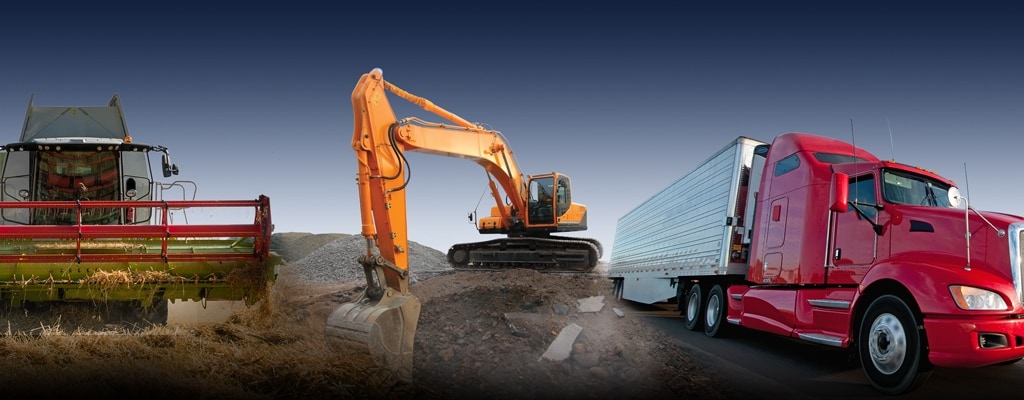
Trend
High-Speed-Datenverbindungen
Um eine Hochgeschwindigkeits-Datenübertragung in Nutzfahrzeugen zu gewährleisten, müssen Sie oder Ihre Entwickler die Komponenten, ihre Platzierung und die Auswirkungen der Umgebungsbedingungen bereits in der frühen Entwurfsphase sorgfältig berücksichtigen.
AUTOR
Christian Manko, Datenverbindungen, Product Manager, TE Connectivity
Technologische Fortschritte
Die Kunden wünschen sich funktionale Produkte, mit denen betriebliche Aufgaben automatisiert oder verbessert werden können, um so die Produktivität und Sicherheit zu steigern, was in vielen Fällen auch zu einer Senkung der Gesamtbetriebskosten führt. Eigenschaften wie automatisches adaptives Bremsen und Lenken, Onboard-Diagnose, Fahrzeug-zu-Fahrzeug (auch V2V, Vehicle-to-Vehicle, genannt) und Fahrzeug-zu-Infrastruktur-Kommunikation (V2I, Vehicle-to-Infrastructure) sowie Kameras, die dem Fahrer einen 360-Grad-Blick auf seine Umgebung ermöglichen, sind zunehmend grundsätzliche Anforderungen der Kunden.
Diese Eigenschaften erfordern die Übertragung großer Datenmengen bei hohen Geschwindigkeiten. Die Herausforderung an die Ingenieure beim Entwerfen neuer Modelle, die diesen Kundenanforderungen gerecht werden, besteht darin, Signalintegrität und Datenübertragung in der rauen Umgebung der LKW- und Off-Highway-Industrie zu gewährleisten.
Anwenden von Ethernet in einer gemischten Architektur
Um den erhöhten Datenbedarf und die Hochgeschwindigkeits-Konnektivität zu bewältigen, ist eine ausgeklügelte Netzwerkinfrastruktur erforderlich. CAN-Bus-Architekturen, die in der Regel Geschwindigkeiten von bis zu 500 Kbps erreichen, bilden seit einigen Jahrzehnten das Rückgrat der meisten Kommunikationsnetze für schwere Nutzfahrzeuge. Allerdings ist die für eine erweiterte Fahrzeugfunktionalität und automatisierte Funktionen für mehr Sicherheit und Produktivität erforderliche Datenbandbreite zu groß, um allein von CAN bedient zu werden.
