Montaje de jaulas de chapa metálica con robots guiados por visión
RESUMEN
El montaje de jaulas de chapa metálica de alta precisión es trabajo laborioso. Para reducir los costos de montaje y mejorar la eficiencia y calidad del mismo, la robótica es una opción óptima para construir el sistema de montaje automático por sus ventajas principales en cuanto a velocidad, precisión y flexibilidad. Aquí se presenta la tecnología robótica para el montaje de jaulas de chapa metálica para demostrar, verificar y optimizar las soluciones principales en la automatización del proceso de montaje personalizado en masa.
PLANTEAMIENTO DEL PROBLEMA
Los procesos de montaje de alta precisión de jaulas de chapa metálica son muy laboriosos y hay más de 52 operadores trabajando intensamente en el proceso. Como se muestra en la fig. 1, los separadores se montan a la jaula inferior para formar un subconjunto, luego el subconjunto se monta con el resorte de desenganche y la jaula superior para montar el conjunto de la jaula. Al parecer, es indispensable tener mucho cuidado en el montaje de jaulas, ya que el producto se puede deformar y rayar fácilmente. El grosor de la pieza de chapa metálica es de 0.25 mm y la precisión de montaje es inferior a 0.03 mm. Además, hay más de 100 números de piezas de productos que deben ser corroborados, el producto ilustrado en la fig. 1 es un producto característico de jaulas de SFP+ 1X4 y hay algunos otros productos como los 1XN y 2XN, clasificados en las familias de productos de SFP, SFP+, QSFP, ZQSFP, etc. Evidentemente, automatizar el proceso de montaje de jaulas es lidiar con un problema de automatización personalizada en masa de alta mezcla y bajo volumen. Además, los métodos convencionales de automatización con herramientas duras no serían adecuados en este caso para el requisito de montaje personalizado en masa.
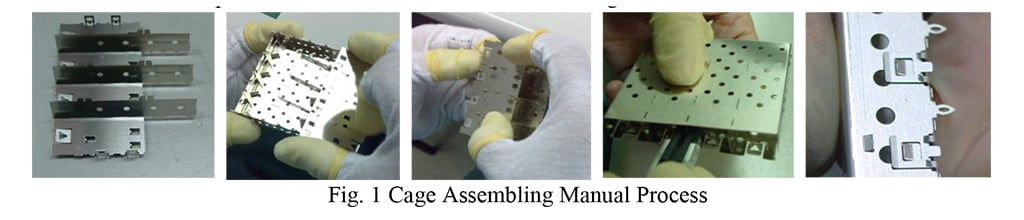
La robótica con sus principales ventajas en cuanto a velocidad, precisión y flexibilidad se considera una opción óptima para construir un sistema de montaje automático y flexible. Esta investigación explora las interesantes capacidades del robot/robótica y presenta las soluciones para el proceso de montaje personalizado en masa con robótica de jaulas de chapa metálica, que pueden generar un gran impacto empresarial y desarrollo tecnológico para TE. Para mejorar la fiabilidad y solidez del sistema de montaje robótico de jaulas, esta investigación también estudia los detalles del proceso de montaje y realiza dos diseños de experimentos (DoE) para optimizar el montaje del separador y la jaula inferior y el montaje de la jaula superior y el resorte de desenganche. El sistema de montaje robotizado y el método de optimización del proceso de montaje desarrollados a partir de esta investigación podrían aplicarse a otros procesos de montaje de producto en todas las unidades de negocio de TE para reducir significativamente el costo de montaje y mejorar la eficiencia y calidad del mismo.
MÉTODOS Y RESULTADOS
Introducción al robot industrial
El robot industrial se conoce normalmente como robot SCARA, robot de 6 ejes y robot Delta. El robot SCARA tiene 3 GDL (Grados de libertad) de traslación y 1 GDL de rotación, además se utiliza generalmente para realizar operaciones de recogida y colocación; el robot de 6 ejes tiene 3 GDL de traslación y 3 GDL de rotación y es tan versátil que puede usarse en diferentes procesos de fabricación y montaje. El robot Delta tiene una arquitectura paralela con 3 GDL de traslación y 1 GDL de rotación y se utiliza normalmente para realizar operaciones rápidas de recogida y colocación. Para el proceso de montaje de jaulas de chapa, el montaje del separador y de la jaula superior necesita tanto traslaciones como rotaciones para que la pieza siga una trayectoria de montaje para terminar de montar, por esto se prefiere el uso del robot de 6 ejes en este caso. La fig. 2 ilustra el típico robot de 6 ejes y la arquitectura del robot para estudiar la movilidad del efector final del robot. El robot industrial de 6 ejes también se conoce como Mecanismo 6-R (R: Junta rotativa), que puede separarse en dos partes: el brazo y la muñeca. El brazo del robot permite realizar traslaciones de 3 GDL y la muñeca del robot permite realizar rotaciones de 3 GDL. Con la coordinación entre el brazo y la muñeca del robot, el efector final del robot es capaz de alcanzar cualquier posición definida dentro de su espacio de trabajo y sería bastante ágil para cumplir con el proceso de montaje de jaulas de chapa metálica.
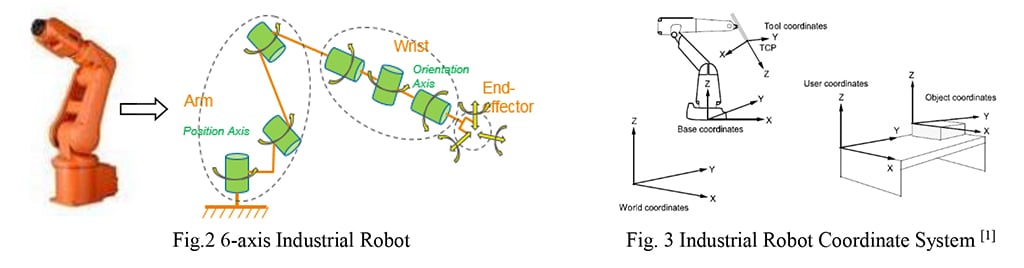
Hoy en día, el robot industrial está bien desarrollado con un método de modelado y control, así como con un buen lenguaje de programación de robots y con una interfaz de programación. No es necesario que el usuario final revise los detalles del control del motor, la cinemática directa/inversa o la dinámica. Pero es necesario desarrollar algunas técnicas con los lenguajes de programación de robots sobre el movimiento del robot y la planificación de la trayectoria. Con el efector final instalado en el robot, el movimiento y la planificación de trayectorias se basan en las coordenadas de la herramienta del robot que se definirían y se conectarían al efector final del robot. La fig. 3 ilustra algunos conceptos de los sistemas de coordenadas clave del robot. La regulación exacta de la trayectoria del robot consiste en controlar con precisión los objetivos críticos del robot. Especialmente en el proceso de montaje de jaulas, el paso para construir la trayectoria de montaje del robot puede ser la traslación lineal o la rotación, o incluso la combinación de ambas, es fundamental definir con precisión el tamaño del paso del robot con el objetivo de construir una trayectoria lisa de montaje para evitar cualquier interferencia. Para cada objetivo del robot, el efector final del robot deberá ser definido con precisión en su posición (x, y, z) y orientación (Ex, Ey, Ez), donde x, y, z son las coordenadas con respecto al sistema de coordenadas del objeto y Ex, Ey, Ez son los ángulos de Euler con respecto al sistema de coordenadas del objeto.
