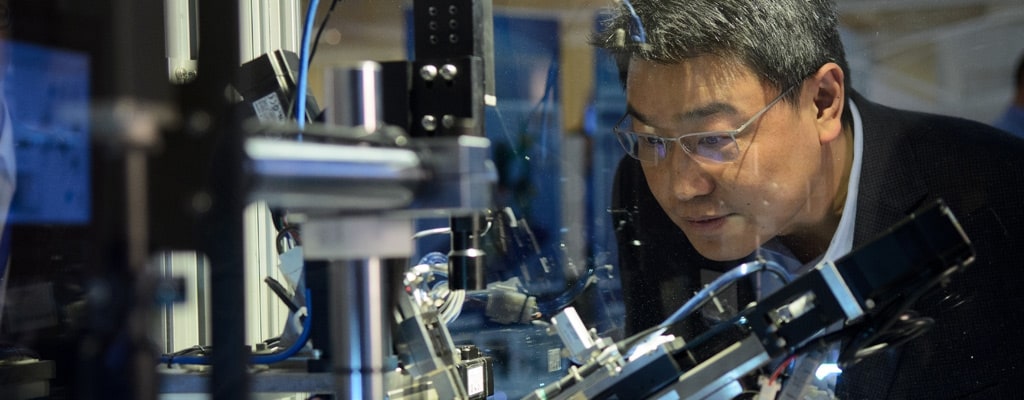
Innovationsprozesse beschleunigen
Auf dem heutigen Technologiemarkt kann nur erfolgreich sein, wer eine optimale Lösung entwickelt, die Kunden zufriedenstellt und eine kurze Markteinführungszeit hat. Der effizienteste Weg ist der 3D-Druck - Ideen können schnell in vollständig funktionsfähige Prototypen verwandelt werden.
Autoren:
Gregory T. Pawlikowski, Principal Development Engineer, Harrisburg Research Center
Jessica H. B. Hemond, Principal Development Engineer, Harrisburg Research Center
Ranjan D. Deshmukh, Staff Scientist, Harrisburg Research Center
Die Fertigung funktionsfähiger Prototypen beginnt mit der Verwendung von technischen Harzen, die über die erforderlichen Eigenschaften und Nennwerte verfügen, sowie mit Herstellungsprozessen, die denen der Endproduktfertigung ähneln. Die heutigen 3D-Drucktechnologien verfügen meist nicht über die Materialoptionen und die erforderliche physische Leistungsfähigkeit. Dadurch wird die Fähigkeit von Herstellern, funktionelle Kunststoffteile direkt zu drucken, eingeschränkt. Trotzdem können Hersteller den 3D-Druck zur schnellen Fertigung von Formen nutzen, um funktionsfähige Prototypteile mit den gleichen Materialien und Prozessen wie bei Produktionsteilen anzufertigen. Hersteller haben dadurch vier Vorteile, die ihnen erlauben:
- die Prüfung zur Designverifizierung abzuschließen
- Teile auf Produktionswürdigkeit zu prüfen
- Teile für Kundenbewertungen zur Verfügung zu stellen
- den Produktentwicklungsprozess zu beschleunigen
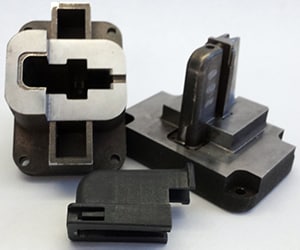
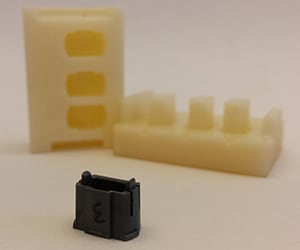
DIE ALTERNATIVE: SPRITZGUSS AUS DEM 3D-DRUCKER
Spritzgussformen werden normalerweise aus mehreren Teilen gefertigt. Zur Fertigung und Montage der Werkzeuge sind extrem präzise Maschinentechniken erforderlich. Um die Kosten zu rechtfertigen, sind in der Regel große Produktionsmengen erforderlich. Dieser Prozess ist für kleinere Mengen untauglich, besonders wenn sich das Design ändert.
