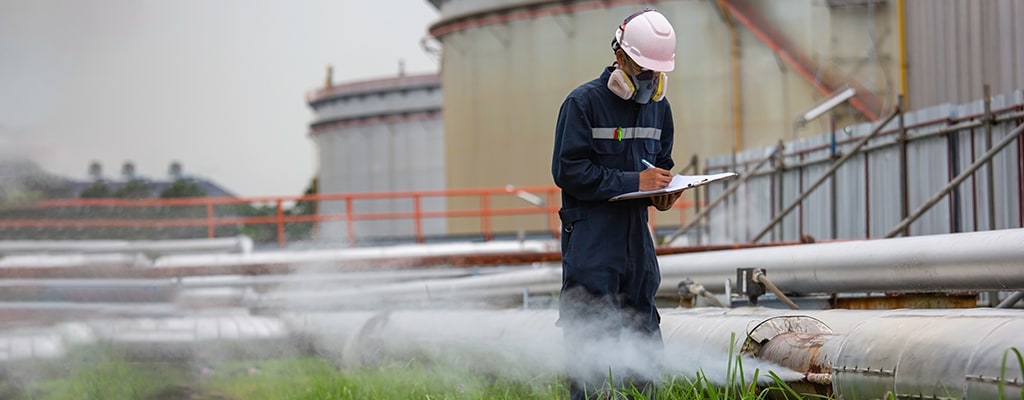
Branchen
Erkennung und Überwachung der
CUI in der Öl- und Gasindustrie
Korrosion unter Isolierung (Corrosion Under Insulation, CUI) ist eine große Herausforderung in verschiedenen Branchen, insbesondere in der Petrochemie und der Öl- und Gasindustrie. Dieses weit verbreitete Problem, das sich unter Isolationsschichten verbirgt, bleibt oft unbemerkt, bis eine routinemäßige Wartung durchgeführt wird. Wird dieses Problem ignoriert, kann dies zu Sicherheitseinbußen, Umweltschäden, Betriebsunterbrechungen, finanziellen Verlusten, Nichteinhaltung gesetzlicher Vorschriften, verkürzter Lebensdauer von Anlagen und erhöhten Anforderungen an die Instandhaltung führen. Letztendlich stellt dies ein ernsthaftes Risiko für Verletzungen oder sogar den Verlust von Menschenleben dar. Berichten zufolge ist Korrosion unter der Isolierung für 40 bis 60 % der Kosten für die Reparatur von Pipelines verantwortlich (Dey, o.J.), was Hunderte von Milliarden US-Dollar an jährlichen Industrieausgaben ausmacht.
Dieses Whitepaper befasst sich mit dem hartnäckigen CUI-Problem. Es behandelt fortschrittliche Sensortechnologien und Überwachungstechniken, die für die Früherkennung und kontinuierliche Überwachung von Korrosion unter der Isolierung entscheidend sind, um potenzielle Risiken proaktiv zu verringern. Dadurch kann die Integrität der Anlagen aufrechterhalten und ein kontinuierlicher und sicherer Betrieb in der Öl- und Gasindustrie ermöglicht werden.

Übersicht: Korrosion unter der Isolierung (CUI)
CUI ist die äußere Korrosion, die typischerweise bei isolierten Anlagen aus Kohlenstoffstahl oder niedrig legiertem Stahl, wie z. B. Rohrleitungen, auftritt. Damit es zu dieser Art von Korrosion kommen kann, müssen zwei Bedingungen erfüllt sein:
- Vorhandensein von Wasser
- Verfügbarkeit von Sauerstoff
CUI ist am häufigsten in Prozessanlagen und Raffinerien anzutreffen, die bei schwankenden Temperaturen betrieben werden, was wesentlich zum Korrosionsprozess beiträgt. Darüber hinaus wirkt die Exposition des Systems gegenüber korrosiven Produkten, die mit der Rohroberfläche in Kontakt kommen, als Korrosionsquelle.
Das von der Isolierung umgebene Rohr besteht in der Regel aus Stahl und die Isolierung aus Materialien oder Materialkombinationen, die um das Rohr gewickelt werden, um die Übertragung von Wärmeenergie erheblich zu verringern. Diese effektive Reduzierung von Energieverlusten trägt zu erheblichen Kosteneinsparungen bei.
Wärme- und Kälteisolierung von Rohrleitungen
Die Wärmeisolierung verhindert die Energieübertragung der erhitzten Flüssigkeit. Die Hauptfunktion dieser Isolierung ist die Wärmespeicherung. Außerdem schützt sie die Bediener vor heißen Oberflächen. Häufig verwendete Materialien für die Wärmeisolierung sind Mineralwolle, Glaswolle und Kalziumsilikat.
Andererseits reduziert die Kälteisolierung die Wärmeübertragung von der Außenumgebung auf die Rohrleitungen und begrenzt die Kondensation. Zu den am weitesten verbreiteten Materialien für die Kälteisolierung gehören Polyurethanschaum oder Gummischaum.
