Moldagem rápida de vedações elastoméricas funcionais para ambientes severos
RESUMO
Um processo rápido e de baixo custo para fazer protótipos funcionais ou vedações elastoméricas de alta mistura e baixo volume (HMLV) é demonstrado usando moldes de plástico ou polímero impressos em 3D. Demonstramos que este processo simples e versátil é capaz de moldar diferentes silicones e fluorossilicones de nível de produção da TE, produzindo uma variedade de projetos de vedação funcional complexos com detalhes finos e precisão que atendem aos requisitos de nossos clientes.
DECLARAÇÃO DO PROBLEMA
As vedações elastoméricas são componentes essenciais que protegem os contatos elétricos em conectores, sensores e conjuntos de cabos contra a corrosão devida a fatores ambientais adversos como umidade, gases, poeira, fluidos e outros produtos químicos. A TE oferece um grande portfólio de desenhos de vedações, incluindo vedações faciais, vedações familiares, vedações de cabo, vedações periféricas e O-rings. As vedações precisam atender às necessidades dos clientes quanto a diferentes conectores e componentes elétricos.
O objetivo do nosso trabalho foi desenvolver um processo versátil, rápido e de baixo custo que pudesse produzir protótipos funcionais e/ou vedações HMLV vendáveis que fossem feitas de materiais de nível de produção variando de borracha de silicone líquido (LSR) a borracha de alta consistência (HCR) ou fluorossilicones de pasta de goma (consistência de argila ou material semelhante a massa de vidraceiro) a borrachas e outras classes de elastômeros. Além disso, as vedações rápidas devem ser qualificadas para os três critérios principais de forma, ajuste e função (ou seja, capazes de atender aos requisitos de teste dimensional, de montagem e funcional). Um processo rápido fornece aos engenheiros da TE a capacidade de qualificar rapidamente as vedações, comparando diferentes versões de um projeto de vedação em diferentes materiais com propriedades variadas (por exemplo, dureza, conjunto de compressão, força de ruptura, resistência química). Os engenheiros da TE agora não só serão capazes de fornecer peças rapidamente para os clientes finais, mas também obterão feedback mais rápido dos testes do produto.
Aqui demonstramos o uso de moldes de polímeros impressos em 3D para moldagem de vedações elastoméricas que podem alcançar os critérios acima mencionados. A vantagem desse processo está em sua simplicidade e adaptabilidade para trabalhar com estoques líquidos e de goma. Foi avaliada uma variedade de tecnologias de impressão baseadas em fotopolimerização, como a estereolitografia (SLA), o jateamento de monômero e o processamento de luz digital (DLP), bem como diferentes materiais de molde, e combinações de impressora/material apropriadas foram identificadas para imprimir moldes de polímeros capazes de suportar as condições de moldagem típicas (por exemplo, alta temperatura e pressão). Fora da TE, os fornecedores continuam a desenvolver novos materiais de molde de polímero voltados para a moldagem por injeção de termoplásticos [1].
Comparamos também o desempenho funcional das vedações feitas de moldes de polímero impresso com relação a moldes de metal, e a economia geral de tempo/custo do processo associada à prototipagem usando moldes de polímero. Além disso, destacamos a importância de escolher o material correto para o molde de polímero e as condições de processamento do molde, as capacidades e limitações dos moldes de polímero.
MÉTODOS E RESULTADOS
Impressoras e materiais
As impressoras primárias usadas neste estudo foram impressoras comerciais SLA, DLP e jato de monômero, e vários materiais de resina comercial para moldes de impressão. Aspectos como diferenças na qualidade/precisão da impressão, rugosidade da superfície do molde e reutilização do molde serão descritos na seção de discussão.
Nosso processo é capaz de moldar graus comerciais de materiais de silicone e fluorossilicone, como borrachas de alta consistência (HCR) (também conhecidas como goma ou silicones sólidos) e silicones líquidos (por exemplo, 2 partes). As temperaturas de cura desses graus notas geralmente são >150 ºC. Os graus usados neste estudo variam de dureza 20 a 70 shore (por exemplo, shore A 20 ou shore A 50) e são adequados para exposição ambiental adversa.
Descrição do processo
Preparação de moldes de polímeros: moldes de várias cavidades foram projetados usando modelos de vedações. Modelos de moldes em CAD 3D (formato .stl) foram usados para criar arquivos de fatias ou de camadas para impressão 3D. Após a impressão 3D, os moldes (Figura 1a) foram limpos em solventes orgânicos para remover qualquer excesso de resina na superfície do molde, seguido por desgaseificação/tratamento UV e, em seguida, tratamento térmico a uma temperatura adequada para garantir que os moldes impressos fossem completamente curados. Descobrimos que é crucial curar os materiais do molde de polímero a uma temperatura apropriada; caso contrário, o silicone pode não curar completamente no molde de polímero, permanecendo pegajoso ao toque.
