Bildverarbeitungsgesteuerte Roboter-Blechkäfig-Montage
AUSZUG
Die hochpräzise Montage von Blechkäfigen ist arbeitsintensiv. Um die Montagekosten zu senken und die Montageeffizienz und -qualität zu verbessern, war die Robotik mit ihren entscheidenden Vorteilen in Bezug auf Geschwindigkeit, Präzision und Flexibilität eine optimale Option für die Konstruktion des automatischen Montagesystems. Vorgestellt wird hier die roboterbasierte Technologie für die Blechkäfigmontage zur Demonstration, Verifizierung und Optimierung der Schlüssellösungen bei der Automatisierung von maßgeschneiderten Montageprozessen.
PROBLEMSTELLUNG
Hochpräzise Blechkäfig-Montageprozesse sind arbeitsintensiv, und es arbeiten mehr als 52 Bediener intensiv an dem Prozess. Wie in Abb. 1 dargestellt, werden die Trennelemente mit dem unteren Käfig zu einer Unterbaugruppe zusammengebaut, und dann wird die Unterbaugruppe mit der Kick-out-Feder und dem oberen Käfig zusammengesetzt, um die gesamte Käfigbaugruppe zu montieren. Offensichtlich ist es besonders wichtig, beim Zusammenbau von Käfigen sehr vorsichtig zu sein, da das Produkt leicht verformt und zerkratzt werden kann. Die Dicke des Blechteils beträgt 0,25 mm, und die Montagegenauigkeit beträgt weniger als 0,03 mm. Darüber hinaus gibt es mehr als 100 zu unterstützende Produktteilenummern. Das in Abb.1 dargestellte Produkt ist ein typisches SFP+ 1X4 Käfigprodukt, und es gibt einige andere Produkte wie 1XN und 2XN, die den Produktfamilien SFP, SFP+, QSFP, ZQSFP usw. zugeordnet sind. Es ist offensichtlich, dass die Automatisierung des Käfigmontageprozesses ein Problem der kundenspezifischen Massenfertigung mit hoher Durchmischung und geringen Stückzahlen ist, und die herkömmlichen Automatisierungsmethoden mit harten Werkzeugen wären in diesem Fall für die Anforderung der kundenspezifischen Massenfertigung nicht geeignet.
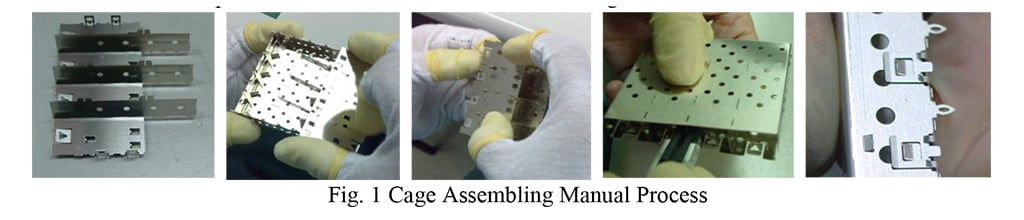
Die Robotik mit ihren entscheidenden Vorteilen in Bezug auf Geschwindigkeit, Präzision und Flexibilität wurde als optimale Option für die Konstruktion des automatischen und flexiblen Montagesystems angesehen. Diese Forschung untersucht die interessanten Fähigkeiten des Roboters / der Robotik, und präsentiert die Lösungen für den Blechkäfig-Montageprozess zur Massenfertigung mit Robotik, welche hervorragende Auswirkungen auf die Wirtschaftlichkeit und die Technologieentwicklung von TE haben können. Um die Zuverlässigkeit und die Robustheit des robotergesteuerten Käfig-Montagesystems zu verbessern, untersucht diese Forschung auch die Details des Montageprozesses und führt zwei Design of Experiments (DoEs) durch, um die Montage des Seperators und des unteren Käfigs und die Montage des oberen Käfigs und der Kick-out-Feder zu optimieren. Das auf Robotik basierende Montagesystem und die aus dieser Forschung entwickelte Methode zur Optimierung des Montageprozesses könnten hoffentlich auf andere Produktmontageprozesse in allen TE-Geschäftsbereichen angewandt werden, um die Montagekosten deutlich zu senken und die Montageeffizienz und -qualität zu verbessern.
METHODEN UND ERGEBNISSE
Einführung in Industrieroboter
Der Industrieroboter ist normalerweise als SCARA-Roboter, 6-Achsen-Roboter und Delta-Roboter bekannt. Der SCARA-Roboter verfügt über 3-DOF (Freiheitsgrad)-Verschiebungen und 1-DOF-Rotation und wird im Allgemeinen zur Durchführung von Pick-and-Place-Operationen eingesetzt; der 6-Achsen-Roboter verfügt über 3-DOF-Verschiebungen und 3-DOF-Rotationen und kann sehr vielseitig in verschiedenen Fertigungs- und Montageprozessen eingesetzt werden. Der Delta-Roboter ist von paralleler Architektur im Allgemeinen mit 3-DOF-Übersetzungen und 1-DOF-Rotation, und wird normalerweise genutzt, um schnelle Pick-and-Place-Operationen durchzuführen. Für den Montageprozess des Blechkäfigs erfordert die Montage des Trennelements und des Oberkäfigs sowohl Übersetzungen als auch Rotationen, damit das Teil einem Montagepfad folgen kann, um die Montage zu beenden. Daher wird in diesem Fall der 6-Achsen-Roboter bevorzugt eingesetzt. Abb. 2 zeigt den typischen 6-Achsen-Roboter und die Roboterarchitektur, um die Mobilität des Roboterendeffektors zu untersuchen. Der 6-achsige Industrieroboter ist auch als 6-R-Mechanismus (R: Revolute Joint) bekannt, der sich weiter in zwei Teile zerlegen lässt: den Arm und das Handgelenk. Der Roboterarm ermöglicht 3-DOF-Übersetzungen und das Roboterhandgelenk 3-DOF-Rotationen. Durch die Koordination zwischen dem Roboterarm und dem Roboterhandgelenk ist der Roboter-End-Effektor in der Lage, jede definierte Pose innerhalb seines Arbeitsbereichs zu erreichen, und wäre recht beweglich, um den Blechkäfig-Montageprozess zu erfüllen.
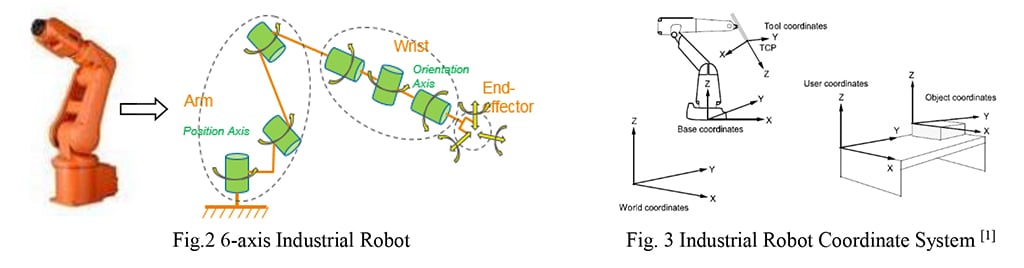
Der Industrieroboter ist inzwischen mit seiner Modellierungs- und Steuerungsmethode sowie mit einer guten Roboterprogrammiersprache als Programmierschnittstelle gut entwickelt. Für den Endanwender ist es nicht notwendig, sich mit den Details der Motorsteuerung, der direkten/inversen Kinematik oder gar der Dynamik auseinanderzusetzen. Es ist jedoch notwendig, einige Techniken mit den Roboterprogrammiersprachen zur Roboterbewegung und Wegplanung zu entwickeln. Wenn der Endeffektor am Roboter installiert ist, basiert die Bewegungs- und Wegplanung auf der Roboter-Werkzeugkoordinate, die definiert und am Roboter-Endeffektor angebracht wird. Abb. 3 zeigt ein Konzept für die wichtigsten Roboterkoordinatensysteme. Die präzise Steuerung des Roboterwegs besteht darin, die kritischen Roboterziele präzise zu steuern. Insbesondere beim Käfigmontageprozess kann der Schritt zur Konstruktion des Roboter-Montagewegs eine lineare Übersetzung oder Rotation oder sogar eine Kombination aus beidem sein. Um einen reibungslosen Montageweg zu konstruieren und Interferenzen zu vermeiden, ist es entscheidend, die Schrittgröße des Roboters genau zu definieren. Für jedes Roboterziel muss der Roboter-Endeffektor in seiner Position (x, y, z) und Ausrichtung (Ex, Ey, Ez) genau definiert sein, wobei x, y, z die Koordinaten ohne das Objekt-Koordinatensystem und Ex, Ey, Ez die Euler-Winkel ohne das Objekt-Koordinatensystem sind.
