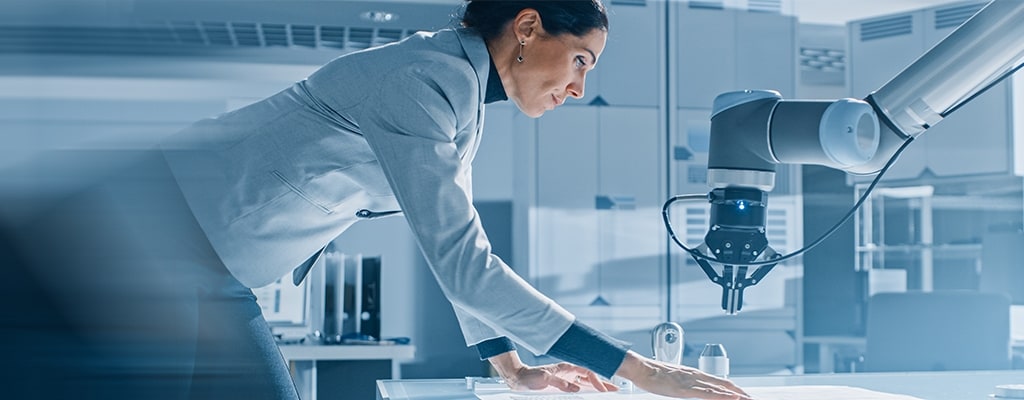
Trend
Mehr Sicherheitsleistung für Cobots durch Drehmomentsensoren
Erfahren Sie mehr über unsere Drehmomentsensoren
Autoren:
Arthur Vignolles, Product Development Engineering Manager, TE Connectivity
Ricardo Garcia, Product Manager – Kraft- und Drehmomentsensoren, TE Connectivity

Steigerung der Effizienz und Rentabilität mit Cobots
Im Zuge der Entwicklung der Industrie 4.0 ist der Einsatz von hochentwickelten Robotern sowie von fortschrittlichen Automatisierungs- und Steuerungssystemen innerhalb industrieller Anwendungen immer üblicher geworden, da die Firmen ihr Streben nach mehr Effizienz und Rentabilität fortsetzen. Die Weiterentwicklung der automatisierten Technologie hat dazu beigetragen, die Entwicklung kollaborativer Roboter voranzutreiben. Kollaborative Roboter oder Cobots sind Roboter, die neben oder mit Menschen arbeiten können. Diese Cobots sollen mit Arbeitern interagieren und ihnen helfen, anstatt eigenständige automatisierte Geräte mit wenig bis gar keiner menschlichen Interaktion zu sein. Historisch gesehen war diese begrenzte Interaktion auf Sicherheitsbedenken und die Tatsache zurückzuführen, dass Mensch und Roboter nicht in der Lage waren, effektiv und effizient zusammenzuarbeiten.
Heute bieten Cobots eine viel größere Flexibilität am Arbeitsplatz, da Schutzkäfige nicht mehr für Sicherheitszwecke benötigt werden und Cobots entwickelt wurden, um nahtlos mit Menschen zusammenzuarbeiten. Sie sind in der Lage, Aufgaben gemeinsam auszuführen, die weder Menschen noch Roboter alleine bewerkstelligen können. Diese Flexibilität trägt auch dazu bei, die Kapitalrendite (ROI) aufgrund der höheren Produktivität und der geringeren Arbeitskosten zu erhöhen. Diese Cobots können auch komplexe oder gefährliche Aufgaben
bewältigen, die der Mensch entweder nicht oder nicht sicher erledigen kann. Zum Beispiel haben Cobots die Fähigkeit, Operationen mit einem Grad an Präzision und Stabilität durchzuführen, der über die Fähigkeiten selbst des besten menschlichen Chirurgen hinausgeht. Was die Sicherheit betrifft, so können Cobots mit toxischen Materialien umgehen und in Umgebungen arbeiten, die für den Menschen nicht geeignet sind.
Von der Produktfertigung bis hin zu industriellen Verpackungsanwendungen – und bei allem, das dazwischen stattfindet – spielen Cobots eine wichtige Rolle bei der Steigerung der Produktivität am Arbeitsplatz. Da Firmen weiterhin neue Wege finden, Cobots zu integrieren, und die Vorteile der Nutzung von Cobots besser verstanden werden, führt dies zu einem enormen Wachstum bei ihrem Einsatz in Fabriken und Fertigungsstätten. Laut dem World Robotics Report der International Federation of Robotics (IFR) wurden im Jahr 2020 22.000 Cobots montiert – ein Anstieg von 11.000 gegenüber 2017. Darüber hinaus ist der weltweite Umsatz mit kollaborativen Robotern seit 2018 um mehr als 25 % gestiegen, obwohl der Gesamtmarkt für Industrieroboter eine pandemiebedingte Verlangsamung verzeichnete. Was das zukünftige Wachstum betrifft, so wird erwartet, dass der Absatz von Robotern auf dem chinesischen Markt in den nächsten 5 Jahren um 30 % steigen wird. Mit dem zunehmenden Einsatz von Cobots hat man sich auf Vorschriften konzentriert, die eine sichere Arbeitsumgebung gewährleisten und das Personal, das mit diesen Cobots arbeitet, schützen sollen.