Das Verständnis der Zusammensetzung und Funktion von Isoliermaterialien, sowohl für die Wärme- als auch für die Kälteisolierung, liefert grundlegende Erkenntnisse über ihre Rolle bei der komplexen Problematik der Korrosion unter der Isolierung. Während die Hauptaufgabe der Isolierung darin besteht, die Energieübertragung zu kontrollieren, schafft sie in Kombination mit bestimmten Umwelt- und Betriebsbedingungen unbeabsichtigt eine Umgebung, die Korrosion begünstigt.
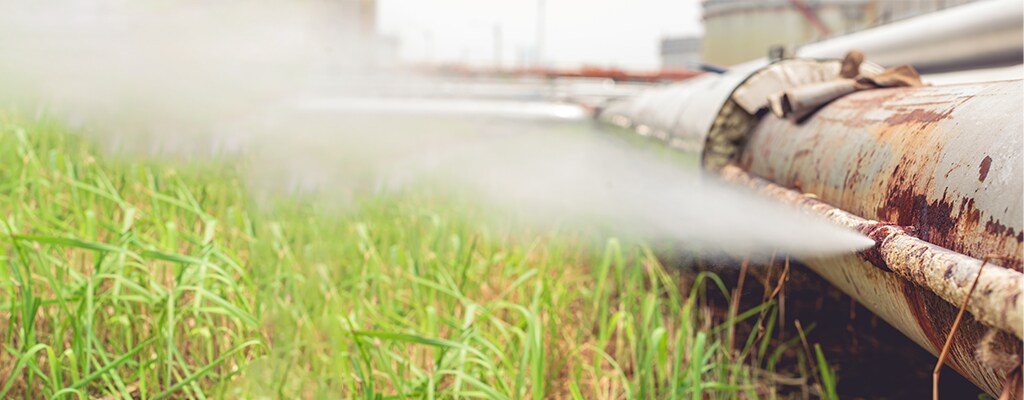
Korrosive Umgebungsbedingungen, die auf ein isoliertes Rohr einwirken.
Konventionelle CUI-Erkennung
CUI wird durch mehrere Faktoren gefördert. Das Zusammenspiel dieser Elemente bildet ein komplexes Geflecht von Kausalitäten, das das Problem verschärft und seine Erkennung und Bewältigung erschwert. Lassen Sie uns das Zusammenspiel dieser Faktoren genauer analysieren und untersuchen, wie ihre komplexen Wechselwirkungen die Entwicklung von CUI unterstützen.
Erstens haben die Umweltbedingungen einen großen Einfluss auf das Auftreten von CUI. Feuchtigkeit, Temperaturschwankungen und die Exposition gegenüber Salznebel oder die industrielle Schadstoffbelastung können die Wahrscheinlichkeit erhöhen, dass Wasser in die Isolaierung eindringt, was eine Voraussetzung für CUI ist. Diese Bedingungen, kombiniert mit der Betriebstemperatur der Ausrüstung, schaffen oft perfekte Bedingungen für Korrosion.
Ein weiterer kritischer Faktor ist die Qualität und Art der Isolierung. Wie bereits erwähnt, gibt es große Unterschiede bei den Isoliermaterialien, und ihre Wirksamkeit und Anfälligkeit für Wasseransammlungen können zu CUI beitragen. Beispielsweise tragen poröse Isoliermaterialien (hydrophil) oder geschlossene Zellen (hydrophob) auf unterschiedliche Weise zu CUI bei.
Die Materialeigenschaften der isolierten Geräte, insbesondere ihre Korrosionsbeständigkeit, spielen bei der Entstehung von CUI eine entscheidende Rolle. Kohlenstoffstähle und niedrig legierte Stähle neigen zum Rosten, wenn sie Feuchtigkeit ausgesetzt sind, was durch hohe Temperaturen noch verstärkt wird.
Auch die betriebliche Praxis trägt dazu bei. Zum Beispiel können Geräte, die häufig zwischen hohen und niedrigen Temperaturen wechseln, zu Kondensation innerhalb der Isolierung führen, was ein ideales Umfeld für Korrosion schafft. Auch die Instandhaltungspraktiken haben einen erheblichen Einfluss auf das Auftreten von CUI. Bleibt die Isolierung beschädigt oder wird die Durchfeuchtung nicht rechtzeitig behoben, steigt das Risiko.
Das Verständnis dieser komplexen Wechselwirkungen ist entscheidend für die Formulierung wirksamer Strategien zur Vermeidung und Verminderung von CUI. Bevor wir uns mit diesen Strategien und ihrer Wirksamkeit befassen, wollen wir das CUI-Phänomen anhand eines typischen Fallbeispiels vertiefen: dem Bau von wärmeisolierten Rohren. Um die Isolierung physisch zu sichern und vor äußeren Witterungseinflüssen zu schützen, wird eine Ummantelung aus Metall, oft als „Mantel“ bezeichnet, um die Isolierung gelegt und mit Metallbändern befestigt. Dieser Mantel ist so konzipiert, dass er sich um die Isolierung wickelt, wodurch Längs- oder Radialfugen entstehen.