Robots guiados por visión
Para el montaje de alta precisión, el método tradicional de automatización consiste en diseñar y fabricar dispositivos mecánicos de alta precisión para realizar el posicionamiento de la pieza y desarrollar un mecanismo de alta precisión para ejecutar la carga y el montaje de la pieza, lo que sería un reto para el sistema mecánico mantener la precisión. Mientras que con el método de robótica guiada por visión se integra un sistema de visión como parte del sistema robótico para identificar con precisión la posición de la pieza agarrada en la herramienta del robot, entonces el robot/herramienta del robot traslada o rota la pieza de forma adaptativa basándose en la retroalimentación de la identificación de la visión para asegurar la precisión del montaje.
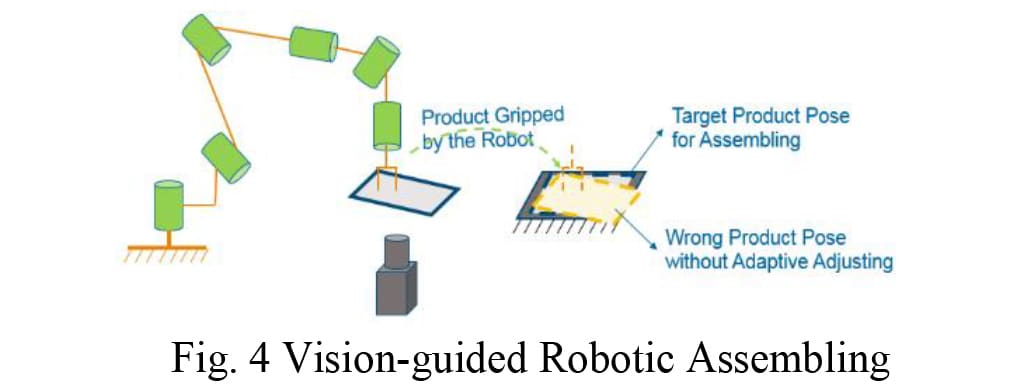
La fig. 4 ilustra un típico sistema de robots guiados por visión para una operación de montaje/recogida y colocación adaptativo. Como es posible que el robot no recoja el producto en la misma posición u orientación debido a algunos errores de posicionamiento, la postura constante del robot generada por el aprendizaje del robot podría fallar a la hora de ensamblar el producto, el sistema de visión sería muy útil para guiar al robot para ajustar adaptativamente la trayectoria de conjunto y así garantizar la fiabilidad y resistencia del sistema de montaje
El procedimiento para desarrollar el algoritmo de montaje adaptativo del robot consiste en crear primero el Modelo base como modelo de referencia y luego formular el modelo de cálculo de posición del objetivo para ajustar de forma adaptativa la posición del robot y así montar el producto con precisión. El modelo base se crea tomando la posición del robot para la captura de imágenes (XRb, YRb, ARb), la posición del producto identificada en la herramienta del robot (XCb, YCb, ACb) por el sistema de visión 2D y la posición maestra para montar el producto con precisión (XFb, YFb, AFb) como base de referencia, con la que se calcula la posición del objetivo del producto (XCFb, YCFb, ACFb) y es evidente que la posición del objetivo del producto es constante para montar el producto con precisión. Aquí, X/Y significa la posición, A significa el ángulo de rotación a lo largo del eje z, ya que aquí se usa el sistema de visión 2D, el componente de posición en el plano 2D se estudia aquí.
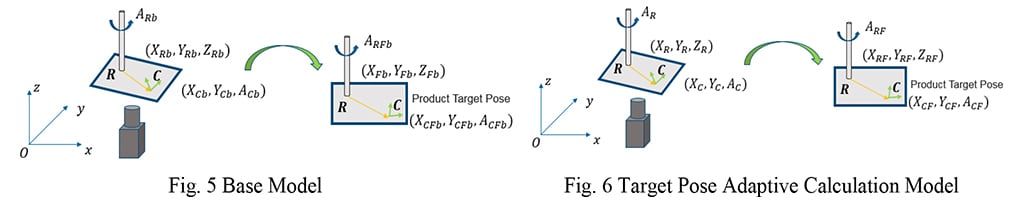
Como se muestra en la Fig. 4, la herramienta del robot agarra el producto en el punto R y la característica para representar la posición y orientación del producto en la herramienta del robot es el cuadro C, con la posición de aprendizaje del robot para montar el producto, la posición objetivo del producto para el montaje del producto se calcula basándose en la transformación plana del vector 풗푟푐 desde la pose de captura de la imagen a la pose de montaje y la pose de aprendizaje del robot para montar el producto. Por lo tanto, la posición del objetivo del producto se formula de la siguiente manera:

Donde, 풗푟푐 = (푋퐶푏 − 푋푅푏, 푌퐶푏 − 푌푅푏)푇.
La orientación del objetivo del producto para su conjunto se calcula en función de la orientación de la característica del producto ACb y la variación rotacional del robot ∆퐴푏 = 퐴푅퐹푏 − 퐴푅푏, como Eq. (2):
퐴퐶퐹푏 = 퐴퐶푏 + ∆퐴푏 (2)
La Posición del objetivo del robot adaptativo para el montaje del producto se formula con el modelo que se muestra en la fig. 6 y es fácil de conocer la posición del objetivo del producto, ya que es la misma con la base de referencia:
푋퐶퐹 = 푋퐶퐹푏, 푌퐶퐹 = 푌퐶퐹푏, 퐴퐶퐹 = 퐴퐶퐹푏 (3)
La posición del robot para captura de imágenes es (XR, YR, AR), la postura identificada del producto en la herramienta del robot es (XC, YC, AC), y la variación del ángulo de rotación del producto desde la posición de captura de imagen hasta la posición de montaje se formula como Eq. (4):
∆A = 퐴퐶퐹 − 퐴퐶 (4)
Por lo tanto, la orientación del robot objetivo para montar el producto se calcula de forma adaptativa con la orientación de la característica del producto identificado como Eq. (5):
퐴푅퐹 = 퐴푅 + ∆퐴 = 퐴푅 + 퐴퐶퐹 − 퐴퐶 (5)
La posición del robot objetivo para el montaje del producto se formula con base en la transformación plana del vector 풗푟푐 y la posición del objetivo del producto como Eq. (6):

Donde, 풗푟푐 = (푋C − 푋R, 푌C − 푌R)T
Con el sistema de visión para identificar con precisión la característica del producto como se muestra en la fig. 5 y fig. 6, la posición del robot para montar el producto con precisión no es una posición constante pero es una postura del robot adaptativo formulada por Eq. (5) y Eq. (6).
Para el proceso de montaje de jaulas de chapa metálica, la precisión de posicionamiento mecánico para el separador y el resorte de desenganche es de aproximadamente 0.3 mm y la precisión de posicionamiento mecánico de la jaula superior es de aproximadamente 0.1 mm en su sitio y casi 0.25 grados de orientación. Para cumplir con la precisión de montaje de 0.03 mm, se integra un sistema de visión con una precisión de posicionamiento de +/-0.003 mm para guiar de forma adaptativa al robot, como se muestra en la fig. 8. En combinación con la repetitividad del robot de +/-0.01 mm, la precisión general del sistema robótico para realizar el montaje es de aproximadamente 0.02 mm, lo que es suficiente para cumplir con el proceso de montaje de jaulas de chapa metálica.
