうかに直接影響し、成形不足になったモールドインサートの亀裂や変形の原因になることがあります。特にサイズが小さいコアや縦横比が大きいコアでこの影響が顕著です。インサートの亀裂と変形に大きく影響する要因として、高温でのモールド材料の強度、高温のポリマ メルトに接触しているモールド材料の品質劣化、熱膨張率や熱伝導率の差、熱衝撃などがあります。
当社のチームでは、適切なプリンタとモールド材料を選択する際の要素として以下を洗い出しています。
- 部品の形状と最小サイズの基本形状
- 成形する生産用材料
- 必要な部品の数
これらのほかにも成形の成否に影響する要因があります。成形プロセスに適切な条件の設定やポリマ モールドに適するように修正したモールド デザイン ルールの決定などが重要です。
ポリマ モールド ツーリングの耐久性とそれに基づく性能のほとんどは、成形部品に使用するエンジニアリング樹脂、充填剤の種類 (たとえば、非充填樹脂に比べ、研磨性のガラス ファイバを充填した樹脂はモールドの摩耗を促進する原因となる傾向があります)、メルトの粘度、およびモールドの処理パラメータで決まるという点に留意する必要があります。この結果、正確な部品寸法を確保するために、印刷プロセスまたはモデル、あるいはその両方の調整が必要になることがあります。
印刷した金属工具を使用することで、標準的なポリマ処理と収縮値を適用できます。そのような作業をポリマ モールドで実施するには、プロセスの調整とモールド デザインの調整が必要になる場合があります。プロセスとデザインとの適合性をすべて把握することで、この技術から最良の結果を得ることができます。
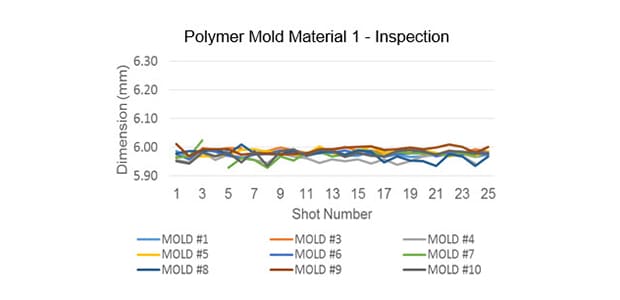
すべてのポリマ モールドが性能面で同等というわけではありません。効果的な結果を得るには適切なモールド材料の選択が重要です。
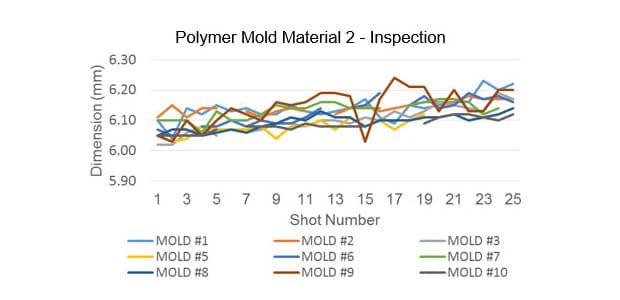
TE では、ポリマ モールドを製作するプロセスの開発と改良を全社体制で継続しており、これらのプロセスを製品のポートフォリオ全体に適用することを目指しています。 樹脂ピラミッドと既存の成形機で使用するほとんどの材料もこの対象になります。デザインとプロセスにおける当社独自の進展を活用することで、印刷ツーリングに存在するこれまでの制約を克服できます。適切なプロセスを使用することで、詳細な基本形状を印刷できるだけでなく、これらの基本形状を成形部品に再現することもできます。このようなプロセスとして、液晶性ポリマ (LCP) などの耐熱材料を印刷ポリマ モールドで成形するものがあります。必要となるすべての公差は使用する技術で決まります。
ポリマ モールド材料の性能は大幅に変化する点に留意が必要です。さまざまなポリマ モールド材料を比較する際に、材料の明らかな優位点となる要素は耐久性と成形サイクルの繰り返しによる摩耗です。公称寸法のモールドを公差の範囲内で実現するにはデザインの調整が必要になりますが、その内容もポリマ モールド材料に基づいて一定の範囲で異なります。
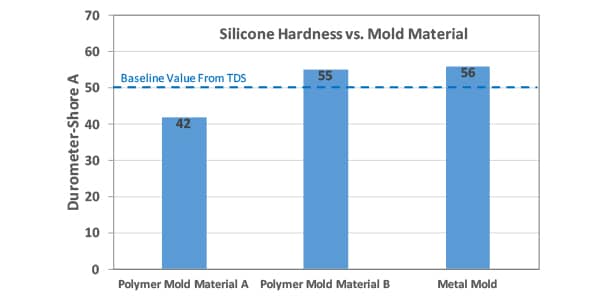