Moldes metálicos: moldes de aço de 4 cavidades foram preparados por usinagem convencional. Os moldes de aço foram limpos usando um solvente desengordurante e, em seguida, usados para moldagem de silicone.
Processo de moldagem: os moldes de polímero impressos em 3D foram pulverizados com um desmoldante à base de silicone antes da moldagem. Ampliamos o uso de moldes impressos em 3D para vários processos de moldagem, como injeção, transferência e moldagem por compressão. Desenvolvemos experiência em projetos de moldes de polímeros, ajuste do processo de moldagem e uso de abordagens não convencionais, dada a vida útil limitada da ferramenta devido à menor resistência/condutividade térmica do material do molde de polímeros. Normalmente, a moldagem com ferramenta de polímero exigiria um tempo de ciclo mais alto, o que é aceitável para fins de prototipagem. É fundamental escolher um material de molde apropriado, pois os moldes de polímero foram submetidos a 180 ºC em nosso processo de cura dos silicones.
Após a desmoldagem, as vedações foram rebarbadas manualmente e depois pós-curadas por mais 10 a 120 min a 180 ºC para garantir a cura completa. Dependendo da durabilidade das características principais, os moldes podem ser descartáveis ou reutilizáveis. Para comparação, as vedações também foram feitas a partir de moldes metálicos usinados utilizando um processo de moldagem padrão.
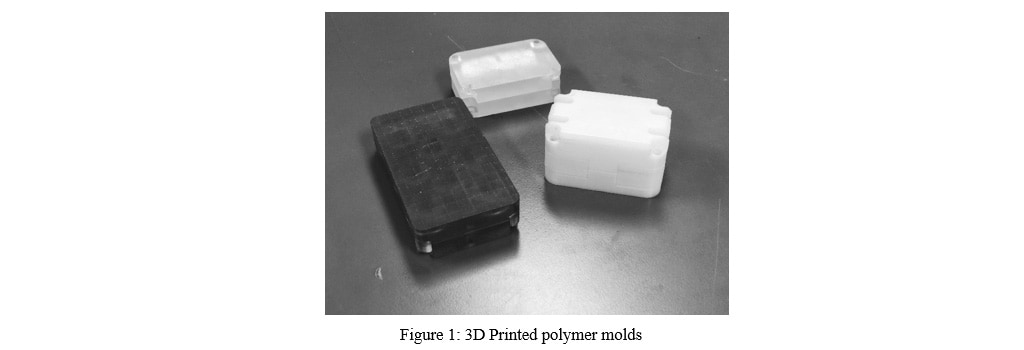
A Figura 2a-g mostra exemplos de vedações moldadas produzidas usando diferentes materiais de molde de polímero impresso em uma variedade de formas, tamanhos, complexidade e tipos de material de silicone. Usando moldes de polímero de alta resolução, conseguimos moldar pequenos anéis de vedação (Figura 2b-c) com um perfil de furo complexo (diâmetro do furo de 1,01 mm, diâmetro mínimo no perfil do furo de 0,53 mm, espessura da parede entre dois furos de apenas 0,25 mm). A Figura 2e-f mostra um exemplo de projeto de vedação automotiva com pequenos recursos (menor espessura de parede de 0,35 mm e pequenos furos com 0,69 mm de diâmetro) que foram moldados com êxito. A Figura 2g mostra exemplos de vedações automotivas de fio único, periféricos e anéis isolantes.
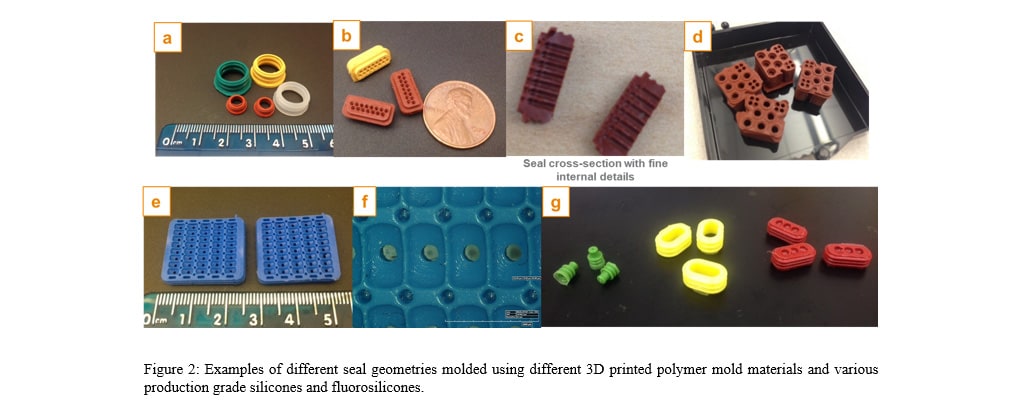
Resultados de testes funcionais de vedações
As vedações funcionais (Figura 2a) para um cliente aeroespacial, preparados utilizando a) moldes de polímero impressos em 3D, e b) moldes de aço, foram montadas em terminais de alumínio, seguidos de inserção de fio e crimpagem (ver Figura 3). Todas as vedações passaram pelo conjunto e os requisitos dimensionais (os diâmetros da gaxeta de vedação estavam dentro da tolerância permitida de 0,1 mm). Os terminais montados foram pressurizados na extremidade do fio e testados para vazamento de ar sob a água em 1 bar e 2 bars. O teste de vazamento foi feito antes e depois de as peças serem submetidas a a) 10 ciclos de choque térmico (-65 ºC a 180 ºC) e b) condicionamento de temperatura (180 ºC por 5 dias). Os requisitos para a qualificação do projeto da vedação do cliente eram passar por todos os testes em 1 bar sem vazamento.