Bildverarbeitungsgeführte Robotik
Für die hochpräzise Montage besteht die traditionelle Automatisierungsmethode darin, hochpräzise mechanische Vorrichtungen zu entwerfen und herzustellen, um die Positionierung für das Teil durchzuführen, und hochpräzise Mechanismen zu entwickeln, um das Laden des Teils und die Montage durchzuführen. Dies würde eine Herausforderung für das mechanische System darstellen, um die Präzision aufrechtzuerhalten. Während bei der bildverarbeitungsgeführten Robotermethode ein Bildverarbeitungssystem als Teil des Robotersystems integriert ist, um die Pose des am Roboterwerkzeug gehaltenen Teils genau zu identifizieren, übersetzt oder dreht dar Roboter / das Roboterwerkzeug das Teil adaptiv auf der Grundlage des Feedbacks der Bildverarbeitungsidentifikation, um die Montagepräzision zu gewährleisten.
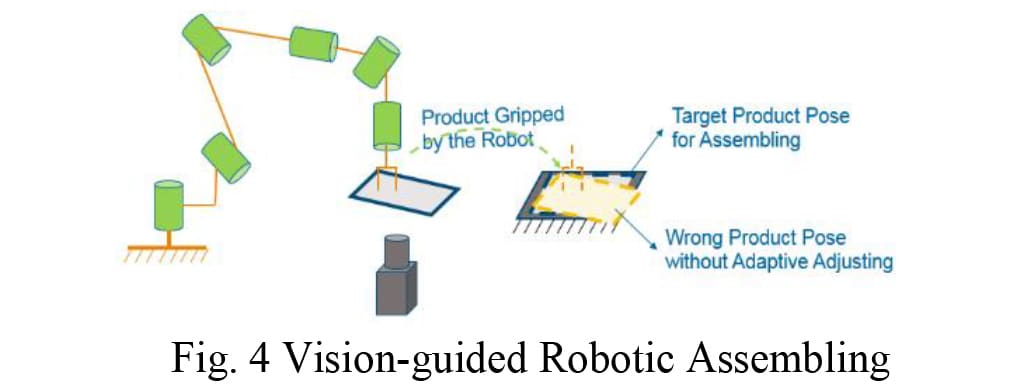
Abb. 4 zeigt ein typisches bildverarbeitungsgeführtes Robotersystem für die adaptive Montage/Pick-and-Place-Bedienung. Da der Roboter das Produkt aufgrund einiger Positionierungsfehler möglicherweise nicht in der gleichen Position oder Ausrichtung aufnimmt und die durch das Roboter-Teaching erzeugte konstante Roboterposition das Produkt nicht zusammenbauen kann, wäre das Bildverarbeitungssystem sehr hilfreich, um den Roboter bei der adaptiven Anpassung des Montagepfades zu führen. So ließe sich die Zuverlässigkeit und Robustheit des Montagesystems gewährleisten.
Das Verfahren zur Entwicklung eines roboteradaptiven Montagealgorithmus besteht darin, zuerst das Basismodell als Referenzmodell zu erstellen und dann das Ziel-Pose-Berechnungsmodell zu formulieren, um die Roboterpose adaptiv anzupassen, damit das Produkt präzise montiert werden kann. Das Basismodell wird erstellt, indem man die Roboter-Pose für die Bilderfassung (XRb, YRb, ARb), die identifizierten Produkt-Pose am Roboter-Werkzeug (XCb, YCb, ACb) durch das 2D-Vision-System und die Teach-Pose (XFb, YFb, AFb) zum präzisen Zusammenbau des Produkts als Bezugsbasis nimmt, mit dem die Produkt-Ziel-Pose (XCFb, YCFb, ACFb) berechnet wird. Es ist offensichtlich, dass die Produkt-Ziel-Pose für den präzisen Zusammenbau des Produkts konstant sein muss. X/Y steht hier für die Position, A steht für den Rotationswinkel entlang der z-Achse, da hier mittels des 2D-Vision-Systems die Posen-Komponente in der 2D-Ebene untersucht wird.
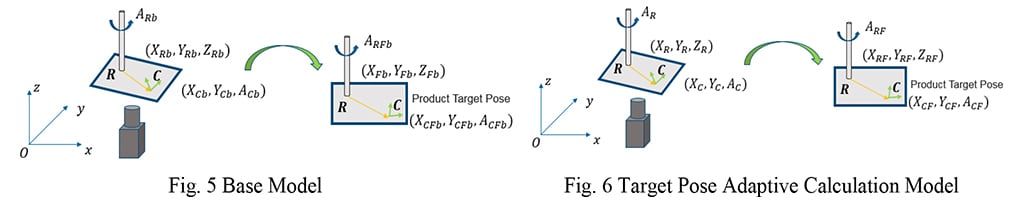
Wie in Abb. 4 dargestellt, greift das Roboterwerkzeug das Produkt am Punkt R, und das Feature zur Darstellung der Produktposition und -ausrichtung am Roboterwerkzeug ist Rahmen C, wobei die Roboter-Teach-Pose zur Montage des Produkts bekannt ist. Die Produktzielposition für die Produktmontage wird basierend auf der planaren Transformation des Vektors 𝒗𝑟𝑐 von der Bilderfassungs-Pose zur Montage-Pose und der Roboter-Teach-Pose zur Montage des Produkts berechnet. Daher wird die Produktzielposition wie folgt formuliert:

wobei Folgendes gilt: 𝒗𝑟𝑐 = (𝑋𝐶𝑏 − 𝑋𝑅𝑏, 𝑌𝐶𝑏 − 𝑌𝑅𝑏)𝑇.
Die Produktzielausrichtung für die Produktmontage wird auf der Grundlage der Produktmerkmalsorientierung ACb und der Rotationsvariation des Roboters berechnet ∆𝐴𝑏 = 𝐴𝑅𝐹𝑏 − 𝐴𝑅𝑏, wie Gl. (2):
𝐴𝐶𝐹𝑏 = 𝐴𝐶𝑏 + ∆𝐴𝑏 (2)
Die adaptive Roboter-Zielposition für die Montage des Produkts wird mit dem in Abb. 6 gezeigten Modell formuliert, und es ist leicht, die Zielposition des Produkts zu kennen, da sie mit der Referenzbasis übereinstimmt:
𝑋𝐶𝐹 = 𝑋𝐶𝐹𝑏, 𝑌𝐶𝐹 = 𝑌𝐶𝐹𝑏, 𝐴𝐶𝐹 = 𝐴𝐶𝐹𝑏 (3)
Die Roboter-Pose für die Bilderfassung ist (XR, YR, AR), die identifizierte Produkt-Pose am Roboterwerkzeug ist (XC, YC, AC) und die Variation des Produktdrehwinkels von der Bilderfassungs-Pose zur Montage-Pose wird als Gl. 4 formuliert:
∆A = 𝐴𝐶𝐹 − 𝐴𝐶 (4)
Daher wird die Zielroboterausrichtung zur Montage des Produkts mit der identifizierten Produkt-Feature-Ausrichtung als Eq. (5) adaptiv berechnet:
𝐴𝑅𝐹 = 𝐴𝑅 + ∆𝐴 = 𝐴𝑅 + 𝐴𝐶𝐹 − 𝐴𝐶 (5)
Die Ziel-Roboterposition für die Produktmontage wird auf der Grundlage der planaren Transformation des Vektors 𝒗𝑟𝑐 und der Produkt-Zielposition als Gl. (6) formuliert:

Wobei Folgendes gilt: 𝒗𝑟𝑐 = (𝑋C − 𝑋R, 𝑌C − 𝑌R)T
Mit dem Bildverarbeitungssystem zur genauen Identifizierung des Produktmerkmals, wie in Abb. 5 und Abb. 6 dargestellt, ist die Roboterpose zur präzisen Montage des Produkts keine konstante Pose, sondern eine adaptive Roboterpose, die durch Gl. (5) und Gl. (6) formuliert wurde.