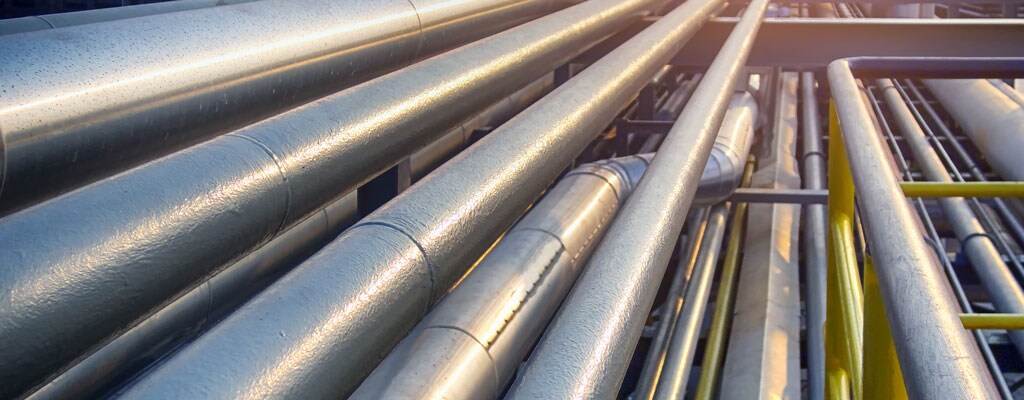
Isoliertes Rohr mit Metallmantel.
Regen ist zwar eine häufige Ursache, aber nicht die einzige Wasserquelle, die Auslöser von CUI sein kann. Wasser kann auch aus Kühltürmen, Dampf und verschiedenen Prozessen stammen, bei denen Flüssigkeiten austreten können. Das Eindringen von Wasser kann durch Beschädigungen der Auskleidung, durch gebrochene Abdichtungen oder durch äußere Einwirkungen wie Stöße, scharfe oder herabfallende Gegenstände oder durch Personen, die auf der Rohrleitung gehen, verursacht werden. Sobald Wasser eindringt, ist dies nicht immer sofort erkennbar, aber bei Regen ist das Eindringen von Wasser unvermeidlich.
Die Wechselwirkung zwischen Wasser und Isoliermaterial kann je nach Art des Materials unterschiedlich sein. Wie bereits erwähnt, fließt das Wasser bei hydrophobem Isoliermaterial (geschlossene Zellen, die keine Wasseraufnahme zulassen) ab und bleibt zwischen Isolierung und Rohr eingeschlossen. Dieses Wasser wird im Laufe der Zeit nicht immer vollständig verdunsten und an einigen Stellen können Wassertaschen zurückbleiben.
Umgekehrt, wenn das Isoliermaterial hydrophil ist (in der Lage, Feuchtigkeit wie ein Schwamm aufzunehmen), erzeugt das Wasser eine Wärmeleitung durch den Schwamm, und der Wärmeimpuls geht vom Rohr zur Ummantelung, wodurch ein Verdunstungs-Kondensations-Kreislauf entsteht, der zu einer Erhöhung der „Salz“-Konzentration auf der Rohrhaut führt, wenn das Wasser verdunstet. Dieses „Salz“ kann zusammen mit anderen natürlichen Bestandteilen dieser Art von Isoliermaterial den Rohrschutz beeinträchtigen und zu Korrosion und Rissen unter der Isolierung führen, die als Chlorid-Spannungsrisskorrosion (CSCC) bekannt sind.
Unter der Isolierung treten häufig Verunreinigungen auf, insbesondere Chloride und Sulfate. Diese können aus den Isoliermaterialien ausgewaschen werden oder aus externen Quellen stammen. Ihre wässrigen Lösungen, die eine hohe elektrische Leitfähigkeit besitzen, können den Korrosionsprozess begünstigen.
Dabei spielt auch die Temperatur eine ganz entscheidende Rolle. Es ist allgemein anerkannt (oder wird von verschiedenen Quellen angegeben), dass Kohlenstoffstähle, die im Temperaturbereich von –4 °C (25 °F) bis 149 °C (300 °F) betrieben werden, dem höchsten CUI-Risiko ausgesetzt sind. Geräte, die ständig unter –4 °C (25 °F) betrieben werden, neigen nicht zur Korrosion. Geräte, die bei Temperaturen über 149 °C (300 °F) und über dem Siedepunkt von Wasser betrieben werden, weisen eine geringere Korrosion auf, da die Oberfläche des Kohlenstoffstahls weitgehend trocken bleibt.
Das Verständnis der Wechselwirkungen zwischen Isoliermaterialien, Wassereintritt, Verunreinigungen und Temperaturschwankungen ist entscheidend für das Verständnis des Auftretens von CUI. Dieses Verständnis ist jedoch nicht vollständig, ohne die möglichen Folgen dieses Problems zu berücksichtigen. Die Auswirkungen gehen über die Korrosion selbst hinaus und betreffen nicht nur die finanzielle Seite der Öl- und Gasindustrie, sondern auch Gesundheits-, Sicherheits- und Umweltaspekte.
