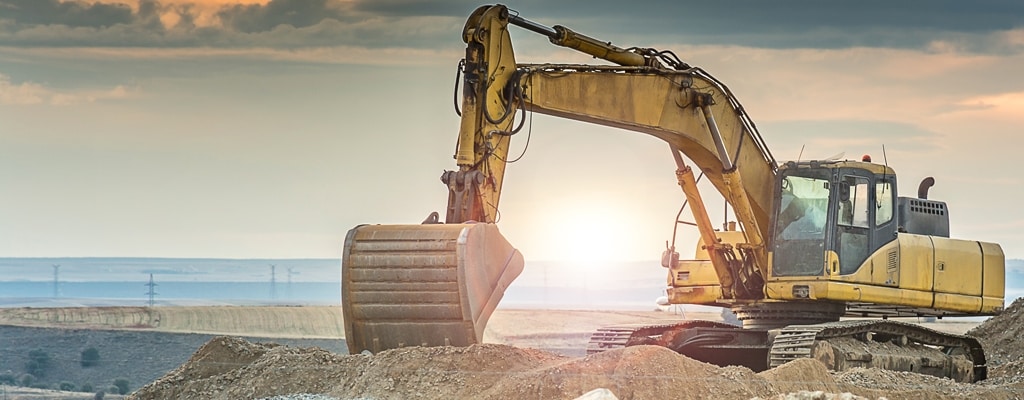
Anwendung
Der Leistungsdruck in hydraulischen Systemen und Kreisläufen
In den letzten zwei Jahrzehnten hat die Hydraulikindustrie von den Fortschritten in der Elektronik, der weit verbreiteten Einführung des IoT (Internet der Dinge), der Senkung der Technologiekosten und der Miniaturisierung von Komponenten profitiert. Darüber hinaus hat die Hydraulikindustrie bei der Umstellung von herkömmlichen Druckschaltern auf Drucksensoren und -Messumformer immer mehr Herausforderungen zu bewältigen. Diese Herausforderungen umfassen etwa Druckanstieg, höhere Betriebstemperaturen, Einsatz in gefährlichen und rauen Umgebungen sowie Druck-Störsignale in Hydraulikkreisläufen. Dies sind Herausforderungen für Konstrukteure und Systemintegratoren und können zu Projektverzögerungen oder Problemen mit der Zuverlässigkeit im Feld führen, wenn sie nicht angemessen angegangen werden. Auch diese Druckmessgeräte haben sich weiterentwickelt, von der Messzelle über das mechanische Gesamtpaket bis hin zum elektronischen Ausgangssignal und der Signalaufbereitung. In diesem Bericht werden wir die Technologie betrachten, die hinter Drucksensoren und -Messumformern steckt, erfahren Sie etwas über die allgemeinen mechanischen Herausforderungen, denen diese Sensoren ausgesetzt sind, und darüber, wie der Druckmessumformer M9100 von TE Connectivity (TE) in diesen anspruchsvollen Umgebungen funktioniert.
Sensortechnologie
Ein Blick in Ihren Sensor
Äußerlich sehen Druckmessumformer alle relativ gleich aus, doch das Kernstück der Messzelle ist zwischen den verschiedenen Sensorherstellern sehr unterschiedlich. Einer der gängigsten wirtschaftlichen und technologisch machbaren Ansätze ist die Verwendung eines Dehnungsmessstreifens als Sensorelement, um die mechanische Belastung, die der Druck auf eine Membran ausübt, in ein genaues und wiederholbares elektrisches Ausgangssignal zu übertragen. TE verwendet seine Microfused-Dehnungsmessstreifentechnologie in einer Wheatstone-Brückenkonfiguration, um die Dehnung in ein Spannungsausgangssignal umzuwandeln. TE hat das Sensorelement als ein einziges bearbeitetes Bauteil konzipiert, das in den Gewindeanschluss integriert ist. Dieses optimierte Design sorgt für ein robustes Signal des Sensorelements und bietet ein hohes Maß an Überdruck- und Berstleistung.
TE verwendet ein Glasbondverfahren, um die Silizium-Dehnungsmessstreifen mit dem Metallanschluss zu verschmelzen. Die Messstreifen sind optimal positioniert, um die Dehnung bei Druckänderungen korrekt zu messen. Zur Herstellung der Verbindungen zwischen den Messstreifen und der Auswerteelektronik werden industrieerprobte Drahtbondverfahren eingesetzt. Konkurrierende Technologien auf dem Markt für hydraulische Drucksensoren, wie Dünnschicht-, Dickschicht- und keramikbasierte Technologien, verwenden separate Membranen mit Sensorelementen mit geringer Empfindlichkeit. Diese Technologien erfordern zusätzliche Schweißnähte in den Flüssigkeitswegen, internen O-Ringen oder zusätzliche Verarbeitungsschritte, die lange für lange Lieferketten-Durchlaufzeiten sorgen können. Alternative Technologien erfordern möglicherweise hohe Dehnungen in ihrem Sensorelement, um die geringe Empfindlichkeit zu kompensieren. Diese hohen Belastungen zusammen mit der mehrteiligen Konstruktion können zu einer reduzierten Langzeitstabilität und Haltbarkeit führen. Die Microfused-Dehnungsmessstreifentechnologie von TE hat sich seit Jahrzehnten in der großvolumigen Fertigung bewährt, birgt ein geringes Risiko von Lieferkettenunterbrechungen und liefert eine robuste einteilige Flüssigkeitsverbindung, die das Risiko von internen Sensorausfällen und anderen mechanischen Herausforderungen reduziert.