Das Single-Pair-Ethernet-Protokoll (100BASE-T1 bei 100 Mbit/s oder 1000BASE-T1 bei 1 Gbit/s) bietet die Möglichkeit, Daten mit hohen Geschwindigkeiten zu übertragen. Die Verwendung von Ethernet-Netzwerken und -Steckverbindern ermöglicht es OEM-Designern, mehr Geräte nahtlos in das Netzwerk zu integrieren und die Datenverbindungen in ihren Fahrzeugen zu beschleunigen. Als Punkt-zu-Punkt-Topologie ändert Ethernet jedoch die elektrische und elektronische (E/E) Architektur des Fahrzeugs. Da die OEMs immer mehr Funktionen und Geräte hinzuzufügen, müssen Designer auch Ethernet-Switches berücksichtigen, um Signal und Gateways für die Kommunikation zwischen Ethernet und CAN zu lenken.
Um Platz, Gewicht und Leistung unter rauen Bedingungen zu optimieren, müssen Designer bereits in der Anfangsphase der Entwicklung überlegen, wie sie Ethernet bei Bedarf für erweiterte Funktionalitäten integrieren. Entscheidungen wie z. B. wie viele Kabel im Fahrzeug zu platzieren sind, und wo sie zu legen sind, wo Ethernet-Switches angebracht werden sollen und ob der Switch in eine vorhandene elektronische Steuereinheit (ECU) oder ein neues spezielles Steuergerät zu integrieren ist, müssen für jede Funktion, für die Ethernet erforderlich ist, getroffen werden. Dies ist entscheidend, um Probleme mit elektromagnetischer Interferenz (EMI) oder anderen mechanischen Störungen zu vermeiden oder zu minimieren.

Beispielsweise 360-Grad-Kameras an einem Schwerlastfahrzeug übertragen Hochgeschwindigkeitsdaten von der Außenseite des Fahrzeugs auf die Anzeige in der Fahrerkabine. Vier Kameras (eine an jeder Seite des Fahrzeugs) senden Signale an ein Steuergerät. Designer müssen planen, wo sie einen Switch platzieren, um die Daten der vier Kameras zu kombinieren und in einem Signal an das Steuergerät zu senden. Der Switch kann sich im Fahrzeug oder in einer der Kameras befinden, die vier Anschlüsse haben, um Daten von den drei anderen Kameras aufzunehmen und dann Daten zu senden. Eine weitere Option besteht darin, den Switch in den Videoanzeigebildschirm zu integrieren.
Aufgrund aktiver automatisierter Funktionen wie dem automatischen adaptiven Bremsen und anderen fortschrittlichen Fahrerassistenzsystemen (ADAS, Advanced Driver-Assistance Systems), die ein Multisensor-Array enthalten, muss das Design bereits in den frühen Entwicklungsphasen noch besser durchdacht werden. Jeder Sensor verfügt über eine spezielle Kommunikationsverbindung zu einem Steuergerät. Je mehr Sensoren das Fahrzeug hat, desto mehr Kabel und Kommunikationsverbindungen werden benötigt. Ein autonomes Schwerlastfahrzeug der Zukunft würde beispielsweise ein umfassendes Sensor-Array für etwa 16 Radare, 10 LIDARs und 10 Kameras rund um das Fahrzeug benötigen. Das sind mehr als 30 Kabel und Verbindungen, die EMI-widerstandsfähig sein müssen und deren Verlegung gut durchdacht sein muss, wobei Platzverhältnisse, Gewicht und EMI zu berücksichtigen sind, um die Signalintegrität innerhalb und außerhalb des Gehäuses aufrechtzuerhalten, da die Verbindungen in einem Steuergerät zusammenkommen. Mehr Daten bedeuten, dass eine höhere Bandbreite erforderlich ist. Also müssen auch die verwendeten Steckverbinder und Kabel für eine höhere Geschwindigkeit geeignet sein.