Schnelle subtraktive Verfahren ermöglichen Herstellern die Fertigung vereinfachter Formen. Sie nutzen automatisierte Fräsmaschinen mit computergestützter numerischer Steuerung (CNC), die oftmals eine begrenzte Reichweite haben, besonders bei tiefen Kontaktkammern oder geometrischen Einschränken, wie Inneneckenradien. Dadurch können subtraktive Verfahren auch zu langen Fertigungszeiten und schlussendlich überhöhten Kosten führen.
Erfreulicherweise gibt es eine Alternative: Spritzguss aus dem 3D-Drucker. Dadurch werden Formen gefertigt, die in traditionellen Formmaschinen genutzt werden können und mit Produktionsharzen kompatibel sind. Dieser Ansatz wurde für verschiedene 3D-Drucktechniken entwickelt, sodass die Spritzgusstechnik auf Metall- und Kunststoffmaterialien ausgeweitet werden kann. Maschinell gefertigte Metallwerkzeuge haben den Vorteil, über filigrane Eigenschaften mit hoher Haltbarkeit zu verfügen. 3D-Druck bietet ergänzend eine ausreichende Auflösung, Thermostabilität und Materialstärke, um Schrumpfschlauch-Formteile schnell und in kleinen Mengen fertigen zu können.
Es gibt beispielsweise zahlreiche Anwendungen, in denen Teile benötigt werden, die auch rauen Umgebungen standhalten. Die Fertigung dieser Teile erfordert die Verwendung temperaturbeständiger technischer Harze sowie die Berücksichtigung von Eigenschaften wie filigraner Beschaffenheit, dünnen Wänden und hoher Komplexität in Kombination mit engen Toleranzen. Die erfolgreiche Formung exakter Teile mit Spritzguss aus dem 3D-Drucker birgt mehrere Herausforderungen. Unser Team bei TE hat mehrere dieser Probleme identifiziert und gelöst, darunter:
- Druckauflösung und -genauigkeit
- Sekundäre Endbearbeitung gedruckter Werkzeugformen
- Strapazierfähiger Formeinsatz
- Art des technischen Harzes und Verarbeitungsbedingungen
- Nachbearbeitung des Schrumpfschlauch-Formteils
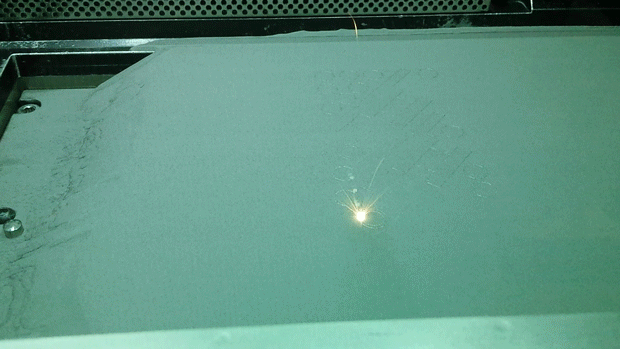
AUSWAHL DES RICHTIGEN DRUCKERS UND DER PASSENDEN MATERIALIEN
Um dieser Herausforderungen anzugehen, müssen wir mit der Auswahl des richtigen 3D-Druckers und der passenden Formmaterialien beginnen. Die Auflösung und die Genauigkeit gedruckter Formen sind begrenzt und können sich je nach Drucker und Formmaterial unterscheiden. Unserer Erfahrung nach bieten Stereolithografie (SLA)-Drucker, die Flüssigharze mithilfe eines Lasers aushärten, sowohl einen hohen Genauigkeitsgrad (~ 0,02 bis 0,05 mm) als auch die beste Auflösung (bis zu 0,125 mm) bieten. Dadurch können auch Werkzeuge mit detaillierten, scharfen Eigenschaften und Ecken angefertigt werden.
Zu weiteren wichtigen Technologien gehören die digitale Lichtverarbeitung (DLP), die eine Lichtprojektionstechnologie nutzt, sowie Monomer-Strahldrucker, die abgegebene Photopolymer-Harze mit Breitband-UV-Licht aushärten können. 3D-Drucktechnologien mit Pulverbett, z. B. direktes Metall-Lasersintern (DMLS), können zwar sehr detailgetreu und hochauflösend sein, führen aber zu rauen Oberflächen.