Für den Montageprozess des Blechkäfigs beträgt die mechanische Positioniergenauigkeit für den Separator und die Kick-out-Feder etwa 0,3 mm, und die mechanische Positioniergenauigkeit für den Oberkäfig beträgt etwa 0,1 mm in der Position und etwa 0,25 Grad in der Ausrichtung. Um die Montagegenauigkeit von 0,03 mm zu erreichen, ist ein Visionssystem mit einer Positioniergenauigkeit von +/-0,003 mm integriert, um den Roboter adaptiv zu führen, wie in Abb. 8 dargestellt. In Kombination mit der Wiederholgenauigkeit des Roboters von +/-0,01 mm liegt die Gesamtgenauigkeit des Robotersystems für die Montage bei etwa 0,02 mm, was für die Ausführung des Blechkäfig-Montageprozesses ausreicht.
Roboter-Blechkäfig-Montagesystem
Für die Entwicklung eines kundenspezifischen Massenautomatisierungssystems, das die hochpräzise Montage von Käfigprodukten mit hoher Mischung und geringen Stückzahlen abdeckt, wurde das Blechkäfig-Montagesystem (siehe Abb. 7-a) mit einem 6-Achsen-Roboter zur Teilebeladung und -montage, einem Visionssystem zur genauen Identifizierung der am Roboterwerkzeug gegriffenen Teileposition und der Montagevorrichtung konstruiert. Der Roboter ist mit zwei Roboterwerkzeugen ausgestattet, einem pneumatischen Greifer zur Beladung und Montage des Separators und der Kick-out-Feder und einem pneumatischen Sauger zur Beladung und Montage des Unterkäfigs und des Oberkäfigs. Die Montagevorrichtung wird durch eine Linearschraube zwischen der Montagestation für den Separator und der Montagestation für den Oberkäfig und die Kick-out-Feder transportiert.
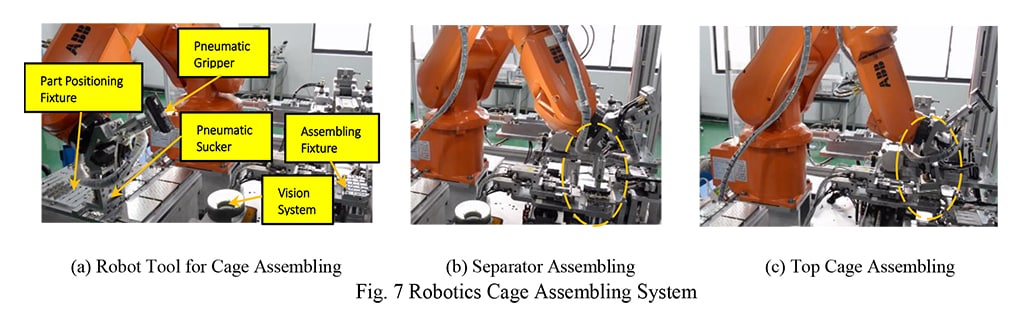
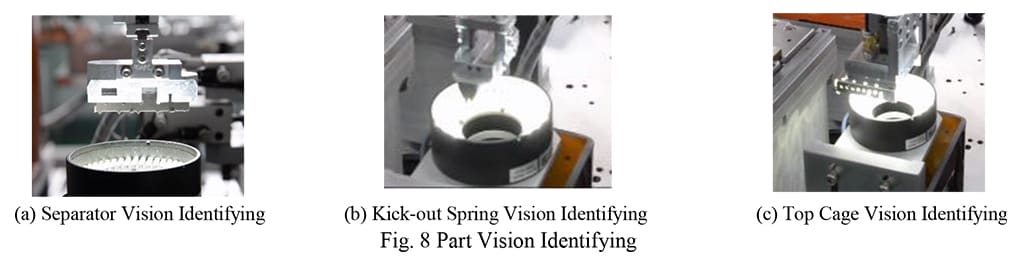
Der Roboter lädt zunächst den unteren Käfig in die Montagevorrichtung an der Montagestation für Trennelemente und lädt und montiert dann die Trennelemente bzw. den unteren Käfig, um eine Unterbaugruppe herzustellen, wie in Abb. 7-b gezeigt. Dann transportiert die Linearschraube die Montagevorrichtung mit der Baugruppe zur Kick-out-Feder-Montagestation und der Montagestation für den Oberkäfig, wo die Montagevorrichtung präzise positioniert wird und die Trennelemente durch den Trennelement-Haltemechanismus für die Kick-out-Feder- und Oberkäfig-Montage präzise gehalten werden, wie in Abb. 7-c dargestellt. Mit dem Bildverarbeitungssystem zur genauen Identifizierung der Pose des am Roboterwerkzeug gegriffenen Teils werden Separator, Kick-out-Feder und Oberkäfig adaptiv mit den von Gl. (5) und Gl. (6) entwickelten Formeln zusammengesetzt.
Optimierung des robotergestützten Montageprozesses
Zur Verbesserung der Zuverlässigkeit und zur Maximierung der Leistungsfähigkeit des Roboter-Blechkäfig-Montagesystems wurden zwei Design of Experiments (DoE) zur Optimierung des Montageprozesses durchgeführt, ein DoE ist für den Separator eine Unterkäfig-Montage, das andere DoE ist für die Kick-out Feder- und Oberkäfig-Montage. Die Schlüsselfaktoren für den hochpräzisen Montageprozess sind in der Regel der Mechanismus zur Teilepositionierung an der Montagevorrichtung und die Roboter-Montagebahn.
Für die Prozessoptimierung beim Zusammenbau des Separators und des Unterkäfigs wird der Unterkäfig gut positioniert und durch den Positionierungsmechanismus an der Montagevorrichtung fixiert. Wie sich herausgestellt hat, dass bei der Montagevorrichtung für die Separatormontage keine großen Probleme auftreten, wurden zwei weitere Faktoren (Montagegeschwindigkeit und Montageweg) zur Optimierung der Ausbeute ausgewählt, und der Pareto, wie in Abb. 9-a dargestellt, deutet darauf hin, dass der Montageweg der effektive Faktor ist, der die Ausbeute bei der Montage stark beeinflusst. Eine optimale Separator-Montage-Ausbeute wurde mit 97 % erreicht, wobei der optimale Separator-Montagepfad in Abb. 10-a und Abb. 10-b dargestellt ist. Aufgrund der Unterschiede in der Trennstruktur unterscheidet sich der Montagepfad für Separator Nr. 1 mit dem Pfad von Separator Nr. 2 und Nr. 3, um Störungen mit dem unteren Käfig zu vermeiden.
