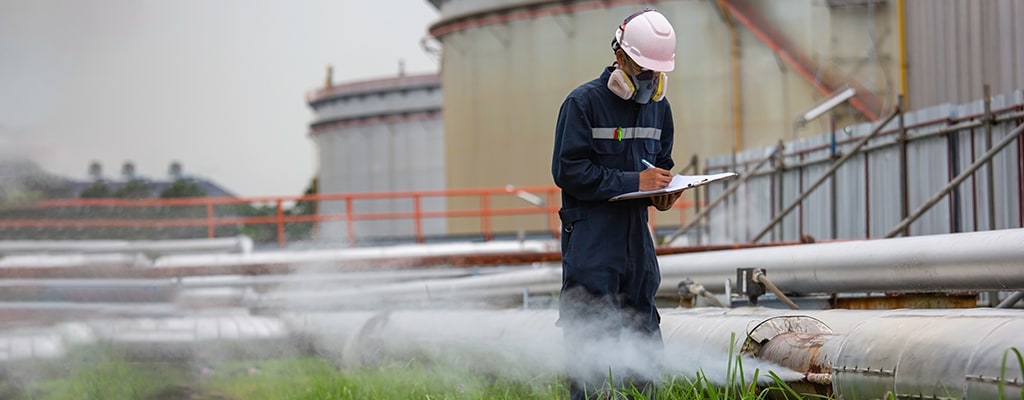
Indústrias
Monitoramento e Detecção de Corrosão sob Isolamento no Setor de Petróleo e Gás
A corrosão sob isolamento (CUI) é um desafio importante para várias indústrias, principalmente para o setor de petróleo e gás. Um problema generalizado, oculto sob camadas de isolamento, que frequentemente não é percebido até o momento da manutenção de rotina. Caso seja negligenciado, esse problema pode comprometer a segurança, gerar danos ambientais, interrupções operacionais, prejuízos financeiros, além de quebra da conformidade, redução da vida útil dos ativos e aumento dos desafios de manutenção. Ainda, pode gerar ferimentos ou até mesmo a perda de vidas. Relatórios sugerem que a corrosão sob isolamento é responsável por 40% a 60% dos custos de reparos de tubulações (Dey, n.d.), totalizando centenas de bilhões de dólares em despesas anuais para a indústria.
Este white paper aborda o problema persistente da corrosão sob isolamento. O white paper apresenta as tecnologias avançadas de sensores e técnicas de monitoramento, fundamentais para a detecção precoce da corrosão sob isolamento e para seu monitoramento contínuo. Com o emprego dessas técnicas e tecnologias, é possível mitigar perigos potenciais de forma proativa, bem como preservar a integridade dos ativos, a segurança e a continuidade das operações da indústria de petróleo e gás.

Visão Geral da Corrosão sob Isolamento (CUI)
A chamada “CUI”, na sigla em inglês, é a corrosão externa que normalmente ocorre em equipamentos isolados feitos de aços carbonos ou de liga baixa, como tubulações. Para que esse tipo de corrosão ocorra, duas condições são necessárias:
- A presença de água
- A disponibilidade de oxigênio
A corrosão sob isolamento é prevalente em instalações de processamento e refinarias que operam sob temperaturas flutuantes, as quais contribuem significativamente para o processo de corrosão. Além disso, a exposição do sistema a produtos corrosivos em contato com a superfície da tubulação também atua como fonte da corrosão.
A tubulação abaixo do isolamento é tipicamente feita de aço, enquanto o isolamento é composto por materiais ou combinações de materiais que a envolvem para reduzir significativamente a transferência da energia térmica. A redução efetiva de perdas de energia contribui para uma redução considerável dos custos.
Tubulação de Isolamento a Quente e a Frio
O isolamento a quente impede a transferência de energia do fluido aquecido. A principal função do isolamento é a conservação do calor. Também protege os operadores das superfícies quentes. Os materiais isolantes a quente comumente usados incluem lã mineral, lã de vidro e silicato de cálcio.