Sistema robótico de montaje de jaulas de chapa metálica
Para desarrollar un sistema de automatización personalizada en masa que cubra el montaje de alta precisión de productos de jaula de alta mezcla y bajo volumen, el sistema de montaje de jaulas de chapa metálica (ver fig. 7-a) se construye con un robot de 6 ejes para realizar la carga y el montaje de la pieza, un sistema de visión para identificar con precisión la posición de la pieza agarrada a la herramienta del robot y al dispositivo de montaje. El robot está equipado con dos herramientas del robot, una de ellas es una pinza neumática para realizar la carga y el montaje del deparador y del resorte de desenganche, la otra es una ventosa neumática para realizar la carga y el montaje de la jaula inferior y la jaula superior. El dispositivo de montaje se transporta mediante un tornillo lineal entre la estación de montaje del separador y la estación de montaje de la jaula superior y del resorte de desenganche.
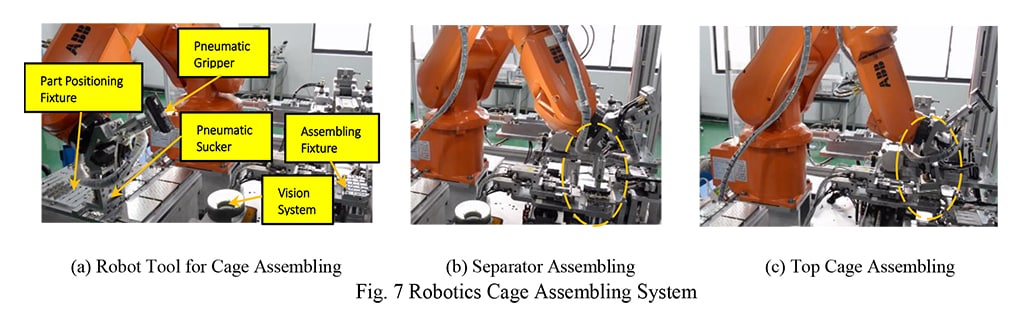
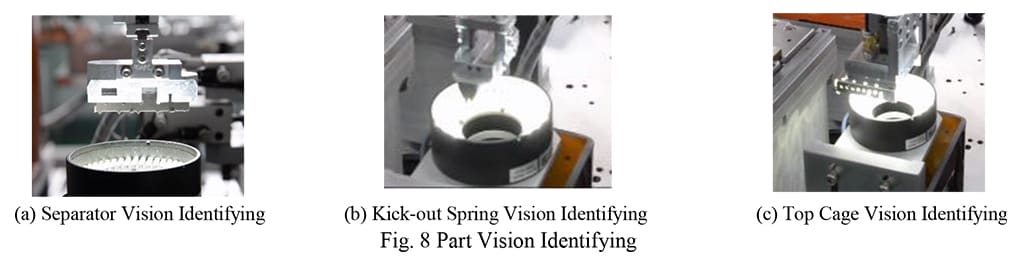
El robot carga primero la jaula inferior al dispositivo de montaje en la estación de montaje del separador y luego carga y monta los separadores respectivamente con la jaula inferior para hacer un submontaje, como se muestra en la fig. 7-b. Después, el tornillo lineal transporta el dispositivo de montaje con el submontaje a la estación de montaje del resorte de desenganche y de la jaula superior, donde el dispositivo de montaje se posiciona con precisión y los separadores se sujetan correctamente por el mecanismo de sujeción del separador para el montaje del resorte de desenganche y de la jaula superior, como se muestra en la fig. 7-c. Con el sistema de visión para identificar con precisión la posición de la pieza agarrada a la herramienta del robot, el separador, el resorte de desenganche y la jaula superior se ensamblan de forma adaptativa con las fórmulas desarrolladas por Eq. (5) y Eq. (6).
Optimización del proceso de montaje robótico
Con el objetivo de mejorar la fiabilidad y maximizar la capacidad del sistema robótico de montaje de jaulas de chapa metálica se han realizado dos Diseños de Experimentos (DoE) para optimizar el proceso de montaje. Uno de estos diseños es para el montaje del separador y de la jaula inferior, el otro es para el montaje del resorte de desenganche y de la jaula superior. Los factores principales para el proceso de montaje de alta precisión son, generalmente, el mecanismo de posicionamiento de piezas en el dispositivo de montaje y la trayectoria de montaje del robot.
Para la optimización del proceso de montaje del separador y de la jaula inferior, esta última está bien posicionada y fijada por el mecanismo de posicionamiento en el dispositivo de montaje. Como se ha comprobado, no hay un gran problema en el dispositivo de montaje para el montaje del separador, se han seleccionado otros dos factores (Velocidad de montaje y Trayectoria de montaje) para optimizar la tasa de rendimiento y el Pareto como se muestra en la fig. 9-a, que sugiere que la Trayectoria de montaje sea el factor efectivo que afecta considerablemente la tasa de rendimiento de montaje. Se ha logrado una tasa de rendimiento de montaje del separador óptima del 97 %, con la trayectoria de montaje del separador óptima mostrada en la Fig. 10-a y la Fig. 10-b. Debido a las diferencias en la estructura del separador, la trayectoria de montaje del separador #1 es diferente a la trayectoria de los separadores #2 y #3 para evitar cualquier interferencia con la jaula inferior.
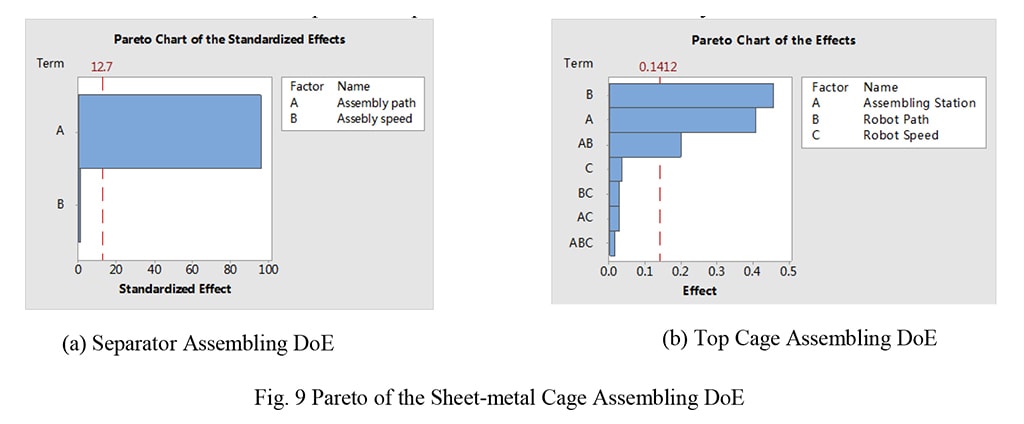
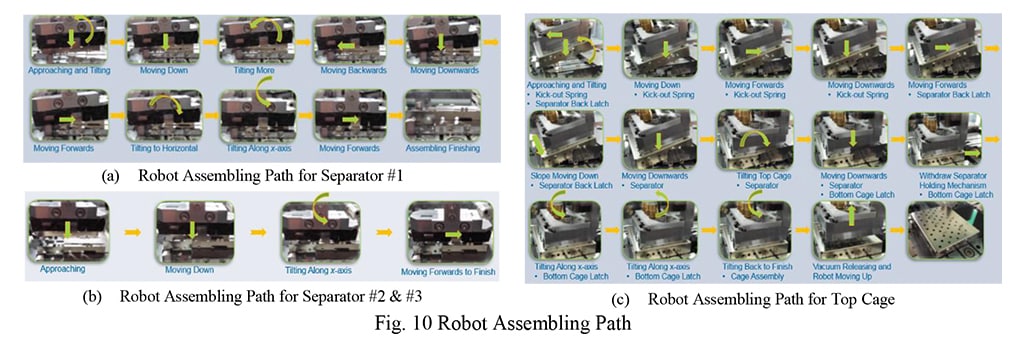
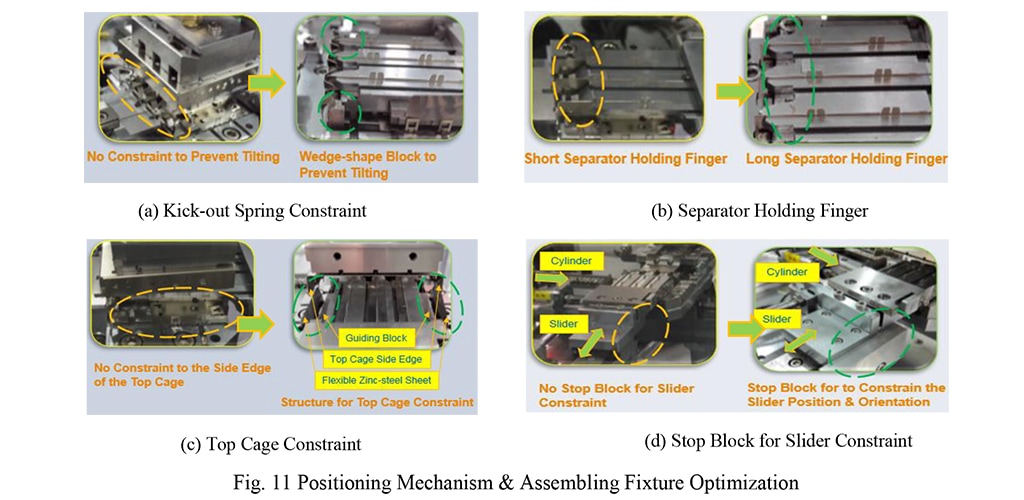
Para la optimización del montaje de la jaula superior, se han seleccionado tres factores para llevar a cabo el DoE del montaje y el Pareto como se muestra en la fig. 9-b, que ilustra la trayectoria del robot, el dispositivo de montaje y el mecanismo de posicionamiento y la interacción de los dos factores son los factores efectivos. Con la trayectoria óptima de montaje de la jaula superior como se muestra en la fig. 10-c y el mecanismo de posicionamiento óptimo y el dispositivo de montaje como se muestra en la fig. 11 se ha conseguido un Índice de rendimiento óptimo del 97 % en el montaje de la jaula superior. Como la jaula superior tiene que encajar bien con el muelle de salida, el separador y la jaula inferior para que el montaje se realice correctamente, cada uno de los pasos óptimos