Protótipos de vedações foram feitos para vários tamanhos de fios e diferentes materiais de silicone e fluorossilicone foram examinados por testes de vazamento. Um grau adequado de material de silicone HCR foi selecionado com base em um desempenho de teste de vazamento aceitável. As vedações de moldes de polímeros para todos os tamanhos de fio passaram no teste de vazamento antes e depois do condicionamento de choque térmico, o que é um resultado muito encorajador. Além disso, todas as vedações de molde de polímero para fios maiores (AWG 000, 00, 0A, 1, 2, 3) passaram no teste de vazamento após o condicionamento de temperatura de cinco dias a 180 ºC. O processo de prototipagem usando molde de polímero também nos permitiu qualificar rapidamente vedações AWG 8 menores com um design modificado (parede mais grossa, de 1,99 mm) que passou por todos os testes de vazamento. Nossos resultados mostram que os protótipos de vedações de moldes de polímero são capazes de passar os requisitos funcionais semelhantes aos moldes metálicos.
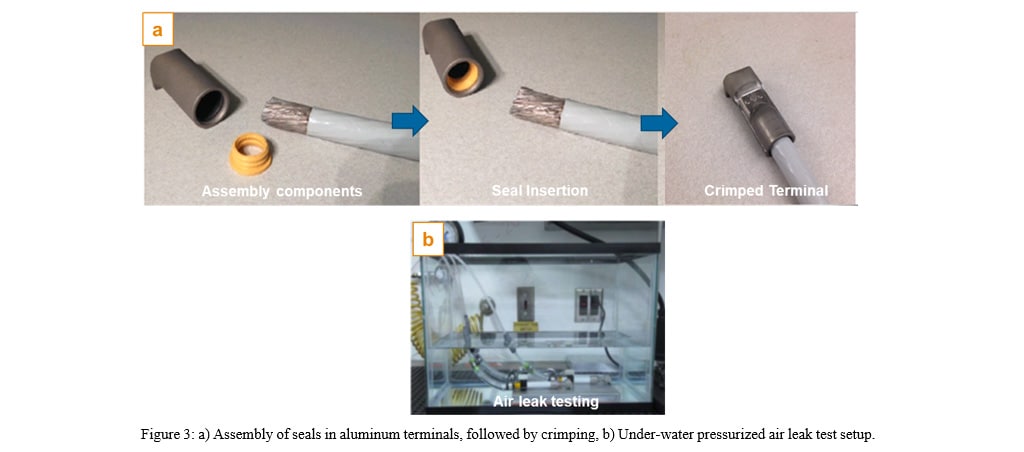
DISCUSSÃO E PONTOS-CHAVE
Recursos e limitações do molde de polímero impresso em 3D
O processo de moldagem usando moldes de polímeros impressos em 3D de várias cavidades pode produzir desenhos de vedações intrincados e complexos aplicáveis a um grande portfólio de vedações da TE. O número de cavidades por molde de polímero pode variar de 1 para vedações de maior porte a >35, para vedações de tamanho menor. As impressoras SLA normalmente usam laser, fornecendo a mais alta precisão e a melhor resolução de recursos (observe que a SLA também pode imprimir recursos ou cantos nítidos), seguidos de perto por impressoras DLP que usam tecnologia de projeção de luz seguidas por impressoras de jato de monômero que curam fotopolímeros usando luz UV de banda larga (observe que os cantos afiados são impressos arredondados). A cura excessiva da resina perto das bordas características devido à penetração da luz mais profunda do que o desejado pode afetar a resolução e a precisão da impressora.