Mechanische Herausforderungen
Da Druckmessumformer als Teil eines hydraulischen Systems montiert werden, sollten verschiedene mechanische Herausforderungen bei der Konstruktion berücksichtigt und erkannt werden. Nachfolgend sind die typischen Bereiche innerhalb hydraulischer Systeme aufgeführt, die Systemdesigner im Rahmen des Designprozesses berücksichtigen müssen:
- Arbeitsdruck
- Druckspitzen
- Prüfdruck
- Flüssigkeitsverbindungen
- Berstdruck
- Vibrationen/Mechanische Stöße
- Druckermüdung
- Beständigkeit gegenüber Umwelteinflüssen
Jedes dieser Probleme wird durch das Design und die Validierung des Sensors angegangen. Überdruckwerte, Berstdruckwerte, Ermüdungsanalysen und die Verwendung von Druckdämpfern sind bei TE Teil des Designprozesses und werden sowohl durch Simulation als auch durch empirische Tests validiert.
Arbeitsdruckbereich
Einfach definiert, ist dies der Druckbereich, der eine Systemsteuerung oder -rückführung erfordert. Im typischen Betriebszustand wird das System immer innerhalb dieses Bereichs bleiben. Drücke außerhalb dieses Bereichs erfordern normalerweise keine Messung.
Prüfdruck
Bei der Systemauslegung treten häufig Druckereignisse auf, die den benötigten Messbereich überschreiten, aber keine Schäden am System verursachen sollten. Typischerweise wird erwartet, dass das System nach einem Überdruckereignis wieder in die normale Funktion zurückkehrt. TE spezifiziert den Prüfdruck als den Druck, der auf die Messzelle ausgeübt werden darf, ohne eine dauerhafte Änderung der Ausgangscharakteristik oder der Genauigkeit des Druckmessumformers zu verursachen.
Berstdruck
Es kann potenzielle Fehlermodi auf der Systemebene geben, die dazu führen können, dass das System übermäßige Drücke erfährt, die ein Versagen des Druckbehälters riskieren. TE entwickelt und validiert seine Druckmessumformer sowohl theoretisch als auch empirisch, um den Mindestdruck festzulegen, dem der Sensor ausgesetzt werden kann, ohne zu reißen.
Druckermüdung
Typische Druckermüdung findet man in Systemen, in denen es eine Pumpe oder ein Ventil gibt, die ständig zu Druckschwankungen im System führen. Diese Schwankungen variieren in Ausmaß und Häufigkeit. Eine Pumpe kann eine Hochfrequenz-Druckschwingung mit sehr geringer Größe erzeugen, während ein Ventil zu einer signifikanten Druckänderung führen kann. Dies geschieht aber seltener. In einigen Fällen kann das Gegenteil eintreten. Es ist unmöglich, jedes potenzielle Systemverhalten vorherzusagen. Daher wird der M9100 von TE von 0 bis zum vollen Druckzyklus mit bis zu 10 Mio. Zyklen getestet und theoretisch validiert. So kann bestätigt werden, dass die Spannungen unterhalb der Ermüdungsgrenze bleiben, was für eine im Wesentlichen unbegrenzte Lebensdauer innerhalb des Betriebsbereichs und oft auch innerhalb des Prüfdruckbereichs sorgt. Es sollte darauf hingewiesen werden, dass, da das Sensorelement von TE viel empfindlicher ist als konkurrierende Technologien, das Belastungsniveau so niedrig ist, dass die Druckermüdung kein Problem darstellt.
Druckspitzen
Die vielleicht versteckteste Herausforderung in einem hydraulischen System ist das Vorhandensein von sehr hochfrequenten Drucktransienten, die gemeinhin als „Druckspitzenn“ bezeichnet werden und manchmal auch als Wasserschlag-Effekt bezeichnet werden. Eine Druckspitze kann während der Ventilbetätigung auftreten; auferlegte Druckwellen aufgrund der Systemarchitektur oder die Einfuhr von Luft in die Hydraulikpumpe. Der Druckspitze ist typischerweise durch einen extrem schnellen Druckanstieg (typischerweise Mikrosekunden) auf sehr hohe Amplituden (potenziell 10-facher Betriebsdruck) gekennzeichnet. Die Geschwindigkeit einer Druckspitze kann so schnell sein, dass ein typischer Drucksensor möglicherweise nicht erkennen kann, dass es zu dem Ereignis kam. Dieses Phänomen kann jedoch den Druckmessumformer dauerhaft beschädigen, was zu einer permanenten Nullpunktverschiebung führt, den Sensor nicht mehr auf Druck reagieren oder die Membran reißen lässt, wodurch die Flüssigkeit in das Sensorgehäuse eindringt. Oft verfügen Kunden nicht über die richtige Ausrüstung, um Druckspitzen in ihrem System richtig zu identifizieren, doch die Auswahl eines Druckmessumformers mit der richtigen Technologie kann ihnen dabei helfen. Das robuste Design des M9100 von TE und der optionale Dämpfer reduzieren die potenziellen Ausfallmodi, die durch Druckspitzen verursacht werden.
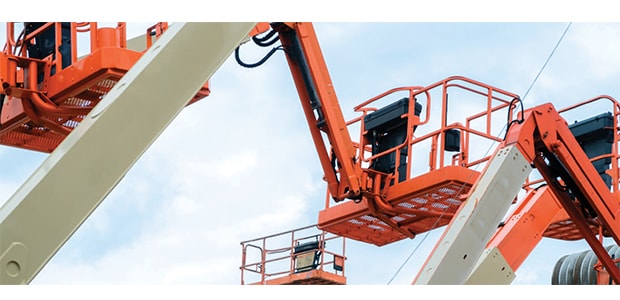
Flüssigkeitsverbindungen
Eine weitere mechanische Überlegung ist der Anschluss an den Hydraulikkreislauf. Es gibt verschiedene Gewindeanschlussoptionen, die in den globalen Regionen beliebt sind, einschließlich SAE (Nordamerika), G-Serie (EMEA) und Metrik (APAC). TE verfügt über langjährige Erfahrung mit historischen Industriestandards wie SAE J1926 oder ISO 1179 und hält stets mit den sich ändernden Anforderungen Schritt. Da hohe Drücke in der Hydraulikindustrie immer häufiger vorkommen, sollten zusätzliche Vorsichtsmaßnahmen getroffen werden, um sicherzustellen, dass der Druckmessumformer richtig ausgelegt, eingesetzt und angezogen ist.