Por outro lado, o isolamento a frio reduz a transferência de calor do ambiente externo para a tubulação e também limita a condensação. Materiais isolantes a frio comumente usados incluem espuma de poliuretano ou espuma de borracha.
Entender a composição e a função dos materiais de isolamento, tanto quentes como frios, fornece um conhecimento fundamental sobre a função que eles cumprem no complexo problema da corrosão sob isolamento. Embora a função principal do isolamento seja controlar a transferência da energia, ele cria inadvertidamente um ambiente propício à corrosão quando combinado com certas condições ambientais e operacionais.
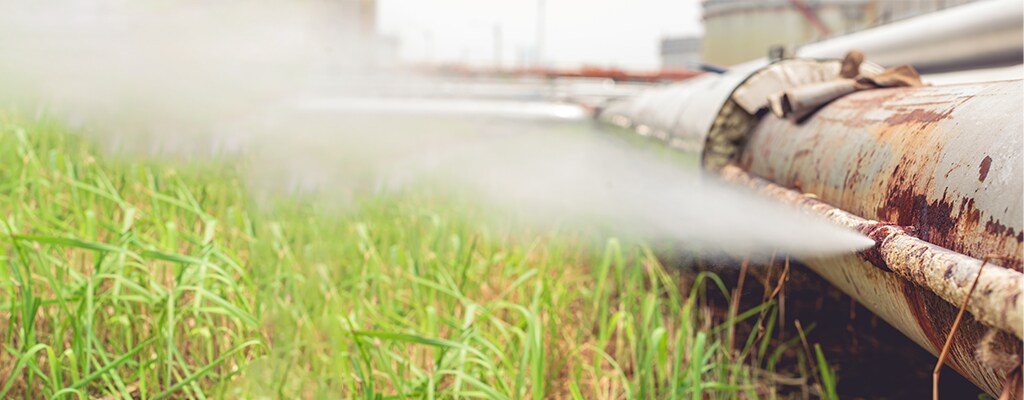
Condições ambientais corrosivas que afetam um tubo isolado.
Detecção Tradicional da Corrosão sob Isolamento
Vários fatores interagem para facilitar a corrosão sob isolamento. A interação dos elementos acima forma uma rede complexa de causalidade que agrava o problema, tornando-o difícil de detectar e gerenciar. Vamos explorar a interação dos fatores de uma forma mais detalhada, esclarecendo como interações complexas resultam no desenvolvimento da corrosão.
Em primeiro lugar, as condições ambientais influenciam enormemente o seu surgimento. A umidade, as flutuações da temperatura e a exposição a aerosol salino ou a poluentes industriais podem aumentar a probabilidade da intrusão de água no isolamento, um pré-requisito para o surgimento da corrosão. Essas condições, em combinação com a temperatura de operação do equipamento, são perfeitas para gerar a corrosão.
Outro fator crítico é a qualidade e o tipo do isolamento. Como observado anteriormente, os materiais de isolamento variam muito. Além disso, sua eficácia e suscetibilidade à retenção da água podem contribuir para a formação de corrosão. Por exemplo, os isolamentos porosos (hidrofílicos) ou as células fechadas (hidrofóbicas) contribuirão de diferentes maneiras para a criação da corrosão sob isolamento.
As propriedades materiais do equipamento isolado, particularmente a resistência à corrosão, cumprem uma função fundamental no início da CUI. Os aços carbonos e de liga baixa são propensos à ferrugem quando expostos à umidade, um processo agravado pelas altas temperaturas.
Além disso, as práticas operacionais são um fator contribuinte. Por exemplo, equipamentos que alternam frequentemente entre temperaturas altas e baixas podem levar à condensação dentro do isolamento, criando um ambiente ideal para a corrosão. As práticas de manutenção também influenciam significativamente a ocorrência da CUI. Se o isolamento permanecer danificado ou se a intrusão de umidade não for tratada imediatamente, o risco aumentará.