de montaje está bien diseñado para tener en cuenta los elementos críticos. Para que el mecanismo de posicionamiento y la optimización del dispositivo de montaje se coordinen con la trayectoria de montaje del robot a fin de mejorar la tasa de rendimiento del montaje, la restricción del resorte de desenganche ha sido perfeccionada para limitarla con un par de bloques de cuña con el fin de evitar que el resorte se incline por una ligera fuerza ejercida por la jaula superior, que podría resultar en el montaje NG de la jaula superior como se muestra en la fig. 11-a. El dedo de sujeción del separador se ha mejorado con dedos más largos para sostener con fuerza y precisión a fin de evitar cualquier vibración en el separador con alta velocidad, como se muestra en la fig. 11-b. La restricción de la jaula superior se ha mejorado al limitar los bordes laterales con el bloque de guía y la lámina flexible de acero galvanizado para asegurar la compatibilidad de la gran tolerancia (-0.1~0.7 mm) de la distancia entre los dos bordes laterales de la jaula superior, como se muestra en la fig. 11-c. Es posible que haya algunos errores de posición y rotación para los separadores y la jaula inferior al considerar las distancias entre el deslizador y su carril guía para alimentar y retirar el dedo de sujeción del separador con el cilindro neumático para presionar en los dedos de sujeción del separador a fin de sujetar el separador con firmeza. Por esta razón se añade un bloque de tope para limitar la posición y orientación del control deslizante para garantizar la precisión del posicionamiento del separador y de la jaula inferior en la estación de montaje, lo cual es importante para la fiabilidad y resistencia del montaje como se muestra en la fig. 11-d.
Sin la pérdida de la tasa de rendimiento de montaje, también se ha mejorado la eficiencia de montaje mediante la optimización de la velocidad del robot. Tabulador. 1 muestra el tiempo de ciclo óptimo para el montaje de cada pieza, donde la velocidad de desplazamiento del robot se optimiza a 2000 mm/s, la velocidad del robot para el montaje del separador y del resorte de desenganche se optimiza a 50 mm/s y la velocidad del robot para el montaje de la jaula superior se optimiza a 30 mm/s. El tiempo de ciclo óptimo cumple el requisito de la industrialización del proceso de montaje de jaulas.
Tabla 1
Artículo de montaje | Jaula inferior | Separador #1 | Separador #2 | Separador #3 | Resorte de desenganche | Jaula superior |
Tiempo de ciclo (s/pcs) | 2.2 | 4.6 | 3.2 | 3.4 | 4.0 | 7.0 |
ANÁLISIS Y PUNTOS CLAVE
Desarrollo de máquinas de producción para el montaje de jaulas de chapa metálica
Esta investigación realiza la verificación de la posibilidad del montaje robótico de jaulas de chapa metálica y lleva a cabo dos DoE sobre la optimización del proceso de montaje para mejorar la tasa de rendimiento de montaje y el tiempo de ciclo de montaje. Evidentemente, la tecnología ha sido verificada para cumplir con el objetivo de la industrialización y la plataforma de DoE se ha transferido a la Planta D&D en Zhuhai para ayudar en la producción en masa. Los últimos datos de producción demuestran que la plataforma está funcionando con una tasa de rendimiento del 98 %, con el ahorro de costos de mano de obra para 4 operadores (48,000 dólares de ahorro de costos al año). El siguiente paso es la construcción de la máquina de producción para el montaje de jaulas de chapa metálica y se prevé que la implementación de la máquina de producción con esta tecnología suponga un ahorro de costos de mano de obra de 520 mil dólares anuales para la unidad de negocios D&D de TE. Además, la tecnología robótica de montaje de jaulas de chapa metálica desarrollada aquí, mejoraría considerablemente las capacidades de TE en el montaje personalizado en masa a un nivel de alta precisión y se puede transformar para apoyar el desarrollo de la automatización del montaje personalizado en masa para otras unidades de negocios como automotriz, industrial, CPD, sensor, etc., lo que produciría un gran impacto comercial en todo TE.
AGRADECIMIENTOS
Ha sido un proceso emocionante trabajar en el desarrollo de la tecnología robótica de montaje de jaulas de chapa metálica. Los creadores están muy agradecidos por el apoyo y el patrocinio de los líderes de TE Global Operations y de la unidad de negocios D&D, especialmente con Philip Gilchrist, Darel Callis, Rolando Saavedra y Marshall Chen por las útiles sugerencias e instrucciones.