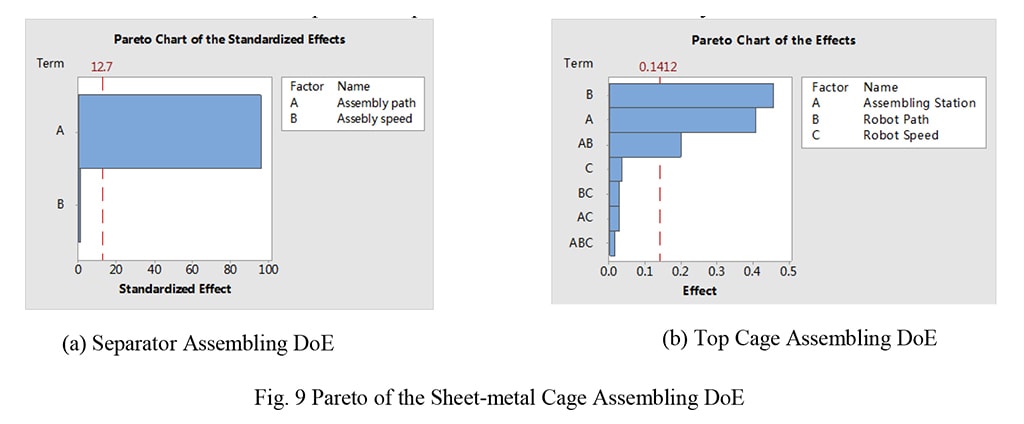
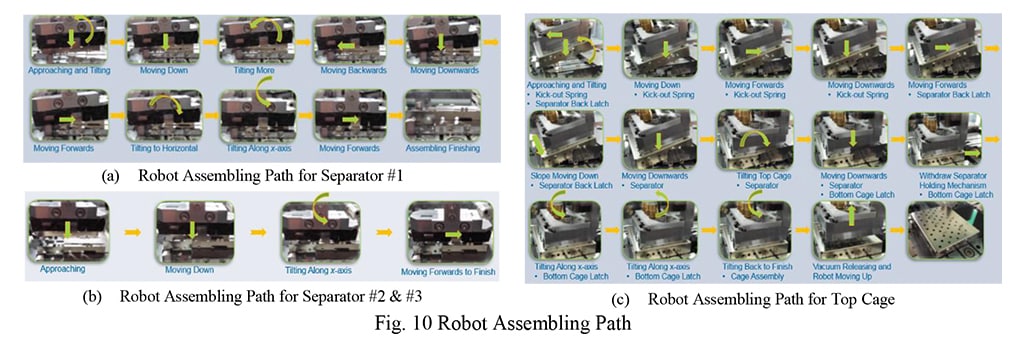
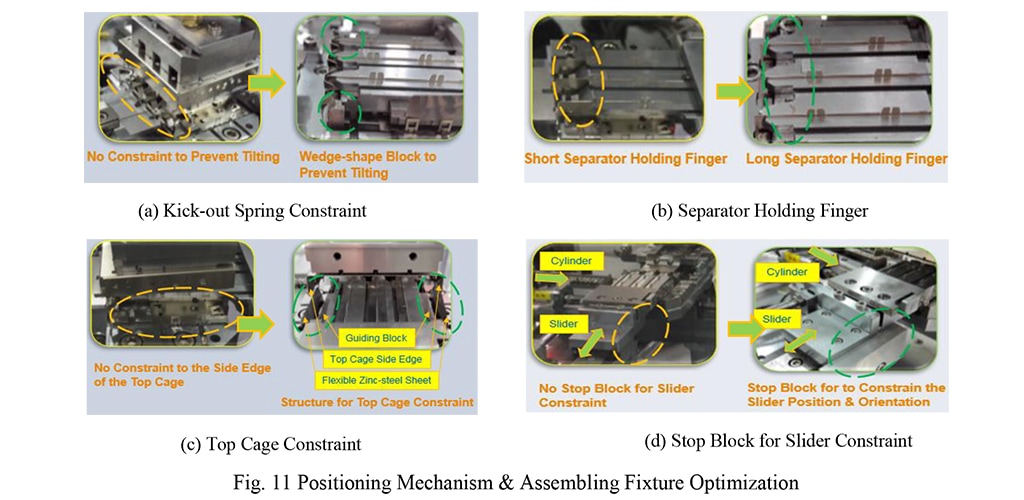
Für die Optimierung der Montage des Oberkäfigs wurden drei Faktoren für die Durchführung der Montage-DoE ausgewählt, und der Pareto, wie in Abb. 9-b dargestellt, zeigt, dass der Roboterweg, die Montagevorrichtung und der Positionierungsmechanismus sowie das Zusammenwirken der beiden Faktoren die wirksamen Faktoren sind. Eine optimale Streckgrenze bei der Montage des Oberkäfigs wurde mit 97 % erreicht, mit dem optimalen Montageweg des Oberkäfigs, wie in Abb. 10-c gezeigt, und dem optimalen Positionierungsmechanismus und der Montagevorrichtung, wie in Abb. 11 gezeigt. Da der obere Käfig gut mit der Kick-out-Feder, des Seperators und dem unteren Käfig zusammenpassen muss, um erfolgreich montiert werden zu können, ist jeder der optimalen Montageschritte gut konzipiert, um die kritischen Punkte zu berücksichtigen. Für den Positionierungsmechanismus wurde eine Montagevorrichtungsoptimierung zur Koordination mit dem Roboter-Montageweg verbessert, um die Montage-Ertragsrate zu verbessern. Die Kick-out-Federeinschränkung wurde verbessert, um durch ein Paar keilförmiger Blöcke eingeschränkt zu werden, um zu verhindern, dass die Feder durch eine geringe Kraft, die vom Oberkäfig ausgeübt wird, gekippt wird, was zur Montage des Oberkäfigs NG führen könnte, wie in Abb. 11-a gezeigt. Der Separator-Haltefinger wurde mit längeren Finger verbessert, um die Separatoren fest und präzise zu halten, damit Vibrationen im Separator mit hoher Geschwindigkeit vermieden werden können, wie in Abb. 11-b gezeigt. Die Einschränkung des Oberkäfigs wurde verbessert, indem die Seitenränder mit dem Führungsblock und dem flexiblen Zinkstahlblech eingeschränkt wurden, um die Kompatibilität der großen Toleranz (-0,1 ~ 0,7 mm) des Abstands zwischen den beiden Seitenrändern des Oberkäfigs sicherzustellen, wie in Abb. 11-c gezeigt. Unter Berücksichtigung der Freiräume zwischen dem Schieber und seiner Führungsbahn für die Zuführung und Entnahme des Separatorhaltefingers, wobei der Pneumatikzylinder auf die Separatorhaltefinger drückt, um den Separator festzuhalten, kann es zu einigen Positions- und Rotationsfehlern für die Separatoren und den unteren Käfig kommen. Damit die Positioniergenauigkeit des Separators und des unteren Käfigs an der Montagestation gewährleistet werden kann, die für die Zuverlässigkeit und Robustheit der Montage entscheidend ist, wird ein Anschlagblock hinzugefügt, um die Position und Ausrichtung des Schiebers zu begrenzen, wie in Abb. 11-d. gezeigt.
Ohne Verlust der Montageausbeute wurde auch die Montageeffizienz durch Optimierung der Robotergeschwindigkeit verbessert. Registerkarte 1 zeigt die optimale Zykluszeit für die Montage der einzelnen Teile, wobei die Verfahrgeschwindigkeit des Roboters auf 2.000 mm/s, die Geschwindigkeit des Roboters für die Montage des Trennelements und die Montage der Trittfeder auf 50 mm/s und die Geschwindigkeit des Roboters für die Montage des Oberkäfigs auf 30 mm/s optimiert ist. Die optimale Zykluszeit erfüllt die Voraussetzung für die Industrialisierung des Käfigmontageprozesses.
Tabelle 1
Montageelement | Unterkäfig | Separator Nr. 1 | Separator Nr. 2 | Separator Nr. 3 | Kick-out-Feder | Oberkäfig |
Zykluszeit (S/St.) | 2.2 | 4.6 | 3.2 | 3.4 | 4.0 | 7.0 |
ERÖRTERUNG UND KERNASPEKTE
Produktionsmaschinenentwicklung für die Blechkäfigmontage
Diese Forschung führt eine Machbarkeitsüberprüfung der roboterbasierten Blechkäfigmontage durch und führte zwei DoEs zur Optimierung des Montageprozesses durch, um die Montageausbeute und die Montagezykluszeit zu verbessern. Offensichtlich wurde die Technologie verifiziert, um das Ziel der Industrialisierung zu erreichen, und die DoE-Plattform wurde in das Werk D&D Zhuhai transferiert, um in der Massenproduktion eingesetzt zu werden. Die neuesten Produktionsdaten zeigen, dass die Plattform eine Ausbeute von 98 % erreicht, mit einer Einsparung der Arbeitskosten für 4 Bediener (48.000 US-Dollar Kostenersparnis pro Jahr). Der nächste Schritt ist der Bau der Produktionsmaschine für die Montage von Blechkäfigen, und es ist vorherzusehen, dass die Einführung der Produktionsmaschine mit dieser Technologie zu einer Einsparung der Arbeitskosten für die Unternehmenssparte D&D von TE in Höhe von jährlich 520.000 US-Dollar führen würde. Außerdem würde die hier entwickelte, auf Robotik basierende Technologie zur Montage von Blechkäfigen die Fähigkeiten von TE in der kundenspezifischen Massenmontage auf hochpräzisem Niveau erheblich verbessern, und sie ist wandelbar, um die Entwicklung der Automatisierung für kundenspezifischen Massenmontage für andere Geschäftsbereiche wie Automobil, Industrie, CPD, Sensorik usw. zu unterstützen, was definitiv große geschäftliche Auswirkungen auf das gesamte Unternehmen TE haben würde.
DANKSAGUNGEN
Es war eine aufregende Reise, an der Entwicklung der auf Robotik basierenden Blechkäfig-Montagetechnologie zu arbeiten. Die Autoren sind der Unterstützung und dem Sponsoring durch die Leiter von TE Global Operations und D&D Business Unit äußerst dankbar, insbesondere Philip Gilchrist, Darel Callis, Rolando Saavedra und Marshall Chen für die hilfreichen Vorschläge und Anweisungen.
