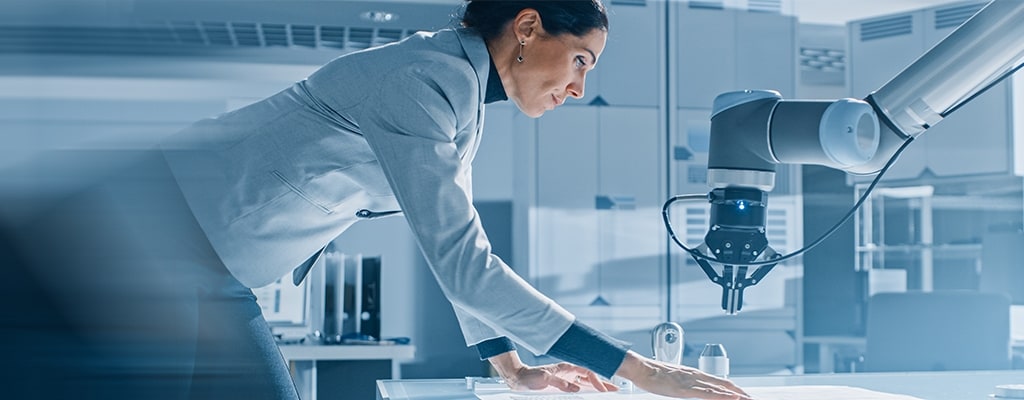
トレンド
トルク センサによる協働ロボットの安全性能の向上
協働ロボット用途における安全性能を向上させる、TE Connectivity (TE) のトルク センサについてご紹介します。
著者:
Arthur Vignolles (TE Connectivity 製品開発エンジニアリング マネージャ)
Ricardo Garcia (TE Connectivity、Product Manager - 荷重センサ&トルク センサ)

協働ロボットで、効率性と利益性を向上
Industry 4.0 が進展し、企業が効率性や収益性の向上を追求し続ける状況において、より洗練されたロボットや高度なオートメーション&コントロール システムを産業用途で使用する動きが広がっています。また、自動化技術の進歩も、協働ロボットの開発を後押ししてきました。協働ロボット (または「Cobot」) とは、人間の身近で、または人間と協力して作業可能なロボットです。人間とのやり取りをまったく、あるいはほとんど行わないスタンドアロン型の自動化装置とは対照的に、協働ロボットは作業員との対話や支援を想定して作られています。歴史上、対話的やり取りが制限されてきた背景には、安全上の懸念や、人間とロボットでは効率的・効果的な共同作業ができなかったという事実があります。
今日では、安全のための保護ケージは不要になり、協働ロボットが人間とシームレスに連動できるようになり、人間だけ、あるいはロボットだけでは実現できなかったタスクが実行可能になったこともあって、作業現場における協働ロボットの柔軟性は飛躍的に向上しています。こうした柔軟性が生産性の向上や人件費の節約につながり、投資利益率 (ROI) の向上にも役立っています。協働ロボットなら、人間では完遂できない、あるいは安全に実行できないような
複雑・危険なタスクにも対応できます。たとえば、協働ロボットは、最高クラスの外科医の能力さえをも凌ぐ正確さと確実さで手術を実行する能力を持っています。安全上の面から言えば、協働ロボットは毒物の取り扱いや、人間には適していない環境での作業にも対応できます。
製品製造作業から産業用パッケージング用途までのあらゆる領域で、協働ロボットは作業現場の生産性向上のため重要な役割を果たしています。企業が協働ロボットの新たな導入手法について模索を続け、協働ロボットを使うメリットについて理解が高まっていることで、工場や製造施設への協働ロボットの導入が大幅に増加しています。国際ロボット連盟 (IFR) によれば、2020 年に設置された協働ロボット台数は 22,000 台で、2017 年と比べて 11,000 台増加しています。さらに、産業用ロボット市場全体でパンデミックによる低迷が確認されたにもかかわらず、世界の協働ロボット売上高は 2018 年から 25% 超上昇しました。中国市場で今後成長するという観点から、協働ロボットの売上高は今後 5 年で 30% 成長することが期待されています。協働ロボットの利用増加に伴い、作業環境の安全を確保し、このような協働ロボットの傍で作業する人間を保護するための規制にも、注目が集まっています。
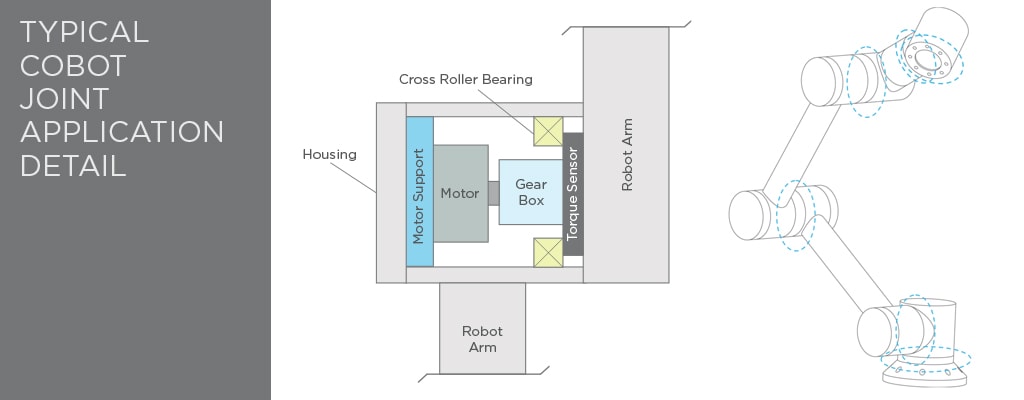