この技術は熱可塑性樹脂以外でも有効です。 当社では、シリコン、フッ素シリコン、他のエラストマなどの熱硬化性樹脂の成形でもこの技術を使用しています。従来のシリコン モールドのコストと複雑さを考慮すると、低コストのクイックターン手法への適合に明らかな利点があります。熱可塑性樹脂をポリマ モールドで成形する場合のように、工具のデザインとプロセスの調整が必要になることがあります。適切なモールド材料の選択はここでも重要ですが、目標は従来のモールドと同等の性能を持つ工具の製作にあります。
所要時間の面でも利点があり、多くの場合は従来の機械加工による方法よりも所要時間は短くなります。印刷プロセスでは短時間で結果が得られるだけではなく (わずか数時間で完了することもあります)、わずかな二次仕上げで使用可能か、二次仕上げを必要とせずに使用可能な印刷モールド ツーリングを製作できます。コストを最小限とし、製作時間を短縮するには、印刷モールドを可能な限り小型化する方針を取り入れます。
3D プリンティング ポリマ モールドで生産できる成形部品の数には限度があることが普通ですが、新しい技術では追加のプリンティング モールドを使用して、実現できる部品総数を数倍にしています。必要に応じ、3D プリンティング金属モールドを使用し、生産処理条件の下で大量の成形部品を生産できます。
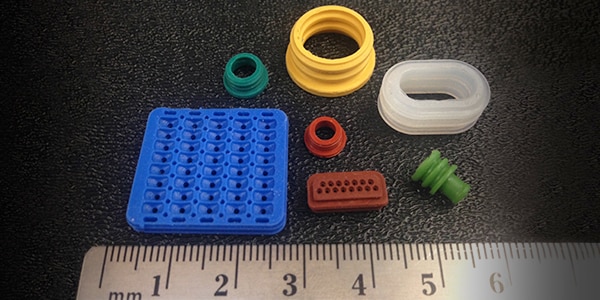
イノベーションに向けた当社の取り組み
TE では、使用しているほとんどの生産用樹脂にこの技術を適用できます。 一方で、克服しなければならない課題が未だにいくつかあります。現在、当社ではより細密な基本形状の耐久性向上に取り組んでおり、エネルギー製品やトランスポーテーション製品のポートフォリオに合わせて、より大規模な製品を生産できるようにプロセスを調整しています。また、厳しい公差と 0.4 mm 未満のファイン ピッチを持つ基本形状に対応できる技術の開発を進めています。
同時に、12 cm を超える部品を生産する際にデザインと処理を調整する作業も進行中です。モールド デザインとプロセスのパラメータを練り上げることで、当社のポートフォリオ全体にこの技術を展開できることが見込まれます。
現在、1 つの 3D プリンティング技法ですべての製品形状や雑多な数量を生産できる状況には至っていません。3D プリンティングに関して、TEは、広範なプリンティング技法を社内展開しています。当社では、モールド ツーリングと成形で当社が有する広範な能力と豊かなノウハウを生かす技術への投資に長期間継続的に取り組んできました。これは、動作可能な試作品を少量生産するための新たなソリューションを開発し、試験できることを目指すものです。3D プリンティング技術に関する当社の幅広い見識は、1980 年代末に始まって現在も進行中のこの取り組みの結果に他なりません。全社的に日々、これらの技術を使用し、社内の専門知識の進展を図っているほか、イノベーションの推進と迅速なツーリング技術の導入に取り組んでいる広範なエンジニアによるグローバルなネットワークにわたる共同作業を進めています。