Vibrationen/Mechanische Stöße
Mechanische Stöße und Vibrationen sind traditionell in der Sensorindustrie miteinander verbunden. Druckmessumformer sind aufgrund der spezifischen mechanischen Umgebung der Anwendungen, in denen sie eingesetzt werden, häufig sowohl den Bedingungen im On- als auch im Off-Road-Bereich ausgesetzt. Von den hochfrequenten Vibrationen eines Dieselmotors bis hin zu den Erschütterungen eines Gabelstaplers, der eine volle Ladung auf den Boden fallen lässt, erfordern diese Bedingungen, dass der Druckmessumformer immun gegen die nachteiligen Auswirkungen von „Schock und Vibration“ ist.
Beständigkeit gegenüber Umwelteinflüssen
Die Beständigkeit gegenüber Umwelteinflüssen ist von entscheidender Bedeutung, um sicherzustellen, dass jedes Produkt den extremen Umweltbedingungen gewachsen ist und über Jahre hinaus zuverlässig funktioniert. Bei einem Drucksensor müssen das mechanische Design und die Materialauswahl berücksichtigt werden, um Kompatibilität und Zuverlässigkeit über die gesamte Nutzungsdauer zu gewährleisten. Auch die Auswirkungen dieser Umgebungsbedingungen auf die langfristige Leistung des Sensors muss Beachtung finden. Nachdem wir nun die üblichen mechanischen Herausforderungen an Drucksensoren besprochen haben, wollen wir einen Blick auf das robuste Design des M9100-Hochleistungsdruckmessumformers von TE werfen, der für die mechanischen Herausforderungen kritischer Hydraulikmaschinen entwickelt wurde

Robuste Bauweise
Das robuste Design und die zuverlässige Leistung des Druckmessumformers M9100 erfüllen die Anforderungen an die Druckmessung in anspruchsvollen Anwendungen. Der M9100-Sensor von TE ist einer der klassenbesten Sensoren für hydraulische Haltbarkeit. Bei der Entwicklung des M9100 wurde sowohl auf Einfachheit als auch auf Langlebigkeit geachtet, um den Anforderungen der robustesten Anwendungen zu entsprechen oder sie zu übertreffen. Komplexe Konstruktionen, die mehrere Leiterplatten, interne Verdrahtung und mehrere gelötete Verbindungen erfordern, sind typischerweise anfälliger für einen frühzeitigen Ausfall und Probleme mit der Zuverlässigkeit im Feld. Der M9100 ist so konzipiert, dass er einfach, kompakt und langlebig ist, da so viele Fehlermöglichkeiten wie möglich eliminiert werden. Der Druckmessumformer erreicht seine kompakte Grundfläche mit einem einfachen Leiterplattendesign. Alle Lötstellen im Sensor werden durch automatisierte Bestückungsautomaten und Reflow-Löten gut kontrolliert. Es gibt keine Handlötstellen oder gelötete Verbindungen im Inneren des Sensors. Des Weiteren gibt es keine Stapelung von Leiterplatten.
Die einteilige, maschinell bearbeitete Struktur der Messmembran aus Edelstahl macht zusätzliche Montageschritte wie Schweißen und Verkleben überflüssig. Die Konstruktion sorgt für einen geringen Dehnungsgrad, was zu einer ausgezeichneten Festigkeit, Berstfestigkeit, Ermüdungsfestigkeit und Druckspitzenbeständigkeit führt. So wird das Risiko von Problemen sowohl während des Konstruktionsprozesses als auch im Feld verringert. Das Microfused-Sensordesign verfügt im Vergleich zu anderen Technologien über eine extrem dicke Membran. Dadurch ist der Sensor widerstandsfähiger gegen Beschädigungen durch Druckspitzen und kann diese Druckereignisse vollständig eindämmen. Darüber hinaus verfügt der M9100 von TE über einen optionalen integrierten Dämpfer, der die Geschwindigkeit und Amplitude einer Druckspitze weitergehend reduzieren kann. Durch das integrierte Design entfällt die Notwendigkeit einer separaten Komponente. Der Innenkörper des Sensors ist mit einem O-Ring gegen die äußere Umgebung abgedichtet. Diese Konstruktion schützt die internen Komponenten des Sensors vor Salznebel, Feuchtigkeit, Hochdruckreinigung und Untertauchen.
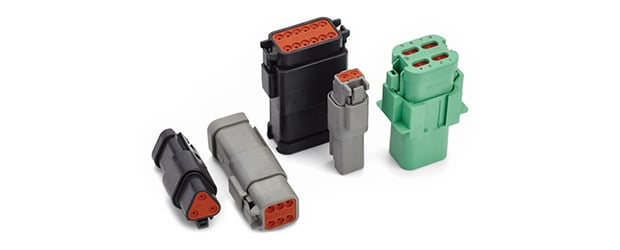
Kompatibilität mit Heavy-Duty-Verbindungssystemen
Der Druckmessumformer M9100 ist für große, langlebige Anschlusssysteme wie die DEUTSCH DT-Steckverbinderserie von TE, eine der besten für den Eindringschutz, ausgestattet. Das DEUTSCH-Anschlusssystem in Verbindung mit dem robusten Sensordesign ergibt einen Sensor, der von Grund auf so konzipiert ist, dass der Sensor unter einer Vielzahl von rauen Bedingungen bestehen kann und das Risiko ausschließt, dass Salzspray, Feuchtigkeit, Staub oder Wasser in das Produkt eindringen und zu einem Ausfall führen könnte. Die für die Konstruktion ausgewählten Materialien überschreiten den Betriebstemperaturbereich des Produkts. Die Wahl des Thermoplasts, des Klebstoffs und der elektronischen Komponenten (einschließlich eines ASICs mit AEC-Q100-Einstufung) tragen zur Robustheit des Produkts gegenüber extremen Temperaturen, Sonnenlicht, Sauerstoff oder typischen Chemikalien bei, die in Hochleistungsgeräten verwendet werden

Leistung des Druckmessumformers M9100
Hydraulische Maschinen und deren Komponenten müssen unter extremen Bedingungen zuverlässig funktionieren. Die Kerntechnologie eines Drucksensors ist ein äußerst komplexes elektromechanisches System. Die Aufgabe des Drucksensors ist es, den Druck in einem System in einen elektrischen Ausgang umzuwandeln. Auf der physikalischen Ebene besteht die Strategie darin, eine Dehnung in einer Oberfläche, der „Membran“, in einen elektrischen Ausgang umzuwandeln, der direkt proportional zum ausgeübten Druck und wiederholbar ist. Die Komplexität ergibt sich jedoch aus der Tatsache, dass die verwendeten Elemente anfällig für so ziemlich jeden anderen Umwelteinfluss sind.