QUELLENANGABEN
[1] Technisches Referenzhandbuch – RAPID-Anweisungen, Funktionen und Datentypen, ABB-Roboter-Dokumentation M2004, rev H, RW5.15
Bildverarbeitungsgesteuerte Roboter-Blechkäfig-Montage
AUSZUG
Die hochpräzise Montage von Blechkäfigen ist arbeitsintensiv. Um die Montagekosten zu senken und die Montageeffizienz und -qualität zu verbessern, war die Robotik mit ihren entscheidenden Vorteilen in Bezug auf Geschwindigkeit, Präzision und Flexibilität eine optimale Option für die Konstruktion des automatischen Montagesystems. Vorgestellt wird hier die roboterbasierte Technologie für die Blechkäfigmontage zur Demonstration, Verifizierung und Optimierung der Schlüssellösungen bei der Automatisierung von maßgeschneiderten Montageprozessen.
PROBLEMSTELLUNG
Hochpräzise Blechkäfig-Montageprozesse sind arbeitsintensiv, und es arbeiten mehr als 52 Bediener intensiv an dem Prozess. Wie in Abb. 1 dargestellt, werden die Trennelemente mit dem unteren Käfig zu einer Unterbaugruppe zusammengebaut, und dann wird die Unterbaugruppe mit der Kick-out-Feder und dem oberen Käfig zusammengesetzt, um die gesamte Käfigbaugruppe zu montieren. Offensichtlich ist es besonders wichtig, beim Zusammenbau von Käfigen sehr vorsichtig zu sein, da das Produkt leicht verformt und zerkratzt werden kann. Die Dicke des Blechteils beträgt 0,25 mm, und die Montagegenauigkeit beträgt weniger als 0,03 mm. Darüber hinaus gibt es mehr als 100 zu unterstützende Produktteilenummern. Das in Abb.1 dargestellte Produkt ist ein typisches SFP+ 1X4 Käfigprodukt, und es gibt einige andere Produkte wie 1XN und 2XN, die den Produktfamilien SFP, SFP+, QSFP, ZQSFP usw. zugeordnet sind. Es ist offensichtlich, dass die Automatisierung des Käfigmontageprozesses ein Problem der kundenspezifischen Massenfertigung mit hoher Durchmischung und geringen Stückzahlen ist, und die herkömmlichen Automatisierungsmethoden mit harten Werkzeugen wären in diesem Fall für die Anforderung der kundenspezifischen Massenfertigung nicht geeignet.
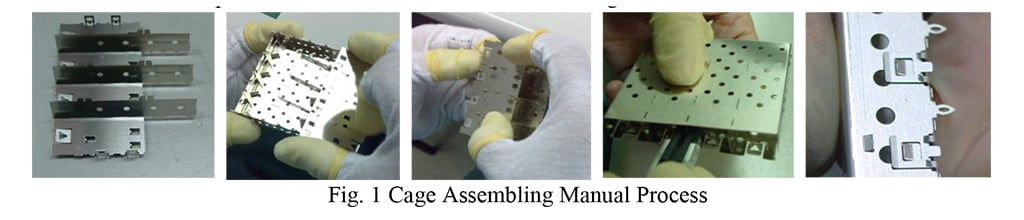
Die Robotik mit ihren entscheidenden Vorteilen in Bezug auf Geschwindigkeit, Präzision und Flexibilität wurde als optimale Option für die Konstruktion des automatischen und flexiblen Montagesystems angesehen. Diese Forschung untersucht die interessanten Fähigkeiten des Roboters / der Robotik, und präsentiert die Lösungen für den Blechkäfig-Montageprozess zur Massenfertigung mit Robotik, welche hervorragende Auswirkungen auf die Wirtschaftlichkeit und die Technologieentwicklung von TE haben können. Um die Zuverlässigkeit und die Robustheit des robotergesteuerten Käfig-Montagesystems zu verbessern, untersucht diese Forschung auch die Details des Montageprozesses und führt zwei Design of Experiments (DoEs) durch, um die Montage des Seperators und des unteren Käfigs und die Montage des oberen Käfigs und der Kick-out-Feder zu optimieren. Das auf Robotik basierende Montagesystem und die aus dieser Forschung entwickelte Methode zur Optimierung des Montageprozesses könnten hoffentlich auf andere Produktmontageprozesse in allen TE-Geschäftsbereichen angewandt werden, um die Montagekosten deutlich zu senken und die Montageeffizienz und -qualität zu verbessern.
METHODEN UND ERGEBNISSE
Einführung in Industrieroboter
Der Industrieroboter ist normalerweise als SCARA-Roboter, 6-Achsen-Roboter und Delta-Roboter bekannt. Der SCARA-Roboter verfügt über 3-DOF (Freiheitsgrad)-Verschiebungen und 1-DOF-Rotation und wird im Allgemeinen zur Durchführung von Pick-and-Place-Operationen eingesetzt; der 6-Achsen-Roboter verfügt über 3-DOF-Verschiebungen und 3-DOF-Rotationen und kann sehr vielseitig in verschiedenen Fertigungs- und Montageprozessen eingesetzt werden. Der Delta-Roboter ist von paralleler Architektur im Allgemeinen mit 3-DOF-Übersetzungen und 1-DOF-Rotation, und wird normalerweise genutzt, um schnelle Pick-and-Place-Operationen durchzuführen. Für den Montageprozess des Blechkäfigs erfordert die Montage des Trennelements und des Oberkäfigs sowohl Übersetzungen als auch Rotationen, damit das Teil einem Montagepfad folgen kann, um die Montage zu beenden. Daher wird in diesem Fall der 6-Achsen-Roboter bevorzugt eingesetzt. Abb. 2 zeigt den typischen 6-Achsen-Roboter und die Roboterarchitektur, um die Mobilität des Roboterendeffektors zu untersuchen. Der 6-achsige Industrieroboter ist auch als 6-R-Mechanismus (R: Revolute Joint) bekannt, der sich weiter in zwei Teile zerlegen lässt: den Arm und das Handgelenk. Der Roboterarm ermöglicht 3-DOF-Übersetzungen und das Roboterhandgelenk 3-DOF-Rotationen. Durch die Koordination zwischen dem Roboterarm und dem Roboterhandgelenk ist der Roboter-End-Effektor in der Lage, jede definierte Pose innerhalb seines Arbeitsbereichs zu erreichen, und wäre recht beweglich, um den Blechkäfig-Montageprozess zu erfüllen.
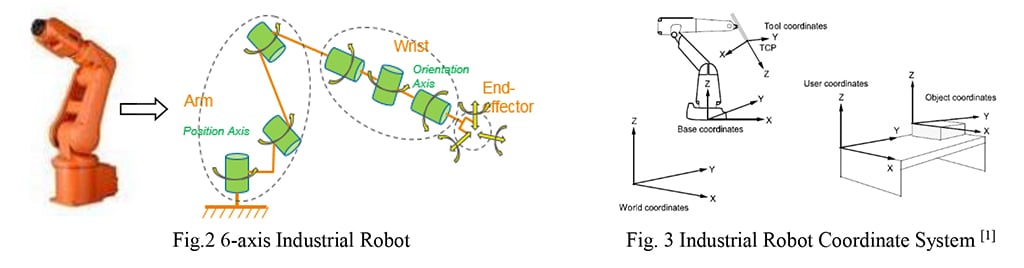
Der Industrieroboter ist inzwischen mit seiner Modellierungs- und Steuerungsmethode sowie mit einer guten Roboterprogrammiersprache als Programmierschnittstelle gut entwickelt. Für den Endanwender ist es nicht notwendig, sich mit den Details der Motorsteuerung, der direkten/inversen Kinematik oder gar der Dynamik auseinanderzusetzen. Es ist jedoch notwendig, einige Techniken mit den Roboterprogrammiersprachen zur Roboterbewegung und Wegplanung zu entwickeln. Wenn der Endeffektor am Roboter installiert ist, basiert die Bewegungs- und Wegplanung auf der Roboter-Werkzeugkoordinate, die definiert und am Roboter-Endeffektor angebracht wird. Abb. 3 zeigt ein Konzept für die wichtigsten Roboterkoordinatensysteme. Die präzise Steuerung des Roboterwegs besteht darin, die kritischen Roboterziele präzise zu steuern. Insbesondere beim Käfigmontageprozess kann der Schritt zur Konstruktion des Roboter-Montagewegs eine lineare Übersetzung oder Rotation oder sogar eine Kombination aus beidem sein. Um einen reibungslosen Montageweg zu konstruieren und Interferenzen zu vermeiden, ist es entscheidend, die Schrittgröße des Roboters genau zu definieren. Für jedes Roboterziel muss der Roboter-Endeffektor in seiner Position (x, y, z) und Ausrichtung (Ex, Ey, Ez) genau definiert sein, wobei x, y, z die Koordinaten ohne das Objekt-Koordinatensystem und Ex, Ey, Ez die Euler-Winkel ohne das Objekt-Koordinatensystem sind.