Die Auswirkungen von CUI sind ein Spiegelbild der Auswirkungen von Korrosion im Allgemeinen. Korrosion kann Risse verursachen, die schließlich zu Brüchen und Leckagen in Ölpipelines führen können. Dies stellt nicht nur eine erhebliche Bedrohung für die Umwelt durch potenzielle Verschmutzung dar, sondern auch ein Gesundheitsrisiko für die Menschen, die in der Nähe der Leckage leben. Die Brand- und Explosionsgefahr fügt der ohnehin kritischen Situation eine weitere Gefahr hinzu.
Diese Schäden sind nicht nur gefährlich. Sie sind auch teuer. Die Reparatur dieser Defekte kann sowohl eine finanzielle Belastung in Form von Investitions- und Betriebskosten (CAPEX und OPEX) als auch eine Gefahr für die Techniker darstellen, die die Reparaturen durchführen. In den folgenden Abschnitten werden Strategien zur Vermeidung und Verminderung von CUI untersucht, um diese Risiken wirksam zu kontrollieren.
Die Erkennung von CUI ist eine Herausforderung, da sie unter der Isolierung verborgen ist und oft erst zu spät erkannt wird. Herkömmliche Methoden zur Erkennung von CUI reichen von einfachen bis hin zu hoch entwickelten Techniken, die alle darauf abzielen, Korrosion zu erkennen, bevor sie zu größeren Schäden führt.
Der am weitesten verbreitete und direkteste Ansatz zur Inspektion von CUI besteht darin, Teile aus der Isolierung herauszuschneiden, um zerstörungsfreie Prüfungen oder Sichtprüfungen zu ermöglichen.
Die folgenden Methoden mit ihren jeweiligen Vor- und Nachteilen werden üblicherweise zur Identifizierung von CUI verwendet:
- Sichtprüfung: Die einfachste und erste Methode besteht darin, die Isolierung zu entfernen, den Zustand der Rohroberfläche zu prüfen und die Isolierung wieder anzubringen. Studien zeigen, dass CUI in den meisten Fällen nach dem Entfernen der Isolierung nicht mehr gefunden wird. Eine weitere Herausforderung kann die Gefährdung durch den Umgang mit asbesthaltigen Isoliermaterialien oder durch die Verschlechterung der thermischen Isolierung während des Betriebs der Rohrleitungen sein.
- Inspektion ohne Entfernen der Isolierung: Diese Technik reduziert die Kosten für Inspektionen erheblich, da sie die Notwendigkeit der Entfernung und Wiederherstellung der Isolierung vermeidet. Für diesen Ansatz werden in der Regel zerstörungsfreie Prüfmethoden verwendet.
- Zerstörungsfreie Prüfung (ZfP): Die ZfP umfasst verschiedene nicht-invasive Prüftechniken, die zur Bewertung von Materialeigenschaften, Komponenten oder ganzen Prozesseinheiten eingesetzt werden. Verschiedene Methoden, wie z. B. gepulster Wirbelstrom (Pulsed Eddy Current, PEC) und digitale Radiographie, werden zur Untersuchung auf CUI eingesetzt. In der Regel wird keine Methode isoliert eingesetzt – mehrere Methoden werden kombiniert, um optimale Ergebnisse zu erzielen.
- Gepulster Wirbelstrom (PEC): PEC-Geräte arbeiten mit Elektromagnetismus und bestimmen effektiv die durchschnittliche Wandstärke des Rohrs durch ihre Isolierung. Dies ermöglicht die Identifizierung und Lokalisierung von CUI. Der Hauptvorteil der PEC ist ihre Fähigkeit, eine allgemeine Ausdünnung der Wände in isolierten Objekten zu erkennen, ohne die Isolierung oder die Oberflächenvorbereitung des Objekts zu entfernen.
- Guided Waves (GW): Alternative Technologie zur Bewertung von CUI über lange Rohrlängen. Es verwendet geführte niederfrequente Ultraschallwellen, die sich entlang der Rohrleitung ausbreiten. Sowohl Innen- als auch Außenkorrosion können erkannt werden, aber der Sensor mit der geführten Welle muss in direktem Kontakt mit dem Rohr stehen, sodass die Isolierung entfernt werden muss, um den Sensor zu montieren.
- Digitale Durchstrahlungsprüfung in Echtzeit: Röntgenstrahlen werden von einer Seite des isolierten Rohres ausgesendet, durchdringen das Rohr, die Ummantelung und die Isolierung, und ein Sensor empfängt die Röntgenstrahlen auf der gegenüberliegenden Seite. Die vom Sensor empfangenen Strahlen werden in Echtzeitbilder umgewandelt und zeigen Anomalien wie innere oder äußere Korrosion oder Defekte am Rohr. Diese Methode kann ohne Entfernen der Auskleidung angewendet werden und liefert Echtzeitinformationen.