Die immense Größe von Industrie- und Nutzfahrzeugen stellt eine Herausforderung für die Aufrechterhaltung der Signalintegrität und die zuverlässige Datenübertragung dar. Für die Übertragung eines Ethernet-Signals in Autos gibt der Ethernet-Standard technische Anforderungen bis zu 15 m vor. In LKWs, Bussen und Off-Highway-Fahrzeugen muss die Signalintegrität jedoch über größere Entfernungen, bis zu 40 m, und unter erschwerten Bedingungen wie starken Vibrationen, extremen Temperaturen und Stößen, sowie hoher Staubeinwirkung und mehr.
Der Ethernet-Standard legt derzeit bis zu vier Inline-Verbindungen über diese Länge von 40 Metern fest; die Designer müssen also beurteilen, wie lang jedes Segment sein darf, um eine optimale Signalintegrität zu erhalten. Zu den Faktoren, die dies beeinflussen, gehören die Einwirkung äußerer Elemente oder hoher Temperaturen sowie die Platzierung in der Nähe einer Antenne oder einer anderen Komponente, die EMI verursachen könnte. Das Routing ist ein Schlüsselelement beim Designvorgang und die gesamte Bitübertragungsschicht muss für die erwartete Leistung skaliert werden.

Auswahl der geeigneten Komponenten
„Bei der Entwicklung einer gemischten Architektur mit CAN und Ethernet müssen Ingenieure im Voraus bedenken, welche erweiterten, datenlastigen Funktionen die gesamte Konnektivitätsstruktur umfassen soll“, erklärt Abbas Alwishah, Data Connectivity Engineering Manager bei TE Connectivity. „Je fortschrittlicher die Technologie wird, desto wichtiger ist die Zusammenarbeit zwischen OEMs und Zulieferern. Wenn mir ein Kunde sagt, dass er eine High-Definition-Kamera oder ein Näherungserkennungssystem mit sehr geringer Latenz benötigt, kann ich ihm erklären, welche einzelnen Komponenten für diese Funktion oder dieses System benötigt werden – Sensoren, Steckverbinder, Kabelsätze, Antennen, Prozessoren, Displays usw. – und Empfehlungen zur Topologie geben, um Leistung, Platzbedarf, Gewicht und Kosten zu optimieren.“
Um eine zuverlässige Datenübertragung in Schwerlastfahrzeugen mit langer Lebensdauer zu gewährleisten, müssen Ethernet-kompatible Komponenten gewählt werden, die rauen Bedingungen standhalten. Automotive Ethernet-Steckverbinder (ursprünglich für Personenkraftwagen entwickelt) können in der Kabine oder in anderen Bereichen des Fahrzeugs verwendet werden, die keinen extremen Stößen, Temperaturen oder anderen Elementen ausgesetzt sind und wo daher keine besonders robusten Steckverbinder und überlange Kabel benötigt werden. Ein hochwertiges, ungeschirmtes Twisted-Pair-Kabel ist in den meisten Bereichen des Fahrzeugs für Ethernet geeignet. Abgeschirmte Twisted-Pair-Kabel werden nur bei Bedarf verwendet. Die Auswahl des Entwicklers trägt ebenfalls dazu bei, Kosten zu kontrollieren sowie Platz und Gewicht einzusparen.
Modulare und skalierbare MATEnet-Steckverbinder, die von TE für Automotive Ethernet entwickelt wurden, können auch in Schwerlastfahrzeugen für Anwendungen eingesetzt werden, die mittlere bis große Datenmengen und niedrige Latenzen erfordern, wie z. B. Onboard-Diagnose (V2X-Technologien), Telematik, Schalttafel-Infotainment, ADAS und mehr. Die Steckverbinder können Daten mit 100 Mbit/s bis 1 Gbit/s (pro IEEE 100BASE-T1/1000BASE-T1) übertragen und mit ungeschirmten oder geschirmten Twisted-Pair-Kabeln verwendet werden.