Dehnungsmesstreifen-Technologie
Die Dehnungsmesstreifen-Technologie von TE, die weiter oben in diesem Artikel erläutert wurde, ist über Jahrzehnte entwickelt und optimiert worden, um Fehlerquellen zu minimieren und einen hochempfindlichen und wiederholbaren Druckausgang zu liefern. Dieses Ausgangssignal kann dann mit Hilfe eines anwendungsspezifischen integrierten Schaltkreises (ASIC) korrigiert und verstärkt werden. Dieser ASIC korrigiert Fehler, die durch nichtlineare Ausgangs- und thermische Fehler sowie Schwankungen der Versorgungsspannung entstehen. Diese Fehlerkorrektur vereinfacht die Basisdefinition der Leistung zu einem einfachen Begriff, dem Gesamtfehlerband. Das Gesamtfehlerband ist die Summe aller verbleibenden Fehler, die der ASIC nicht korrigieren kann (einschließlich der Abweichungen von Teil zu Teil und von Charge zu Charge). Es ist definiert als der maximale Fehler, den der Anwender über den kompensierten Temperaturbereich erfährt. Der M9100 verwendet einen AEC-Q100-qualifizierten ASIC, der Diagnosefunktionen enthält. Die Diagnose bestätigt die korrekte Funktion des Sensors und reduziert die Möglichkeit eines falschen Ausgangssignals.
Die Verwendung der Gesamtfehlerband-Spezifikation über einen weiten Temperaturbereich (-40 °C bis +125 °C) vereinfacht die Erwartungen an das Verhalten des Sensors im System. Der ASIC ist ebenfalls für die Signalkonditionierung des Sensors verantwortlich. Er nimmt das Signal von den Silizium-Dehnungsmessstreifen und wandelt es in ein verstärktes Analogsignal um. Während der ASIC wiederholbare Fehler korrigiert, können dieselben Umwelteinflüsse nicht wiederholbare Fehler verursachen, wobei der häufigste Fehler die Verschiebung im Laufe der Zeit ist. Die Verschiebung wird definiert als eine zeitbasierte Änderung des Sensorausgangs. Diese Beeinflussung kann aus einer Reihe von Quellen stammen, etwa Änderungen der mechanischen Dehnung in einer Membran (Kriech- oder Stressentspannung); physikalische Änderungen im Sensorelement aufgrund von elektrischen oder mechanischen Effekten oder Änderungen des spezifischen Widerstands von elektrischen Verbindungen oder Schutzgelen. Druckwechsel, Überdrücke, Temperatureinwirkung, Temperaturwechsel und Feuchtigkeit können zu dieser Langzeitverschiebung beitragen. Die langjährige Erfahrung von TE mit der Microfused Dehnungsmessstreifen-Technologie und den bekannten Faktoren, die zur Umweltverschiebung beitragen, hat es TE ermöglicht, das Design und die Verarbeitung zu optimieren. So kann den Kunden ein stabiles Produkt geliefert werden. Vom Konzept bis zum Nachweis durch Validierungstests ist der Microfused Dehnungsmessstreifen von TE eine der besten Messtechnologien seiner Klasse.
Hoher EMV-Schutz
Die elektrische Umgebung von Geräten wird immer komplexer, da Daten sowohl innerhalb der Geräte als auch um sie herum kommuniziert werden. Sensoren und Messumformer sind einem zunehmenden elektrischen Rauschen ausgesetzt, das das Signal stören kann, wenn der Sensor nicht richtig geschützt ist. Der M9100 ist nach ISO 11452-2 für die Störempfindlichkeit validiert, sodass das Produkt in der Nähe von elektrischen Störungen und in der Nähe von EMI-emittierenden Komponenten montiert werden kann. Der M9100 widerstandsfähig für BCI-Störungen (Bulk Current Injection) bis zu 200 mA gemäß ISO 11452-4. Darüber hinaus macht ein hoher elektrischer Schutz der Stromversorgung den Sensor robuster gegenüber einer schlechten Stromversorgungssteuerung und reduziert das Risiko von Systemproblemen. Es wird zwar empfohlen, ein Verdrahtungssystem zu entwerfen, das keine umgekehrten Verbindungen zulässt, aber der M9100 kann eine Überspannung von bis zu 28 VDC, umgekehrte Versorgungsspannungen von bis zu 16 VDC und einen Kurzschluss des Analogausgangs mit entweder V(+) oder GND überstehen, ohne dabei Schaden zu erleiden. Eine vollständige Liste der elektrischen Prüfspezifikationen, nach denen das Produkt validiert wurde, finden Sie im Datenblatt des M9100.

Zusammenfassung
Hydraulische Systeme sind ein wichtiger Bestandteil von industriellen und gewerblichen Transportsystemen. Bei der Umstellung von herkömmlichen Druckschaltern auf -Drucksensoren und -Messumformer hat die Hydraulikindustrie immer mehr Herausforderungen zu bewältigen, wie etwa Druckanstieg, höhere Betriebstemperaturen, Einsatz in gefährlichen und rauen Umgebungen sowie Druck-Störsignale in Hydraulikkreisläufen. Das robuste Design und die zuverlässige Leistung des Druckmessumformers M9100 von TE Connectivity gehen diese Herausforderung an und erfüllen die Anforderungen an die Druckmessung in anspruchsvollen Anwendungen.