Eine wichtige Überlegung ist die sekundäre Endbearbeitung der gedruckten Formen und Formeinsätze, da sie sich auf die gesamten Prozesskosten und die Bearbeitungszeit auswirken kann. Eine raue Oberfläche verringert nicht nur die Oberflächenqualität der Warmschrumpf-Formteile, sie kann auch das Herauslösen von Teilen aus der Form erschweren. Aushärtungstechnologien für Photopolymere (z. B. SLA und Monomerspritzen) führen zu relativ glatten Oberflächen, die wenig bis gar keine Nachbearbeitung benötigen.
Wegen der rauen Oberfläche von DMLS-gedruckten Metallwerkzeugen ist oftmals eine sekundäre maschinelle Bearbeitung erforderlich. Wenn eine raue Oberfläche jedoch tolerierbar ist, sind in einigen Fällen Prozesse wie Perlenstrahlung und eine Nachbearbeitung per Hand ausreichend. Beim schichtweisen Druck (z. B. mit einer Schichtdicke von 0,5 mm bei SLA) lassen sich in manchen Fällen raue Oberflächen oder Stufeneffekte (bei angewinkelten Oberflächen) nicht vermeiden, selbst beim Einsatz von Polymeren.
3D-Drucktechnologien, einschließlich direkten Metall-Lasersinterns (DMLS), sind bei TE für ein Rapid Tooling mit hoher Präzision und Auflösung von großer Bedeutung.
Während die raue Oberfläche das größte Problem bei DMLS-gedruckten Metallformen darstellt, besteht die primäre Herausforderung bei Polymerformen in der Haltbarkeit. Der Grund dafür liegt in der geringeren Stärke von Polymeren im Vergleich zu Metallen, besonders wenn verschiedene thermische und mechanische Eigenschaften bei erhöhten Formtemperaturen und Druckwerten zum Tragen kommen. Die mechanischen und thermischen Eigenschaften der Polymer-Werkzeugbereitstellung bestimmt letztendlich die Anzahl der erfolgreich gefertigten Schrumpfschlauch-Formteile oder die Anzahl der Spritzvorgänge.
Diese Merkmale beeinflussen diese wichtigen Eigenschaften unmittelbar (besonders bei kleinen Modellen oder Adern mit hohem Seitenverhältnis) und können zu frühzeitigem Springen oder Verformungen führen. Solche Sprünge und Verformungen werden hauptsächlich durch Faktoren wie die Stärke des Formmaterials bei höheren Temperaturen, die Abtragung des Formmaterials bei Kontakt mit heißen Polymeren, den Wärmeausdehnungskoeffizienten bzw. die thermische Leitfähigkeit und thermischen Schock herbeigeführt.
Unser Team hat die Elemente identifiziert, die bei der Auswahl des richtigen Druckers und des angemessenen Formmaterials berücksichtigt werden sollten:
- Teilegeometrie, kleinste Eigenschaften
- Produktionsmaterialien, die geformt werden sollen
- Anzahl der benötigten Teile
Es gibt noch weitere Faktoren, die den Erfolg beeinflussen: Für den Formfertigungsprozess ist es wichtig, angemessene Bedingungen sicherzustellen und die abgeänderten Konstruktionsregeln für Polymerformen zu bestimmen.
Die Haltbarkeit und dementsprechend auch die Leistung der Polymerformen werden maßgeblich von dem für das Warmschrumpf-Formteil genutzten technischen Harz, der Art der Fülleinlage (z. B. rauen Glasfasern, die zu hohem Verschleiß führen, im Gegensatz zu Harzen ohne Füllung), der Schmelzviskosität sowie den Verarbeitungsparametern bestimmt. Dadurch sind möglicherweise Anpassungen am Druckvorgang, am Modell oder an beidem erforderlich, damit präzise Abmessungen gewährleistet werden.