- Thermografie: Wird in der petrochemischen Industrie verwendet. Es liefert ein Wärmebild eines Objekts und erkennt Energieverluste, die z. B. durch Isolierungsfehler, Wassereintritt, Gas- oder Flüssigkeitslecks verursacht werden, die sich auf die Temperatur des isolierten Rohrs auswirken.
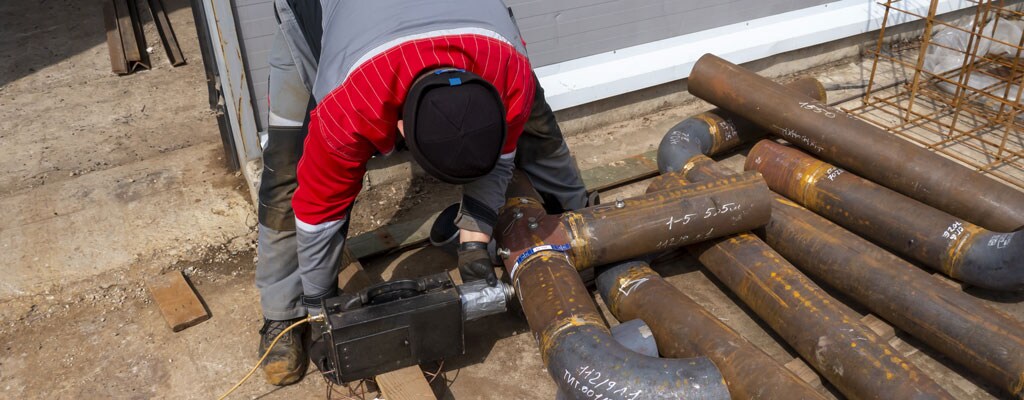
Ein Spezialist, der ein Röntgengerät zur zerstörungsfreien Prüfung von Schweißverbindungen montiert.
Während jede der beschriebenen Methoden ihre eigenen Stärken hat, haben sie alle inhärente Beschränkungen, die sie unwirksam machen können, wenn es darum geht, unter der Isolierung verborgene CUI aufzudecken. Sichtprüfungen sind zwar einfach, zeigen aber nur den Zustand der Oberfläche und übersehen möglicherweise tiefer liegende Korrosion. Das Entfernen und Wiederherstellen der Dämmung während dieser Inspektionen ist ebenfalls mit erheblichen Kosten und logistischen Herausforderungen verbunden, wie z. B. dem Umgang mit Asbest. (Texas Nondestructive Testing Academy & Level III Services, o.J.)
Zerstörungsfreie Prüfmethoden (ZfP), die Materialeigenschaften ohne Beschädigung der Isolierung bewerten, sind durch die Art ihrer Anwendung begrenzt. Beispielsweise liefern gepulste Wirbelstromsysteme (PEC) wertvolle Informationen über die Ausdünnung von Wänden, können aber möglicherweise nicht genau lokalisierte Korrosion oder kleine Hohlräume erkennen. (Texas Nondestructive Testing Academy & Level III Services, o.J.)
Bei der Technologie der geführten Wellen muss die Isolierung an einigen Stellen entfernt werden, was zu Korrosion führen kann, die an anderen Stellen auftritt. Darüber hinaus können Faktoren wie verlustbehaftete Beschichtungen oder Signalreflexionen von Merkmalen wie Schweißnähten und Anschlüssen die Signaldämpfung beeinflussen und die Länge der zu prüfenden Rohre begrenzen. (Chukwuemeka, et al., 2021)
Die digitale Echtzeit-Röntgentechnik ermöglicht die Darstellung potenzieller Anomalien unter der Isolierung, ist aber möglicherweise nicht empfindlich genug, um Korrosion im Frühstadium zu erkennen. Darüber hinaus ist es nur für Materialdichten nützlich und kann Korrosion in bestimmten Rohrwerkstoffen möglicherweise nicht effektiv erkennen. (Nanan, 2020)
Sichtprüfungen und thermografische Untersuchungen sind zwar wirksam bei der Identifizierung potenzieller CUI-Gefahren aufgrund beschädigter Wetterschutzeinrichtungen oder Ummantelungen, liefern jedoch nur eine Oberflächenanalyse und übersehen möglicherweise Korrosion, die tiefer unter der Isolierung verborgen ist. (Fujifilm, 2022)
Im Wesentlichen besteht die größte Herausforderung darin, dass diese Methoden keine vollständige und umfassende Bewertung der versteckten Korrosion ermöglichen, insbesondere wenn diese lokal begrenzt ist oder sich in einem frühen Stadium befindet. Die Grenzen jeder Methode können dazu führen, dass große Bereiche unkontrolliert bleiben, was zu übersehenen CUI führen kann, die sich unter der Isolierung weiterentwickeln.
