Moldeo rápido de sellos elastoméricos funcionales para entornos hostiles
RESUMEN
Se demuestra un proceso rápido y de bajo costo para hacer prototipos funcionales o sellos elastoméricos de bajo volumen y alta mezcla (HMLV) para la comercialización utilizando moldes de plástico o polímeros impresos en 3D. Demostramos que este proceso simple y versátil permite moldear diferentes siliconas y fluorosiliconas de grado de producción de TE, para producir diversos diseños de sellos funcionales complejos con detalles finos y precisión que cumplen con los requisitos de nuestros clientes.
PLANTEAMIENTO DEL PROBLEMA
Los sellos elastoméricos son componentes esenciales que protegen los contactos eléctricos en conectores, sensores y conjuntos de cables de la corrosión causada por factores ambientales severos como la humedad, los gases, el polvo, los fluidos y otros productos químicos. TE ofrece una amplia cartera de diseños de sellos que incluyen sellos faciales, sellos familiares, sellos de cables, sellos periféricos y juntas tóricas. Los sellos deben cumplir con los exigentes requisitos del cliente para diferentes conectores y componentes eléctricos.
El objetivo de nuestro trabajo ha sido desarrollar un proceso versátil, rápido y de bajo costo para producir prototipos funcionales o sellos de HMLV para la comercialización que se puedan elaborar con materiales de grado de producción, desde caucho de silicona líquida (LSR) hasta caucho de alta consistencia (HCR) o fluorosiliconas de goma (consistencia de arcilla o material similar a la masilla), cauchos y otras clases de elastómeros. Además, los sellos rápidos deben poder calificarse según los tres criterios clave de forma, ajuste y función (es decir, capaces de cumplir con los requisitos de prueba dimensional, de ensamblaje y funcional). Un proceso rápido permite a los ingenieros de TE calificar rápidamente los sellos y, al mismo tiempo, comparar diferentes versiones de un diseño de sello en diferentes materiales con diversas propiedades (p. ej., dureza, propiedades de compresión, resistencia a la rotura, resistencia química). Los ingenieros de TE ahora no solo podrán entregar piezas rápidamente a los clientes finales, sino que también obtendrán una retroalimentación más rápida a partir de las pruebas de productos.
Aquí demostramos el uso de moldes de polímeros impresos en 3D para moldear sellos elastoméricos que pueden cumplir con los criterios mencionados anteriormente. La ventaja de este proceso radica en su simplicidad y adaptabilidad para trabajar con materiales tanto líquidos como de goma. Se han evaluado diversas tecnologías de impresión basadas en la fotopolimerización, a saber, la estereolitografía (SLA), la inyección de monómeros y el procesamiento digital de luz (DLP), así como diferentes materiales de molde, y se han identificado combinaciones apropiadas de impresoras y materiales para imprimir moldes de polímeros capaces de soportar condiciones de moldeo típicas (p. ej., alta temperatura y presión). Fuera de TE, los proveedores continúan desarrollando nuevos materiales de moldes de polímeros orientados al moldeo por inyección de termoplásticos [1].
También hemos evaluado el rendimiento funcional de los sellos elaborados con moldes de polímeros impresos frente a los moldes de metal, y el ahorro general de tiempo y costo del proceso en relación con la creación de prototipos utilizando moldes de polímeros. Además, destacamos la importancia de elegir adecuadamente el material para los moldes de polímeros y las condiciones para el procesamiento de moldes, así como las capacidades y las limitaciones de los moldes de polímeros.
MÉTODOS Y RESULTADOS
Impresoras y materiales
Las principales impresoras utilizadas en este estudio fueron impresoras comerciales de SLA, DLP y de inyección de monómeros y diversos materiales de resinas comerciales para imprimir moldes. En la sección de análisis se describirán aspectos como las diferencias en la calidad/precisión de la impresión, la rugosidad de la superficie del molde y la reutilización del molde.
Nuestro proceso es capaz de moldear grados comerciales de materiales de silicona y fluorosilicona, como cauchos de alta consistencia (HCR) (también conocidos como material de goma o siliconas sólidas) y siliconas líquidas (p. ej., de 2 componentes). Las temperaturas de curado de estos grados suelen ser mayores a los 150 ºC. Los grados utilizados en este estudio tienen una dureza Shore de 20 a 70 (p. ej., Shore A 20 o Shore A 50) y son adecuados para una exposición ambiental severa.
Descripción del proceso
Preparación de moldes de polímeros: Los moldes de múltiples cavidades se diseñaron utilizando modelos de sellos. Se utilizaron modelos de molde CAD 3D (formato .stl) para crear archivos de segmentos o capas para la impresión 3D. Después de la impresión 3D, los moldes (figura 1a) se limpiaron en disolventes orgánicos para eliminar todo exceso de resina en la superficie del molde, seguido de un proceso de desgasificación o tratamiento ultravioleta (UV), y luego tratamiento térmico a una temperatura adecuada para garantizar que los moldes impresos se curaran por completo. Llegamos a la conclusión de que es crucial curar por calor los materiales de los moldes de polímeros a una temperatura adecuada, de lo contrario, es posible que la silicona no se cure por completo en el molde de polímeros y permanezca pegajosa al tacto.