Entender tais interações complexas é essencial para formular estratégias efetivas para prevenir e mitigar a CUI. Antes de falar sobre estratégias e suas respectivas eficácias, vamos explicar o fenômeno da CUI com um exemplo recorrente: a construção de tubos de isolamento a quente. Para proteger o isolamento fisicamente e contra as condições climáticas externas, uma capa metálica (chamada também de "blindagem"), é fixada ao redor do isolamento e mantida no lugar com cintas metálicas. A capa foi projetada para envolver o isolamento, resultando na criação de juntas longitudinais ou radiais.
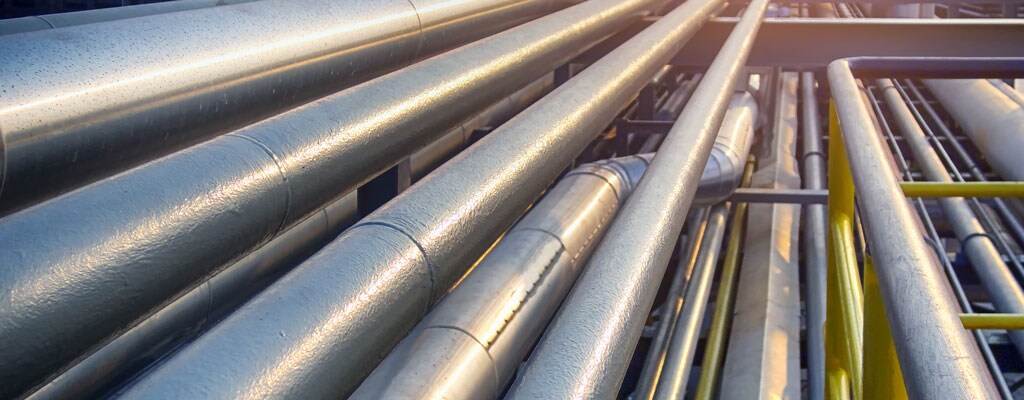
Tubo isolado com blindagem metálica.
As chuvas, embora sejam uma causa comum, não são a única fonte de água que pode desencadear a CUI. A água também pode ser proveniente das torres de resfriamento, vapor e diversos processos que podem resultar em derramamento de líquidos. A intrusão da água poderá ocorrer se o revestimento estiver danificado ou os selos rompidos, ou devido a forças externas como impactos, objetos pontiagudos ou em queda ou pessoas andando sobre o tubo. Quando existe um ponto de entrada de água, nem sempre ele é imediatamente perceptível. Contudo, em caso de chuva, a intrusão de água se torna inevitável.
A interação entre a água e o material de isolamento pode diferir dependendo da natureza do material. Como mencionado acima, se o material de isolamento for hidrofóbico (uma célula fechada que não permite a absorção de água), a água fluirá e permanecerá prensada entre o isolamento e o tubo. A água nem sempre evapora totalmente com o tempo e algumas bolsas de água podem persistir em certos locais.
Por outro lado, se o material de isolamento for hidrofílico (capaz de absorver umidade como uma esponja), a água criará condução térmica através da esponja e o momento térmico seguirá do tubo para o revestimento. Assim, cria-se um ciclo de evaporação-condensação, que aumenta a concentração de "sais” na superfície do tubo à medida que a água evapora. Os "sais", em combinação com outros elementos naturais do material de isolamento, pode degradar a proteção do tubo e gerar corrosão e fissuras. Esse processo no isolamento é conhecido como fissuração por corrosão sob tensão de cloreto (CSCC).
Os contaminantes, principalmente cloretos e sulfatos, são comuns sob isolamento. Podem lixiviar dos materiais de isolamento ou vir de fontes externas. As soluções aquosas, com alta condutividade elétrica, podem facilitar o processo de corrosão.
A temperatura também cumpre uma função fundamental. É geralmente aceito (ou diferentes fontes indicam) que aço carbono em operação na faixa de temperatura de -4 °C (25 °F) a 149 °C (300 °F) está em risco mais alto de CUI. Equipamentos que operam continuamente abaixo de -4 °C (25 °F) tendem a permanecer livres de corrosão. Equipamentos que operam acima de 149 °C (300 °F), excedendo o ponto de ebulição da água, apresentam corrosão reduzida porque a superfície do aço carbono permanece essencialmente seca.