REFERENCIAS
[1] Manual técnico de referencia: Instrucciones RAPID, Funciones y tipos de datos, ABB documentación del robot M2004, rev H, RW5.15
Montaje de jaulas de chapa metálica con robots guiados por visión
RESUMEN
El montaje de jaulas de chapa metálica de alta precisión es trabajo laborioso. Para reducir los costos de montaje y mejorar la eficiencia y calidad del mismo, la robótica es una opción óptima para construir el sistema de montaje automático por sus ventajas principales en cuanto a velocidad, precisión y flexibilidad. Aquí se presenta la tecnología robótica para el montaje de jaulas de chapa metálica para demostrar, verificar y optimizar las soluciones principales en la automatización del proceso de montaje personalizado en masa.
PLANTEAMIENTO DEL PROBLEMA
Los procesos de montaje de alta precisión de jaulas de chapa metálica son muy laboriosos y hay más de 52 operadores trabajando intensamente en el proceso. Como se muestra en la fig. 1, los separadores se montan a la jaula inferior para formar un subconjunto, luego el subconjunto se monta con el resorte de desenganche y la jaula superior para montar el conjunto de la jaula. Al parecer, es indispensable tener mucho cuidado en el montaje de jaulas, ya que el producto se puede deformar y rayar fácilmente. El grosor de la pieza de chapa metálica es de 0.25 mm y la precisión de montaje es inferior a 0.03 mm. Además, hay más de 100 números de piezas de productos que deben ser corroborados, el producto ilustrado en la fig. 1 es un producto característico de jaulas de SFP+ 1X4 y hay algunos otros productos como los 1XN y 2XN, clasificados en las familias de productos de SFP, SFP+, QSFP, ZQSFP, etc. Evidentemente, automatizar el proceso de montaje de jaulas es lidiar con un problema de automatización personalizada en masa de alta mezcla y bajo volumen. Además, los métodos convencionales de automatización con herramientas duras no serían adecuados en este caso para el requisito de montaje personalizado en masa.
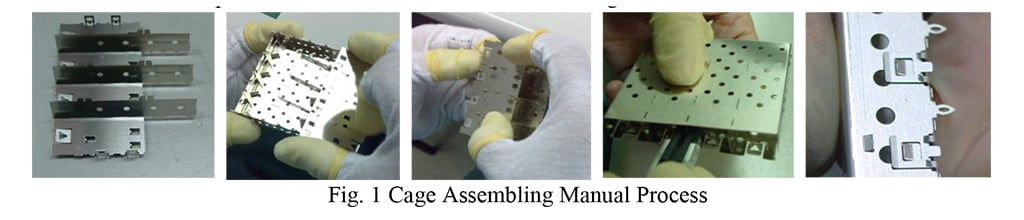
La robótica con sus principales ventajas en cuanto a velocidad, precisión y flexibilidad se considera una opción óptima para construir un sistema de montaje automático y flexible. Esta investigación explora las interesantes capacidades del robot/robótica y presenta las soluciones para el proceso de montaje personalizado en masa con robótica de jaulas de chapa metálica, que pueden generar un gran impacto empresarial y desarrollo tecnológico para TE. Para mejorar la fiabilidad y solidez del sistema de montaje robótico de jaulas, esta investigación también estudia los detalles del proceso de montaje y realiza dos diseños de experimentos (DoE) para optimizar el montaje del separador y la jaula inferior y el montaje de la jaula superior y el resorte de desenganche. El sistema de montaje robotizado y el método de optimización del proceso de montaje desarrollados a partir de esta investigación podrían aplicarse a otros procesos de montaje de producto en todas las unidades de negocio de TE para reducir significativamente el costo de montaje y mejorar la eficiencia y calidad del mismo.
MÉTODOS Y RESULTADOS
Introducción al robot industrial
El robot industrial se conoce normalmente como robot SCARA, robot de 6 ejes y robot Delta. El robot SCARA tiene 3 GDL (Grados de libertad) de traslación y 1 GDL de rotación, además se utiliza generalmente para realizar operaciones de recogida y colocación; el robot de 6 ejes tiene 3 GDL de traslación y 3 GDL de rotación y es tan versátil que puede usarse en diferentes procesos de fabricación y montaje. El robot Delta tiene una arquitectura paralela con 3 GDL de traslación y 1 GDL de rotación y se utiliza normalmente para realizar operaciones rápidas de recogida y colocación. Para el proceso de montaje de jaulas de chapa, el montaje del separador y de la jaula superior necesita tanto traslaciones como rotaciones para que la pieza siga una trayectoria de montaje para terminar de montar, por esto se prefiere el uso del robot de 6 ejes en este caso. La fig. 2 ilustra el típico robot de 6 ejes y la arquitectura del robot para estudiar la movilidad del efector final del robot. El robot industrial de 6 ejes también se conoce como Mecanismo 6-R (R: Junta rotativa), que puede separarse en dos partes: el brazo y la muñeca. El brazo del robot permite realizar traslaciones de 3 GDL y la muñeca del robot permite realizar rotaciones de 3 GDL. Con la coordinación entre el brazo y la muñeca del robot, el efector final del robot es capaz de alcanzar cualquier posición definida dentro de su espacio de trabajo y sería bastante ágil para cumplir con el proceso de montaje de jaulas de chapa metálica.
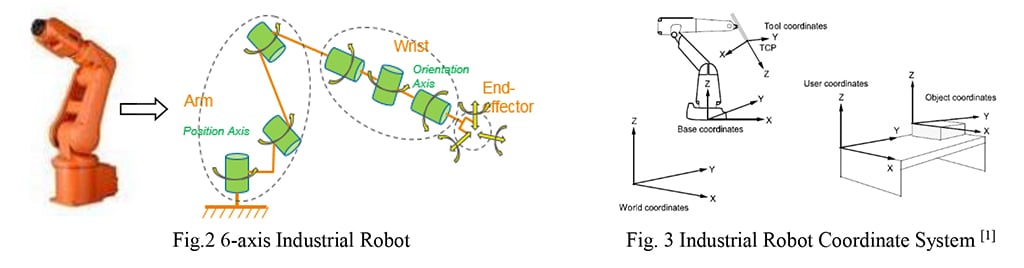
Hoy en día, el robot industrial está bien desarrollado con un método de modelado y control, así como con un buen lenguaje de programación de robots y con una interfaz de programación. No es necesario que el usuario final revise los detalles del control del motor, la cinemática directa/inversa o la dinámica. Pero es necesario desarrollar algunas técnicas con los lenguajes de programación de robots sobre el movimiento del robot y la planificación de la trayectoria. Con el efector final instalado en el robot, el movimiento y la planificación de trayectorias se basan en las coordenadas de la herramienta del robot que se definirían y se conectarían al efector final del robot. La fig. 3 ilustra algunos conceptos de los sistemas de coordenadas clave del robot. La regulación exacta de la trayectoria del robot consiste en controlar con precisión los objetivos críticos del robot. Especialmente en el proceso de montaje de jaulas, el paso para construir la trayectoria de montaje del robot puede ser la traslación lineal o la rotación, o incluso la combinación de ambas, es fundamental definir con precisión el tamaño del paso del robot con el objetivo de construir una trayectoria lisa de montaje para evitar cualquier interferencia. Para cada objetivo del robot, el efector final del robot deberá ser definido con precisión en su posición (x, y, z) y orientación (Ex, Ey, Ez), donde x, y, z son las coordenadas con respecto al sistema de coordenadas del objeto y Ex, Ey, Ez son los ángulos de Euler con respecto al sistema de coordenadas del objeto.