Bildverarbeitungsgeführte Robotik
Für die hochpräzise Montage besteht die traditionelle Automatisierungsmethode darin, hochpräzise mechanische Vorrichtungen zu entwerfen und herzustellen, um die Positionierung für das Teil durchzuführen, und hochpräzise Mechanismen zu entwickeln, um das Laden des Teils und die Montage durchzuführen. Dies würde eine Herausforderung für das mechanische System darstellen, um die Präzision aufrechtzuerhalten. Während bei der bildverarbeitungsgeführten Robotermethode ein Bildverarbeitungssystem als Teil des Robotersystems integriert ist, um die Pose des am Roboterwerkzeug gehaltenen Teils genau zu identifizieren, übersetzt oder dreht dar Roboter / das Roboterwerkzeug das Teil adaptiv auf der Grundlage des Feedbacks der Bildverarbeitungsidentifikation, um die Montagepräzision zu gewährleisten.
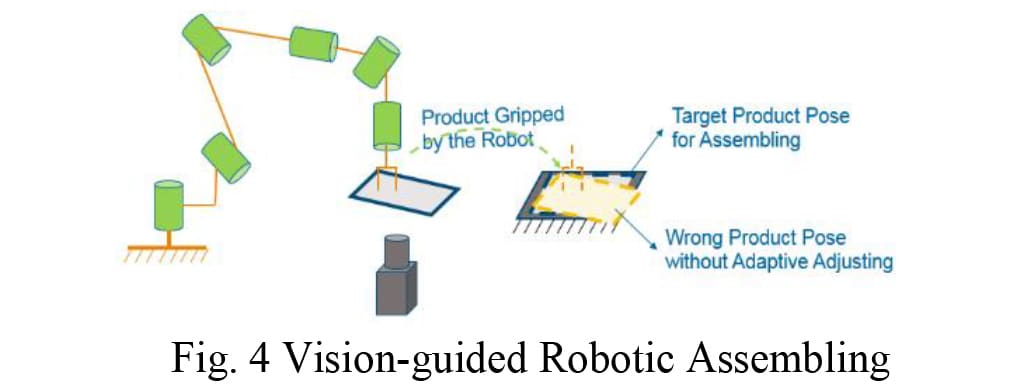
Abb. 4 zeigt ein typisches bildverarbeitungsgeführtes Robotersystem für die adaptive Montage/Pick-and-Place-Bedienung. Da der Roboter das Produkt aufgrund einiger Positionierungsfehler möglicherweise nicht in der gleichen Position oder Ausrichtung aufnimmt und die durch das Roboter-Teaching erzeugte konstante Roboterposition das Produkt nicht zusammenbauen kann, wäre das Bildverarbeitungssystem sehr hilfreich, um den Roboter bei der adaptiven Anpassung des Montagepfades zu führen. So ließe sich die Zuverlässigkeit und Robustheit des Montagesystems gewährleisten.
Das Verfahren zur Entwicklung eines roboteradaptiven Montagealgorithmus besteht darin, zuerst das Basismodell als Referenzmodell zu erstellen und dann das Ziel-Pose-Berechnungsmodell zu formulieren, um die Roboterpose adaptiv anzupassen, damit das Produkt präzise montiert werden kann. Das Basismodell wird erstellt, indem man die Roboter-Pose für die Bilderfassung (XRb, YRb, ARb), die identifizierten Produkt-Pose am Roboter-Werkzeug (XCb, YCb, ACb) durch das 2D-Vision-System und die Teach-Pose (XFb, YFb, AFb) zum präzisen Zusammenbau des Produkts als Bezugsbasis nimmt, mit dem die Produkt-Ziel-Pose (XCFb, YCFb, ACFb) berechnet wird. Es ist offensichtlich, dass die Produkt-Ziel-Pose für den präzisen Zusammenbau des Produkts konstant sein muss. X/Y steht hier für die Position, A steht für den Rotationswinkel entlang der z-Achse, da hier mittels des 2D-Vision-Systems die Posen-Komponente in der 2D-Ebene untersucht wird.
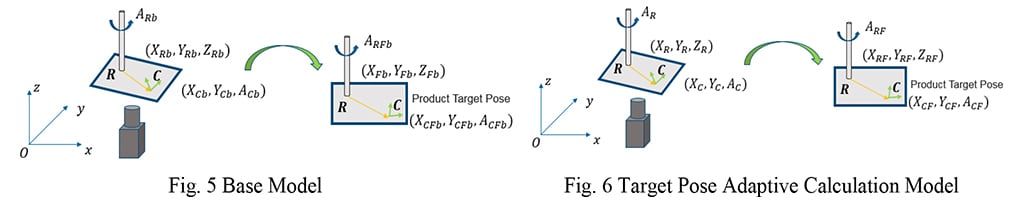
Wie in Abb. 4 dargestellt, greift das Roboterwerkzeug das Produkt am Punkt R, und das Feature zur Darstellung der Produktposition und -ausrichtung am Roboterwerkzeug ist Rahmen C, wobei die Roboter-Teach-Pose zur Montage des Produkts bekannt ist. Die Produktzielposition für die Produktmontage wird basierend auf der planaren Transformation des Vektors 𝒗𝑟𝑐 von der Bilderfassungs-Pose zur Montage-Pose und der Roboter-Teach-Pose zur Montage des Produkts berechnet. Daher wird die Produktzielposition wie folgt formuliert:

wobei Folgendes gilt: 𝒗𝑟𝑐 = (𝑋𝐶𝑏 − 𝑋𝑅𝑏, 𝑌𝐶𝑏 − 𝑌𝑅𝑏)𝑇.
Die Produktzielausrichtung für die Produktmontage wird auf der Grundlage der Produktmerkmalsorientierung ACb und der Rotationsvariation des Roboters berechnet ∆𝐴𝑏 = 𝐴𝑅𝐹𝑏 − 𝐴𝑅𝑏, wie Gl. (2):
𝐴𝐶𝐹𝑏 = 𝐴𝐶𝑏 + ∆𝐴𝑏 (2)
Die adaptive Roboter-Zielposition für die Montage des Produkts wird mit dem in Abb. 6 gezeigten Modell formuliert, und es ist leicht, die Zielposition des Produkts zu kennen, da sie mit der Referenzbasis übereinstimmt:
𝑋𝐶𝐹 = 𝑋𝐶𝐹𝑏, 𝑌𝐶𝐹 = 𝑌𝐶𝐹𝑏, 𝐴𝐶𝐹 = 𝐴𝐶𝐹𝑏 (3)
Die Roboter-Pose für die Bilderfassung ist (XR, YR, AR), die identifizierte Produkt-Pose am Roboterwerkzeug ist (XC, YC, AC) und die Variation des Produktdrehwinkels von der Bilderfassungs-Pose zur Montage-Pose wird als Gl. 4 formuliert:
∆A = 𝐴𝐶𝐹 − 𝐴𝐶 (4)
Daher wird die Zielroboterausrichtung zur Montage des Produkts mit der identifizierten Produkt-Feature-Ausrichtung als Eq. (5) adaptiv berechnet:
𝐴𝑅𝐹 = 𝐴𝑅 + ∆𝐴 = 𝐴𝑅 + 𝐴𝐶𝐹 − 𝐴𝐶 (5)
Die Ziel-Roboterposition für die Produktmontage wird auf der Grundlage der planaren Transformation des Vektors 𝒗𝑟𝑐 und der Produkt-Zielposition als Gl. (6) formuliert:

Wobei Folgendes gilt: 𝒗𝑟𝑐 = (𝑋C − 𝑋R, 𝑌C − 𝑌R)T
Mit dem Bildverarbeitungssystem zur genauen Identifizierung des Produktmerkmals, wie in Abb. 5 und Abb. 6 dargestellt, ist die Roboterpose zur präzisen Montage des Produkts keine konstante Pose, sondern eine adaptive Roboterpose, die durch Gl. (5) und Gl. (6) formuliert wurde.