Entender a interação entre os materiais de isolamento, o ingresso de água, os contaminantes e as variações de temperatura é fundamental para entender o início da CUI. No entanto, essa compreensão não estará completa sem que as consequências potenciais de quando esse problema não é mitigado sejam avaliadas. As complicações vão além da própria corrosão. Vários aspectos essenciais para a indústria de petróleo e gás são afetados, como o financeiro, a saúde, a segurança e o meio ambiente.
As implicações da CUI são semelhantes às da corrosão em termos mais gerais. A corrosão pode precipitar fissuras que geram fraturas e vazamentos da tubulação dos derivados de petróleo. Além de representar uma ameaça significativa para o ambiente circundante devido à poluição potencial, também cria riscos para a saúde daqueles que vivem perto dos vazamentos. Além disso, o risco de incêndios e explosões adiciona uma camada de perigo a uma situação já crítica.
São danos não apenas perigosos, mas também dispendiosos. O processo de reparo pode custar muito caro, tanto em termos de capital quanto de recursos operacionais (CAPEX e OPEX), além de oferecer perigo para os técnicos envolvidos. Nas seções a seguir, apresentaremos estratégias para prevenir e mitigar a CUI, bem como para controlar esses riscos efetivamente.
Descobrir a CUI é um desafio devido à sua natureza oculta sob o isolamento, o que a torna perceptível apenas quando já é tarde demais. Os métodos tradicionais para detectar a CUI variam de técnicas simples a avançadas, todas destinadas a descobrir a corrosão antes que ela cause danos significativos.
A abordagem mais prevalente e direta à inspeção da CUI envolve o corte de partes do isolamento para permitir testes não destrutivos ou inspeções visuais.
Os seguintes métodos, com suas respectivas vantagens e desvantagens, são comumente empregados para detectar a CUI:
- Inspeção visual: o primeiro e mais simples método envolve remover o isolamento, verificar a condição da superfície do tubo e restaurar o isolamento. Estudos mostram que, na maioria das vezes, a CUI não é encontrada após a remoção do isolamento. Outros desafios podem ser o risco associado ao manuseio do isolamento na presença de amianto ou ao impacto no isolamento térmico se a tubulação estiver em serviço.
- Inspeção sem remoção do isolamento: essa técnica reduz consideravelmente o custo das inspeções, pois não requer a remoção e reinstalação do isolamento. Métodos de avaliação não destrutiva (NDE) são normalmente usados nesta abordagem.
- Avaliação não destrutiva (NDE): a NDE engloba várias técnicas de inspeção não invasivas usadas para avaliar as propriedades de materiais , componentes ou unidades de processo inteiras. Vários métodos, como corrente de fuga pulsada (PEC) e radiografia digital, são usados para inspecionar a CUI. Normalmente, nenhum método é usado de forma isolada. Vários métodos são usados em conjunto para alcançar os melhores resultados.
- Corrente de fuga pulsada (PEC): o equipamento de PEC opera com eletromagnetismo, determinando efetivamente a espessura média da parede do tubo por meio do isolamento. Dessa forma, é possível detectar e localizar a CUI. A principal vantagem da PEC é que ela consegue aferir o afinamento das paredes em objetos isolados, sem remover o isolamento ou qualquer preparação da superfície do objeto.
- Ondas guiadas (GW): tecnologia alternativa para avaliar a CUI em trechos longos de tubulação. Usa ondas ultrassônicas guiadas de baixa frequência que se propagam ao longo do tubo. As corrosões interna e externa podem ser detectadas, mas, para isso, os sensores de onda guiada precisam estar em contato direto com o tubo. Assim, ao menos uma parte do isolamento precisa ser removida para a instalação de sensores.
- Radiografia digital em tempo real: raios X são aplicados em um lado do tubo isolado, atravessam seu interior, o revestimento e o isolamento até que o sensor os receba no lado oposto. Os raios recebidos pelos sensores são convertidos em imagens em tempo real, destacando anomalias como a corrosão interna ou externa, além de defeitos no tubo. O método pode ser aplicado sem remover o revestimento e fornece informações em tempo real.
