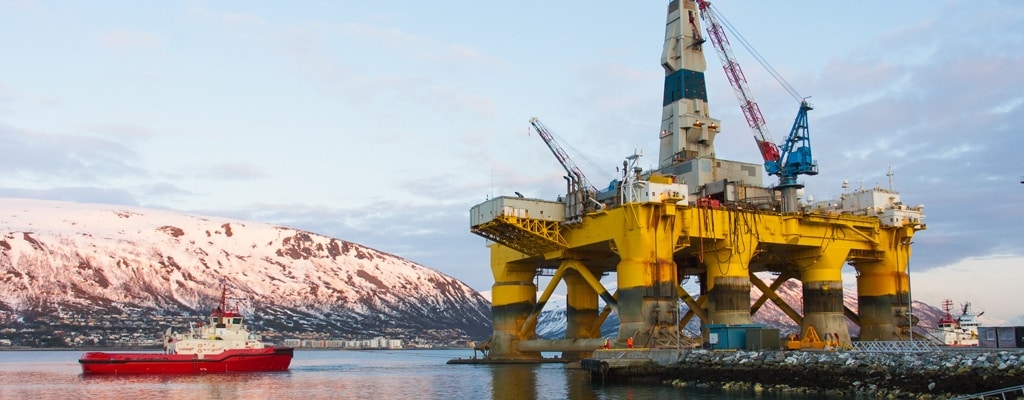
Trend
Zuverlässige Leistung für Tiefseefahrzeuge
Dank neuer Techniken bei Isolierung und Glasfaserverpackung können Versorgungskabel ROVs mit mehr Energie versorgen und immer anspruchsvollere Einsatzmöglichkeiten unterstützen.
Offshore-Aktivitäten dringen in immer tiefere Gewässer und an entferntere Orte vor, deshalb entstehen bei allen Erkundungs- und Entwicklungsaufgaben neue Herausforderungen und eine zunehmende Komplexität.
Die meisten Schlagzeilen zu diesem Thema betreffen die Weiterentwicklung der Plattform- und Steigleitungstechnologie, den Trend zu Bohrschiffen der nächsten Generation sowie die Erhöhung der Produktionskapazitäten für die Unterwasserverarbeitung. All diese Technologien erfordern außerordentlich komplexe Lösungen und werden die Branche weiterhin revolutionieren. Deren Einsatz und Erfolg sind aber immer noch von der Weiterentwicklung kabelgeführter Unterwasserfahrzeuge abhängig, die Schritt halten muss, damit diese Technologien in die Praxis umgesetzt werden können.
33"
Biegeradius des mehrschichtigen Versorgungskabels von TE
2771
Pfund Gewicht in Wasser – pro 1000 Fuß – für das Versorgungskabel von TE
10.000
PSI hydrostatischer Druckwiderstand für die STEEL-LIGHT-Armierung von TE
Arbeiten in der Tiefsee
Stellen Sie sich die grundlegende Herausforderung vor, ein ROV in Tiefseezonen physisch zu platzieren, um die entsprechenden Aufgaben verrichten zu können. Während herkömmliche ROVs in Gewässern mit rund 2500 Metern Tiefe eingesetzt werden, finden viele der heutigen Aktivitäten in Tiefen von über 4000 oder sogar 5000 Metern statt. Die zunehmende Größe, das Gewicht und die Versorgungskapazität des Versorgungskabels, das für solche Aktivitäten notwendig ist, können einen leicht ins Staunen versetzen.
Widerstandsfähig gegenüber rauen Bedingungen
Ein Versorgungskabel für ROVs muss eine Reihe mechanischer und umgebungsbedingter Anforderungen erfüllen, die bei anderen Anwendungen normalerweise nicht anfallen. In der Tiefsee liegen die Temperaturen normalerweise bei 0 bis 3 °C. Auch die Drücke müssen berücksichtigt werden. Bei 2000 Metern übersteigt der Druck von Ozeanwasser 2900 psi (2000 N/cm2). Berücksichtigt man dann noch die großen Kabellängen und die erforderliche Widerstandsfähigkeit gegenüber Verdrehungen und anderen Bewegungen, wird deutlich, dass die Zugbeanspruchung des Kabels eine große Herausforderung darstellt.