協働ロボットに関する安全要件の整備・拡充が進むにつれて、協働ロボットには、監視・制御を支援するための技術が組み込まれるようになりました。その一例に挙げられるのが、協働ロボットのさまざまな回転・旋回点で機械トルクを監視するトルク センサです。トルク センサは、機械的トルクを、加えられたトルクに比例したデジタル出力信号に変換できる、一体型 MEM ロード セルをベースにしています。このようなトルク センサは協働ロボット内で利用され、トルク レベルが高くなって協働用途において人間を傷つけるおそれがある状態、あるいはトルク レベルによって協働ロボット自体が破損するおそれがある状態の検知に、威力を発揮しています。
TE が提供するセーフティ トルク センサではまず、回転トルクを機械的ひずみに変換するよう設計された一体構造の台座を取り付けます。ピエゾ抵抗ひずみゲージを台座部分に取り付け、機械的ひずみを mV/V 出力に変換できるよう、ホイートストン ブリッジ構成で組み立てます。2 つの小型 基板 には、ASIC その他の電気コンポーネントが取り付けられています。生の mV/V 信号は、補償・増幅されて I2C フォーマットでデジタル化され、バス上で利用できるデータになります。用途に応じて、人にケガをさせる前に、あるいは協働ロボット自体が破損する前に、協働ロボットをシャットダウンさせられるよう、トルク閾値を設定できます。
セーフティ トルク センサは通常、協働ロボットの連結ユニット部分に組み込まれています。連結ユニットは完結型システムであり、通常は 1 つ以上の角度センサのほか、モータとギア ボックスが組み込まれています。連結ユニットは協働ロボットの各アームを駆動させるよう働き、トルク センサはモータおよびギア ボックス内のトルク検出に使われます。制御回路はトルク レベルに応じて連結ユニットをシャットダウンさせ、アームの損傷を防止するほか、協働ロボットとして稼働させている場合は、作業員のケガを防止します。
トルク センサがシステムにもたらす利点がきっかけとなって、協働ロボット用途でトルク センサを活用する流れが促進されました。トルク センサは、より素早い応答時間、より高精度で動作できるため、協働ロボット システムの安全性や信頼性の向上、さらには人間にとっての安全向上にも役立ちます。各アーム ジョイントにトルク センサを使用することで、モータ電流から複雑な計算を行うことなく、アームにかかる外的な力やトルクを直接検知できます。その結果、接触時の停止が非常に高速になり、人間の接触による力を制限しなければならない協働状況においてアームのモーションを高速化できます。協働ロボットが適合モードで動作している際にも利点があります。適合を「アクティブ」にすれば、アームを手動で誘導すること (リードスルー プログラミング) で、協働ロボットに新しいタスクを教えるプロセスを簡略化できます。ジョイントのトルクを直接検知して、誘導したとおりにスムーズかつ正確にアームのモーションを制御できます。

TE が提供するセーフティ トルク センサは、クロス トークによるエラー (アキシャル ロード/ラジアル ロード/傾斜モーメント) を最小限に抑え、正確なトルク データを提供するよう設計されているほか、ギア ボックス内のシール壁としても機能します。ISO13849 カテゴリ 3 PL d までの機能的安全要件に適合するよう、デュアル チャネル システムをベースにした設計を採用しているほか、安全に影響を及ぼす不具合を検出するための機能も盛り込んでいます。TE が提供するトルク セーフティ センサは、今後も Industry 4.0 の発展の推進役であり続ける協働ロボットの、安全性・信頼性向上への道をリードしています。