Sensoren für die CUI-Erkennung
Hervorgegangen aus der digitalen Transformation der Branche, hat die rasche Verbreitung von IoT-Geräten (Internet of Things) und vernetzten Systemen die Voraussetzungen für innovative Technologien zur Erkennung von CUI geschaffen, insbesondere durch drahtlose, batteriebetriebene Sensoren. Die Beschleunigung dieser technologischen Revolution ist vor allem auf das Aufkommen batteriebetriebener drahtloser Sensoren zurückzuführen, die von den Fortschritten in der Niedrigenergieelektronik profitieren, sowie auf die Einführung „batteriefreundlicher“ drahtloser Kommunikationsprotokolle wie LoRaWAN, NB-IoT, LTE M und Bluetooth.
Verschiedene Messprinzipien werden evaluiert, einschließlich Sensoren, die Feuchtigkeit – sowohl Feuchte als auch Temperatur – zwischen Rohr und Außenmantel oder in oder um Isoliermaterialien wie Glasfaser oder EMGR messen. Es gibt jedoch auch Herausforderungen, wie z. B. die Schwierigkeit, bestehende Infrastrukturen mit Glasfaser nachzurüsten oder „Opferdrähte“ (Kabel) in die Isolierung zu integrieren.
Diese „Opferdrähte“ werden in Verbindung mit elektromagnetisch geführtem Radar (EMGR) verwendet, bei dem das Kabel als Vorindikator für CUI korrodiert, während ein nicht korrodierendes Kabel Signale an ein Funkmodul außerhalb des Mantels überträgt. Diese Integration ermöglicht eine nahtlose Verbindung zwischen innovativen Detektionsmethoden und praktischen Einschränkungen bei der Umsetzung und spiegelt die Komplexität wider, die mit der Verschmelzung neuer Technologien mit etablierten Infrastrukturen verbunden ist.
TE Connectivity zeichnet sich bei der Bewältigung dieser Herausforderungen durch sein einzigartiges Sensor-Know-how aus, insbesondere durch seine kapazitive Feuchtesensortechnologie und drahtlose Messumformer. Diese Sensoren, die strategisch an isolierten Rohren angebracht werden, ermöglichen eine effiziente Kartierung ganzer Infrastrukturen. Sie können eindringendes Wasser erkennen und durch intelligente Analyse die Lokalisierung von Bereichen erleichtern, die eine weitere CUI-Untersuchung mit zerstörungsfreien Prüfmethoden (ZfP) erfordern. Weitere Details zur Anwendung dieser Technologie in der Praxis werden im Abschnitt „Fallbeispiel“ erläutert.
Die Zusammenarbeit in der Branche bietet Möglichkeiten für eine verbesserte Echtzeit-Überwachung. Die Effizienz dieser Lösungen wird jedoch in Kombination mit den fortschrittlichen Sensortechnologien von TE Connectivity erheblich gesteigert.
Der konventionelle Ansatz erfordert oft kostspielige und ressourcenintensive Inspektionen. Die Sensoren von TE Connectivity zielen jedoch darauf ab, diesen Prozess effizienter und weniger ressourcenintensiv zu gestalten und damit Zeit und Kosten zu sparen. Mehr als 90 % der Sichtprüfungen, die nach dem Entfernen der Beschichtung durchgeführt werden, zeigen keine Korrosion. Gezielte Inspektionen, die durch unsere fortschrittliche Sensortechnik ermöglicht werden, können so zu erheblichen Kosteneinsparungen führen.
Verschiedene Unternehmen können ihre eigenen risikobasierten Strategien für Inspektionen haben. Bei kritischen Anlagen werden wahrscheinlich weiterhin planmäßige Wartungsarbeiten und NDE-Methoden zum Einsatz kommen, aber bei weniger kritischen Anlagen könnten die Wartungskosten erheblich gesenkt werden, wenn sie mit den drahtlosen Fernsensoren von
TE Connectivity ausgestattet werden.
Ziel ist es, einen robusten, genauen, kostengünstigen und langlebigen Sensor zu entwickeln und einzusetzen, der in der Lage ist, alle isolierten Rohre und Oberflächen in Raffinerien zu überwachen. Die Sensoren von TE Connectivity, die diese Kriterien bereits erfüllen, sind darüber hinaus vollständig ATEX FCE-zertifiziert und bieten einen sicheren Betrieb in potenziell gefährlichen Anwendungsumgebung.
Fortschritte in der Sensortechnologie und ihre Vorteile
Durch den Einsatz von Technologien wie LoRaWAN können Sensordaten aus Entfernungen von wenigen Metern bis zu mehreren Kilometern abgerufen werden. In Kombination mit Gateways, fortschrittlichen Analysen, CUI-zentrierten Managementstrategien und spezialisiertem Korrosions-Know-how können Betreiber und Instandhalter Korrosion proaktiv erkennen. Dies ermöglicht ein schnelles und gezieltes Eingreifen zur Reparatur von Korrosionsstellen, was Zeit und Kosten spart und gleichzeitig die Sicherheit und Langlebigkeit der Infrastruktur gewährleistet.