Beim Verpacken der erforderlichen Elemente in einem Versorgungskabelsatz müssen diese mechanisch und vor Umgebungsbedingungen geschützt werden. Gleichzeitig sollte das Design nicht größer und schwerer als nötig sein und genügend Flexibilität aufweisen, um sich den Bewegungen des ROV anzupassen. Versorgungskabel dienen normalerweise auch als primäres Hebekabel für das ROV. Die Schwierigkeit beim Design liegt darin, den Mittelweg zwischen einem mechanisch robusten Kabel sowie einer Minimierung von Größe und Gewicht zu finden.
Informationen zu Versorgungskabeln
Angesichts der Komplexität des Designs und der Tatsache, dass Versorgungskabel extrem zuverlässig sein müssen, konnten sich nur eine Handvoll Unternehmen das Vertrauen der globalen ROV-Gemeinschaft erarbeiten, solche Kabel fertigen zu können. Kleinere und leichtere Kabel vereinfachen den Bordeinsatz, indem der erforderliche Platz zum Winschen der Ausrüstung und Lagern der Kabel reduziert wird. Da Tiefsee-Versorgungskabel mehrere Tausend Meter lang sind, kann ein um 10 Prozent verringerter Kabeldurchmesser zu erheblichen Platzeinsparungen auf dem Schiffsdeck führen. Ein Hochleistungs-Versorgungskabel enthält normalerweise mehrere Arten von Komponenten, um Stromversorgung, Steuerung, Video und Telemetrie zu handhaben. Daher finden Sie eine Kombination aus Stromkabeln mit größeren Leitern, Elementen mit verdrilltem Paar und mehreren Leitern, Koaxial-Kabeln und Glasfaserkabeln vor, um die speziellen Anforderungen der Anwendung zu erfüllen.
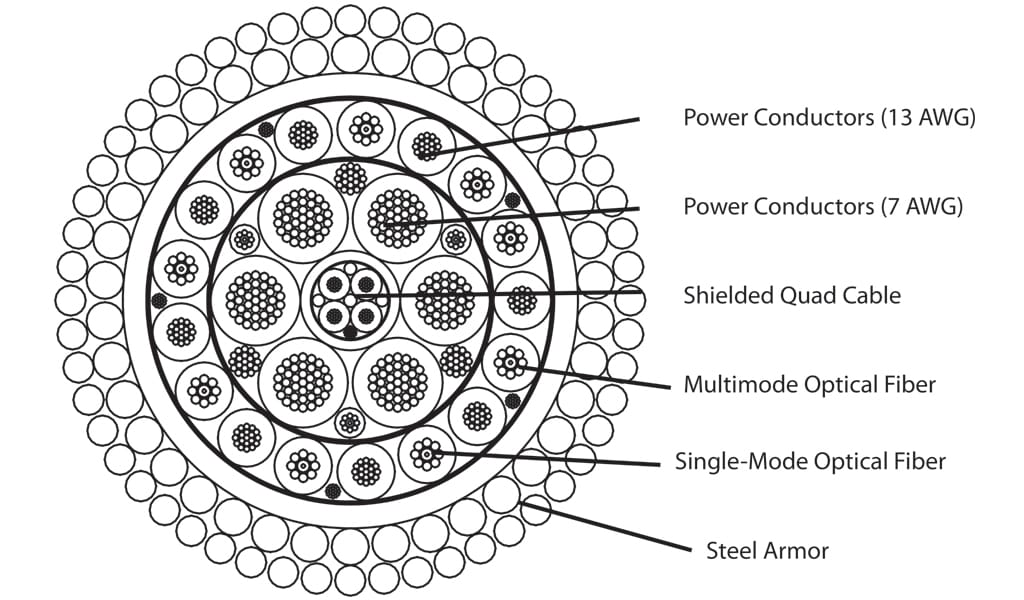
Ein typisches Versorgungskabel ist ein armierter Bausatz mit Signalleitern, Stromleitern und Glasfasern.
Auf den Durchmesser kommt es an, um die Konzentrizität zu bewahren.