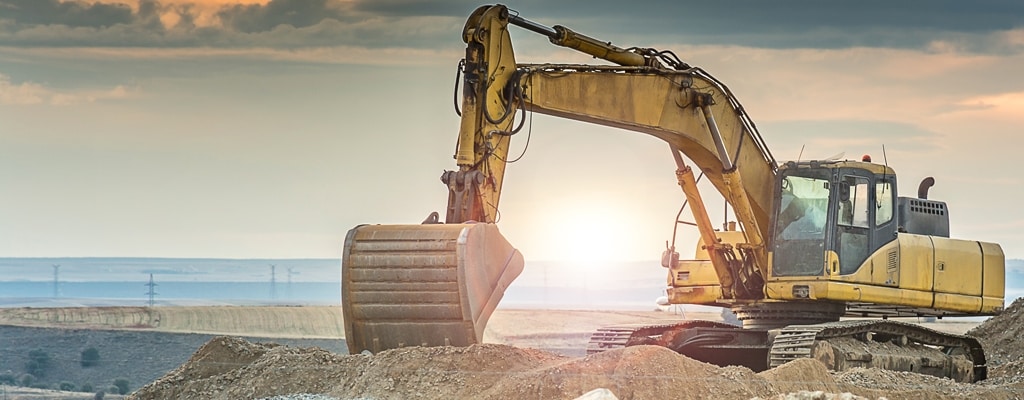
Anwendung
Der Leistungsdruck in hydraulischen Systemen und Kreisläufen
In den letzten zwei Jahrzehnten hat die Hydraulikindustrie von den Fortschritten in der Elektronik, der weit verbreiteten Einführung des IoT (Internet der Dinge), der Senkung der Technologiekosten und der Miniaturisierung von Komponenten profitiert. Darüber hinaus hat die Hydraulikindustrie bei der Umstellung von herkömmlichen Druckschaltern auf Drucksensoren und -Messumformer immer mehr Herausforderungen zu bewältigen. Diese Herausforderungen umfassen etwa Druckanstieg, höhere Betriebstemperaturen, Einsatz in gefährlichen und rauen Umgebungen sowie Druck-Störsignale in Hydraulikkreisläufen. Dies sind Herausforderungen für Konstrukteure und Systemintegratoren und können zu Projektverzögerungen oder Problemen mit der Zuverlässigkeit im Feld führen, wenn sie nicht angemessen angegangen werden. Auch diese Druckmessgeräte haben sich weiterentwickelt, von der Messzelle über das mechanische Gesamtpaket bis hin zum elektronischen Ausgangssignal und der Signalaufbereitung. In diesem Bericht werden wir die Technologie betrachten, die hinter Drucksensoren und -Messumformern steckt, erfahren Sie etwas über die allgemeinen mechanischen Herausforderungen, denen diese Sensoren ausgesetzt sind, und darüber, wie der Druckmessumformer M9100 von TE Connectivity (TE) in diesen anspruchsvollen Umgebungen funktioniert.
Sensortechnologie
Ein Blick in Ihren Sensor
Äußerlich sehen Druckmessumformer alle relativ gleich aus, doch das Kernstück der Messzelle ist zwischen den verschiedenen Sensorherstellern sehr unterschiedlich. Einer der gängigsten wirtschaftlichen und technologisch machbaren Ansätze ist die Verwendung eines Dehnungsmessstreifens als Sensorelement, um die mechanische Belastung, die der Druck auf eine Membran ausübt, in ein genaues und wiederholbares elektrisches Ausgangssignal zu übertragen. TE verwendet seine Microfused-Dehnungsmessstreifentechnologie in einer Wheatstone-Brückenkonfiguration, um die Dehnung in ein Spannungsausgangssignal umzuwandeln. TE hat das Sensorelement als ein einziges bearbeitetes Bauteil konzipiert, das in den Gewindeanschluss integriert ist. Dieses optimierte Design sorgt für ein robustes Signal des Sensorelements und bietet ein hohes Maß an Überdruck- und Berstleistung.
TE verwendet ein Glasbondverfahren, um die Silizium-Dehnungsmessstreifen mit dem Metallanschluss zu verschmelzen. Die Messstreifen sind optimal positioniert, um die Dehnung bei Druckänderungen korrekt zu messen. Zur Herstellung der Verbindungen zwischen den Messstreifen und der Auswerteelektronik werden industrieerprobte Drahtbondverfahren eingesetzt. Konkurrierende Technologien auf dem Markt für hydraulische Drucksensoren, wie Dünnschicht-, Dickschicht- und keramikbasierte Technologien, verwenden separate Membranen mit Sensorelementen mit geringer Empfindlichkeit. Diese Technologien erfordern zusätzliche Schweißnähte in den Flüssigkeitswegen, internen O-Ringen oder zusätzliche Verarbeitungsschritte, die lange für lange Lieferketten-Durchlaufzeiten sorgen können. Alternative Technologien erfordern möglicherweise hohe Dehnungen in ihrem Sensorelement, um die geringe Empfindlichkeit zu kompensieren. Diese hohen Belastungen zusammen mit der mehrteiligen Konstruktion können zu einer reduzierten Langzeitstabilität und Haltbarkeit führen. Die Microfused-Dehnungsmessstreifentechnologie von TE hat sich seit Jahrzehnten in der großvolumigen Fertigung bewährt, birgt ein geringes Risiko von Lieferkettenunterbrechungen und liefert eine robuste einteilige Flüssigkeitsverbindung, die das Risiko von internen Sensorausfällen und anderen mechanischen Herausforderungen reduziert.