Durch die Verwendung eines gedruckten Metallwerkzeugs können Hersteller Standardwerte der Polymerverarbeitung und der Schrumpfung anwenden. Damit dies auch für Polymerformen funktioniert, müssen Hersteller möglicherweise Prozess- und Konstruktionsanpassungen vornehmen. Ein umfassendes Verständnis des Prozesses und der Konstruktion wird Ihnen dabei helfen, das beste Ergebnis zu erzielen.
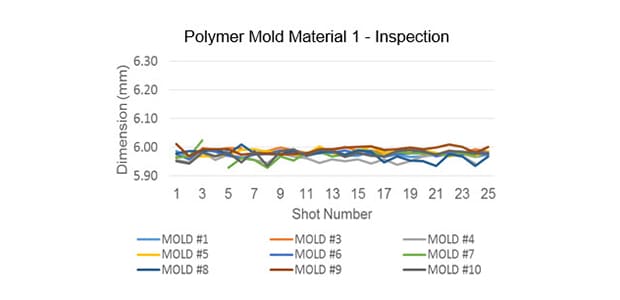
Nicht alle Polymerformen sind gleichermaßen leistungsfähig. Für eine erfolgreiche Umsetzung ist das richtige Formmaterial von großer Bedeutung.
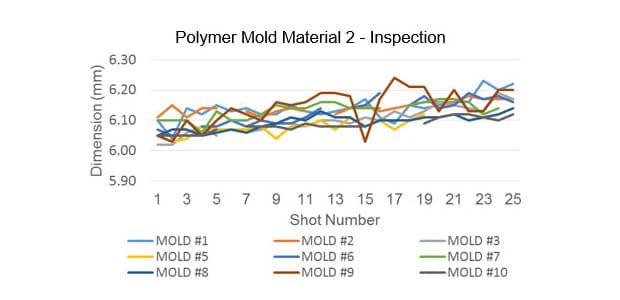
Bei TE entwickeln und verbessern wir fortwährend unsere Prozesse zur Herstellung von Polymerformen, um diese für unser gesamtes Produktportfolio einzusetzen. Dies umfasst die meisten Materialien der Harzpyramide und bestehende Formmaschinen. Durch die Nutzung einzigartiger Konstruktions- und Prozessfortschritte können wir traditionelle Einschränkungen bei der Bereitstellung gedruckter Werkzeuge umgehen. Mit den richtigen Prozessen können wir filigrane Eigenschaften nicht nur drucken, sondern auch in den Schrumpfschlauch-Formteilen reproduzieren. Dies umfasst die Ausformung mit Hochtemperaturmaterialien, z. B. flüssigkristalline Polymere (LCPs) bei gedruckten Polymerformen. Alle möglicherweise notwendigen Kompromisse hängen von der verwendeten Technologie ab.
Bedenken Sie, dass sich die Leistungsfähigkeiten der verschiedenen Polymer-Formmaterialien stark voneinander unterscheiden. Beim Vergleich verschiedener Polymer-Formmaterialien verfügen einige über deutliche Vorteile hinsichtlich Haltbarkeit und Verschleiß bei einer Nutzung über mehrere Formungszyklen hinweg. Auch die notwendigen Konstruktionsanpassungen verfügen, je nach dem Polymer-Formmaterial, über einen gewissen Spielraum, damit die Form die nominalen Abmessungen erreicht und innerhalb der Toleranz liegt.
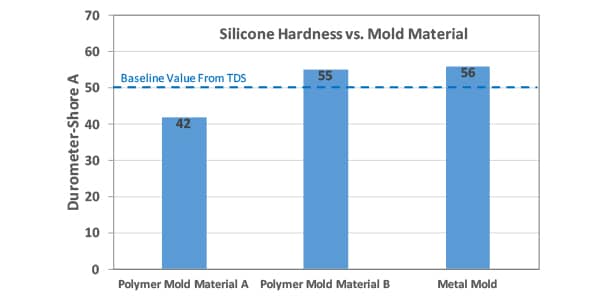
Diese Technologie ist nicht auf thermoplastische Harze beschränkt. Wir nutzen sie auch zur Formung von technischen Harzen mit thermischen Parametern, z. B. Silikonen, Fluorsilikonen und anderen Elastomeren. In Anbetracht der Kosten und der Komplexität herkömmlicher Silikonformen hat ein günstigerer und schnellerer Ansatz klare Vorteile. Ähnlich wie bei der Fertigung von Polymerformen aus thermoplastischen Harzen müssen Hersteller dabei die Konstruktion und die Prozesse anpassen. Auch wenn die Auswahl des passenden Formmaterials wichtig ist, besteht das Ziel dennoch in der Herstellung eines Werkzeugs, das die Leistungsfähigkeit einer herkömmlichen Form bietet.