A rugosidade superficial dos moldes impressos varia de acordo com a impressora e o material que está sendo impresso. A rugosidade da superfície é inerente à impressão camada por camada (por exemplo, espessura da camada de 0,05 mm para SLA) e ao efeito de degrau de escada (superfícies construídas em um ângulo) que podem ser claramente vistas na imagem microscópica de um detalhe de molde SLA (Figura 4a). A topografia superficial da superfície do molde do polímero é claramente replicada nas vedações moldadas (Figura 4b). A rugosidade da superfície da vedação moldada de um molde de polímero é maior do que a das vedações dos moldes metálicos (Figura 4c). Podem estar presentes rugosidades adicionais em áreas onde o material de suporte é removido da superfície do molde. A rugosidade adicional da superfície pode não ser aceitável para algumas aplicações de vedação. Observe que também é possível usar ferramentas híbridas, nas quais moldes de polímeros impressos são combinados com inserções de pinos de núcleo metálico para aplicações que exijam superfícies de vedação com rugosidade de superfície extremamente baixa.
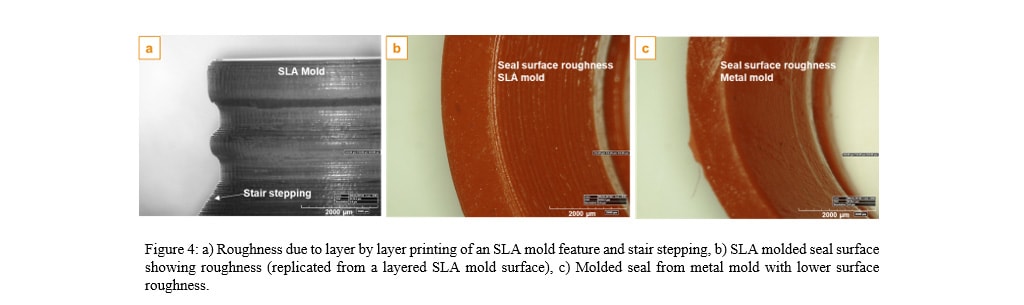
A vida útil dos moldes de polímero é limitada, ao contrário dos moldes metálicos. As propriedades mecânicas dos moldes de polímeros caem significativamente a temperaturas mais altas, especialmente acima da temperatura de deflexão de calor [2]. A reutilização dos moldes depende fortemente do tamanho mínimo da característica do núcleo, bem como dos parâmetros do processo de moldagem, como temperatura do molde, pressão etc. Por exemplo, moldes com características de núcleo maiores podem ser usados várias vezes antes que o molde de polímero rache, enquanto a quebra de características de núcleo menores limitaria o número de usos por molde. Para vedações com geometria extremamente pequena (não alcançável pela impressão), e/ou quando um grande número de peças forem necessárias, pode ser desejável o uso de ferramentas híbridas (ou seja, molde de polímero impresso com insertos de pinos metálicos), em vez de moldes de polímero sacrificiais ou de uso único.
Custo/tempo
Nossos custos de impressão de moldes internos foram significativamente mais baixos para moldes de várias cavidades de polímero impresso em comparação com um molde de metal usinado de um fornecedor externo. Para moldes impressos, o tempo total necessário desde o desenho do molde até as vedações moldadas foi de 2 semanas, contra de 8 a 10 semanas em relação aos de um fornecedor externo.
RESUMO
Em resumo, desenvolvemos uma capacidade sem igual para a moldagem rápida de vedações em diferentes silicones de grau de produção da TE e fluorossilicones usando moldes de polímeros impressos em 3D. A chave para essa capacidade é a experiência em design de molde de polímero, ajustando o processo de moldagem e usando abordagens não convencionais, dada a vida útil limitada da ferramenta do material do molde de polímero. A rápida capacidade de retorno do projeto CAD para a produção de vedações totalmente funcionais ajuda os engenheiros da TE a qualificar rapidamente vedações ao comparar vários projetos/materiais de vedação e fornecer peças rapidamente aos clientes finais para um feedback mais rápido dos testes de produtos. Nosso processo de moldagem rápida é uma ferramenta valiosa que pode oferecer economias significativas de custo/tempo para a produção de protótipos totalmente funcionais ou vedações HMLV que atendam a todos os requisitos do cliente.
AGRADECIMENTOS
Os autores gostariam de agradecer a Martin Bayes, John Wasserbauer e Bob Zubrickie (Tecnologia Corporativa), Nicholas Ruffini, Kenneth Dowhower (A D & M) e Galen Martin (Automotivo) por seu valioso apoio a este trabalho.
REFERÊNCIAS
[1] L. Zonder, N. Sella, “Precision Prototyping: The role of 3D printed molds in the injection molding industry”, Stratasys.
[2] G. A. Mendible, “Applications of transient cooling simulations in injection molding”, Thesis, University of Massachusetts Lowell, 2015.