Moldes de metal: Los moldes de acero de 4 cavidades se prepararon mediante mecanizado convencional. Los moldes de acero se limpiaron con un disolvente desengrasante y luego se utilizaron para moldear silicona.
Proceso de moldeo: Los moldes de polímeros impresos en 3D se rociaron con un desmoldante a base de silicona antes del moldeo. Hemos extendido el uso de moldes impresos en 3D a varios procesos de moldeo, como el moldeo por inyección, transferencia y compresión. Hemos desarrollado experiencia en torno al diseño de moldes de polímeros, el ajuste del proceso de moldeo y el uso de enfoques no convencionales, dada la vida útil limitada de las herramientas debido al menor nivel de resistencia y conductividad térmica del material de los moldes de polímeros. Por lo general, el moldeo con herramientas de polímeros requeriría un tiempo de ciclo más alto, lo cual es aceptable a los fines de crear prototipos. Es fundamental elegir un material de molde adecuado, ya que los moldes de polímeros se sometieron a 180 ºC en nuestro proceso de curado de las siliconas.
Después del desmoldeo, los sellos se retiraron manualmente y luego se les realizó un tratamiento posterior durante 10 a 120 minutos más a 180 ºC para garantizar un curado completo. Dependiendo de la durabilidad de las características del núcleo, los moldes podrían ser de un solo uso o reutilizables. A modo de comparación, los sellos también se hicieron a partir de moldes metálicos mecanizados utilizando un proceso de moldeo estándar.
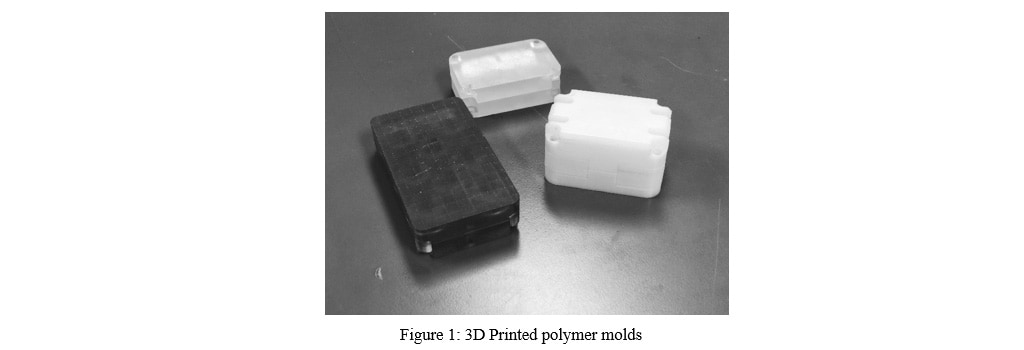
En la figura 2a-g se muestran ejemplos de sellos moldeados producidos utilizando diferentes materiales de moldes de polímeros impresos en una variedad de formas, tamaños, complejidad y tipos de materiales de silicona. Utilizando moldes de polímeros de alta resolución, pudimos moldear pequeños sellos de arandela (figura 2b-c) con un perfil de orificio complejo (diámetro del orificio: 1,01 mm, diámetro mínimo en el perfil del orificio: 0,53 mm, espesor de pared entre dos orificios: solo 0,25 mm). En la figura 2e-f se muestra un ejemplo de un diseño de sello automotriz con características pequeñas (espesor de pared más pequeño de 0,35 mm y pequeños orificios con 0,69 mm de diámetro) que se moldearon con éxito. En la figura 2g se muestran ejemplos de sellos automotrices de un solo cable, periféricos y de arandelas.
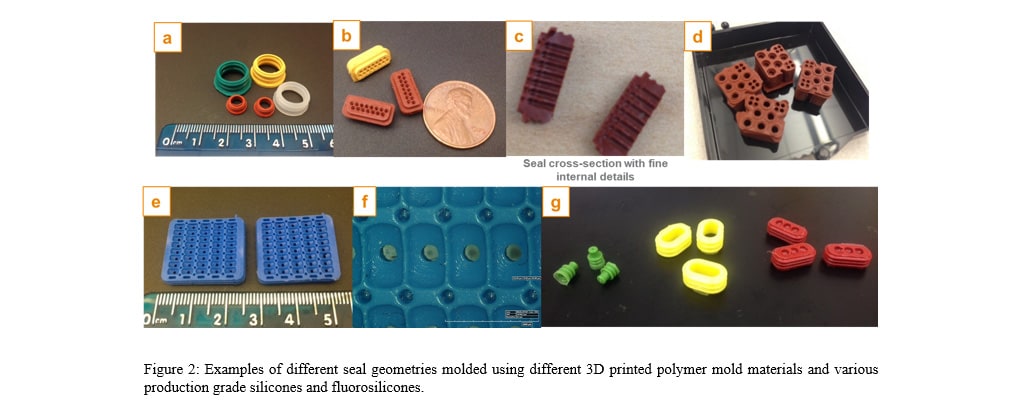
Resultados de las pruebas funcionales de sellos
Los sellos funcionales (figura 2a) para un cliente del ámbito aeroespacial, preparados utilizando a) moldes de polímeros impresos en 3D y b) moldes de acero, se ensamblaron en terminales de aluminio y luego se les insertaron y engarzaron los cables (véase la figura 3). Todos los sellos cumplieron con los requisitos de ensamblaje y dimensiones (los diámetros de las glándulas de sellado estaban dentro de la tolerancia permitida de 0,1 mm). Los terminales ensamblados se presurizaron en el extremo del cable y se les realizaron pruebas de fugas de aire bajo el agua a 1 bar y 2 bares. Las pruebas de fugas se realizaron antes y después de que las piezas se sometieran a) a 10 ciclos de choque térmico (de -65 ºC a 180 ºC) y b) al acondicionamiento de temperatura (180 ºC durante 5 días). Para la calificación del diseño de los sellos, el cliente estableció como requisito que debían aprobar todas las pruebas a 1 bar sin fugas.