Ein Versorgungskabel besteht normalerweise aus mehreren konzentrischen Schichten. Die Abbildung weiter oben zeigt einen Konstruktionstyp von TE Connectivity (TE), der Stromversorgungs-, Multimode- und Singlemode-Glasfaserkabel sowie ein Quad-Kabel in einem doppelt armierten Kabel miteinander kombiniert. Wie Sie sehen, ist dies ein sehr komplexes Design, und es ist wichtig, dass alle Elemente aufeinander abgestimmt sind, um die erforderlichen Kriterien bezüglich Stromversorgung, Daten und Mechanik zu erfüllen. Die einzelnen Schichten werden nicht anhand ihrer Funktion, sondern anhand des Durchmessers der einzelnen Kabelelemente definiert, um die Konzentrizität zu bewahren. Bei einigen Kabeln sind die Stromkabel beispielsweise nahe der Mitte, während sie sich bei anderen Kabeln in den äußeren Schichten befinden. Die Konzentrizität muss unbedingt beibehalten werden, um ein ordentliches und effizientes Winschen zu ermöglichen und robuste Flexibilität zu erzielen.
Jede Schicht wird mit einem Band umwickelt, das normalerweise aus Aluminium/Polymer besteht, und Hohlräume werden mit wasserblockierenden Materialien gefüllt. Nicht in der oberen Abbildung aufgeführt sind die Beidrähte und Füllmaterialien. Diese werden je nach Bedarf hinzugefügt.
Die äußere Armierung dient als Festigkeitsträger und Schutz des Kerns. Außerdem entlastet sie die Kabelkomponenten von der allgemeinen Zugbeanspruchung, die auf das Kabel einwirkt. Der Durchmesser des Kabels beträgt 42,42 mm. Sein Gewicht in Wasser beträgt 2771 Pfund pro 1000 Fuß (4123 kg/km). Es weist eine Traglast von 35.000 Pfund (156 kN) und einen Biegeradius von 84 cm auf. Der Biegeradius muss besonders beim Durchmesser der Laufrolle berücksichtigt werden. Die Verwendung des Kabels bei kleineren Biegeradien kann zu einem erhöhten Ermüdungswiderstand und einer kürzeren Lebensdauer führen.
Angesichts der Herausforderungen beim Entwickeln robuster Versorgungskabel verwenden Entwickler moderne Simulationstools, um die mechanische und elektrische Leistung zu analysieren. Es ist nicht praktikabel, Prototypen von mehreren Kilometern Länge zu anzufertigen. Daher sind Fachkenntnisse in Design und Simulation entscheidend.
Die aktuellen Bemühungen um Innovationen bei Versorgungskabeln konzentrieren sich auf den Kern des Kabels. Dabei wird nach Möglichkeiten gesucht, mehr Funktionalität auf dem gleichen oder kleinerem Raum unterzubringen. Die Ingenieure, die unsere Rochester Cable-Produktfamilie entwickeln, arbeiten beispielsweise mit einer dünnwandigen Isolierung und Glasfaserverpackung, um die Kabel der nächsten Generation zu entwerfen.
Unterstützung optischer Verbindungen
Glasfaser wird aufgrund der hohen Bandbreite, die damit über lange Strecken übertragen werden kann, immer häufiger in Versorgungskabeln eingesetzt. Glasfaser weist zwar eine hohe Zugfestigkeit in Längsrichtung auf, sie kann jedoch leicht brechen oder beschädigt werden, wenn sie nicht ausreichend geschützt wird. Daher verfügen Glasfaserkabel normalerweise über eine eigene Armierung. Dafür wird Aramidfaser – der gleiche Festigkeitsträger wie bei anderen Glasfaserkabeln – verwendet, in robusteren Designs kann jedoch auch eine metallische Armierung zum Einsatz kommen. Durch die hohen hydrostatischen Anwendungsdrücke kann sich die Dämpfung innerhalb der Glasfaser erhöhen.
Unsere drei Ansätze
- Bei der FIST-Methode (Fiber in Steel Tube) befindet sich die Glasfaser in einem massiven Edelstahlrohr, um sie vor hydrostatischen Drücken, hohen Temperaturen und korrosiven Umgebungen zu schützen. Bei der FIST-Verpackung handelt es sich um ein Design mit losem Rohr, das mehrere Glasfasern aufnehmen kann, die lose im Rohr verlaufen und in Gel eingekapselt werden. Da die Glasfasern innerhalb des Rohrs „schwimmen“, sind diese ein wenig länger als das Rohr, um eine geringe Zugbelastung sicherzustellen. Die FIST-Technologie ist die einfachste und kostengünstigste Methode. Sie sorgt für eine geringe Zugbelastung an der Glasfaser, indem die Beanspruchung des Rohrs von der Beanspruchung der Glasfaser entkoppelt wird. Wenn das Kabel bei der Installation oder Verwendung gestreckt wird, kann die überschüssige Glasfaser die Streckung ausgleichen, ohne strapaziert zu werden. Designs mit losem Rohr sind außerdem sehr beständig gegenüber extremen Temperaturabweichungen, aber nicht so gut für sehr anspruchsvolle Anwendungen geeignet, z. B. in extremen Tiefen oder mit extremen Kabellängen. Mit FIST können auch mehrere Glasfasern mit hoher Dichte im Rohr verpackt werden. Darüber hinaus stellt diese Methode von den insgesamt drei Optionen die einfachste Art dar, die Glasfasern abzuschließen.