Die Integration solcher Systeme bietet erhebliche Vorteile für ein proaktives Korrosionsmanagement unter der Isolierung. In den letzten Jahren wurden zahlreiche Simulationen und Laborexperimente mit Feuchtesensoren durchgeführt. Die Ergebnisse sind vielversprechend und zeigen, dass Feuchte- und Temperaturmessungen wirksam sein können, um CUI zu erkennen, bevor sie auftreten. Wir bei TE Connectivity sind stolz auf unser Know-how in der Sensortechnologie, das der Schlüssel zu diesen Fortschritten war. Fortschritte wie diese bleiben jedoch nicht im Labor, sondern finden ihren Weg in die Praxis durch starke strategische Partnerschaften, wie wir im Folgenden näher erläutern werden.
Fallbeispiel: KAEFER
Anerkennung der ernsthaften Sorgen in der Branche
In den vergangenen Jahren hat die KAEFER Group, ein führender Anbieter integrierter industrieller Servicelösungen, weltweit eine Vielzahl von Öl- und Gasunternehmen beraten. Eine Gemeinsamkeit zeigte sich: Alle nannten die Korrosion unter der Isolierung (CUI) als oberste Priorität. Die Bedenken waren nicht nur technischer Natur, sondern hatten, wie in diesem Artikel bereits erwähnt, weitreichende Auswirkungen. Vor diesem Hintergrund entstand die Zusammenarbeit mit KAEFER, um diesen dringenden Bedarf zu decken.
Umfassende Lösungen durch KIT®
Blu Empowered by KAEFER hat KIT® (KAEFER Integrity Technology) als ganzheitlichen End-to-End-Service für das CUI-Management eingeführt. KIT zeigt die Kompetenz von KAEFER im effektiven Management von CUI-Projekten unterschiedlicher Größenordnung. Von der komplexen Optimierung der Sensorplatzierung über die Montage bis hin zur Systemkonfiguration ist KIT ein Komplettpaket. Die Sensortechnologie von TE Connectivity verstärkt diese Fähigkeiten.
Die Synergie zwischen den integrierten Dienstleistungen von KAEFER und den fortschrittlichen Sensorlösungen von TE bildet die Grundlage dieser innovativen Partnerschaft. Die drahtlose Sensortechnologie von TE mit Merkmalen wie einer langen Batterielebensdauer und der Fähigkeit, rauen Umgebungen standzuhalten, stellt einen bedeutenden Fortschritt bei der Erkennung von CUI dar. Diese drahtlosen Sensoren sind nach den höchsten Sicherheitsstandards zertifiziert und ermöglichen die Kommunikation über große Entfernungen mit fortschrittlichen Protokollen wie LoRaWAN™ und sind mit Bluetooth® Low Energy für eine vielseitige Fernkonfiguration ausgestattet.
Darüber hinaus verdeutlicht die Integration von anpassbaren Messzeiten und einem intelligenten Schwellwertmanagement den zukunftsweisenden Ansatz dieser Partnerschaft zur Verbesserung der Zuverlässigkeit und Genauigkeit der Daten bei gleichzeitiger Optimierung der Batterielebensdauer. Mit Sensoren, die in der Lage sind, ihre Messung und Datenübertragung auf der Grundlage konfigurierter Schwellenwerte selbstständig anzupassen, und automatischen Benachrichtigungen für das Batteriemanagement wird die Zusammenarbeit zu einer hohen Effizienz führen.
Die Sensorelemente dieser Technologie sind sorgfältig konstruiert und verwenden oft seit langem bewährte MEMS-Feuchte-Die- und ASIC-Technologien, die in verschiedenen Branchen wie der Automobil-, Offroad- und Lkw-Branche ausgiebig genutzt werden. Diese branchenübergreifende Anwendung unterstreicht das Potenzial für eine groß angelegte Skalierung in Branchen wie der Öl- und Gasindustrie, um die Qualitätsniveaus zu erreichen, die in Branchen wie der Automobilindustrie erforderlich sind, und um als Rückgrat für eine effiziente Datenerfassung und Echtzeitüberwachung zu dienen.
Technische Raffinesse in KIT®
KIT bietet ein vollständig digitalisiertes CUI-Überwachungspaket an. Zwar erfordern die identifizierten Problembereiche nach wie vor herkömmliche Inspektionen, doch besteht das Potenzial, die Tätigkeiten vor Ort zu autonomisieren, menschliche Eingriffe zu reduzieren und damit die Risiken zu verringern. Darüber hinaus wird das System derzeit weiterentwickelt, um verschiedene Funktionen wie einen Beratungsdienst und sogar die Möglichkeit einer robotergestützten, autonomen Montage zu bieten, die durch die batteriebetriebenen, drahtlosen Sensoren von TE unterstützt wird.
Im Bereich der Datenvisualisierung bietet KIT Möglichkeiten, die von modernen Dashboards bis hin zu digitalen Zwillingen reichen. Diese werden durch hochentwickelte Analysen ergänzt, die helfen, Korrosion unter der Isolierung vorherzusagen und Instandhaltungsmaßnahmen zu empfehlen.
