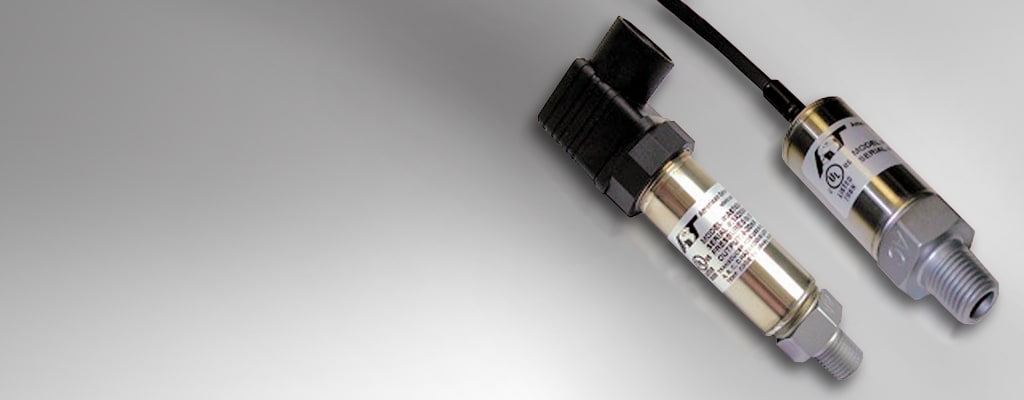
Trend
Druckmessung
Systemintegratoren und OEMs sind ständig bestrebt, die Zuverlässigkeit, Sicherheit und Leistung zu steigern und gleichzeitig Kosten zu senken. Von überragender Bedeutung sind hier die in Verteiler, Rückschlagventile, Aktuatoren und Pumpen eingebettete Sensoren. Autor: Karmjit Sidhu, Senior Director, Sensoren für die Erdöl-, Erdgas- und Offshore-Industrie
Drucksensoren, die in puncto Einsatzhäufigkeit nur von Temperatursensoren übertroffen werden, sind in Hydraulik-, Wasser-, medizinischen und in vielen weiteren Anwen-dungen im Aufschwung, die trotz kleinem Platzangebot Präzision verwirklichen müssen. Die Systemdrücke steigen zugunsten höherer Effizienz – zugleich gilt es aber, kleinere Baumaße zu realisieren. Die durch ein kompaktes System erzielbaren Kosteneinsparungen zwingen Hersteller zu intelligenten Lösungen. Eigenständige Sensoren mit integrierter Elektronik, EMV-Schutz und Temperatur-kompensation eignen sich für Anwendungen, bei denen ausreichend Raum verfügbar ist. Sie sind jedoch nicht für kompakte und Miniatursysteme geeignet.
Eingebettete Sensoren können in Umgebungen mit hoher Temperatur-, Vibrations- und Strahlungsbelastung eingesetzt werden. Dabei wird die Elektronik von der rauen Umgebung isoliert.
Eingebettete Drucksensoren können je nach Preis und Gesamtleistung, die für das System angestrebt werden, mit einem kompensierten oder unkompensierten Ausgang ausgestattet werden. Manche Anwender verwenden Elektronik mit einer Funktion zur Charakterisierung der unkompensierten Sensoren (die Leistungsmerkmale des Sensors werden im Druck- und Temperaturverlauf erlernt), um den Einsatz innerhalb der Anwendung zu optimieren. Bei unkompensierten Sensoren benötigen Anwender Druck- und Temperatureingänge, die die Reaktionsweise des Sensors genau erfassen, bevor die Daten verwendet werden können. Unkompensierte Sensoren sind meist kostengünstiger und bieten eine gewisse Flexibilität, wenn eine Charakterisierung mittels Elektronik möglich ist. Kompensierte Sensoren sind äußerst benutzerfreundlich, da diese ab Werk im Druck- und Temperaturverlauf charakterisiert werden. Für die Bereit-stellung des gewünschten Ausgangs ist ein Verstärkermodul erforderlich. Da der Sensor für eine bestimmte Präzision im Druck- und Temperaturverlauf gemäß den Kundenanforder-ungen ausgelegt ist, sind weniger Tests oder Programmierungen erforderlich.