- Termografia: usada na indústria petroquímica. Exibe uma imagem térmica do objeto e detecta a energia desperdiçada que, por exemplo, pode ser causada por defeitos do isolamento, ingresso de água, gás ou vazamentos de líquidos que afetam a temperatura do tubo isolado.
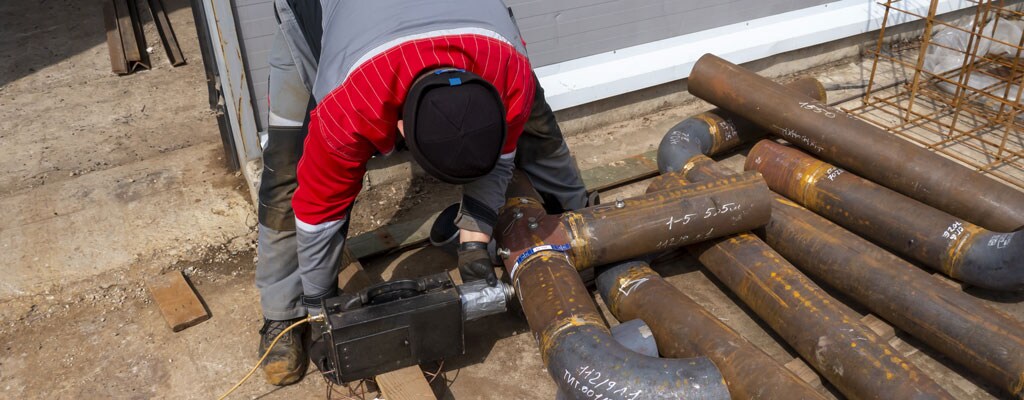
Especialista instalando um dispositivo de raios X para a avaliação não destrutiva de juntas soldadas.
Embora cada um dos métodos descritos tenha pontos fortes únicos, todos compartilham limitações inerentes que podem torná-los ineficazes para revelar corrosões ocultas sob isolamento. As inspeções visuais, embora simples, expõem apenas as condições da superfície, negligenciando potencialmente a corrosão mais profunda. A remoção e o restabelecimento do isolamento durante as inspeções também adicionam custos substanciais e desafios logísticos como o gerenciamento do amianto. (Texas Nondestructive Testing Academy & Level III Services, n.d.)
Os métodos de avaliação não destrutiva (NDE), que avaliam as propriedades do material sem danificar o isolamento, são limitados por sua própria natureza. Por exemplo, os sistemas de corrente de fuga pulsada (PEC) oferecem informações valiosas sobre o afinamento da parede, mas podem não detectar precisamente a corrosão localizada ou pequenas cavidades. (Texas Nondestructive Testing Academy & Level III Services, n.d.)
A tecnologia de ondas guiadas requer a remoção do isolamento em pontos específicos, permitindo a possibilidade de negligenciar a corrosão que ocorre em outros lugares. Além disso, fatores como revestimentos de alta perda ou reflexões de sinal de características como soldas e grampos podem afetar a atenuação do sinal, limitando o comprimento da tubulação que pode ser inspecionado. (Chukwuemeka, et al., 2021)
A radiografia digital em tempo real fornece imagens das anomalias potenciais sob o isolamento, mas pode não ter sensibilidade para detectar a corrosão no estágio inicial. Além disso, é útil apenas para densidades de materiais e pode não revelar a corrosão efetivamente em certos materiais de tubos. (Nanan, 2020)
Exames visuais e termografia, embora efetivos para identificar perigos potenciais de CUI devido a danos na impermeabilização ou no revestimento, oferecem apenas uma análise no nível da superfície e podem negligenciar a corrosão oculta mais profundamente sob o isolamento. (Fujifilm, 2022)
Em essência, o principal desafio está na incapacidade dos métodos de fornecer uma avaliação completa e abrangente da corrosão oculta, principalmente quando ela é localizada ou ainda está nos estágios iniciais. As limitações de cada método podem deixar áreas significativas sem verificação, levando potencialmente à negligência de uma CUI que continuará evoluindo sob o isolamento.
