インプロセスミクロンレベル確度厚さ検査プラットフォーム
要約
重要な製造パラメータである厚さは、プラークの性能に直接影響します。インプロセス検査手法が存在しないために、現在の生産ライン外検査では破壊検査を実施する必要があるうえ、製品の切り替えに伴うコストが毎回数百ドルに上っています。当社のイノベーションによる厚さ検査プラットフォームの 1 つでは、ミクロンレベルの確度で非接触の動的検査を工程の中で実施できます。
問題の提示
プラークは、多くのチップ製品にとって、重要な製品の一種であり、基本的なコンポーネントの 1 つです。プラーク製品は 3 層構成になっています。2 つの金属層と 1 つの PTC (Positive Temperature Coefficient; 正温度係数) 層がまとめてラミネート加工されています。図 1 は、プラークの製造工程を示しています。性能に直接影響する厚さは、プラークの品質面で最も重要なパラメータです。最終製品の厚さがその仕様を満足していない場合、再加工による修正は不可能で、その製品はすべて廃棄することにあります。
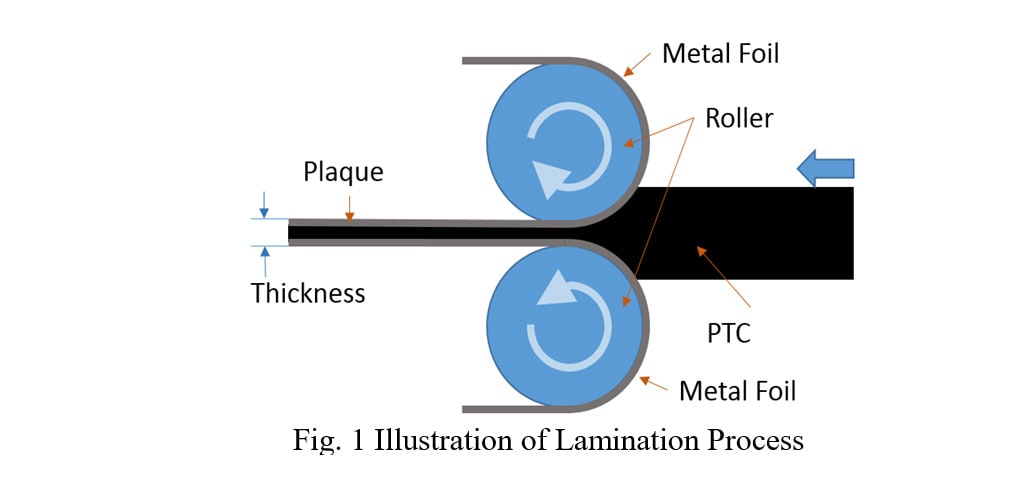
実際の生産現場では、2 本のローラ間の距離をオペレータが調整して厚さを管理しています。問題が発生するのは生産切り替えのときです。製品ファミリ全体で、厚さが異なる 9 種類の型番が存在しています。通常は、1 日に 2 回の頻度で別型番の製品に生産が切り替えられています。
生産切り替えにはきわめて高いコストが発生します。生産ライン上に厚さ検査装置がないと、現在の切り替えは生産ライン外で実施する検査に基づくことになります。オペレータは、最初に数点のサンプルを生産してから生産設備をいったん停止し、サンプルを切断して生産ライン外で破壊検査を実施する必要があります。良好な結果が得られるまで、この検査を繰り返す必要があります。これは手作業によるミクロンレベルの調整であり、難度がきわめて高いうえに時間もかかります。
生産ライン上でプラークの厚さを検査する 1 つのシステムを開発するには、次の 3 点の課題を検討する必要があります。
1) ミクロンレベルの確度
2) 動的検査
3) 非接触検査
当社のイノベーションによる厚さ検査プラットフォームの 1 つでは、ミクロンレベルの確度で非接触の動的検査を工程の中で実施できます。このプラットフォームでは、レーザ技術を使用して非接触検査を実行します。当社では、確度の要件を達成するために 1 つの実験計画法 (DoE) を実施し、動的検査で主要な有力要因と動的検査で求められる確度を達成する方法を把握しています。このプラットフォームは GR&R 認定に適合しています。
解決方法と結果
プラットフォームの概要