Robots guiados por visión
Para el montaje de alta precisión, el método tradicional de automatización consiste en diseñar y fabricar dispositivos mecánicos de alta precisión para realizar el posicionamiento de la pieza y desarrollar un mecanismo de alta precisión para ejecutar la carga y el montaje de la pieza, lo que sería un reto para el sistema mecánico mantener la precisión. Mientras que con el método de robótica guiada por visión se integra un sistema de visión como parte del sistema robótico para identificar con precisión la posición de la pieza agarrada en la herramienta del robot, entonces el robot/herramienta del robot traslada o rota la pieza de forma adaptativa basándose en la retroalimentación de la identificación de la visión para asegurar la precisión del montaje.
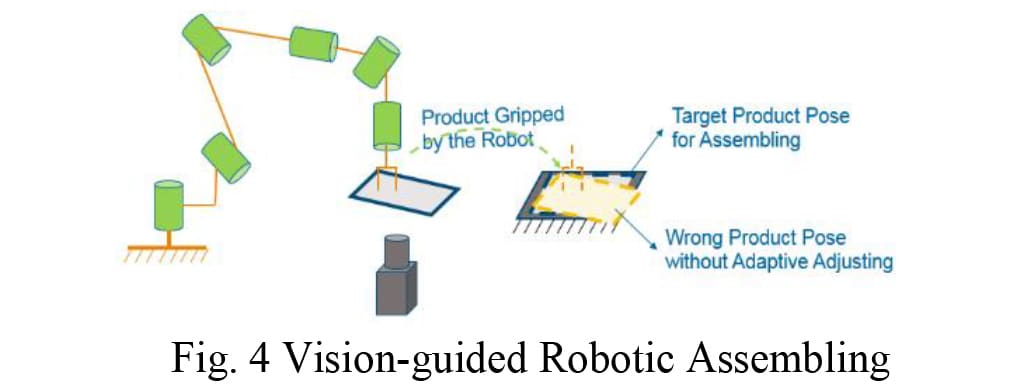
La fig. 4 ilustra un típico sistema de robots guiados por visión para una operación de montaje/recogida y colocación adaptativo. Como es posible que el robot no recoja el producto en la misma posición u orientación debido a algunos errores de posicionamiento, la postura constante del robot generada por el aprendizaje del robot podría fallar a la hora de ensamblar el producto, el sistema de visión sería muy útil para guiar al robot para ajustar adaptativamente la trayectoria de conjunto y así garantizar la fiabilidad y resistencia del sistema de montaje
El procedimiento para desarrollar el algoritmo de montaje adaptativo del robot consiste en crear primero el Modelo base como modelo de referencia y luego formular el modelo de cálculo de posición del objetivo para ajustar de forma adaptativa la posición del robot y así montar el producto con precisión. El modelo base se crea tomando la posición del robot para la captura de imágenes (XRb, YRb, ARb), la posición del producto identificada en la herramienta del robot (XCb, YCb, ACb) por el sistema de visión 2D y la posición maestra para montar el producto con precisión (XFb, YFb, AFb) como base de referencia, con la que se calcula la posición del objetivo del producto (XCFb, YCFb, ACFb) y es evidente que la posición del objetivo del producto es constante para montar el producto con precisión. Aquí, X/Y significa la posición, A significa el ángulo de rotación a lo largo del eje z, ya que aquí se usa el sistema de visión 2D, el componente de posición en el plano 2D se estudia aquí.
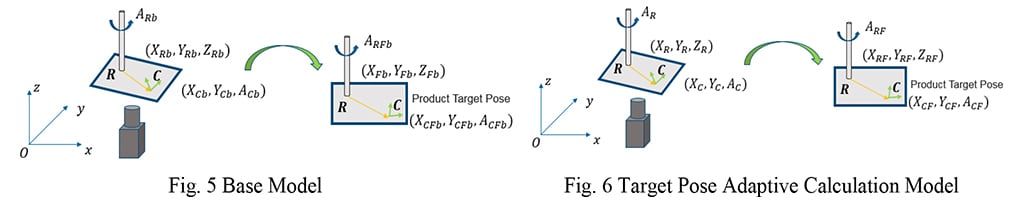
Como se muestra en la Fig. 4, la herramienta del robot agarra el producto en el punto R y la característica para representar la posición y orientación del producto en la herramienta del robot es el cuadro C, con la posición de aprendizaje del robot para montar el producto, la posición objetivo del producto para el montaje del producto se calcula basándose en la transformación plana del vector 풗푟푐 desde la pose de captura de la imagen a la pose de montaje y la pose de aprendizaje del robot para montar el producto. Por lo tanto, la posición del objetivo del producto se formula de la siguiente manera:

Donde, 풗푟푐 = (푋퐶푏 − 푋푅푏, 푌퐶푏 − 푌푅푏)푇.
La orientación del objetivo del producto para su conjunto se calcula en función de la orientación de la característica del producto ACb y la variación rotacional del robot ∆퐴푏 = 퐴푅퐹푏 − 퐴푅푏, como Eq. (2):
퐴퐶퐹푏 = 퐴퐶푏 + ∆퐴푏 (2)
La Posición del objetivo del robot adaptativo para el montaje del producto se formula con el modelo que se muestra en la fig. 6 y es fácil de conocer la posición del objetivo del producto, ya que es la misma con la base de referencia:
푋퐶퐹 = 푋퐶퐹푏, 푌퐶퐹 = 푌퐶퐹푏, 퐴퐶퐹 = 퐴퐶퐹푏 (3)
La posición del robot para captura de imágenes es (XR, YR, AR), la postura identificada del producto en la herramienta del robot es (XC, YC, AC), y la variación del ángulo de rotación del producto desde la posición de captura de imagen hasta la posición de montaje se formula como Eq. (4):
∆A = 퐴퐶퐹 − 퐴퐶 (4)
Por lo tanto, la orientación del robot objetivo para montar el producto se calcula de forma adaptativa con la orientación de la característica del producto identificado como Eq. (5):
퐴푅퐹 = 퐴푅 + ∆퐴 = 퐴푅 + 퐴퐶퐹 − 퐴퐶 (5)
La posición del robot objetivo para el montaje del producto se formula con base en la transformación plana del vector 풗푟푐 y la posición del objetivo del producto como Eq. (6):

Donde, 풗푟푐 = (푋C − 푋R, 푌C − 푌R)T
Con el sistema de visión para identificar con precisión la característica del producto como se muestra en la fig. 5 y fig. 6, la posición del robot para montar el producto con precisión no es una posición constante pero es una postura del robot adaptativo formulada por Eq. (5) y Eq. (6).
Para el proceso de montaje de jaulas de chapa metálica, la precisión de posicionamiento mecánico para el separador y el resorte de desenganche es de aproximadamente 0.3 mm y la precisión de posicionamiento mecánico de la jaula superior es de aproximadamente 0.1 mm en su sitio y casi 0.25 grados de orientación. Para cumplir con la precisión de montaje de 0.03 mm, se integra un sistema de visión con una precisión de posicionamiento de +/-0.003 mm para guiar de forma adaptativa al robot, como se muestra en la fig. 8. En combinación con la repetitividad del robot de +/-0.01 mm, la precisión general del sistema robótico para realizar el montaje es de aproximadamente 0.02 mm, lo que es suficiente para cumplir con el proceso de montaje de jaulas de chapa metálica.