Die Verarbeitungszeit, die oftmals kürzer ist als bei herkömmlichen Bearbeitungsverfahren, ist einer der Vorteile. Durch den Druckprozess können nicht nur schnell Ergebnisse erzielt werden (in manchen Fällen sogar bereits nach wenigen Stunden), sondern er kann gedruckte Werkzeugformen herstellen, die wenig bis keine sekundäre Endbearbeitung erfordern. Um Kosten und Produktionszeiten zu verringern, können Hersteller Strategien entwickeln, mit denen gedruckte Formen so klein wie möglich gestaltet werden können.
Polymerformen aus dem 3D-Drucker eignen sich oftmals nur für die Herstellung einer beschränkten Anzahl an Schrumpfschlauch-Formteilen. Die neue Technologie nutzt weitere gedruckte Formen, um die Gesamtanzahl zu erhöhen. Nach Bedarf können Hersteller Metallformen aus dem 3D-Drucker zur Fertigung weiterer Warmschrumpf-Formteile unter Produktionsverarbeitungsbedingungen verwenden.
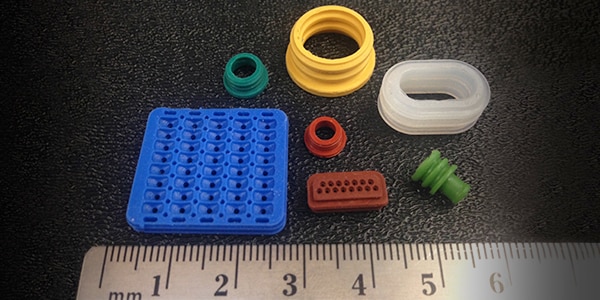
UNSER ENGAGEMENT FÜR INNOVATION
Bei TE können wir diese Technologie auf die meisten der von uns genutzten Produktionsharze anwenden. Aber es müssen immer noch einige Hindernisse überwunden werden. Heute arbeiten wir an der Verbesserung der Haltbarkeit filigranerer Eigenschaften und passen den Prozess an, um größere Anzahlen produzieren und diese in unsere Energie- und Transportportfolios aufnehmen zu können. Derzeit arbeiten wir mit Technologien, die uns erlauben, enge Toleranzen und Feinmerkmale (< 0,4 mm) einzuhalten.
Gleichzeitig passen wir die Konstruktion und Verarbeitung bei der Herstellung von Teilen mit einer Größe von über 12 cm an. Durch die Verfeinerung der Bauweise der Form und unserer Prozessparameter werden wir diese Technologie zukünftig für unser gesamtes Portfolio einsetzen können.
Bislang gibt es keine 3D-Drucklösung, die sich für die Herstellung aller verschiedenen Produktgeometrien und -mengen eignet. Zum 3D-Druck nutzen wir bei uns vor Ort verschiedene Drucktechnologien. Die Bandbreite unserer 3D-Drucktechnologien ist das Ergebnis unseres anhaltenden, langfristigen Engagements seit den späten 80er Jahren: Wir investieren in Technologien, die unser Potenzial und unser Know-how im Bereich der Werkzeugausstattung und Formgebung voranbringen und uns ermöglichen, neue Lösungen für geringere Stückzahlen funktionsfähiger Prototypen zu entwickeln und zu testen. Wir nutzen diese Technologien tagtäglich, um unser internes Know-how zu erweitern und weltweit mit Technikern zusammenzuarbeiten, denen es darum geht, Innovationsprozesse zu beschleunigen und die Rapid Tooling-Technologie zu übernehmen.