図 4 に、このプラットフォームの概要を示します。紫色の部分がプラークを表しています。C 字状のセンサ取り付けフレームの上方部分と下方部分それぞれにレーザ センサを設け、これら 2 つのレーザ センサの相互動作によって厚さを検査します。サーボ モータ駆動の 2 本のシャフトにより、この C 字状フレームが前後に移動します。これらのシャフトは、高い安定性を実現するために大理石製のフレームに取り付けられています。大理石は、座標測定機のような高精度測定システムのベースに使用されることが普通です。大理石製フレームの下には、電気制御系キャビネットが収められています。
生産稼働中は、プラークが検査ステーションを X 方向に連続して通過し、上方レーザ センサと下方レーザ センサが Y 方向に移動して、図 4 の下方に示すジグザグ状の検査軌道を描きます。
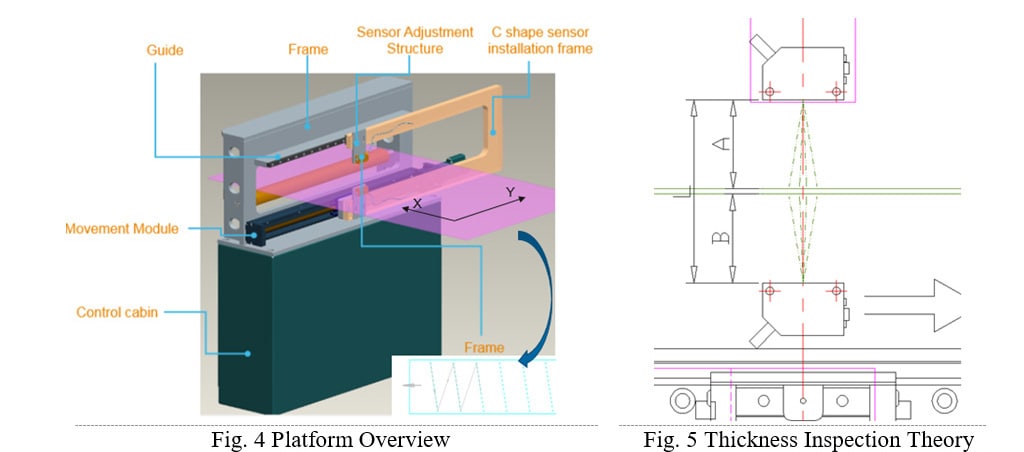
2 つのセンサによる厚さ検査の原理を図 5 に示します。2 つのレーザ センサを使用して、センサと測定対象物との距離を検査します。2 つのセンサ間の距離を L、上方レーザ センサで測定した対対象物距離を A、下方レーザ センサで測定した対対象物 距離を B とすると、次の計算式でプラークの厚さが得られます。
厚さ = L-A-B (1)
ロボットによる DoE プラットフォーム
式 (1) を実際の生産に適用するには、検査環境が検査中に式 (1) の条件を全面的に満足していることを確認する必要があります。しかし、実際の製造環境には、レーザ センサの誤差、プラークの振動、プラークの回転、センサの移動と製品の移動など、多種の雑音源が存在するので、式 (1) を直接適用することは困難です。
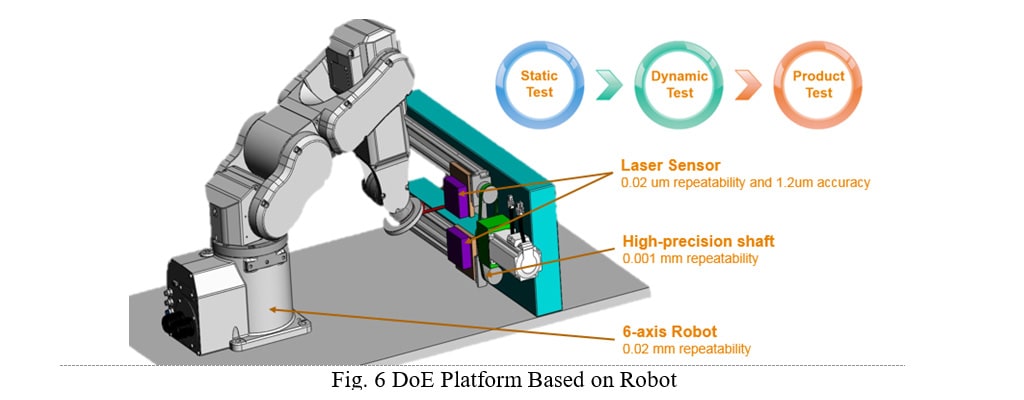
当社では、各有力要因による影響を分析する DoE プラットフォームを構築しました。この DoE プラットフォームは、0.02 mm の再現性を発揮する 6 軸ロボットを使用しています。エンド エフェクタ端に取り付けたグリッパでプラークのサンプルを操作することで、プラークの振動、回転、垂直移動、水平移動をシミュレーションできます。ロボットのほか、重要なデバイスとして、0.02 ミクロンの再現性、1.2 ミクロンの確度を持つ高精度レーザ センサがあります。このセンサを水平方向にシフトするシャフトには 0.001 mm の再現性があります。このシステムの内在確度は目的に対して十分なものです。しかし、この内在確度は外部環境によって低下する可能性があるので、この DoE は、影響を低減して内在確度を回復する手段を探し出すことを目的としています。
当社では、次の 3 種類の実験を実施しています。