Moldagem rápida de vedações elastoméricas funcionais para ambientes severos
RESUMO
Um processo rápido e de baixo custo para fazer protótipos funcionais ou vedações elastoméricas de alta mistura e baixo volume (HMLV) é demonstrado usando moldes de plástico ou polímero impressos em 3D. Demonstramos que este processo simples e versátil é capaz de moldar diferentes silicones e fluorossilicones de nível de produção da TE, produzindo uma variedade de projetos de vedação funcional complexos com detalhes finos e precisão que atendem aos requisitos de nossos clientes.
DECLARAÇÃO DO PROBLEMA
As vedações elastoméricas são componentes essenciais que protegem os contatos elétricos em conectores, sensores e conjuntos de cabos contra a corrosão devida a fatores ambientais adversos como umidade, gases, poeira, fluidos e outros produtos químicos. A TE oferece um grande portfólio de desenhos de vedações, incluindo vedações faciais, vedações familiares, vedações de cabo, vedações periféricas e O-rings. As vedações precisam atender às necessidades dos clientes quanto a diferentes conectores e componentes elétricos.
O objetivo do nosso trabalho foi desenvolver um processo versátil, rápido e de baixo custo que pudesse produzir protótipos funcionais e/ou vedações HMLV vendáveis que fossem feitas de materiais de nível de produção variando de borracha de silicone líquido (LSR) a borracha de alta consistência (HCR) ou fluorossilicones de pasta de goma (consistência de argila ou material semelhante a massa de vidraceiro) a borrachas e outras classes de elastômeros. Além disso, as vedações rápidas devem ser qualificadas para os três critérios principais de forma, ajuste e função (ou seja, capazes de atender aos requisitos de teste dimensional, de montagem e funcional). Um processo rápido fornece aos engenheiros da TE a capacidade de qualificar rapidamente as vedações, comparando diferentes versões de um projeto de vedação em diferentes materiais com propriedades variadas (por exemplo, dureza, conjunto de compressão, força de ruptura, resistência química). Os engenheiros da TE agora não só serão capazes de fornecer peças rapidamente para os clientes finais, mas também obterão feedback mais rápido dos testes do produto.
Aqui demonstramos o uso de moldes de polímeros impressos em 3D para moldagem de vedações elastoméricas que podem alcançar os critérios acima mencionados. A vantagem desse processo está em sua simplicidade e adaptabilidade para trabalhar com estoques líquidos e de goma. Foi avaliada uma variedade de tecnologias de impressão baseadas em fotopolimerização, como a estereolitografia (SLA), o jateamento de monômero e o processamento de luz digital (DLP), bem como diferentes materiais de molde, e combinações de impressora/material apropriadas foram identificadas para imprimir moldes de polímeros capazes de suportar as condições de moldagem típicas (por exemplo, alta temperatura e pressão). Fora da TE, os fornecedores continuam a desenvolver novos materiais de molde de polímero voltados para a moldagem por injeção de termoplásticos [1].
Comparamos também o desempenho funcional das vedações feitas de moldes de polímero impresso com relação a moldes de metal, e a economia geral de tempo/custo do processo associada à prototipagem usando moldes de polímero. Além disso, destacamos a importância de escolher o material correto para o molde de polímero e as condições de processamento do molde, as capacidades e limitações dos moldes de polímero.
MÉTODOS E RESULTADOS
Impressoras e materiais
As impressoras primárias usadas neste estudo foram impressoras comerciais SLA, DLP e jato de monômero, e vários materiais de resina comercial para moldes de impressão. Aspectos como diferenças na qualidade/precisão da impressão, rugosidade da superfície do molde e reutilização do molde serão descritos na seção de discussão.
Nosso processo é capaz de moldar graus comerciais de materiais de silicone e fluorossilicone, como borrachas de alta consistência (HCR) (também conhecidas como goma ou silicones sólidos) e silicones líquidos (por exemplo, 2 partes). As temperaturas de cura desses graus notas geralmente são >150 ºC. Os graus usados neste estudo variam de dureza 20 a 70 shore (por exemplo, shore A 20 ou shore A 50) e são adequados para exposição ambiental adversa.
Descrição do processo
Preparação de moldes de polímeros: moldes de várias cavidades foram projetados usando modelos de vedações. Modelos de moldes em CAD 3D (formato .stl) foram usados para criar arquivos de fatias ou de camadas para impressão 3D. Após a impressão 3D, os moldes (Figura 1a) foram limpos em solventes orgânicos para remover qualquer excesso de resina na superfície do molde, seguido por desgaseificação/tratamento UV e, em seguida, tratamento térmico a uma temperatura adequada para garantir que os moldes impressos fossem completamente curados. Descobrimos que é crucial curar os materiais do molde de polímero a uma temperatura apropriada; caso contrário, o silicone pode não curar completamente no molde de polímero, permanecendo pegajoso ao toque.