Für den Montageprozess des Blechkäfigs beträgt die mechanische Positioniergenauigkeit für den Separator und die Kick-out-Feder etwa 0,3 mm, und die mechanische Positioniergenauigkeit für den Oberkäfig beträgt etwa 0,1 mm in der Position und etwa 0,25 Grad in der Ausrichtung. Um die Montagegenauigkeit von 0,03 mm zu erreichen, ist ein Visionssystem mit einer Positioniergenauigkeit von +/-0,003 mm integriert, um den Roboter adaptiv zu führen, wie in Abb. 8 dargestellt. In Kombination mit der Wiederholgenauigkeit des Roboters von +/-0,01 mm liegt die Gesamtgenauigkeit des Robotersystems für die Montage bei etwa 0,02 mm, was für die Ausführung des Blechkäfig-Montageprozesses ausreicht.
Roboter-Blechkäfig-Montagesystem
Für die Entwicklung eines kundenspezifischen Massenautomatisierungssystems, das die hochpräzise Montage von Käfigprodukten mit hoher Mischung und geringen Stückzahlen abdeckt, wurde das Blechkäfig-Montagesystem (siehe Abb. 7-a) mit einem 6-Achsen-Roboter zur Teilebeladung und -montage, einem Visionssystem zur genauen Identifizierung der am Roboterwerkzeug gegriffenen Teileposition und der Montagevorrichtung konstruiert. Der Roboter ist mit zwei Roboterwerkzeugen ausgestattet, einem pneumatischen Greifer zur Beladung und Montage des Separators und der Kick-out-Feder und einem pneumatischen Sauger zur Beladung und Montage des Unterkäfigs und des Oberkäfigs. Die Montagevorrichtung wird durch eine Linearschraube zwischen der Montagestation für den Separator und der Montagestation für den Oberkäfig und die Kick-out-Feder transportiert.
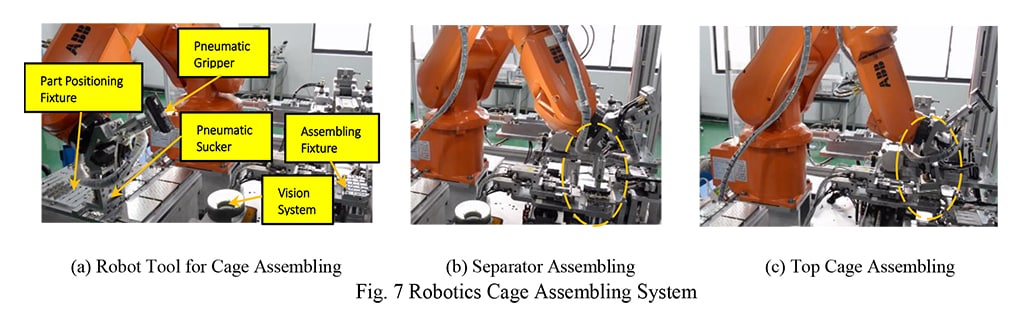
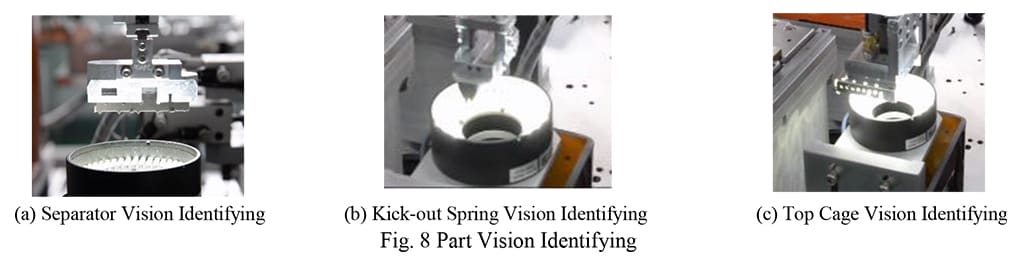
Der Roboter lädt zunächst den unteren Käfig in die Montagevorrichtung an der Montagestation für Trennelemente und lädt und montiert dann die Trennelemente bzw. den unteren Käfig, um eine Unterbaugruppe herzustellen, wie in Abb. 7-b gezeigt. Dann transportiert die Linearschraube die Montagevorrichtung mit der Baugruppe zur Kick-out-Feder-Montagestation und der Montagestation für den Oberkäfig, wo die Montagevorrichtung präzise positioniert wird und die Trennelemente durch den Trennelement-Haltemechanismus für die Kick-out-Feder- und Oberkäfig-Montage präzise gehalten werden, wie in Abb. 7-c dargestellt. Mit dem Bildverarbeitungssystem zur genauen Identifizierung der Pose des am Roboterwerkzeug gegriffenen Teils werden Separator, Kick-out-Feder und Oberkäfig adaptiv mit den von Gl. (5) und Gl. (6) entwickelten Formeln zusammengesetzt.
Optimierung des robotergestützten Montageprozesses
Zur Verbesserung der Zuverlässigkeit und zur Maximierung der Leistungsfähigkeit des Roboter-Blechkäfig-Montagesystems wurden zwei Design of Experiments (DoE) zur Optimierung des Montageprozesses durchgeführt, ein DoE ist für den Separator eine Unterkäfig-Montage, das andere DoE ist für die Kick-out Feder- und Oberkäfig-Montage. Die Schlüsselfaktoren für den hochpräzisen Montageprozess sind in der Regel der Mechanismus zur Teilepositionierung an der Montagevorrichtung und die Roboter-Montagebahn.
Für die Prozessoptimierung beim Zusammenbau des Separators und des Unterkäfigs wird der Unterkäfig gut positioniert und durch den Positionierungsmechanismus an der Montagevorrichtung fixiert. Wie sich herausgestellt hat, dass bei der Montagevorrichtung für die Separatormontage keine großen Probleme auftreten, wurden zwei weitere Faktoren (Montagegeschwindigkeit und Montageweg) zur Optimierung der Ausbeute ausgewählt, und der Pareto, wie in Abb. 9-a dargestellt, deutet darauf hin, dass der Montageweg der effektive Faktor ist, der die Ausbeute bei der Montage stark beeinflusst. Eine optimale Separator-Montage-Ausbeute wurde mit 97 % erreicht, wobei der optimale Separator-Montagepfad in Abb. 10-a und Abb. 10-b dargestellt ist. Aufgrund der Unterschiede in der Trennstruktur unterscheidet sich der Montagepfad für Separator Nr. 1 mit dem Pfad von Separator Nr. 2 und Nr. 3, um Störungen mit dem unteren Käfig zu vermeiden.