Mechanische Herausforderungen
Da Druckmessumformer als Teil eines hydraulischen Systems montiert werden, sollten verschiedene mechanische Herausforderungen bei der Konstruktion berücksichtigt und erkannt werden. Nachfolgend sind die typischen Bereiche innerhalb hydraulischer Systeme aufgeführt, die Systemdesigner im Rahmen des Designprozesses berücksichtigen müssen:
- Arbeitsdruck
- Druckspitzen
- Prüfdruck
- Flüssigkeitsverbindungen
- Berstdruck
- Vibrationen/Mechanische Stöße
- Druckermüdung
- Beständigkeit gegenüber Umwelteinflüssen
Jedes dieser Probleme wird durch das Design und die Validierung des Sensors angegangen. Überdruckwerte, Berstdruckwerte, Ermüdungsanalysen und die Verwendung von Druckdämpfern sind bei TE Teil des Designprozesses und werden sowohl durch Simulation als auch durch empirische Tests validiert.
Arbeitsdruckbereich
Einfach definiert, ist dies der Druckbereich, der eine Systemsteuerung oder -rückführung erfordert. Im typischen Betriebszustand wird das System immer innerhalb dieses Bereichs bleiben. Drücke außerhalb dieses Bereichs erfordern normalerweise keine Messung.
Prüfdruck
Bei der Systemauslegung treten häufig Druckereignisse auf, die den benötigten Messbereich überschreiten, aber keine Schäden am System verursachen sollten. Typischerweise wird erwartet, dass das System nach einem Überdruckereignis wieder in die normale Funktion zurückkehrt. TE spezifiziert den Prüfdruck als den Druck, der auf die Messzelle ausgeübt werden darf, ohne eine dauerhafte Änderung der Ausgangscharakteristik oder der Genauigkeit des Druckmessumformers zu verursachen.
Berstdruck
Es kann potenzielle Fehlermodi auf der Systemebene geben, die dazu führen können, dass das System übermäßige Drücke erfährt, die ein Versagen des Druckbehälters riskieren. TE entwickelt und validiert seine Druckmessumformer sowohl theoretisch als auch empirisch, um den Mindestdruck festzulegen, dem der Sensor ausgesetzt werden kann, ohne zu reißen.
Druckermüdung
Typische Druckermüdung findet man in Systemen, in denen es eine Pumpe oder ein Ventil gibt, die ständig zu Druckschwankungen im System führen. Diese Schwankungen variieren in Ausmaß und Häufigkeit. Eine Pumpe kann eine Hochfrequenz-Druckschwingung mit sehr geringer Größe erzeugen, während ein Ventil zu einer signifikanten Druckänderung führen kann. Dies geschieht aber seltener. In einigen Fällen kann das Gegenteil eintreten. Es ist unmöglich, jedes potenzielle Systemverhalten vorherzusagen. Daher wird der M9100 von TE von 0 bis zum vollen Druckzyklus mit bis zu 10 Mio. Zyklen getestet und theoretisch validiert. So kann bestätigt werden, dass die Spannungen unterhalb der Ermüdungsgrenze bleiben, was für eine im Wesentlichen unbegrenzte Lebensdauer innerhalb des Betriebsbereichs und oft auch innerhalb des Prüfdruckbereichs sorgt. Es sollte darauf hingewiesen werden, dass, da das Sensorelement von TE viel empfindlicher ist als konkurrierende Technologien, das Belastungsniveau so niedrig ist, dass die Druckermüdung kein Problem darstellt.
Druckspitzen
Die vielleicht versteckteste Herausforderung in einem hydraulischen System ist das Vorhandensein von sehr hochfrequenten Drucktransienten, die gemeinhin als „Druckspitzenn“ bezeichnet werden und manchmal auch als Wasserschlag-Effekt bezeichnet werden. Eine Druckspitze kann während der Ventilbetätigung auftreten; auferlegte Druckwellen aufgrund der Systemarchitektur oder die Einfuhr von Luft in die Hydraulikpumpe. Der Druckspitze ist typischerweise durch einen extrem schnellen Druckanstieg (typischerweise Mikrosekunden) auf sehr hohe Amplituden (potenziell 10-facher Betriebsdruck) gekennzeichnet. Die Geschwindigkeit einer Druckspitze kann so schnell sein, dass ein typischer Drucksensor möglicherweise nicht erkennen kann, dass es zu dem Ereignis kam. Dieses Phänomen kann jedoch den Druckmessumformer dauerhaft beschädigen, was zu einer permanenten Nullpunktverschiebung führt, den Sensor nicht mehr auf Druck reagieren oder die Membran reißen lässt, wodurch die Flüssigkeit in das Sensorgehäuse eindringt. Oft verfügen Kunden nicht über die richtige Ausrüstung, um Druckspitzen in ihrem System richtig zu identifizieren, doch die Auswahl eines Druckmessumformers mit der richtigen Technologie kann ihnen dabei helfen. Das robuste Design des M9100 von TE und der optionale Dämpfer reduzieren die potenziellen Ausfallmodi, die durch Druckspitzen verursacht werden.
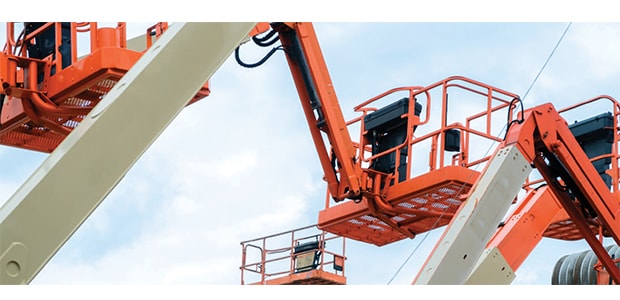
Flüssigkeitsverbindungen
Eine weitere mechanische Überlegung ist der Anschluss an den Hydraulikkreislauf. Es gibt verschiedene Gewindeanschlussoptionen, die in den globalen Regionen beliebt sind, einschließlich SAE (Nordamerika), G-Serie (EMEA) und Metrik (APAC). TE verfügt über langjährige Erfahrung mit historischen Industriestandards wie SAE J1926 oder ISO 1179 und hält stets mit den sich ändernden Anforderungen Schritt. Da hohe Drücke in der Hydraulikindustrie immer häufiger vorkommen, sollten zusätzliche Vorsichtsmaßnahmen getroffen werden, um sicherzustellen, dass der Druckmessumformer richtig ausgelegt, eingesetzt und angezogen ist.