Sistema robótico de montaje de jaulas de chapa metálica
Para desarrollar un sistema de automatización personalizada en masa que cubra el montaje de alta precisión de productos de jaula de alta mezcla y bajo volumen, el sistema de montaje de jaulas de chapa metálica (ver fig. 7-a) se construye con un robot de 6 ejes para realizar la carga y el montaje de la pieza, un sistema de visión para identificar con precisión la posición de la pieza agarrada a la herramienta del robot y al dispositivo de montaje. El robot está equipado con dos herramientas del robot, una de ellas es una pinza neumática para realizar la carga y el montaje del deparador y del resorte de desenganche, la otra es una ventosa neumática para realizar la carga y el montaje de la jaula inferior y la jaula superior. El dispositivo de montaje se transporta mediante un tornillo lineal entre la estación de montaje del separador y la estación de montaje de la jaula superior y del resorte de desenganche.
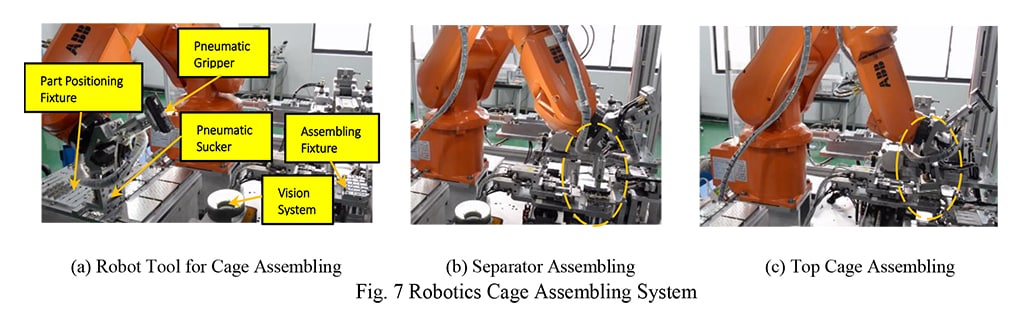
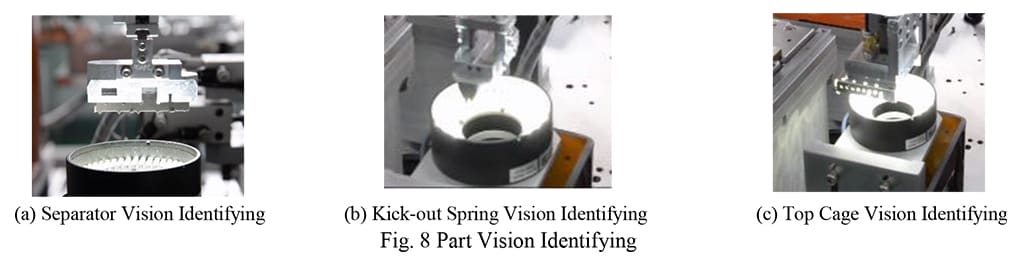
El robot carga primero la jaula inferior al dispositivo de montaje en la estación de montaje del separador y luego carga y monta los separadores respectivamente con la jaula inferior para hacer un submontaje, como se muestra en la fig. 7-b. Después, el tornillo lineal transporta el dispositivo de montaje con el submontaje a la estación de montaje del resorte de desenganche y de la jaula superior, donde el dispositivo de montaje se posiciona con precisión y los separadores se sujetan correctamente por el mecanismo de sujeción del separador para el montaje del resorte de desenganche y de la jaula superior, como se muestra en la fig. 7-c. Con el sistema de visión para identificar con precisión la posición de la pieza agarrada a la herramienta del robot, el separador, el resorte de desenganche y la jaula superior se ensamblan de forma adaptativa con las fórmulas desarrolladas por Eq. (5) y Eq. (6).
Optimización del proceso de montaje robótico
Con el objetivo de mejorar la fiabilidad y maximizar la capacidad del sistema robótico de montaje de jaulas de chapa metálica se han realizado dos Diseños de Experimentos (DoE) para optimizar el proceso de montaje. Uno de estos diseños es para el montaje del separador y de la jaula inferior, el otro es para el montaje del resorte de desenganche y de la jaula superior. Los factores principales para el proceso de montaje de alta precisión son, generalmente, el mecanismo de posicionamiento de piezas en el dispositivo de montaje y la trayectoria de montaje del robot.
Para la optimización del proceso de montaje del separador y de la jaula inferior, esta última está bien posicionada y fijada por el mecanismo de posicionamiento en el dispositivo de montaje. Como se ha comprobado, no hay un gran problema en el dispositivo de montaje para el montaje del separador, se han seleccionado otros dos factores (Velocidad de montaje y Trayectoria de montaje) para optimizar la tasa de rendimiento y el Pareto como se muestra en la fig. 9-a, que sugiere que la Trayectoria de montaje sea el factor efectivo que afecta considerablemente la tasa de rendimiento de montaje. Se ha logrado una tasa de rendimiento de montaje del separador óptima del 97 %, con la trayectoria de montaje del separador óptima mostrada en la Fig. 10-a y la Fig. 10-b. Debido a las diferencias en la estructura del separador, la trayectoria de montaje del separador #1 es diferente a la trayectoria de los separadores #2 y #3 para evitar cualquier interferencia con la jaula inferior.
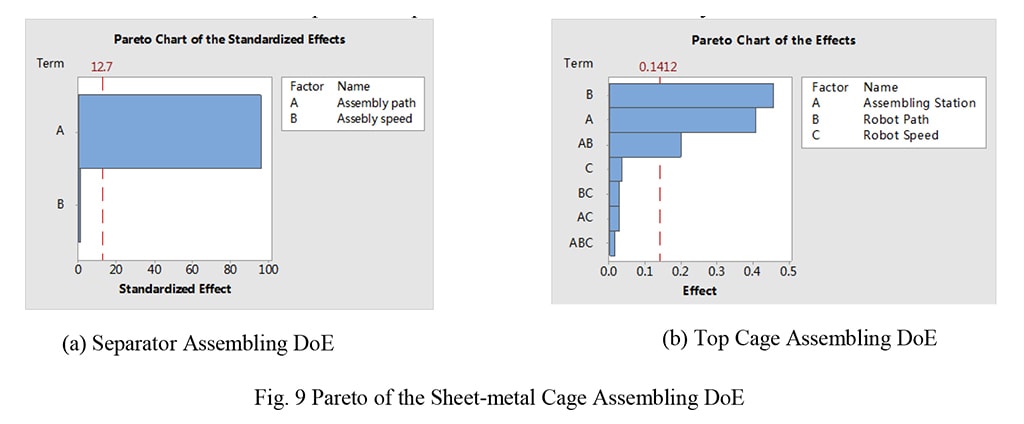
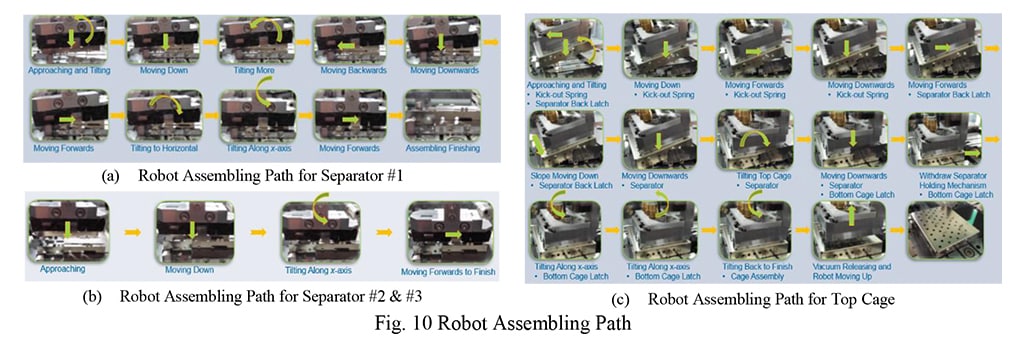
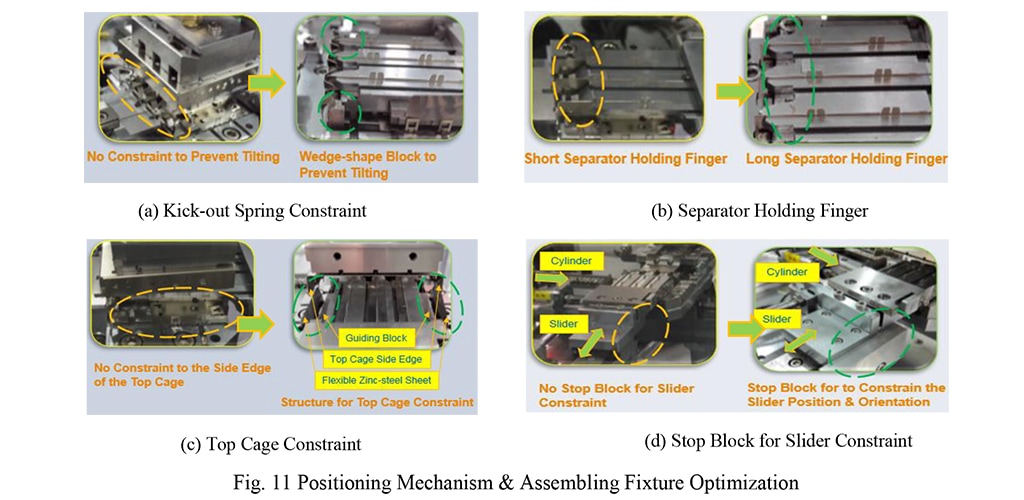
Para la optimización del montaje de la jaula superior, se han seleccionado tres factores para llevar a cabo el DoE del montaje y el Pareto como se muestra en la fig. 9-b, que ilustra la trayectoria del robot, el dispositivo de montaje y el mecanismo de posicionamiento y la interacción de los dos factores son los factores efectivos. Con la trayectoria óptima de montaje de la jaula superior como se muestra en la fig. 10-c y el mecanismo de posicionamiento óptimo y el dispositivo de montaje como se muestra en la fig. 11 se ha conseguido un Índice de rendimiento óptimo del 97 % en el montaje de la jaula superior. Como la jaula superior tiene que encajar bien con el muelle de salida, el separador y la jaula inferior para que el montaje se realice correctamente, cada uno de los pasos óptimos de montaje está bien diseñado para tener en cuenta los elementos