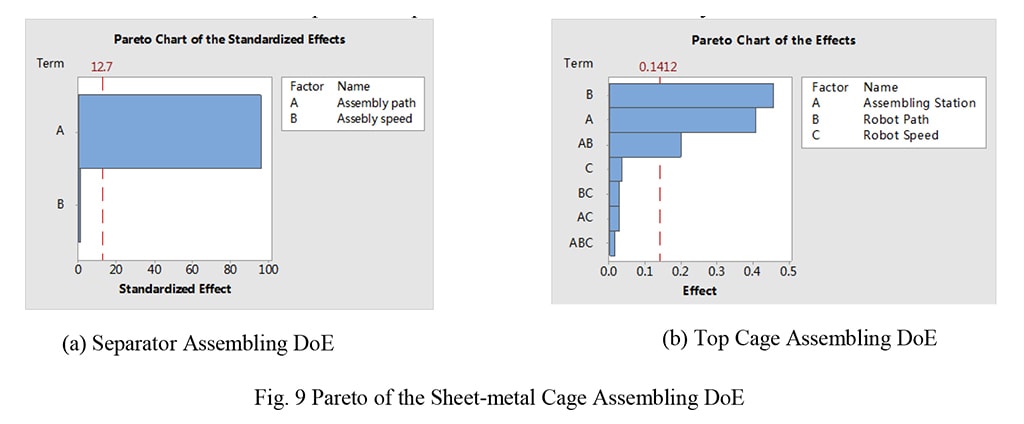
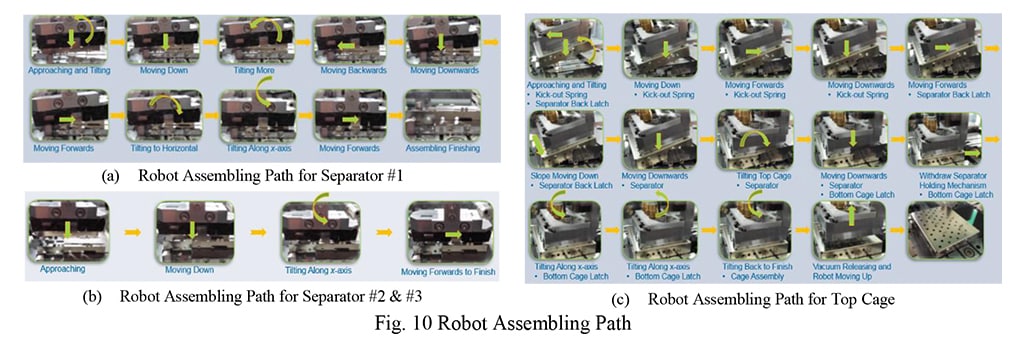
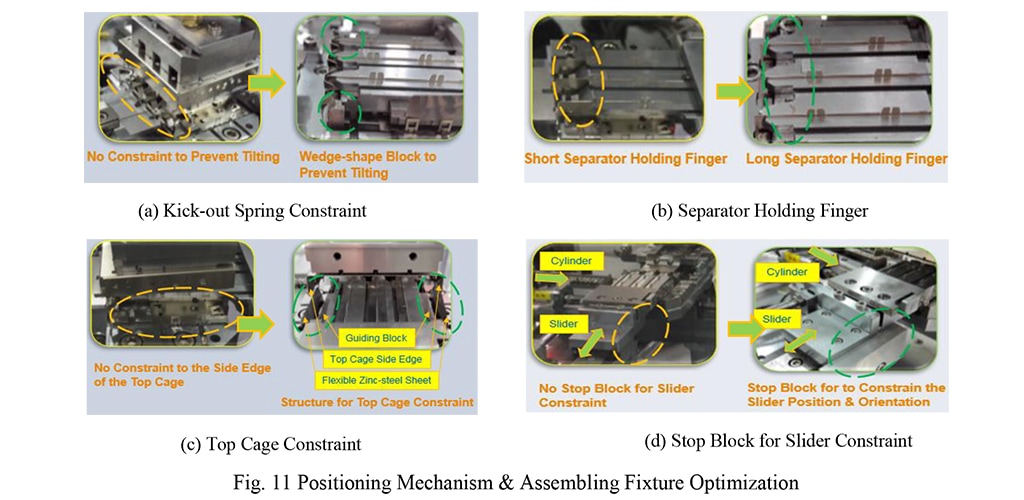
Für die Optimierung der Montage des Oberkäfigs wurden drei Faktoren für die Durchführung der Montage-DoE ausgewählt, und der Pareto, wie in Abb. 9-b dargestellt, zeigt, dass der Roboterweg, die Montagevorrichtung und der Positionierungsmechanismus sowie das Zusammenwirken der beiden Faktoren die wirksamen Faktoren sind. Eine optimale Streckgrenze bei der Montage des Oberkäfigs wurde mit 97 % erreicht, mit dem optimalen Montageweg des Oberkäfigs, wie in Abb. 10-c gezeigt, und dem optimalen Positionierungsmechanismus und der Montagevorrichtung, wie in Abb. 11 gezeigt. Da der obere Käfig gut mit der Kick-out-Feder, des Seperators und dem unteren Käfig zusammenpassen muss, um erfolgreich montiert werden zu können, ist jeder der optimalen Montageschritte gut konzipiert, um die kritischen Punkte zu berücksichtigen. Für den Positionierungsmechanismus wurde eine Montagevorrichtungsoptimierung zur Koordination mit dem Roboter-Montageweg verbessert, um die Montage-Ertragsrate zu verbessern. Die Kick-out-Federeinschränkung wurde verbessert, um durch ein Paar keilförmiger Blöcke eingeschränkt zu werden, um zu verhindern, dass die Feder durch eine geringe Kraft, die vom Oberkäfig ausgeübt wird, gekippt wird, was zur Montage des Oberkäfigs NG führen könnte, wie in Abb. 11-a gezeigt. Der Separator-Haltefinger wurde mit längeren Finger verbessert, um die Separatoren fest und präzise zu halten, damit Vibrationen im Separator mit hoher Geschwindigkeit vermieden werden können, wie in Abb. 11-b gezeigt. Die Einschränkung des Oberkäfigs wurde verbessert, indem die Seitenränder mit dem Führungsblock und dem flexiblen Zinkstahlblech eingeschränkt wurden, um die Kompatibilität der großen Toleranz (-0,1 ~ 0,7 mm) des Abstands zwischen den beiden Seitenrändern des Oberkäfigs sicherzustellen, wie in Abb. 11-c gezeigt. Unter Berücksichtigung der Freiräume zwischen dem Schieber und seiner Führungsbahn für die Zuführung und Entnahme des Separatorhaltefingers, wobei der Pneumatikzylinder auf die Separatorhaltefinger drückt, um den Separator festzuhalten, kann es zu einigen Positions- und Rotationsfehlern für die Separatoren und den unteren Käfig kommen. Damit die Positioniergenauigkeit des Separators und des unteren Käfigs an der Montagestation gewährleistet werden kann, die für die Zuverlässigkeit und Robustheit der Montage entscheidend ist, wird ein Anschlagblock hinzugefügt, um die Position und Ausrichtung des Schiebers zu begrenzen, wie in Abb. 11-d. gezeigt.
Ohne Verlust der Montageausbeute wurde auch die Montageeffizienz durch Optimierung der Robotergeschwindigkeit verbessert. Registerkarte 1 zeigt die optimale Zykluszeit für die Montage der einzelnen Teile, wobei die Verfahrgeschwindigkeit des Roboters auf 2.000 mm/s, die Geschwindigkeit des Roboters für die Montage des Trennelements und die Montage der Trittfeder auf 50 mm/s und die Geschwindigkeit des Roboters für die Montage des Oberkäfigs auf 30 mm/s optimiert ist. Die optimale Zykluszeit erfüllt die Voraussetzung für die Industrialisierung des Käfigmontageprozesses.
Tabelle 1
Montageelement | Unterkäfig | Separator Nr. 1 | Separator Nr. 2 | Separator Nr. 3 | Kick-out-Feder | Oberkäfig |
Zykluszeit (S/St.) | 2.2 | 4.6 | 3.2 | 3.4 | 4.0 | 7.0 |
ERÖRTERUNG UND KERNASPEKTE
Produktionsmaschinenentwicklung für die Blechkäfigmontage
Diese Forschung führt eine Machbarkeitsüberprüfung der roboterbasierten Blechkäfigmontage durch und führte zwei DoEs zur Optimierung des Montageprozesses durch, um die Montageausbeute und die Montagezykluszeit zu verbessern. Offensichtlich wurde die Technologie verifiziert, um das Ziel der Industrialisierung zu erreichen, und die DoE-Plattform wurde in das Werk D&D Zhuhai transferiert, um in der Massenproduktion eingesetzt zu werden. Die neuesten Produktionsdaten zeigen, dass die Plattform eine Ausbeute von 98 % erreicht, mit einer Einsparung der Arbeitskosten für 4 Bediener (48.000 US-Dollar Kostenersparnis pro Jahr). Der nächste Schritt ist der Bau der Produktionsmaschine für die Montage von Blechkäfigen, und es ist vorherzusehen, dass die Einführung der Produktionsmaschine mit dieser Technologie zu einer Einsparung der Arbeitskosten für die Unternehmenssparte D&D von TE in Höhe von jährlich 520.000 US-Dollar führen würde. Außerdem würde die hier entwickelte, auf Robotik basierende Technologie zur Montage von Blechkäfigen die Fähigkeiten von TE in der kundenspezifischen Massenmontage auf hochpräzisem Niveau erheblich verbessern, und sie ist wandelbar, um die Entwicklung der Automatisierung für kundenspezifischen Massenmontage für andere Geschäftsbereiche wie Automobil, Industrie, CPD, Sensorik usw. zu unterstützen, was definitiv große geschäftliche Auswirkungen auf das gesamte Unternehmen TE haben würde.
DANKSAGUNGEN
Es war eine aufregende Reise, an der Entwicklung der auf Robotik basierenden Blechkäfig-Montagetechnologie zu arbeiten. Die Autoren sind der Unterstützung und dem Sponsoring durch die Leiter von TE Global Operations und D&D Business Unit äußerst dankbar, insbesondere Philip Gilchrist, Darel Callis, Rolando Saavedra und Marshall Chen für die hilfreichen Vorschläge und Anweisungen.
QUELLENANGABEN
[1] Technisches Referenzhandbuch – RAPID-Anweisungen, Funktionen und Datentypen, ABB-Roboter-Dokumentation M2004, rev H, RW5.15