Vibrationen/Mechanische Stöße
Mechanische Stöße und Vibrationen sind traditionell in der Sensorindustrie miteinander verbunden. Druckmessumformer sind aufgrund der spezifischen mechanischen Umgebung der Anwendungen, in denen sie eingesetzt werden, häufig sowohl den Bedingungen im On- als auch im Off-Road-Bereich ausgesetzt. Von den hochfrequenten Vibrationen eines Dieselmotors bis hin zu den Erschütterungen eines Gabelstaplers, der eine volle Ladung auf den Boden fallen lässt, erfordern diese Bedingungen, dass der Druckmessumformer immun gegen die nachteiligen Auswirkungen von „Schock und Vibration“ ist.
Beständigkeit gegenüber Umwelteinflüssen
Die Beständigkeit gegenüber Umwelteinflüssen ist von entscheidender Bedeutung, um sicherzustellen, dass jedes Produkt den extremen Umweltbedingungen gewachsen ist und über Jahre hinaus zuverlässig funktioniert. Bei einem Drucksensor müssen das mechanische Design und die Materialauswahl berücksichtigt werden, um Kompatibilität und Zuverlässigkeit über die gesamte Nutzungsdauer zu gewährleisten. Auch die Auswirkungen dieser Umgebungsbedingungen auf die langfristige Leistung des Sensors muss Beachtung finden. Nachdem wir nun die üblichen mechanischen Herausforderungen an Drucksensoren besprochen haben, wollen wir einen Blick auf das robuste Design des M9100-Hochleistungsdruckmessumformers von TE werfen, der für die mechanischen Herausforderungen kritischer Hydraulikmaschinen entwickelt wurde

Robuste Bauweise
Das robuste Design und die zuverlässige Leistung des Druckmessumformers M9100 erfüllen die Anforderungen an die Druckmessung in anspruchsvollen Anwendungen. Der M9100-Sensor von TE ist einer der klassenbesten Sensoren für hydraulische Haltbarkeit. Bei der Entwicklung des M9100 wurde sowohl auf Einfachheit als auch auf Langlebigkeit geachtet, um den Anforderungen der robustesten Anwendungen zu entsprechen oder sie zu übertreffen. Komplexe Konstruktionen, die mehrere Leiterplatten, interne Verdrahtung und mehrere gelötete Verbindungen erfordern, sind typischerweise anfälliger für einen frühzeitigen Ausfall und Probleme mit der Zuverlässigkeit im Feld. Der M9100 ist so konzipiert, dass er einfach, kompakt und langlebig ist, da so viele Fehlermöglichkeiten wie möglich eliminiert werden. Der Druckmessumformer erreicht seine kompakte Grundfläche mit einem einfachen Leiterplattendesign. Alle Lötstellen im Sensor werden durch automatisierte Bestückungsautomaten und Reflow-Löten gut kontrolliert. Es gibt keine Handlötstellen oder gelötete Verbindungen im Inneren des Sensors. Des Weiteren gibt es keine Stapelung von Leiterplatten.
Die einteilige, maschinell bearbeitete Struktur der Messmembran aus Edelstahl macht zusätzliche Montageschritte wie Schweißen und Verkleben überflüssig. Die Konstruktion sorgt für einen geringen Dehnungsgrad, was zu einer ausgezeichneten Festigkeit, Berstfestigkeit, Ermüdungsfestigkeit und Druckspitzenbeständigkeit führt. So wird das Risiko von Problemen sowohl während des Konstruktionsprozesses als auch im Feld verringert. Das Microfused-Sensordesign verfügt im Vergleich zu anderen Technologien über eine extrem dicke Membran. Dadurch ist der Sensor widerstandsfähiger gegen Beschädigungen durch Druckspitzen und kann diese Druckereignisse vollständig eindämmen. Darüber hinaus verfügt der M9100 von TE über einen optionalen integrierten Dämpfer, der die Geschwindigkeit und Amplitude einer Druckspitze weitergehend reduzieren kann. Durch das integrierte Design entfällt die Notwendigkeit einer separaten Komponente. Der Innenkörper des Sensors ist mit einem O-Ring gegen die äußere Umgebung abgedichtet. Diese Konstruktion schützt die internen Komponenten des Sensors vor Salznebel, Feuchtigkeit, Hochdruckreinigung und Untertauchen.
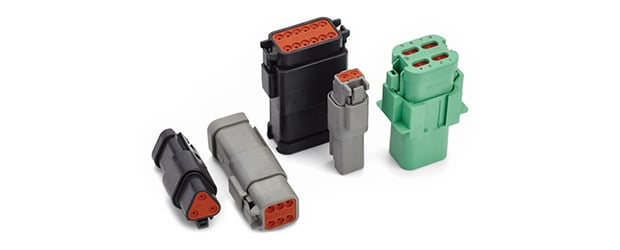
Kompatibilität mit Heavy-Duty-Verbindungssystemen
Der Druckmessumformer M9100 ist für große, langlebige Anschlusssysteme wie die DEUTSCH DT-Steckverbinderserie von TE, eine der besten für den Eindringschutz, ausgestattet. Das DEUTSCH-Anschlusssystem in Verbindung mit dem robusten Sensordesign ergibt einen Sensor, der von Grund auf so konzipiert ist, dass der Sensor unter einer Vielzahl von rauen Bedingungen bestehen kann und das Risiko ausschließt, dass Salzspray, Feuchtigkeit, Staub oder Wasser in das Produkt eindringen und zu einem Ausfall führen könnte. Die für die Konstruktion ausgewählten Materialien überschreiten den Betriebstemperaturbereich des Produkts. Die Wahl des Thermoplasts, des Klebstoffs und der elektronischen Komponenten (einschließlich eines ASICs mit AEC-Q100-Einstufung) tragen zur Robustheit des Produkts gegenüber extremen Temperaturen, Sonnenlicht, Sauerstoff oder typischen Chemikalien bei, die in Hochleistungsgeräten verwendet werden

Leistung des Druckmessumformers M9100
Hydraulische Maschinen und deren Komponenten müssen unter extremen Bedingungen zuverlässig funktionieren. Die Kerntechnologie eines Drucksensors ist ein äußerst komplexes elektromechanisches System. Die Aufgabe des Drucksensors ist es, den Druck in einem System in einen elektrischen Ausgang umzuwandeln. Auf der physikalischen Ebene besteht die Strategie darin, eine Dehnung in einer Oberfläche, der „Membran“, in einen elektrischen Ausgang umzuwandeln, der direkt proportional zum ausgeübten Druck und wiederholbar ist. Die Komplexität ergibt sich jedoch aus der Tatsache, dass die verwendeten Elemente anfällig für so ziemlich jeden anderen Umwelteinfluss sind.