- 静的試験: 製品とセンサの両方を静的条件下に置き、システムの再現性と確度を試験します。この試験によってシステムの内在確度が得られます。
- 動的試験: 製品の回転、振動、水平移動、垂直移動による影響を試験し、各要因と確度との関係を見極めます。
- 実製品試験: 実際の製品に対する GR&R 認定
考察および要点
本ホワイトペーパーでは、工程内ミクロンレベル確度検査プラットフォームの 1 つ に関するイノベーションを紹介し、そのプラットフォームの概要、非接触レーザ技術、動的検査の校正アルゴリズム、ソフトウェアと GR&R 認定などを取り上げています。DoE による実験と化学分析に基づいてシステム確度の向上を図る方法について詳しく説明しました。
このプラットフォームの利点は、工程内ミクロンレベル確度の動的特性と非接触性を特徴としていることにあるといえます。この検査プラットフォームは生産ラインに直接統合されるので、オペレータは検査データをリアルタイムで確認できます。このシステムはミクロンレベルの確度を実現し、GR&R 認定を取得しています。この動的検査は多彩な製品を対象とすることができます。さらに、レーザ技術を採用することで非接触検査を実現しています。
このプラットフォームには、厚さ検査を必要とする他の種類の製品にも拡張できる可能性があると同時に、高速な生産ラインと多彩な製品を扱うことができるように機能向上を図ることができる見込みもあります。
インプロセスミクロンレベル確度厚さ検査プラットフォーム
要約
重要な製造パラメータである厚さは、プラークの性能に直接影響します。インプロセス検査手法が存在しないために、現在の生産ライン外検査では破壊検査を実施する必要があるうえ、製品の切り替えに伴うコストが毎回数百ドルに上っています。当社のイノベーションによる厚さ検査プラットフォームの 1 つでは、ミクロンレベルの確度で非接触の動的検査を工程の中で実施できます。
問題の提示
プラークは、多くのチップ製品にとって、重要な製品の一種であり、基本的なコンポーネントの 1 つです。プラーク製品は 3 層構成になっています。2 つの金属層と 1 つの PTC (Positive Temperature Coefficient; 正温度係数) 層がまとめてラミネート加工されています。図 1 は、プラークの製造工程を示しています。性能に直接影響する厚さは、プラークの品質面で最も重要なパラメータです。最終製品の厚さがその仕様を満足していない場合、再加工による修正は不可能で、その製品はすべて廃棄することにあります。
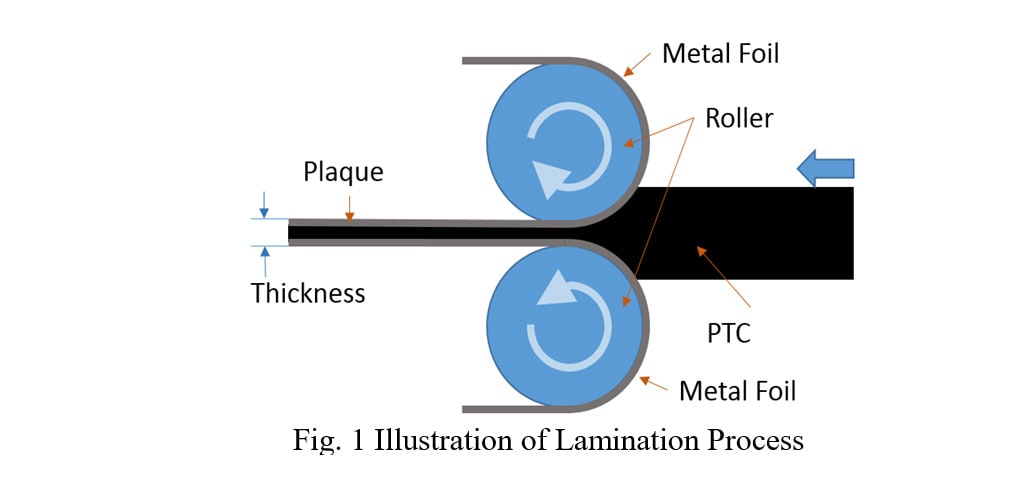
実際の生産現場では、2 本のローラ間の距離をオペレータが調整して厚さを管理しています。問題が発生するのは生産切り替えのときです。製品ファミリ全体で、厚さが異なる 9 種類の型番が存在しています。通常は、1 日に 2 回の頻度で別型番の製品に生産が切り替えられています。