In den meisten Fällen ist der Einsatz von separater Elek-tronik die beste Option in Verbindung mit eingebetteten Sensoren. Je nach Technik und Medien können eingebettete Sensoren in Umgebungen mit hoher Temperatur-, Vibrations- und Strahlungsbelastung eingesetzt werden. Dabei wird die Elektronik von der rauen Umgebung isoliert. Bei Verwendung niedriger Impedanz (leistungsstarke piezoresistive Silizium-Dehnungsmesstreifen mit weniger als 2 kΩ) kann die Elektronik im Abstand von einem Meter und mehr zum Sensor platziert werden. Das medienberührende Material und die Klemm-konfigurationen für die eingebetteten Sensoren müssen sorgfältig ausgewählt werden, um kostspielige Ausfälle zu vermeiden. Edelstahl 316L eignet sich gut für Wasser-, Sauerstoff- und Wasserstoffanwendungen sowie viele weitere aggressive Medien. Für medizinische und toxische Medien wie Körperflüssigkeiten, Schwefelwasserstoff und Bleichmittel werden Titan- und Nickellegierungen bevorzugt. Abbildung 2 veranschaulicht typische Konfigurationen von eingebetteten Drucksensoren für den Einsatz in hydraulischer und medizinischer OEM-Ausrüstung.
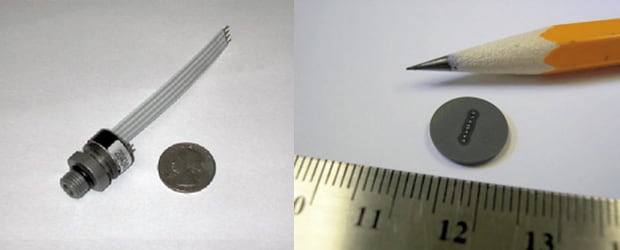
Druckmesstechnik spielt eine entscheidende Rolle bei der Integration eingebetteter Bauelemente. Zuverlässigkeit und Langlebigkeit sind die zwei wichtigsten Faktoren, die die Systemleistung im Verlauf der Zeit bestimmen. Bei anspruchs-vollen Prozessen, z. B. in Medizin-, Halbleiter- und Industrie-anwendungen, bei denen Gase wie Wasserstoff und Sauerstoff verarbeitet werden, dürfen auf keinen Fall Verunreinigungen durch den Drucksensor in den Prozess gelangen. Abbildung 3 veranschaulicht zwei Arten von Sensortechnik, die häufig für das Einbetten verwendet werden. Mit jeder Technik wird der Druck in spezieller Weise und mit unterschiedlichen Fähig-keiten zur Kontrolle des Drucks gemessen. Der wesentliche Unterschied liegt in der Wahrscheinlichkeit für Verunrei-nigungen innerhalb des Prozesses.
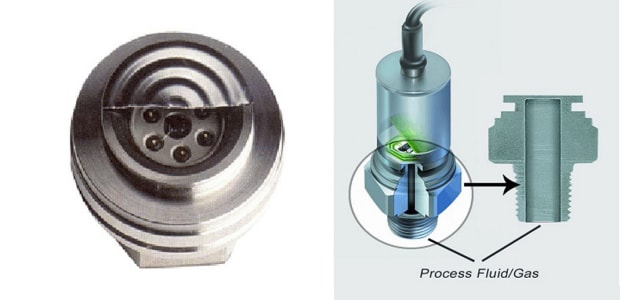
Durch den Einsatz von Ventilen und Aktuatoren in anspruchsvollen Anwendungen, z. B. in den Bereichen Kerntechnik, Hydraulik und Automatisierung, gewinnen eingebettete Positionssensoren für die Positionsrück-meldung immer mehr an Bedeutung. Die lineare Weg-messung kann auf einer Strecke von wenigen Millimetern bis zu mehreren Metern erfolgen. Die Messung des Ventilsitzes wird aufgrund der Sicherheit in der Kernkraft- und Hydraulik-industrie zu einem Schlüsselbereich. Ähnlich wie bei der Druckmesstechnik ist die Auswahl der geeigneten Positions-sensortechnik entscheidend für die Leistung und Zuver-lässigkeit des Systems. Seit Jahren basieren Positionssensoren auf entweder berührender oder berührungsloser Messtechnik. Bei berührender Messtechnik wie dem linearen Potenziometer ist ein Schieber an ein bewegliches Element angebracht, das mit der resistiven Vorrichtung in direktem Kontakt steht. Das Potenziometer