Sensores para Detecção da CUI
Emergindo da transformação digital da indústria, a rápida proliferação dos dispositivos e sistemas interconectados da Internet das Coisas (IoT) abriu o caminho para tecnologias inovadoras de detecção de CUI, particularmente por meio de sensores sem fio alimentados por bateria. A aceleração da revolução tecnológica se deve em grande parte ao surgimento de sensores sem fio alimentados por bateria que aproveitam os avanços na eletrônica de baixa potência e a introdução de protocolos de comunicação sem fio "compatíveis com bateria", como LoRaWAN, NB-IoT, LTE M e Bluetooth.
Vários princípios de sensoriamento estão sendo avaliados, incluindo sensores que detectam umidade e temperatura entre o tubo e o revestimento externo, ou dentro ou ao redor do material de isolamento, por exemplo, fibra óptica ou EMGR. No entanto, existem desafios como o retrofit das infraestruturas existentes com fibra óptica ou a integração de cabos "dispensáveis" no isolamento.
Os fios "dispensáveis" são usados junto do Radar Eletromagnético Guiado (EMGR). Sua corrosão serve como um pré-indicador da CUI, enquanto o cabo não corrosivo transmite sinais para um módulo sem fio colocado fora do revestimento. A incorporação permite uma adequação perfeita entre os métodos de detecção inovadores e as restrições práticas da implementação, refletindo as complexidades inerentes à fusão das novas tecnologias com as infraestruturas estabelecidas.
A TE Connectivity se destaca em superar desafios por meio da sua experiência exclusiva em sensores, particularmente em tecnologia de detecção capacitiva de umidade relativa e em transmissores sem fio. Os sensores, estrategicamente posicionados em tubos isolados, permitem o mapeamento efetivo de infraestruturas inteiras. Eles podem detectar o ingresso de água e, por meio de análises inteligentes, simplificar a tarefa de identificar as áreas que exigem uma investigação adicional da CUI usando métodos de avaliação não destrutiva (NDE). Na seção de estudo de caso, há mais detalhes sobre como a tecnologia é aplicada em ambientes do mundo real.
Os esforços colaborativos na indústria oferecem meios para um monitoramento aprimorado em tempo real. No entanto, a eficácia das soluções é substancialmente amplificada quando emparelhadas com as tecnologias avançadas de sensores da TE Connectivity.
Com frequência, a abordagem tradicional requer inspeções caras e o uso de muitos recursos. No entanto, os sensores da TE Connectivity buscam otimizar os processos e exigir menos recursos, economizando tempo e custos. Mais de 90% das inspeções visuais realizadas após a remoção do revestimento não resultam na localização de uma corrosão. As inspeções direcionadas facilitadas pela nossa avançada tecnologia de sensores podem, portanto, levar a economias de custos significativas.
Diferentes empresas podem ter as próprias estratégias de inspeção baseadas em riscos. Os ativos essenciais provavelmente continuarão a ser submetidos a manutenções programadas e métodos não destrutivos, mas os menos essenciais poderiam ter seus custos de manutenção substancialmente reduzidos se equipados com
os sensores remotos sem fio da TE Connectivity.
A meta continua sendo projetar e implantar um sensor robusto, preciso, econômico e duradouro, capaz de monitorar todos os tubos e superfícies isolados nas refinarias. Os sensores da TE Connectivity, que já atendem a esses critérios, também são totalmente certificados por ATEX FCE, proporcionando uma operação segura em ambientes potencialmente perigosos.
Avanços na Tecnologia de Sensores e suas Respectivas Vantagens
O uso de tecnologias como a LoRaWAN permite a obtenção de dados do sensor em distâncias que variam de alguns metros a vários quilômetros. Trabalhando em conjunto com gateways, análises avançadas, estratégias de gerenciamento focadas em CUI e experiência especializada em corrosão, os operadores e as empresas de manutenção podem detectar a corrosão proativamente. Dessa forma, intervenções rápidas e direcionadas para reparar as áreas em que a corrosão ocorre se tornam possíveis, economizando tempo e reduzindo custos e, ao mesmo tempo, permitindo a segurança e a longevidade da infraestrutura.