críticos. Para que el mecanismo de posicionamiento y la optimización del dispositivo de montaje se coordinen con la trayectoria de montaje del robot a fin de mejorar la tasa de rendimiento del montaje, la restricción del resorte de desenganche ha sido perfeccionada para limitarla con un par de bloques de cuña con el fin de evitar que el resorte se incline por una ligera fuerza ejercida por la jaula superior, que podría resultar en el montaje NG de la jaula superior como se muestra en la fig. 11-a. El dedo de sujeción del separador se ha mejorado con dedos más largos para sostener con fuerza y precisión a fin de evitar cualquier vibración en el separador con alta velocidad, como se muestra en la fig. 11-b. La restricción de la jaula superior se ha mejorado al limitar los bordes laterales con el bloque de guía y la lámina flexible de acero galvanizado para asegurar la compatibilidad de la gran tolerancia (-0.1~0.7 mm) de la distancia entre los dos bordes laterales de la jaula superior, como se muestra en la fig. 11-c. Es posible que haya algunos errores de posición y rotación para los separadores y la jaula inferior al considerar las distancias entre el deslizador y su carril guía para alimentar y retirar el dedo de sujeción del separador con el cilindro neumático para presionar en los dedos de sujeción del separador a fin de sujetar el separador con firmeza. Por esta razón se añade un bloque de tope para limitar la posición y orientación del control deslizante para garantizar la precisión del posicionamiento del separador y de la jaula inferior en la estación de montaje, lo cual es importante para la fiabilidad y resistencia del montaje como se muestra en la fig. 11-d.
Sin la pérdida de la tasa de rendimiento de montaje, también se ha mejorado la eficiencia de montaje mediante la optimización de la velocidad del robot. Tabulador. 1 muestra el tiempo de ciclo óptimo para el montaje de cada pieza, donde la velocidad de desplazamiento del robot se optimiza a 2000 mm/s, la velocidad del robot para el montaje del separador y del resorte de desenganche se optimiza a 50 mm/s y la velocidad del robot para el montaje de la jaula superior se optimiza a 30 mm/s. El tiempo de ciclo óptimo cumple el requisito de la industrialización del proceso de montaje de jaulas.
Tabla 1
Artículo de montaje | Jaula inferior | Separador #1 | Separador #2 | Separador #3 | Resorte de desenganche | Jaula superior |
Tiempo de ciclo (s/pcs) | 2.2 | 4.6 | 3.2 | 3.4 | 4.0 | 7.0 |
ANÁLISIS Y PUNTOS CLAVE
Desarrollo de máquinas de producción para el montaje de jaulas de chapa metálica
Esta investigación realiza la verificación de la posibilidad del montaje robótico de jaulas de chapa metálica y lleva a cabo dos DoE sobre la optimización del proceso de montaje para mejorar la tasa de rendimiento de montaje y el tiempo de ciclo de montaje. Evidentemente, la tecnología ha sido verificada para cumplir con el objetivo de la industrialización y la plataforma de DoE se ha transferido a la Planta D&D en Zhuhai para ayudar en la producción en masa. Los últimos datos de producción demuestran que la plataforma está funcionando con una tasa de rendimiento del 98 %, con el ahorro de costos de mano de obra para 4 operadores (48,000 dólares de ahorro de costos al año). El siguiente paso es la construcción de la máquina de producción para el montaje de jaulas de chapa metálica y se prevé que la implementación de la máquina de producción con esta tecnología suponga un ahorro de costos de mano de obra de 520 mil dólares anuales para la unidad de negocios D&D de TE. Además, la tecnología robótica de montaje de jaulas de chapa metálica desarrollada aquí, mejoraría considerablemente las capacidades de TE en el montaje personalizado en masa a un nivel de alta precisión y se puede transformar para apoyar el desarrollo de la automatización del montaje personalizado en masa para otras unidades de negocios como automotriz, industrial, CPD, sensor, etc., lo que produciría un gran impacto comercial en todo TE.
AGRADECIMIENTOS
Ha sido un proceso emocionante trabajar en el desarrollo de la tecnología robótica de montaje de jaulas de chapa metálica. Los creadores están muy agradecidos por el apoyo y el patrocinio de los líderes de TE Global Operations y de la unidad de negocios D&D, especialmente con Philip Gilchrist, Darel Callis, Rolando Saavedra y Marshall Chen por las útiles sugerencias e instrucciones.
REFERENCIAS
[1] Manual técnico de referencia: Instrucciones RAPID, Funciones y tipos de datos, ABB documentación del robot M2004, rev H, RW5.15