Se hicieron sellos prototipo para cables de diversos tamaños y se evaluaron diferentes materiales de silicona y fluorosilicona mediante pruebas de fugas. Se preseleccionó un grado adecuado de material de silicona de HCR debido a que presentó un rendimiento aceptable en las pruebas de fugas. Los sellos obtenidos a partir de moldes de polímeros para cables de todos los tamaños pasaron la prueba de fugas antes y después del acondicionamiento por choque térmico, lo cual es un resultado muy alentador. Además, todos los sellos de moldes de polímeros para cables más grandes (AWG 000, 00, 0A, 1, 2, 3) pasaron la prueba de fugas después del acondicionamiento de temperatura de cinco días a 180 ºC. El proceso de creación de prototipos mediante el uso de moldes de polímeros también nos permitió calificar rápidamente los sellos AWG 8 más pequeños con un diseño modificado (pared más gruesa, 1,99 mm) que pasó todas las pruebas de fugas. Nuestros resultados muestran que los sellos prototipo obtenidos a partir de moldes de polímeros son capaces de cumplir con los requisitos funcionales tal como sucede con los moldes de metal.
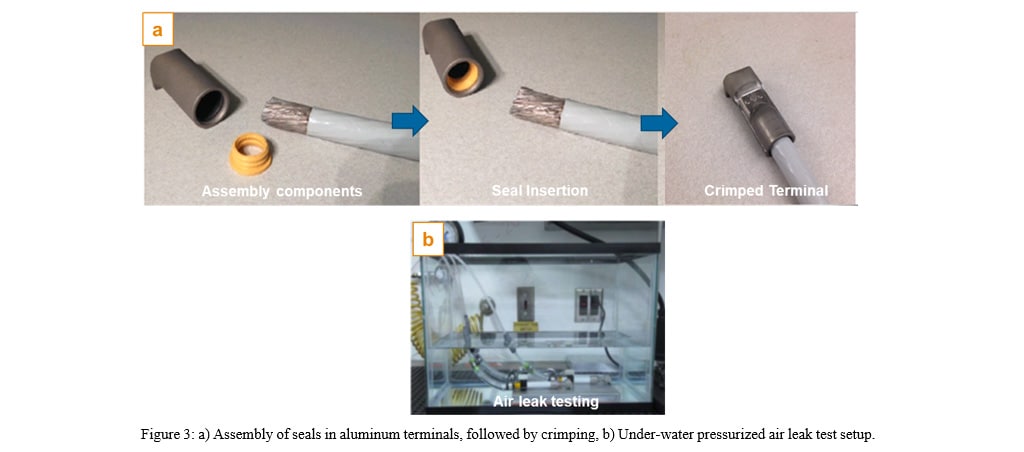
ANÁLISIS Y PUNTOS CLAVE
Capacidades y limitaciones de los moldes de polímeros impresos en 3D
El proceso de moldeo en el que se utilizan moldes de polímeros impresos en 3D de múltiples cavidades puede producir diseños de sellos intrincados y complejos que se pueden aplicar a la amplia cartera de sellos de TE. La cantidad de cavidades por molde de polímeros puede variar de 1 para sellos de mayor tamaño a más de 35 para sellos de menor tamaño. Las impresoras de SLA suelen utilizar un láser, que brinda la mayor precisión y la mejor resolución de características (cabe destacar que la SLA también puede imprimir características o esquinas nítidas), seguidas de cerca por las impresoras de DLP que utilizan tecnología de proyección de luz, a las que le siguen las impresoras de inyección de monómeros que curan fotopolímeros utilizando luz UV de banda ancha (obsérvense las esquinas nítidas con formas redondeadas). El exceso de curado de la resina cerca de los bordes de las características debido a la profundidad de penetración de la luz mayor a la deseada puede afectar la resolución y la precisión de la impresora.