A integração dos sistemas é extremamente vantajosa para o gerenciamento proativo da corrosão sob isolamento. Nos últimos anos, numerosos experimentos e simulações laboratoriais que envolvem sensores de umidade foram realizados. Resultados promissores foram produzidos, demonstrando que as medições de umidade e temperatura podem de fato ser efetivas na detecção de CUI antes que ela ocorra. Na TE Connectivity, temos orgulho de nossa experiência em tecnologia de sensores, fundamental para esses avanços. No entanto, os avanços não ficam apenas no laboratório. Eles são aplicados na prática por meio de parcerias estratégicas importantes, como vamos explicar a seguir.
Estudo de Caso da KAEFER
Reconhecendo as Graves Preocupações da Indústria
Em anos recentes, o KAEFER Group, líder em soluções integradas de serviços industriais, entrevistou várias empresas de petróleo e gás em todo o mundo. Um ponto em comum surgiu: todos citaram a corrosão sob isolamento (CUI) como prioridade máxima. A preocupação não era apenas técnica, mas havia implicações de longo alcance, como as abordadas anteriormente neste artigo. A colaboração com a KAEFER tomou forma nesse contexto, pronta para atender às necessidades urgentes.
Soluções Abrangentes por Meio da KIT®
A Blu Empowered by KAEFER introduziu a KIT® (Tecnologia de Integridade da KAEFER) como um serviço holístico de ponta a ponta para o gerenciamento da CUI. A KIT mostra a experiência da KAEFER no gerenciamento efetivo dos projetos de CUI de diferentes escalas. Desde a intrincada otimização do posicionamento e da instalação do sensor até a configuração do sistema, a KIT se destaca como um pacote completo. Porém, o que amplifica a capacidade é a tecnologia de sensores da TE Connectivity.
A sinergia entre os serviços integrados da KAEFER e as soluções avançadas de detecção da TE constitui a base da parceria inovadora. A tecnologia de sensores sem fio da TE, incorporada a recursos como a bateria de longa duração e a capacidade de resistir em ambientes adversos, representa um avanço significativo na detecção da CUI. Certificados para atender aos mais altos padrões de segurança, os sensores sem fio permitem a comunicação em grandes distâncias usando protocolos avançados como LoRaWAN™ e são equipados com Bluetooth® de Baixa Energia para a configuração remota versátil.
Além disso, a incorporação de tempos de medição personalizáveis e do gerenciamento inteligente de eventos de limiar exemplifica a abordagem inovadora da parceria, aumentando a confiabilidade e a precisão dos dados enquanto a vida útil da bateria é otimizada. O uso de sensores com notificações automáticas para gerenciamento da bateria, além de adaptação autônoma na medição e transmissão de dados com limites configurados, é o que entrega a maior eficiência.
Os elementos de sensoriamento da tecnologia são meticulosamente projetados, frequentemente aproveitando as tecnologias MEMS de matriz de umidade e ASIC há muito comprovadas, ambas amplamente usadas em várias indústrias, incluindo nos setores automotivo, de caminhões e veículos off road. Significativamente, a aplicação interindustrial ressalta o potencial para o escalonamento de alto volume em setores como petróleo e gás, permitindo a entrega dos níveis de qualidade exigidos em indústrias como a automotiva e servindo como espinha dorsal para a aquisição efetiva de dados e monitoramento em tempo real.
Sofisticação Técnica na KIT®
A KIT oferece um esquema de monitoramento da CUI totalmente digitalizado. Embora seja verdade que as áreas problemáticas identificadas ainda requerem inspeções tradicionais, há potencial para autonomizar as atividades de campo, reduzindo a intervenção humana e, assim, mitigando os riscos. Além disso, o sistema está em desenvolvimento contínuo para incluir vários recursos como um serviço de consultoria e até mesmo a possibilidade de instalação por sistemas robóticos e autônomos que funcionam por meio dos sensores sem fio operados por bateria da TE.