生産切り替えにはきわめて高いコストが発生します。生産ライン上に厚さ検査装置がないと、現在の切り替えは生産ライン外で実施する検査に基づくことになります。オペレータは、最初に数点のサンプルを生産してから生産設備をいったん停止し、サンプルを切断して生産ライン外で破壊検査を実施する必要があります。良好な結果が得られるまで、この検査を繰り返す必要があります。これは手作業によるミクロンレベルの調整であり、難度がきわめて高いうえに時間もかかります。
生産ライン上でプラークの厚さを検査する 1 つのシステムを開発するには、次の 3 点の課題を検討する必要があります。
1) ミクロンレベルの確度
2) 動的検査
3) 非接触検査
当社のイノベーションによる厚さ検査プラットフォームの 1 つでは、ミクロンレベルの確度で非接触の動的検査を工程の中で実施できます。このプラットフォームでは、レーザ技術を使用して非接触検査を実行します。当社では、確度の要件を達成するために 1 つの実験計画法 (DoE) を実施し、動的検査で主要な有力要因と動的検査で求められる確度を達成する方法を把握しています。このプラットフォームは GR&R 認定に適合しています。
解決方法と結果
プラットフォームの概要
図 4 に、このプラットフォームの概要を示します。紫色の部分がプラークを表しています。C 字状のセンサ取り付けフレームの上方部分と下方部分それぞれにレーザ センサを設け、これら 2 つのレーザ センサの相互動作によって厚さを検査します。サーボ モータ駆動の 2 本のシャフトにより、この C 字状フレームが前後に移動します。これらのシャフトは、高い安定性を実現するために大理石製のフレームに取り付けられています。大理石は、座標測定機のような高精度測定システムのベースに使用されることが普通です。大理石製フレームの下には、電気制御系キャビネットが収められています。
生産稼働中は、プラークが検査ステーションを X 方向に連続して通過し、上方レーザ センサと下方レーザ センサが Y 方向に移動して、図 4 の下方に示すジグザグ状の検査軌道を描きます。
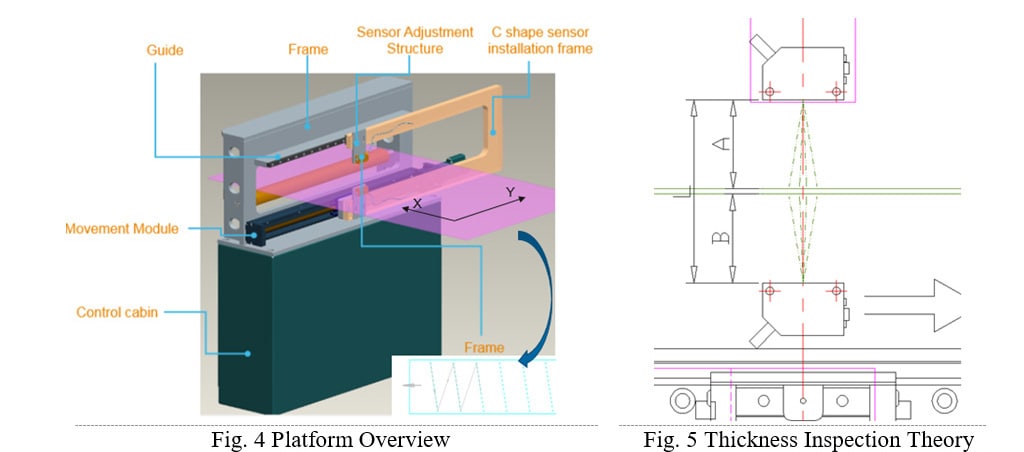
2 つのセンサによる厚さ検査の原理を図 5 に示します。2 つのレーザ センサを使用して、センサと測定対象物との距離を検査します。2 つのセンサ間の距離を L、上方レーザ センサで測定した対対象物距離を A、下方レーザ センサで測定した対対象物 距離を B とすると、次の計算式でプラークの厚さが得られます。
厚さ = L-A-B (1)
ロボットによる DoE プラットフォーム