- STEEL-LIGHT-Armierung verwendet Stränge aus exakt angepasstem Seilstahl, die konzentrisch um den Glasfaserpuffer gelegt werden, um die Glasfaser vor Bruchschäden zu schützen.
- ELECTRO-LIGHT-Armierung ähnelt der STEEL-LIGHT-Armierung, hierbei wird jedoch Kupfer anstelle von Stahl verwendet. Das Kupfer kann auch für die Energieübertragung verwendet werden, um Verbundkabel mit kleineren Außendurchmessern entwerfen zu können.
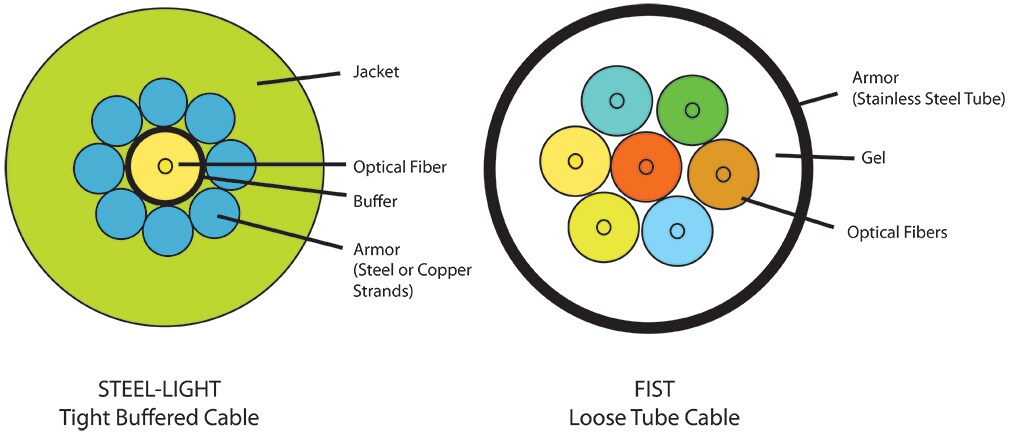
Die innovative Glasfaserverpackung vereinfacht den Einsatz von Glasfaser.
Die STEEL-LIGHT- und ELECTRO-LIGHT-Glasfaserelemente sind fest umhüllte Verpackungsmethoden. Feste Umhüllung erfordert zwar eine sorgfältigere Fertigung, sorgt aber bei hoch dynamischen Anwendungen für eine höhere Leistung und ist die stabilere Wahl. STEEL-LIGHT-Armierung ist am stabilsten und dafür ausgelegt, hydrostatischen Drücken von 10.000 psi standzuhalten. STEEL-LIGHT- und ELECTRO-LIGHT-Glasfasern weisen sehr kleine Durchmesser auf, sodass sie in Zwischenräume im Kabelaufbau eingefügt werden können. Bei einigen neueren Versorgungskabeln mit kleinen Durchmessern, die dünnwandige Kupferleiter verwenden, existieren solche Zwischenräume möglicherweise nicht mehr. FIST ist u. U. die bessere Wahl, um den Kabeldurchmesser in solchen Fällen zu minimieren. Wenn Sie aus diesen drei Optionen die richtige auswählen, können Sie damit viele Herausforderungen bezüglich der Telemetrie bewältigen. Letztendlich geht es darum, den Mittelweg zwischen Robustheit für eine bestimmte Anwendung sowie Kosten, Zweckmäßigkeit und Kabelgröße zu finden. Anbieter von Versorgungskabeln besitzen das Fachwissen, um Sie bei der geeigneten Wahl für Ihre Anwendungen zu unterstützen.