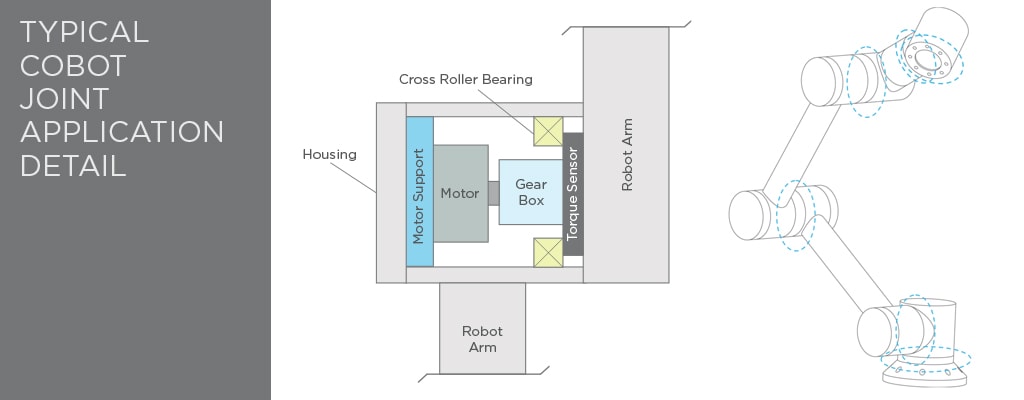
Da die Sicherheitsanforderungen für Cobots entwickelt und erweitert wurden, werden Technologien zur Überwachung und Steuerung von Cobots in diese Maschinen integriert. Ein Beispiel dafür ist ein Drehmomentsensor, der das mechanische Drehmoment in einer Vielzahl von Drehpunkten an einem Cobot überwacht. Der Drehmomentsensor basiert auf einer integrierten MEMs-Kraftmesszelle, die ein mechanisches Drehmoment in ein digitales Ausgangssignal übersetzen kann, das proportional zum angelegten Drehmoment ist. Diese Drehmomentsensoren werden in Cobots verwendet, um Bedingungen zu erkennen, bei denen das Drehmomentniveau hoch genug ist, dass es einen Menschen in einer kooperativen Anwendung potenziell schädigen könnte, oder bei denen das Drehmomentniveau den Cobot selbst beschädigen könnte.
Unser Sicherheitsdrehmomentsensor beginnt mit einem einteiligen Biegeelement, das dazu bestimmt ist, das Rotationsdrehmoment in mechanische Belastung umzusetzen. Piezoresistive Dehnungsmessstreifen werden an den Biegebereichen angebracht und in einer Wheatstone-Brückenkonfiguration montiert, sodass die mechanische Dehnung in mV/V-Ausgang übersetzt werden kann. Zwei kleine Leiterplatten beherbergen einen ASIC und andere elektrische Komponenten. Das rohe mV/V-Signal wird im I2C-Format kompensiert, verstärkt und digitalisiert. Diese Daten sind im Bus verfügbar. Je nach Anwendung kann ein Drehmomentschwellenwert festgelegt werden, der es dem Cobot ermöglicht, herunterzufahren, bevor Menschen verletzt werden oder bevor Schäden am Cobot selbst auftreten.
Sicherheitsdrehmomentsensoren sind in der Regel in die Gelenkeinheiten des Cobots integriert. Die Gelenkeinheit ist ein komplettes System und umfasst normalerweise einen oder mehrere Winkelsensoren sowie einen Motor und ein Getriebe. Die Gelenkeinheit steuert die Bewegung jedes Arms des Roboters, während der Drehmomentsensor verwendet wird, um das Drehmoment im Motor und Getriebe nachzuvollziehen. Das Drehmoment wird von der Steuerkreismaschine verwendet, um die Verbindung herunterzufahren, um Schäden am Arm selbst oder, wenn er kollaborativ verwendet wird, dem entsprechenden Arbeiter zu verhindern.
Der Trend zur Verwendung von Drehmomentsensoren in Cobot-Anwendungen wurde durch die Vorteile, die Drehmomentsensoren für das System bieten, vorangetrieben. Drehmomentsensoren ermöglichen eine schnellere Reaktionszeit und eine verbesserte Genauigkeit, was zu sichereren und zuverlässigeren Cobot-Systemen sowie zu erhöhter menschlicher Sicherheit führt. Die Verwendung eines Drehmomentsensors in jedem Armgelenk ermöglicht die direkte Erfassung der auf den Arm ausgeübten externen Kraft oder des Drehmoments, anstatt sich auf komplexe Berechnungen zu verlassen, die von den Motorströmen abgeleitet werden. Dies ermöglicht ein sehr schnelles Anhalten bei Kontakt und kann daher schnellere Armbewegungen in kollaborativen Situationen ermöglichen, in denen die Kräfte bei menschlichem Kontakt begrenzt werden müssen. Ein weiterer Vorteil ergibt sich, wenn der Cobot im nachgiebigen Modus arbeitet. Die „aktive“ Nachgiebigkeit ermöglicht es, den Arm mit der Hand zu führen (Lead-Through-Programmierung), was das Anlernen des Roboters für neue Aufgaben vereinfacht. Die direkte Erkennung des Drehmoments der Gelenke ermöglicht eine reibungslose und präzise Steuerung der Armbewegung, während er geführt wird.

Unsere Sicherheits-Drehmomentsensoren wurden entwickelt, um genaue Drehmomentdaten bereitzustellen und gleichzeitig Querlastfehler (Axiallast, Radiallast und Kippmoment) zu minimieren und können als Abdichtung in einem Getriebe fungieren. Um funktionale Sicherheitsanforderungen bis ISO13849 Kategorie 3 PL d zu erfüllen, basiert das Design auf einem Dual-Channel-System und enthält weitere Funktionen, um sicherheitsrelevante Fehler zu erkennen. Der Sicherheitsdrehmomentsensor führt zu mehr Sicherheit und Zuverlässigkeit in Cobots, da diese Maschinen die Entwicklung von Industrie 4.0 weiter vorantreiben.