Moldes metálicos: moldes de aço de 4 cavidades foram preparados por usinagem convencional. Os moldes de aço foram limpos usando um solvente desengordurante e, em seguida, usados para moldagem de silicone.
Processo de moldagem: os moldes de polímero impressos em 3D foram pulverizados com um desmoldante à base de silicone antes da moldagem. Ampliamos o uso de moldes impressos em 3D para vários processos de moldagem, como injeção, transferência e moldagem por compressão. Desenvolvemos experiência em projetos de moldes de polímeros, ajuste do processo de moldagem e uso de abordagens não convencionais, dada a vida útil limitada da ferramenta devido à menor resistência/condutividade térmica do material do molde de polímeros. Normalmente, a moldagem com ferramenta de polímero exigiria um tempo de ciclo mais alto, o que é aceitável para fins de prototipagem. É fundamental escolher um material de molde apropriado, pois os moldes de polímero foram submetidos a 180 ºC em nosso processo de cura dos silicones.
Após a desmoldagem, as vedações foram rebarbadas manualmente e depois pós-curadas por mais 10 a 120 min a 180 ºC para garantir a cura completa. Dependendo da durabilidade das características principais, os moldes podem ser descartáveis ou reutilizáveis. Para comparação, as vedações também foram feitas a partir de moldes metálicos usinados utilizando um processo de moldagem padrão.
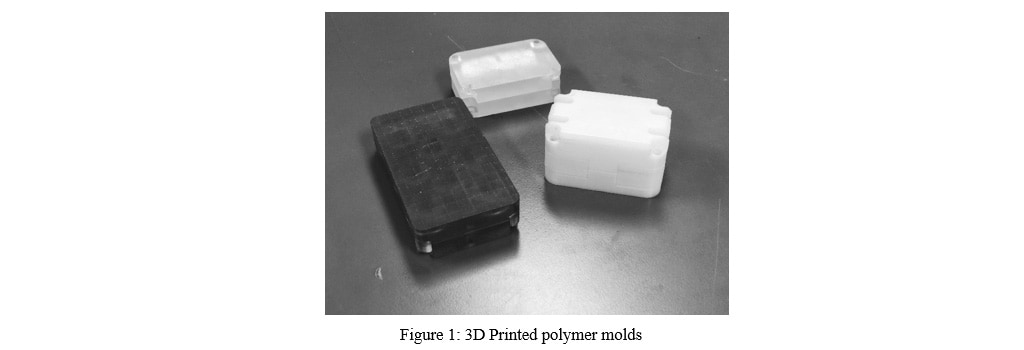
A Figura 2a-g mostra exemplos de vedações moldadas produzidas usando diferentes materiais de molde de polímero impresso em uma variedade de formas, tamanhos, complexidade e tipos de material de silicone. Usando moldes de polímero de alta resolução, conseguimos moldar pequenos anéis de vedação (Figura 2b-c) com um perfil de furo complexo (diâmetro do furo de 1,01 mm, diâmetro mínimo no perfil do furo de 0,53 mm, espessura da parede entre dois furos de apenas 0,25 mm). A Figura 2e-f mostra um exemplo de projeto de vedação automotiva com pequenos recursos (menor espessura de parede de 0,35 mm e pequenos furos com 0,69 mm de diâmetro) que foram moldados com êxito. A Figura 2g mostra exemplos de vedações automotivas de fio único, periféricos e anéis isolantes.
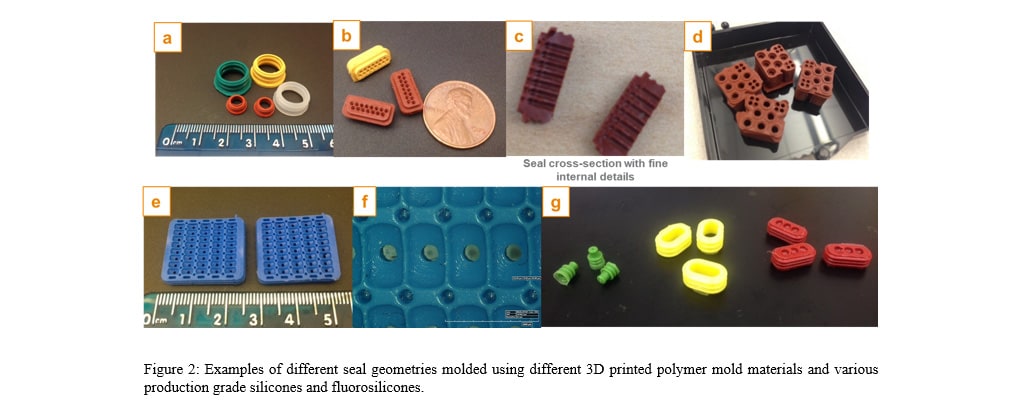
Resultados de testes funcionais de vedações
As vedações funcionais (Figura 2a) para um cliente aeroespacial, preparados utilizando a) moldes de polímero impressos em 3D, e b) moldes de aço, foram montadas em terminais de alumínio, seguidos de inserção de fio e crimpagem (ver Figura 3). Todas as vedações passaram pelo conjunto e os requisitos dimensionais (os diâmetros da gaxeta de vedação estavam dentro da tolerância permitida de 0,1 mm). Os terminais montados foram pressurizados na extremidade do fio e testados para vazamento de ar sob a água em 1 bar e 2 bars. O teste de vazamento foi feito antes e depois de as peças serem submetidas a a) 10 ciclos de choque térmico (-65 ºC a 180 ºC) e b) condicionamento de temperatura (180 ºC por 5 dias). Os requisitos para a qualificação do projeto da vedação do cliente eram passar por todos os testes em 1 bar sem vazamento.