Mehr Energie im Innern
Mit den zunehmenden Einsatzmöglichkeiten von ROVs steigt auch deren Energiebedarf. Es gibt zwei Möglichkeiten, die Belastbarkeit im Kern des Versorgungskabels zu erhöhen. Zum einen können Sie Leiter mit einem größeren Querschnitt verwenden. Dadurch vergrößert sich jedoch auch der Durchmesser des Kabels. Zum anderen können Sie anstelle eines Kabels mit Standardwand eine dünnwandige Isolierung verwenden. Bei TE wird vernetztes Polyethylen (XLPE) für die Isolierung von Stromleitern verwendet. Durch dünnwandige Isolierung kann der Kabeldurchmesser im Vergleich zu Produkten mit Standardwand um 30 Prozent verringert werden. Nach gängiger Meinung muss bei höherer Energieübertragung eine dickere Isolierung verwendet werden. Dank neuer Materialien und Verarbeitungsmethoden ist diese Ansicht jedoch überholt.
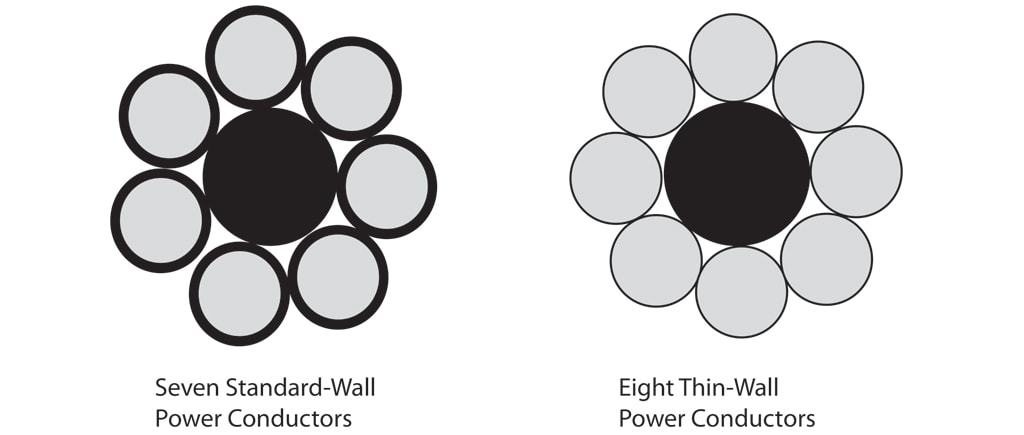
Mithilfe dünnwandiger Isolierungstechnik können mehr Energie und Funktionalität auf gleichem Raum untergebracht werden.
Versorgungskabel für die Tiefe
Dünnwandtechnik ist beim Militär sowie in der Luft- und Raumfahrt weit verbreitet. Dabei werden zum Großteil die gleichen Anforderungen an robuste Leistung erfüllt wie bei Tiefseeanwendungen. Dünnwandige Isolierung bietet eine ausgezeichnete Abriebfestigkeit, eine exzellente Wärmebeständigkeit über einen großen Temperaturbereich sowie elektrische Eigenschaften, die für stromführende Anwendungen benötigt werden. Mithilfe von Dünnwandtechnik können mehr Energie und Funktionalität auf gleichem Raum untergebracht werden.
Durch dünnwandig isolierte Drähte können im Versorgungskabel bei gleicher Größe mehr Leiter untergebracht werden. Gleichzeitig kann das ROV mit mehr Energie versorgt werden. Die Abbildungen weiter oben zeigen ein Beispiel, bei dem acht dünnwandige Leiter auf dem gleichen Raum untergebracht sind wie sieben Leiter mit Standardwand.
Angesichts des steigenden Bedarfs an ROVs zu Forschungszwecken sowie zur Erschließung und Produktion von Öl und Gas erfüllen Versorgungskabel die Anforderungen an eine robuste Leistung. Dank neuer Techniken bei Isolierung und Glasfaserverpackung können Versorgungskabel ROVs mit mehr Energie versorgen und immer anspruchsvollere Einsatzmöglichkeiten unterstützen. Dies drückt sich in leistungsfähigeren Tiefseefahrzeugen mit größerer Reichweite aus, die an ein kompaktes Kabel angeschlossen sind, das für höhere Kapazitäten bei der Energie- und Datenübertragung sorgt.
Mitwirkende Autoren
- Mark Casselton, Product Manager, Marine and Offshore Cables
- Sage Wadke, Global Director, Marketing and Business Development, Aerospace, Defense and Marine