La rugosidad de la superficie de los moldes impresos varía según la impresora y el material que se imprime. La rugosidad de la superficie es inherente a la impresión capa por capa (p. ej., espesor de capa de 0,05 mm para SLA) y al efecto de escalonamiento (superficies construidas en ángulo) que se puede observar claramente en la imagen microscópica de características de un molde de SLA (figura 4a). La topografía superficial de la superficie del molde de polímeros se replica claramente en los sellos moldeados (figura 4b). La rugosidad de la superficie del sello moldeado a partir de un molde de polímeros es mayor que la de los sellos obtenidos a partir de moldes de metal (figura 4c). En áreas donde el material de soporte se elimina de la superficie del molde puede haber mayor rugosidad. Es posible que, en algunas aplicaciones de sellado, la rugosidad adicional de la superficie no sea aceptable. Se debe tener en cuenta que también es posible utilizar herramientas híbridas, en las que los moldes de polímeros impresos se combinan con insertos de conectores de núcleo metálico para aplicaciones que requieren superficies de sellado de rugosidad superficial extremadamente baja.
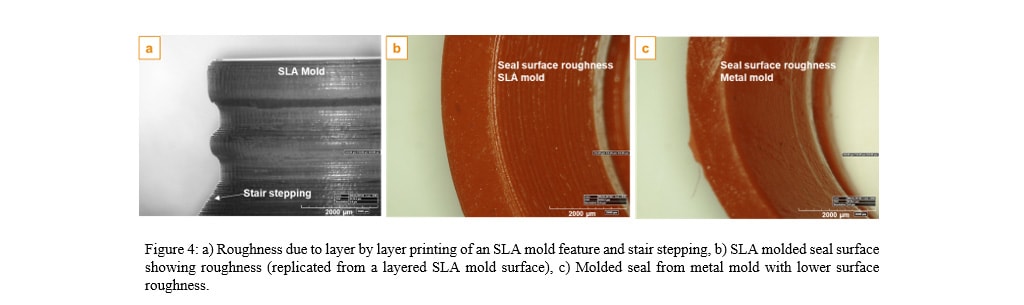
A diferencia de lo que sucede con los moldes de metal, la vida útil de los moldes de polímeros es limitada. Las propiedades mecánicas de los moldes de polímeros disminuyen significativamente a las temperaturas más altas, especialmente por encima de la temperatura de deflexión térmica [2]. La reutilización de los moldes depende en gran medida del tamaño mínimo de las características del núcleo, así como de los parámetros del proceso de moldeo, como la temperatura del molde, la presión, etc. Por ejemplo, los moldes con núcleos más grandes podrían usarse varias veces antes de que el molde de polímeros se agriete, mientras que la rotura de los núcleos más pequeños limitaría el número de disparos por molde. Para sellos con geometría extremadamente pequeña (que no se puede lograr mediante la impresión) o cuando se necesita un gran número de piezas, se sugiere utilizar herramientas híbridas (es decir, moldes de polímeros impresos con insertos de conectores de núcleo metálico), en lugar de moldes de polímeros de sacrificio o de un solo uso.
Costo y tiempo
Nuestros costos de impresión de moldes internos fueron significativamente más bajos para los moldes de polímeros impresos con múltiples cavidades en comparación con los moldes de metal mecanizados de un proveedor externo. Para los moldes impresos, el tiempo total necesario desde el diseño del molde hasta los sellos moldeados fue de 2 semanas frente a 8 a 10 semanas para un proveedor externo.
RESUMEN
En resumen, hemos desarrollado una capacidad única para el moldeo rápido de sellos en diferentes siliconas y fluorosiliconas de grado de producción de TE utilizando moldes de polímeros impresos en 3D. Lo más importante para esta capacidad es la experiencia en torno al diseño de moldes de polímeros, el ajuste del proceso de moldeo y el uso de enfoques no convencionales, dada la vida útil limitada de las herramientas del material de los moldes de polímeros. La rápida capacidad de respuesta desde el diseño CAD hasta la producción de sellos completamente funcionales ayuda a los ingenieros de TE a calificar rápidamente los sellos y, al mismo tiempo, comparar diversos diseños o materiales de sellos y entregar piezas rápidamente a los clientes finales para obtener una retroalimentación más rápida de las pruebas de los productos. Nuestro proceso de moldeo rápido es una herramienta valiosa que puede ofrecer ahorros significativos de costo y tiempo para producir prototipos completamente funcionales o sellos de HMLV que cumplan con todos los requisitos del cliente.
AGRADECIMIENTOS
Los autores desean agradecer a Martin Bayes, John Wasserbauer y Bob Zubrickie (Tecnología Corporativa), Nicholas Ruffini, Kenneth Dowhower (Aplicaciones Aeroespaciales, de Defensa y Marítimas) y Galen Martin (Industria Automotriz) por su valioso apoyo a este trabajo.
REFERENCIAS
[1] L. Zonder, N. Sella, "Precision Prototyping: The role of 3D printed molds in the injection molding industry" (Creación de prototipos de precisión: El rol de los moldes impresos en 3D en la industria de moldeo por inyección), Stratasys.
[2] G. A. Mendible, “Applications of transient cooling simulations in injection molding” (Aplicaciones de las simulaciones de refrigeración transitoria en el moldeo por inyección), Tesis de doctorado, Universidad de Massachusetts Lowell, 2015.