Dehnungsmesstreifen-Technologie
Die Dehnungsmesstreifen-Technologie von TE, die weiter oben in diesem Artikel erläutert wurde, ist über Jahrzehnte entwickelt und optimiert worden, um Fehlerquellen zu minimieren und einen hochempfindlichen und wiederholbaren Druckausgang zu liefern. Dieses Ausgangssignal kann dann mit Hilfe eines anwendungsspezifischen integrierten Schaltkreises (ASIC) korrigiert und verstärkt werden. Dieser ASIC korrigiert Fehler, die durch nichtlineare Ausgangs- und thermische Fehler sowie Schwankungen der Versorgungsspannung entstehen. Diese Fehlerkorrektur vereinfacht die Basisdefinition der Leistung zu einem einfachen Begriff, dem Gesamtfehlerband. Das Gesamtfehlerband ist die Summe aller verbleibenden Fehler, die der ASIC nicht korrigieren kann (einschließlich der Abweichungen von Teil zu Teil und von Charge zu Charge). Es ist definiert als der maximale Fehler, den der Anwender über den kompensierten Temperaturbereich erfährt. Der M9100 verwendet einen AEC-Q100-qualifizierten ASIC, der Diagnosefunktionen enthält. Die Diagnose bestätigt die korrekte Funktion des Sensors und reduziert die Möglichkeit eines falschen Ausgangssignals.
Die Verwendung der Gesamtfehlerband-Spezifikation über einen weiten Temperaturbereich (-40 °C bis +125 °C) vereinfacht die Erwartungen an das Verhalten des Sensors im System. Der ASIC ist ebenfalls für die Signalkonditionierung des Sensors verantwortlich. Er nimmt das Signal von den Silizium-Dehnungsmessstreifen und wandelt es in ein verstärktes Analogsignal um. Während der ASIC wiederholbare Fehler korrigiert, können dieselben Umwelteinflüsse nicht wiederholbare Fehler verursachen, wobei der häufigste Fehler die Verschiebung im Laufe der Zeit ist. Die Verschiebung wird definiert als eine zeitbasierte Änderung des Sensorausgangs. Diese Beeinflussung kann aus einer Reihe von Quellen stammen, etwa Änderungen der mechanischen Dehnung in einer Membran (Kriech- oder Stressentspannung); physikalische Änderungen im Sensorelement aufgrund von elektrischen oder mechanischen Effekten oder Änderungen des spezifischen Widerstands von elektrischen Verbindungen oder Schutzgelen. Druckwechsel, Überdrücke, Temperatureinwirkung, Temperaturwechsel und Feuchtigkeit können zu dieser Langzeitverschiebung beitragen. Die langjährige Erfahrung von TE mit der Microfused Dehnungsmessstreifen-Technologie und den bekannten Faktoren, die zur Umweltverschiebung beitragen, hat es TE ermöglicht, das Design und die Verarbeitung zu optimieren. So kann den Kunden ein stabiles Produkt geliefert werden. Vom Konzept bis zum Nachweis durch Validierungstests ist der Microfused Dehnungsmessstreifen von TE eine der besten Messtechnologien seiner Klasse.
Hoher EMV-Schutz
Die elektrische Umgebung von Geräten wird immer komplexer, da Daten sowohl innerhalb der Geräte als auch um sie herum kommuniziert werden. Sensoren und Messumformer sind einem zunehmenden elektrischen Rauschen ausgesetzt, das das Signal stören kann, wenn der Sensor nicht richtig geschützt ist. Der M9100 ist nach ISO 11452-2 für die Störempfindlichkeit validiert, sodass das Produkt in der Nähe von elektrischen Störungen und in der Nähe von EMI-emittierenden Komponenten montiert werden kann. Der M9100 widerstandsfähig für BCI-Störungen (Bulk Current Injection) bis zu 200 mA gemäß ISO 11452-4. Darüber hinaus macht ein hoher elektrischer Schutz der Stromversorgung den Sensor robuster gegenüber einer schlechten Stromversorgungssteuerung und reduziert das Risiko von Systemproblemen. Es wird zwar empfohlen, ein Verdrahtungssystem zu entwerfen, das keine umgekehrten Verbindungen zulässt, aber der M9100 kann eine Überspannung von bis zu 28 VDC, umgekehrte Versorgungsspannungen von bis zu 16 VDC und einen Kurzschluss des Analogausgangs mit entweder V(+) oder GND überstehen, ohne dabei Schaden zu erleiden. Eine vollständige Liste der elektrischen Prüfspezifikationen, nach denen das Produkt validiert wurde, finden Sie im Datenblatt des M9100.

Zusammenfassung
Hydraulische Systeme sind ein wichtiger Bestandteil von industriellen und gewerblichen Transportsystemen. Bei der Umstellung von herkömmlichen Druckschaltern auf -Drucksensoren und -Messumformer hat die Hydraulikindustrie immer mehr Herausforderungen zu bewältigen, wie etwa Druckanstieg, höhere Betriebstemperaturen, Einsatz in gefährlichen und rauen Umgebungen sowie Druck-Störsignale in Hydraulikkreisläufen. Das robuste Design und die zuverlässige Leistung des Druckmessumformers M9100 von TE Connectivity gehen diese Herausforderung an und erfüllen die Anforderungen an die Druckmessung in anspruchsvollen Anwendungen.