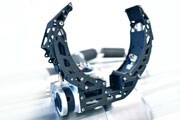
Monkeybot für die Montage von Robotersensoren
Die Integration der Sensortechnologie von TE Connectivity in KIT® bietet nicht nur technologische Raffinesse. Sie bietet handfeste Vorteile. Fallbeispiele haben erhebliche Kosteneinsparungen bei der Instandhaltung und Verbesserungen der Anlagenintegrität gezeigt. All dies führt letztlich zu einem erhöhten Kundennutzen, den sowohl KAEFER als auch TE Connectivity anstreben.
Zusammenfassung
Bei der Bewältigung der weit verbreiteten Herausforderung der Korrosion unter der Isolierung. Dieses Dilemma hat erhebliche Auswirkungen auf die Betriebseffizienz, die Umweltsicherheit und das Wohlergehen der Gemeinschaft, und die Rolle fortschrittlicher Technologien kann nicht hoch genug eingeschätzt werden. Dieses Whitepaper hat die enormen Auswirkungen von Korrosion auf den Öl- und Gassektor aufgezeigt, nicht nur in Bezug auf das finanzielle Endergebnis – Investitions- und Betriebskosten (CAPEX und OPEX) – sondern auch in Bezug auf Gesundheit, Sicherheit und Umwelt (HSE).
Unsere Zusammenarbeit mit KAEFER bildet den Hintergrund und reagiert auf den dringenden Bedarf der Industrie an robusten CUI-Managementlösungen. KIT® by KAEFER, das die innovative Sensortechnologie von TE Connectivity integriert, bietet einen ganzheitlichen End-to-End-Service für das CUI-Management. Diese Zusammenarbeit ist ein Beispiel für einen interdisziplinären Problemlösungsansatz, der unterschiedliche Fachkenntnisse in einem Ökosystem vereint, das sich den komplexen Herausforderungen der Identifizierung und des Managements von CUI widmet. Der breite Einsatz unserer drahtlosen, batteriebetriebenen Sensoren ist mehr als nur eine technologische Errungenschaft. Es bedeutet einen transformativen Einfluss auf die Industrie. Die Möglichkeit, sowohl planmäßige Instandhaltungsarbeiten als auch unnötige Sichtprüfungen zu reduzieren, erhöht die Sicherheit und führt zu erheblichen Kosteneinsparungen.
Die Digitalisierung der Anlagen, einschließlich der Entwicklung „digitaler Zwillinge“, ermöglicht uns einen Sprung nach vorn in Bezug auf Präzision und Vorhersagbarkeit. Unsere Sensoren, die durch robuste Analysewerkzeuge unterstützt werden, fügen sich gut in bestehende Systeme und Standards ein und unterstreichen unser Engagement für Fortschritte bei der Erkennung und Vermeidung von CUI. Es zeigt unser Engagement für die kontinuierliche Weiterentwicklung der Sensortechnologie und die Industriepartnerschaften, die diese Fortschritte ermöglichen.
Mit Blick auf die Zukunft bleibt der Fokus von TE Connectivity klar: Pionierarbeit für sicherere und nachhaltigere Lösungen durch den Einsatz modernster Technologien. Visualisierungstools, die auf unseren drahtlosen intelligenten Sensoren basieren, bieten einen umfassenden Einblick in den Anlagenzustand und ermöglichen einen aufschlussreichen Übergang von einer allgemeinen, risikobasierten Wartung zu einem gezielteren, datengesteuerten Ansatz.

Die drahtlosen Sensoren von TE Connectivity wurden und werden in Zustandsüberwachungsanwendungen eingesetzt, die eine vorausschauende Wartung von rotierenden Anlagen sowie Öl- und Gasbohrlöchern ermöglichen.
Es steht eine umfassende intelligente Plattform zur Verfügung, die ein- und dreiachsige piezoelektrische Vibrationssensoren mit einem Frequenzbereich bis 15 kHz (integrierte FFT und Signalverarbeitung), Temperatursensoren, die an Rohre geklemmt werden können und einer Rohraußentemperatur von bis zu 260 °C standhalten, sowie Drucksensoren, die Absolut- oder Relativdruck messen können, umfasst.
Diese intelligenten Sensoren sind vollständig konfigurierbar über die TE Sensor Toolbox oder über Ihr Smartphone und die TE SensorConnect App, die im Apple App Store oder Google Play Store erhältlich ist. Mit Blick auf die Zukunft sind wir zuversichtlich, dass wir mit unseren führenden CUI-Überwachungslösungen an der Spitze des industriellen Wandels stehen und sowohl die Effizienz als auch die Sicherheit auf ein neues Niveau heben werden.
Durch die Verbindung von Spitzentechnologie mit fundiertem Fachwissen und partnerschaftlicher Zusammenarbeit reagieren wir nicht nur auf die Herausforderungen von heute, sondern gestalten die Lösungen von morgen.