Moldeo rápido de sellos elastoméricos funcionales para entornos hostiles
RESUMEN
Se demuestra un proceso rápido y de bajo costo para hacer prototipos funcionales o sellos elastoméricos de bajo volumen y alta mezcla (HMLV) para la comercialización utilizando moldes de plástico o polímeros impresos en 3D. Demostramos que este proceso simple y versátil permite moldear diferentes siliconas y fluorosiliconas de grado de producción de TE, para producir diversos diseños de sellos funcionales complejos con detalles finos y precisión que cumplen con los requisitos de nuestros clientes.
PLANTEAMIENTO DEL PROBLEMA
Los sellos elastoméricos son componentes esenciales que protegen los contactos eléctricos en conectores, sensores y conjuntos de cables de la corrosión causada por factores ambientales severos como la humedad, los gases, el polvo, los fluidos y otros productos químicos. TE ofrece una amplia cartera de diseños de sellos que incluyen sellos faciales, sellos familiares, sellos de cables, sellos periféricos y juntas tóricas. Los sellos deben cumplir con los exigentes requisitos del cliente para diferentes conectores y componentes eléctricos.
El objetivo de nuestro trabajo ha sido desarrollar un proceso versátil, rápido y de bajo costo para producir prototipos funcionales o sellos de HMLV para la comercialización que se puedan elaborar con materiales de grado de producción, desde caucho de silicona líquida (LSR) hasta caucho de alta consistencia (HCR) o fluorosiliconas de goma (consistencia de arcilla o material similar a la masilla), cauchos y otras clases de elastómeros. Además, los sellos rápidos deben poder calificarse según los tres criterios clave de forma, ajuste y función (es decir, capaces de cumplir con los requisitos de prueba dimensional, de ensamblaje y funcional). Un proceso rápido permite a los ingenieros de TE calificar rápidamente los sellos y, al mismo tiempo, comparar diferentes versiones de un diseño de sello en diferentes materiales con diversas propiedades (p. ej., dureza, propiedades de compresión, resistencia a la rotura, resistencia química). Los ingenieros de TE ahora no solo podrán entregar piezas rápidamente a los clientes finales, sino que también obtendrán una retroalimentación más rápida a partir de las pruebas de productos.
Aquí demostramos el uso de moldes de polímeros impresos en 3D para moldear sellos elastoméricos que pueden cumplir con los criterios mencionados anteriormente. La ventaja de este proceso radica en su simplicidad y adaptabilidad para trabajar con materiales tanto líquidos como de goma. Se han evaluado diversas tecnologías de impresión basadas en la fotopolimerización, a saber, la estereolitografía (SLA), la inyección de monómeros y el procesamiento digital de luz (DLP), así como diferentes materiales de molde, y se han identificado combinaciones apropiadas de impresoras y materiales para imprimir moldes de polímeros capaces de soportar condiciones de moldeo típicas (p. ej., alta temperatura y presión). Fuera de TE, los proveedores continúan desarrollando nuevos materiales de moldes de polímeros orientados al moldeo por inyección de termoplásticos [1].
También hemos evaluado el rendimiento funcional de los sellos elaborados con moldes de polímeros impresos frente a los moldes de metal, y el ahorro general de tiempo y costo del proceso en relación con la creación de prototipos utilizando moldes de polímeros. Además, destacamos la importancia de elegir adecuadamente el material para los moldes de polímeros y las condiciones para el procesamiento de moldes, así como las capacidades y las limitaciones de los moldes de polímeros.
MÉTODOS Y RESULTADOS
Impresoras y materiales
Las principales impresoras utilizadas en este estudio fueron impresoras comerciales de SLA, DLP y de inyección de monómeros y diversos materiales de resinas comerciales para imprimir moldes. En la sección de análisis se describirán aspectos como las diferencias en la calidad/precisión de la impresión, la rugosidad de la superficie del molde y la reutilización del molde.
Nuestro proceso es capaz de moldear grados comerciales de materiales de silicona y fluorosilicona, como cauchos de alta consistencia (HCR) (también conocidos como material de goma o siliconas sólidas) y siliconas líquidas (p. ej., de 2 componentes). Las temperaturas de curado de estos grados suelen ser mayores a los 150 ºC. Los grados utilizados en este estudio tienen una dureza Shore de 20 a 70 (p. ej., Shore A 20 o Shore A 50) y son adecuados para una exposición ambiental severa.
Descripción del proceso
Preparación de moldes de polímeros: Los moldes de múltiples cavidades se diseñaron utilizando modelos de sellos. Se utilizaron modelos de molde CAD 3D (formato .stl) para crear archivos de segmentos o capas para la impresión 3D. Después de la impresión 3D, los moldes (figura 1a) se limpiaron en disolventes orgánicos para eliminar todo exceso de resina en la superficie del molde, seguido de un proceso de desgasificación o tratamiento ultravioleta (UV), y luego tratamiento térmico a una temperatura adecuada para garantizar que los moldes impresos se curaran por completo. Llegamos a la conclusión de que es crucial curar por calor los materiales de los moldes de polímeros a una temperatura adecuada, de lo contrario, es posible que la silicona no se cure por completo en el molde de polímeros y permanezca pegajosa al tacto.