Protótipos de vedações foram feitos para vários tamanhos de fios e diferentes materiais de silicone e fluorossilicone foram examinados por testes de vazamento. Um grau adequado de material de silicone HCR foi selecionado com base em um desempenho de teste de vazamento aceitável. As vedações de moldes de polímeros para todos os tamanhos de fio passaram no teste de vazamento antes e depois do condicionamento de choque térmico, o que é um resultado muito encorajador. Além disso, todas as vedações de molde de polímero para fios maiores (AWG 000, 00, 0A, 1, 2, 3) passaram no teste de vazamento após o condicionamento de temperatura de cinco dias a 180 ºC. O processo de prototipagem usando molde de polímero também nos permitiu qualificar rapidamente vedações AWG 8 menores com um design modificado (parede mais grossa, de 1,99 mm) que passou por todos os testes de vazamento. Nossos resultados mostram que os protótipos de vedações de moldes de polímero são capazes de passar os requisitos funcionais semelhantes aos moldes metálicos.
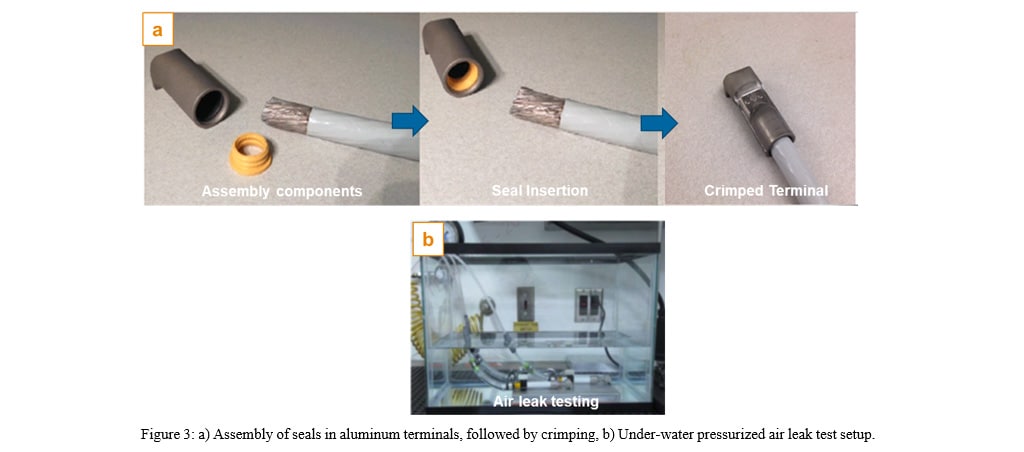
DISCUSSÃO E PONTOS-CHAVE
Recursos e limitações do molde de polímero impresso em 3D
O processo de moldagem usando moldes de polímeros impressos em 3D de várias cavidades pode produzir desenhos de vedações intrincados e complexos aplicáveis a um grande portfólio de vedações da TE. O número de cavidades por molde de polímero pode variar de 1 para vedações de maior porte a >35, para vedações de tamanho menor. As impressoras SLA normalmente usam laser, fornecendo a mais alta precisão e a melhor resolução de recursos (observe que a SLA também pode imprimir recursos ou cantos nítidos), seguidos de perto por impressoras DLP que usam tecnologia de projeção de luz seguidas por impressoras de jato de monômero que curam fotopolímeros usando luz UV de banda larga (observe que os cantos afiados são impressos arredondados). A cura excessiva da resina perto das bordas características devido à penetração da luz mais profunda do que o desejado pode afetar a resolução e a precisão da impressora.