式 (1) を実際の生産に適用するには、検査環境が検査中に式 (1) の条件を全面的に満足していることを確認する必要があります。しかし、実際の製造環境には、レーザ センサの誤差、プラークの振動、プラークの回転、センサの移動と製品の移動など、多種の雑音源が存在するので、式 (1) を直接適用することは困難です。
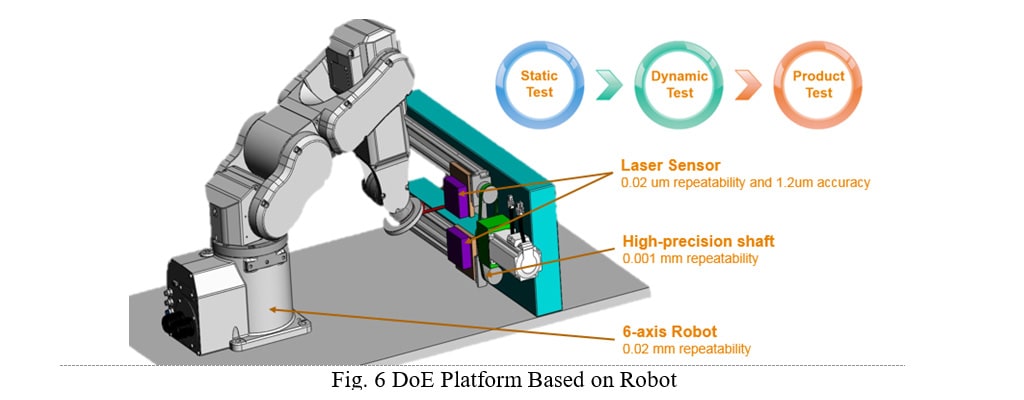
当社では、各有力要因による影響を分析する DoE プラットフォームを構築しました。この DoE プラットフォームは、0.02 mm の再現性を発揮する 6 軸ロボットを使用しています。エンド エフェクタ端に取り付けたグリッパでプラークのサンプルを操作することで、プラークの振動、回転、垂直移動、水平移動をシミュレーションできます。ロボットのほか、重要なデバイスとして、0.02 ミクロンの再現性、1.2 ミクロンの確度を持つ高精度レーザ センサがあります。このセンサを水平方向にシフトするシャフトには 0.001 mm の再現性があります。このシステムの内在確度は目的に対して十分なものです。しかし、この内在確度は外部環境によって低下する可能性があるので、この DoE は、影響を低減して内在確度を回復する手段を探し出すことを目的としています。
当社では、次の 3 種類の実験を実施しています。
- 静的試験: 製品とセンサの両方を静的条件下に置き、システムの再現性と確度を試験します。この試験によってシステムの内在確度が得られます。
- 動的試験: 製品の回転、振動、水平移動、垂直移動による影響を試験し、各要因と確度との関係を見極めます。
- 実製品試験: 実際の製品に対する GR&R 認定
考察および要点
本ホワイトペーパーでは、工程内ミクロンレベル確度検査プラットフォームの 1 つ に関するイノベーションを紹介し、そのプラットフォームの概要、非接触レーザ技術、動的検査の校正アルゴリズム、ソフトウェアと GR&R 認定などを取り上げています。DoE による実験と化学分析に基づいてシステム確度の向上を図る方法について詳しく説明しました。
このプラットフォームの利点は、工程内ミクロンレベル確度の動的特性と非接触性を特徴としていることにあるといえます。この検査プラットフォームは生産ラインに直接統合されるので、オペレータは検査データをリアルタイムで確認できます。このシステムはミクロンレベルの確度を実現し、GR&R 認定を取得しています。この動的検査は多彩な製品を対象とすることができます。さらに、レーザ技術を採用することで非接触検査を実現しています。
このプラットフォームには、厚さ検査を必要とする他の種類の製品にも拡張できる可能性があると同時に、高速な生産ラインと多彩な製品を扱うことができるように機能向上を図ることができる見込みもあります。