fungiert als Spannungsteiler und bietet einen Ausgang, der mit der Bewegung des Schiebers von einem Ende der Vorrichtung zum anderen 0 bis 100 % der angelegten Spannung annehmen kann. Diese Sensoren sind zwar meistens kostengünstiger, aber nicht für Umgebungen mit starker Vibration geeignet. Außerdem müssen sie vor Staub und Flüssigkeiten geschützt werden. Kontaktfreie Techniken wie Optik, variable Reluktanz, Wirbelstrom, magnetostriktive Messverfahren und lineare Differentialtransformatoren (LVDT) wurden erfolgreich eingesetzt. Im Vergleich zu Potenziometern sind diese Messelemente deutlich leistungsstärker und zuverlässiger. Optische Sensoren, die auf Laserinterfero-metern, Wellenlänge und Intensitätsmodulation basieren, werden nur unter laborartigen Bedingungen eingesetzt und sind für aggressive Medien geeignet. Sensoren mit variabler Reluktanz sind eine ausgezeichnete Wahl für ein breites Spektrum an Medien und Temperaturen. Sie sind jedoch hochgradig nicht-linear und können nur über einen kurzen Abtastbereich betrieben werden. Wirbelstromvorrichtungen werden meist bei höheren Frequenzen betrieben, wobei die Elektronik zur Signalverarbeitung in unmittelbarer Nähe zum Sensor platziert werden muss. Dadurch wird der Temperatur- und Strahlungsbereich, in dem die Vorrichtung betrieben werden kann, eingeschränkt. Magnetostriktive Sensoren bieten zwar eine ausgezeichnete Leistung, sind jedoch ebenfalls hinsichtlich der Betriebstemperatur eingeschränkt, da sich die Elektronik zur Signalverarbeitung in unmittelbarer Nähe befinden muss.
Seit Jahren werden LVDTs in Militär- und Zivilflugzeugan-wendungen eingesetzt, z. B. für Landeklappen, Kraftstoff-pumpen und Fahrwerke, bei denen Zuverlässigkeit entscheidend ist. Diese Messelemente verwenden nieder-frequente Magnetkreise (3 bis 5 kHz) und generieren im Gegensatz zu den Wirbelstrom- und sonstigen mit Hochfrequenz betriebenen linearen Sensoren kein Hoch-frequenzrauschen. Dank des niederfrequenten Betriebs können diese Sensoren im Abstand von einem Meter und mehr zur Elektronik platziert werden. Da der LVDT eine magnetische Kopplung von der primären zur sekundären Spule ohne physische Verbindung nutzt, kann diese Art von Sensor hermetisch gegen Wasser, Staub und Eis abgedichtet werden. Dank moderner ASIC-basierter Elektronik (Application Specific Integrated Circuit) kann die Länge des Sensors deutlich reduziert werden – ohne Leistungseinbußen. ASIC ermöglicht eine digitale Signalverarbeitung bei vollständiger Kompen-sation über einen großen Temperaturbereich hinweg. Diese Technik hat den Markt für lineare berührungslose Sensoren geöffnet, die in Anwendungen mit engen Platzverhältnissen eingesetzt werden, z. B. für Ventilsitz oder Unterwasserspulen zur Zylinderabtastung. Abbildung 4 zeigt zwei berührungslose Positionssensoren, die in Ventile und Getriebe eingebettet werden können.
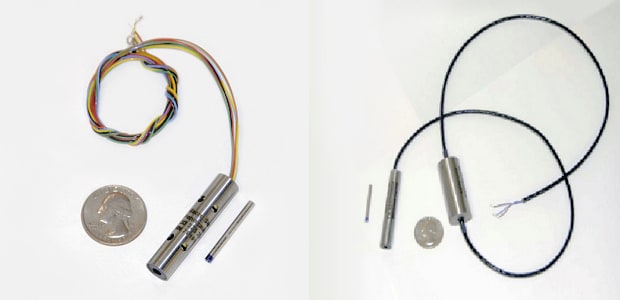