A rugosidade superficial dos moldes impressos varia de acordo com a impressora e o material que está sendo impresso. A rugosidade da superfície é inerente à impressão camada por camada (por exemplo, espessura da camada de 0,05 mm para SLA) e ao efeito de degrau de escada (superfícies construídas em um ângulo) que podem ser claramente vistas na imagem microscópica de um detalhe de molde SLA (Figura 4a). A topografia superficial da superfície do molde do polímero é claramente replicada nas vedações moldadas (Figura 4b). A rugosidade da superfície da vedação moldada de um molde de polímero é maior do que a das vedações dos moldes metálicos (Figura 4c). Podem estar presentes rugosidades adicionais em áreas onde o material de suporte é removido da superfície do molde. A rugosidade adicional da superfície pode não ser aceitável para algumas aplicações de vedação. Observe que também é possível usar ferramentas híbridas, nas quais moldes de polímeros impressos são combinados com inserções de pinos de núcleo metálico para aplicações que exijam superfícies de vedação com rugosidade de superfície extremamente baixa.
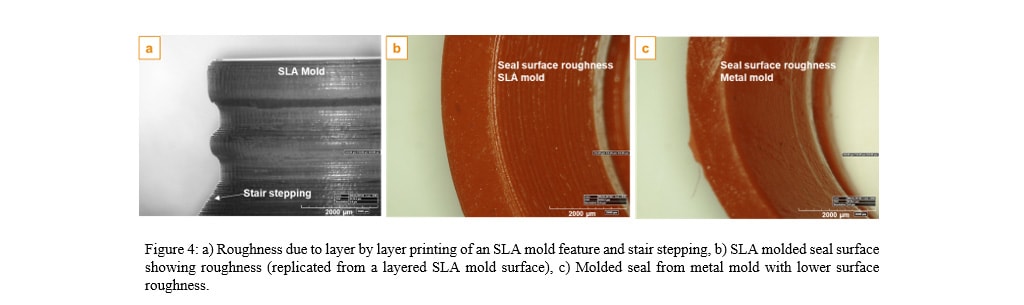
A vida útil dos moldes de polímero é limitada, ao contrário dos moldes metálicos. As propriedades mecânicas dos moldes de polímeros caem significativamente a temperaturas mais altas, especialmente acima da temperatura de deflexão de calor [2]. A reutilização dos moldes depende fortemente do tamanho mínimo da característica do núcleo, bem como dos parâmetros do processo de moldagem, como temperatura do molde, pressão etc. Por exemplo, moldes com características de núcleo maiores podem ser usados várias vezes antes que o molde de polímero rache, enquanto a quebra de características de núcleo menores limitaria o número de usos por molde. Para vedações com geometria extremamente pequena (não alcançável pela impressão), e/ou quando um grande número de peças forem necessárias, pode ser desejável o uso de ferramentas híbridas (ou seja, molde de polímero impresso com insertos de pinos metálicos), em vez de moldes de polímero sacrificiais ou de uso único.
Custo/tempo
Nossos custos de impressão de moldes internos foram significativamente mais baixos para moldes de várias cavidades de polímero impresso em comparação com um molde de metal usinado de um fornecedor externo. Para moldes impressos, o tempo total necessário desde o desenho do molde até as vedações moldadas foi de 2 semanas, contra de 8 a 10 semanas em relação aos de um fornecedor externo.
RESUMO
Em resumo, desenvolvemos uma capacidade sem igual para a moldagem rápida de vedações em diferentes silicones de grau de produção da TE e fluorossilicones usando moldes de polímeros impressos em 3D. A chave para essa capacidade é a experiência em design de molde de polímero, ajustando o processo de moldagem e usando abordagens não convencionais, dada a vida útil limitada da ferramenta do material do molde de polímero. A rápida capacidade de retorno do projeto CAD para a produção de vedações totalmente funcionais ajuda os engenheiros da TE a qualificar rapidamente vedações ao comparar vários projetos/materiais de vedação e fornecer peças rapidamente aos clientes finais para um feedback mais rápido dos testes de produtos. Nosso processo de moldagem rápida é uma ferramenta valiosa que pode oferecer economias significativas de custo/tempo para a produção de protótipos totalmente funcionais ou vedações HMLV que atendam a todos os requisitos do cliente.
AGRADECIMENTOS
Os autores gostariam de agradecer a Martin Bayes, John Wasserbauer e Bob Zubrickie (Tecnologia Corporativa), Nicholas Ruffini, Kenneth Dowhower (A D & M) e Galen Martin (Automotivo) por seu valioso apoio a este trabalho.
REFERÊNCIAS
[1] L. Zonder, N. Sella, “Precision Prototyping: The role of 3D printed molds in the injection molding industry”, Stratasys.
[2] G. A. Mendible, “Applications of transient cooling simulations in injection molding”, Thesis, University of Massachusetts Lowell, 2015.