Ins Fahrgestell integrierte Komponenten erfordern mehr als nur Robustheit. Sie müssen mechanisch zuverlässig und leicht zu warten sein, extremen Temperaturen standhalten und auch bei größeren Kanallängen effizient funktionieren. Bei höheren Frequenzen können die Kabel-/Steckverbinderqualität und das Design erheblichen Einfluss auf die Kanalleistung haben. Dies hat Auswirkungen auf die Systemleistung und folglich auch auf die Anwendungsleistung. Insbesondere bei im Fahrgestell integrierten Komponenten müssen die Entwickler auf Kabel und Steckverbinder setzen, die für die Hochgeschwindigkeits-Datenübertragung in rauen Umgebungen ausgelegt sind.
„Beim Versuch, den Wunsch nach mechanischer Belastbarkeit zu erfüllen, sind manche Entwickler möglicherweise dazu geneigt, ein größeres, robusteres Gehäuse einzusetzen. Aber die dickeren Wände können die elektrische Leistung beeinträchtigen“, erklärt Mark Brubaker, Product Manager im Bereich Datenverbindungen bei TE. „Es ist zwar wichtig, zu wissen, was in der Vergangenheit funktioniert hat, aber ebenso wichtig ist es, die heutigen elektrischen Anforderungen für die Übertragung von Hochgeschwindigkeitsdaten zu verstehen, und zu prüfen, welche Leistung Verbindungen bei höheren Frequenzen erbringen.“
Beim Design von fortschrittlichen und automatisierten Funktionen, die eine Hochgeschwindigkeits-Datenübertragung erfordern, muss die Produktwahl und -platzierung bereits im Voraus gut bedacht werden. Bei der Integration von Ethernet in die Architektur von Schwerlastfahrzeugen müssen die Konstrukteure die damit in Zusammenhang stehenden Komplexitäten heute sehr viel früher und ausgiebiger bedenken als früher, um erfolgreich eine Balance zwischen Zuverlässigkeit und mechanischer Belastbarkeit und den elektrischen Anforderungen hinsichtlich Hochgeschwindigkeitsdaten und größeren Kanallängen sowie dem Bedarf nach einer einfachen Wartung herzustellen.
Durchsuchen Sie unsere Lösungen für vernetzte Schwerlastfahrzeuge
Um mehr über unsere Lösungen für vernetzte Fahrzeuge zu erfahren
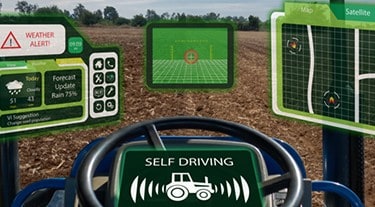
Autonomes Fahren
Ethernet-Lösungen
Erfahren Sie mehr über die Anforderungen an die Konnektivität, die das autonome Fahren von Nutz- und Industriefahrzeugen ermöglichen.
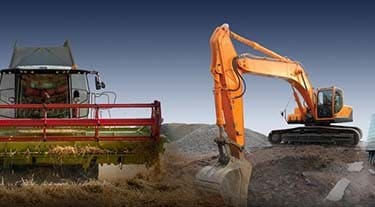
Datenverbindungen
Lösungen für schwere Nutzfahrzeuge
Erfahren Sie, wieso die Produktentwickler die Integration von Ethernet-Systemen in ihren Industrie- und Nutzfahrzeugen sowie Baumaschinen berücksichtigen müssen, um den Anforderungen zukünftiger Kunden gerecht zu werden.
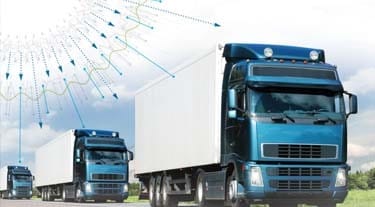
Ethernet-Konnektivität
Anforderungen an schwere Nutzfahrzeuge
Erfahren Sie etwas über die Überlegungen, die wir bei der Entwicklung unserer Ethernet-Steckverbinder für schwere Nutzfahrzeuge angestellt haben.
Ursprünglich veröffentlicht in „Truck & Off-Highway Engineering“