Em termos de visualização de dados, a KIT oferece opções que vão desde painéis modernos até representações de gêmeos digitais. As opções são enriquecidas por análises sofisticadas que ajudam a prever a corrosão sob isolamento, bem como a recomendar ações de manutenção.
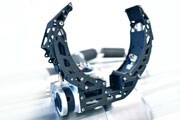
Monkeybot para a instalação de sensor robótico
A integração da tecnologia de sensores da TE Connectivity à KIT® não oferece apenas sofisticação tecnológica, mas vantagens perceptíveis. Estudos de caso demonstraram economias significativas de custos em manutenção e melhorias na integridade das instalações. Por fim, o processo resulta no aumento do valor para o cliente, algo que tanto a KAEFER quanto a TE Connectivity se esforçam para alcançar.
Conclusão
Ao lidar com o desafio generalizado da corrosão sob isolamento, um dilema que gera complicações significativas para a eficiência operacional, segurança ambiental e bem-estar da comunidade, nunca é demais enfatizar a função da tecnologia avançada. O whitepaper ilustrou os vastos impactos da corrosão no setor de petróleo e gás, que afetam não apenas os resultados financeiros como despesas de capital e operacionais (CAPEX e OPEX), mas também fatores de saúde, segurança e meio ambiente (HSE).
Nossa colaboração com a KAEFER serve como pano de fundo, reconhecendo as necessidades urgentes da indústria por soluções robustas de gerenciamento da CUI. A KIT® da KAEFER, que integra a inovadora tecnologia de sensores da TE Connectivity, oferece um serviço holístico de ponta a ponta para gerenciamento da CUI. O esforço colaborativo exemplifica uma abordagem interdisciplinar para a resolução de problemas, unindo diversos conhecimentos em um ecossistema dedicado a enfrentar os complexos desafios da detecção e gerenciamento da CUI. A implantação em larga escala dos nossos sensores sem fio alimentados por bateria vai além da mera conquista tecnológica, resultando em um impacto transformador na indústria. O potencial para reduzir a manutenção programada e as inspeções visuais desnecessárias amplia a segurança e oferece economia de custos substancial.
A digitalização dos ativos, incluindo o desenvolvimento de "gêmeos digitais", permite uma maior precisão e previsibilidade. Nossos sensores, apoiados por ferramentas de análise robustas, se alinham bem aos sistemas e padrões existentes, indicando nosso compromisso com os principais avanços na detecção e prevenção da CUI. É uma prova da nossa dedicação à evolução contínua da tecnologia de sensores e às parcerias da indústria que tornam esses avanços possíveis.
Com relação ao futuro, o foco da TE Connectivity permanece claro: pioneirismo em soluções mais seguras e sustentáveis, empregando tecnologias de ponta. As ferramentas de visualização baseadas em sensores inteligentes sem fio oferecem uma visão abrangente da integridade dos ativos, permitindo uma transição perspicaz da manutenção generalizada e baseada em riscos para uma abordagem mais focada e orientada aos dados.

Os sensores sem fio da TE Connectivity foram implantados e são usados atualmente em aplicações de monitoramento de condições que permitem a manutenção preditiva de ativos rotativos e cabeças de poços de petróleo e gás.
Disponibilizamos uma plataforma inteligente e completa, que inclui sensores de vibração piezoelétricos únicos e triaxiais com uma faixa de frequências até 15 kHz (FFT e processamento de sinal integrados), sensores de temperatura que podem ser fixados na tubulação e suportar até 260 °C de temperatura externa, bem como sensores de pressão que podem medir a pressão absoluta ou relativa.
Os sensores inteligentes são totalmente configuráveis por meio do TE Sensor Toolbox ou com um smartphone e o aplicativo TE SensorConnect (disponível na Apple App Store ou na Google Play Store). Quando analisamos o futuro, continuamos confiantes de que a nossa liderança em soluções de monitoramento da CUI está na vanguarda da transformação do setor, levando a eficiência e a segurança a novos patamares.
Ao unir tecnologia avançada com experiência enraizada e parcerias colaborativas, não estamos apenas respondendo aos desafios de hoje, mas moldando as soluções de amanhã.