Moldes de metal: Los moldes de acero de 4 cavidades se prepararon mediante mecanizado convencional. Los moldes de acero se limpiaron con un disolvente desengrasante y luego se utilizaron para moldear silicona.
Proceso de moldeo: Los moldes de polímeros impresos en 3D se rociaron con un desmoldante a base de silicona antes del moldeo. Hemos extendido el uso de moldes impresos en 3D a varios procesos de moldeo, como el moldeo por inyección, transferencia y compresión. Hemos desarrollado experiencia en torno al diseño de moldes de polímeros, el ajuste del proceso de moldeo y el uso de enfoques no convencionales, dada la vida útil limitada de las herramientas debido al menor nivel de resistencia y conductividad térmica del material de los moldes de polímeros. Por lo general, el moldeo con herramientas de polímeros requeriría un tiempo de ciclo más alto, lo cual es aceptable a los fines de crear prototipos. Es fundamental elegir un material de molde adecuado, ya que los moldes de polímeros se sometieron a 180 ºC en nuestro proceso de curado de las siliconas.
Después del desmoldeo, los sellos se retiraron manualmente y luego se les realizó un tratamiento posterior durante 10 a 120 minutos más a 180 ºC para garantizar un curado completo. Dependiendo de la durabilidad de las características del núcleo, los moldes podrían ser de un solo uso o reutilizables. A modo de comparación, los sellos también se hicieron a partir de moldes metálicos mecanizados utilizando un proceso de moldeo estándar.
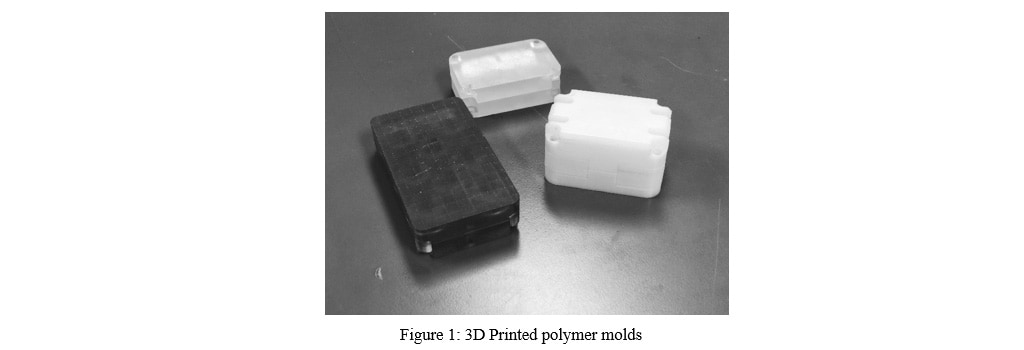
En la figura 2a-g se muestran ejemplos de sellos moldeados producidos utilizando diferentes materiales de moldes de polímeros impresos en una variedad de formas, tamaños, complejidad y tipos de materiales de silicona. Utilizando moldes de polímeros de alta resolución, pudimos moldear pequeños sellos de arandela (figura 2b-c) con un perfil de orificio complejo (diámetro del orificio: 1,01 mm, diámetro mínimo en el perfil del orificio: 0,53 mm, espesor de pared entre dos orificios: solo 0,25 mm). En la figura 2e-f se muestra un ejemplo de un diseño de sello automotriz con características pequeñas (espesor de pared más pequeño de 0,35 mm y pequeños orificios con 0,69 mm de diámetro) que se moldearon con éxito. En la figura 2g se muestran ejemplos de sellos automotrices de un solo cable, periféricos y de arandelas.
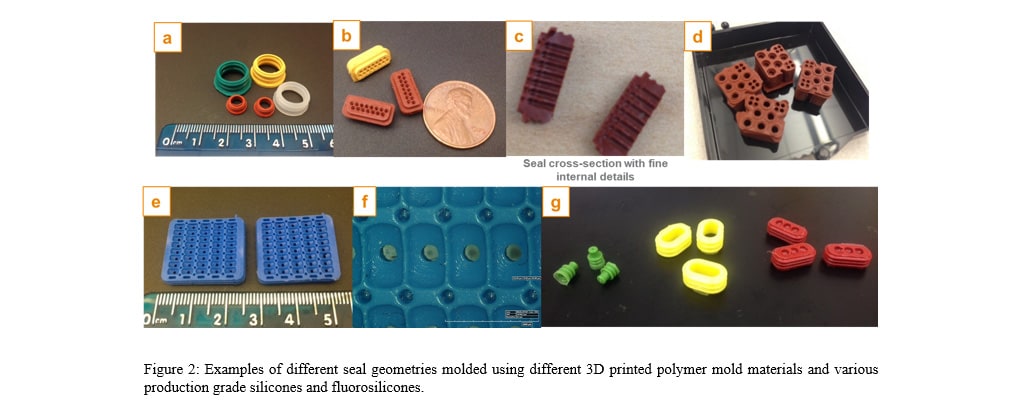
Resultados de las pruebas funcionales de sellos
Los sellos funcionales (figura 2a) para un cliente del ámbito aeroespacial, preparados utilizando a) moldes de polímeros impresos en 3D y b) moldes de acero, se ensamblaron en terminales de aluminio y luego se les insertaron y engarzaron los cables (véase la figura 3). Todos los sellos cumplieron con los requisitos de ensamblaje y dimensiones (los diámetros de las glándulas de sellado estaban dentro de la tolerancia permitida de 0,1 mm). Los terminales ensamblados se presurizaron en el extremo del cable y se les realizaron pruebas de fugas de aire bajo el agua a 1 bar y 2 bares. Las pruebas de fugas se realizaron antes y después de que las piezas se sometieran a) a 10 ciclos de choque térmico (de -65 ºC a 180 ºC) y b) al acondicionamiento de temperatura (180 ºC durante 5 días). Para la calificación del diseño de los sellos, el cliente estableció como requisito que debían aprobar todas las pruebas a 1 bar sin fugas.
Se hicieron sellos prototipo para cables de diversos tamaños y se evaluaron diferentes materiales de silicona y fluorosilicona mediante pruebas de fugas. Se preseleccionó un grado adecuado de material de silicona de HCR debido a que presentó un rendimiento aceptable en las pruebas de fugas. Los sellos obtenidos a partir de moldes de polímeros para cables de todos los tamaños pasaron la prueba de fugas antes y después del acondicionamiento por choque térmico, lo cual es un resultado muy alentador. Además, todos los sellos de moldes de polímeros para cables más grandes (AWG 000, 00, 0A, 1, 2, 3) pasaron la prueba de fugas después del acondicionamiento de temperatura de cinco días a 180 ºC. El proceso de creación de prototipos mediante el uso de moldes de polímeros también nos permitió calificar rápidamente los sellos AWG 8 más pequeños con un diseño modificado (pared más gruesa, 1,99 mm) que pasó todas las pruebas de fugas. Nuestros resultados muestran que los sellos prototipo obtenidos a partir de moldes de polímeros son capaces de cumplir con los requisitos funcionales tal como sucede con los moldes de metal.
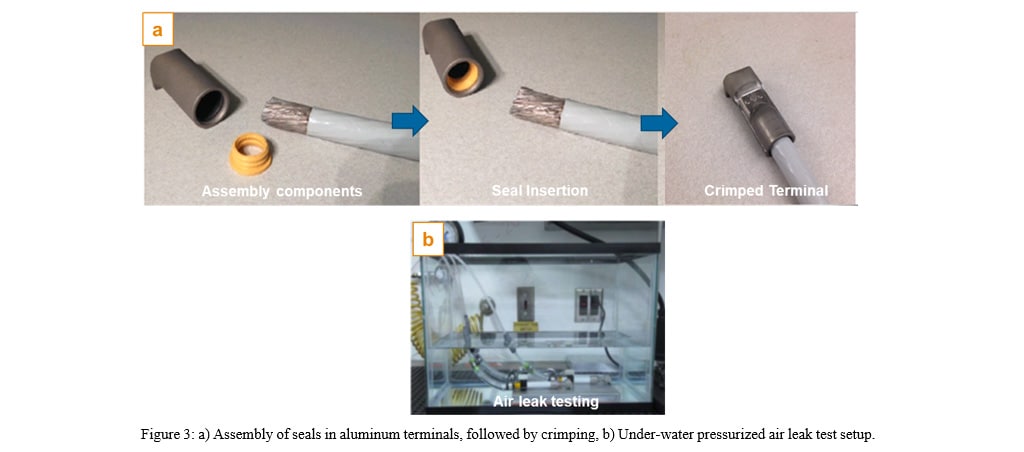
ANÁLISIS Y PUNTOS CLAVE
Capacidades y limitaciones de los moldes de polímeros impresos en 3D
El proceso de moldeo en el que se utilizan moldes de polímeros impresos en 3D de múltiples cavidades puede producir diseños de sellos intrincados y complejos que se pueden aplicar a la amplia cartera de sellos de TE. La cantidad de cavidades por molde de polímeros puede variar de 1 para sellos de mayor tamaño a más de 35 para sellos de menor tamaño. Las impresoras de SLA suelen utilizar un láser, que brinda la mayor precisión y la mejor resolución de características (cabe destacar que la SLA también puede imprimir características o esquinas nítidas), seguidas de cerca por las impresoras de DLP que utilizan tecnología de proyección de luz, a las que le siguen las impresoras de inyección de monómeros que curan fotopolímeros utilizando luz UV de banda ancha (obsérvense las esquinas nítidas con formas redondeadas). El exceso de curado de la resina cerca de los bordes de las características debido a la profundidad de penetración de la luz mayor a la deseada puede afectar la resolución y la precisión de la impresora.
La rugosidad de la superficie de los moldes impresos varía según la impresora y el material que se imprime. La rugosidad de la superficie es inherente a la impresión capa por capa (p. ej., espesor de capa de 0,05 mm para SLA) y al efecto de escalonamiento (superficies construidas en ángulo) que se puede observar claramente en la imagen microscópica de características de un molde de SLA (figura 4a). La topografía superficial de la superficie del molde de polímeros se replica claramente en los sellos moldeados (figura 4b). La rugosidad de la superficie del sello moldeado a partir de un molde de polímeros es mayor que la de los sellos obtenidos a partir de moldes de metal (figura 4c). En áreas donde el material de soporte se elimina de la superficie del molde puede haber mayor rugosidad. Es posible que, en algunas aplicaciones de sellado, la rugosidad adicional de la superficie no sea aceptable. Se debe tener en cuenta que también es posible utilizar herramientas híbridas, en las que los moldes de polímeros impresos se combinan con insertos de conectores de núcleo metálico para aplicaciones que requieren superficies de sellado de rugosidad superficial extremadamente baja.
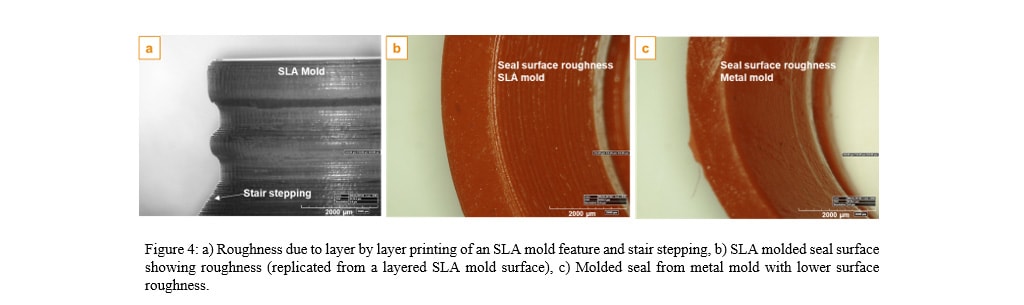
A diferencia de lo que sucede con los moldes de metal, la vida útil de los moldes de polímeros es limitada. Las propiedades mecánicas de los moldes de polímeros disminuyen significativamente a las temperaturas más altas, especialmente por encima de la temperatura de deflexión térmica [2]. La reutilización de los moldes depende en gran medida del tamaño mínimo de las características del núcleo, así como de los parámetros del proceso de moldeo, como la temperatura del molde, la presión, etc. Por ejemplo, los moldes con núcleos más grandes podrían usarse varias veces antes de que el molde de polímeros se agriete, mientras que la rotura de los núcleos más pequeños limitaría el número de disparos por molde. Para sellos con geometría extremadamente pequeña (que no se puede lograr mediante la impresión) o cuando se necesita un gran número de piezas, se sugiere utilizar herramientas híbridas (es decir, moldes de polímeros impresos con insertos de conectores de núcleo metálico), en lugar de moldes de polímeros de sacrificio o de un solo uso.
Costo y tiempo
Nuestros costos de impresión de moldes internos fueron significativamente más bajos para los moldes de polímeros impresos con múltiples cavidades en comparación con los moldes de metal mecanizados de un proveedor externo. Para los moldes impresos, el tiempo total necesario desde el diseño del molde hasta los sellos moldeados fue de 2 semanas frente a 8 a 10 semanas para un proveedor externo.
RESUMEN
En resumen, hemos desarrollado una capacidad única para el moldeo rápido de sellos en diferentes siliconas y fluorosiliconas de grado de producción de TE utilizando moldes de polímeros impresos en 3D. Lo más importante para esta capacidad es la experiencia en torno al diseño de moldes de polímeros, el ajuste del proceso de moldeo y el uso de enfoques no convencionales, dada la vida útil limitada de las herramientas del material de los moldes de polímeros. La rápida capacidad de respuesta desde el diseño CAD hasta la producción de sellos completamente funcionales ayuda a los ingenieros de TE a calificar rápidamente los sellos y, al mismo tiempo, comparar diversos diseños o materiales de sellos y entregar piezas rápidamente a los clientes finales para obtener una retroalimentación más rápida de las pruebas de los productos. Nuestro proceso de moldeo rápido es una herramienta valiosa que puede ofrecer ahorros significativos de costo y tiempo para producir prototipos completamente funcionales o sellos de HMLV que cumplan con todos los requisitos del cliente.
AGRADECIMIENTOS
Los autores desean agradecer a Martin Bayes, John Wasserbauer y Bob Zubrickie (Tecnología Corporativa), Nicholas Ruffini, Kenneth Dowhower (Aplicaciones Aeroespaciales, de Defensa y Marítimas) y Galen Martin (Industria Automotriz) por su valioso apoyo a este trabajo.
REFERENCIAS
[1] L. Zonder, N. Sella, "Precision Prototyping: The role of 3D printed molds in the injection molding industry" (Creación de prototipos de precisión: El rol de los moldes impresos en 3D en la industria de moldeo por inyección), Stratasys.
[2] G. A. Mendible, “Applications of transient cooling simulations in injection molding” (Aplicaciones de las simulaciones de refrigeración transitoria en el moldeo por inyección), Tesis de doctorado, Universidad de Massachusetts Lowell, 2015.