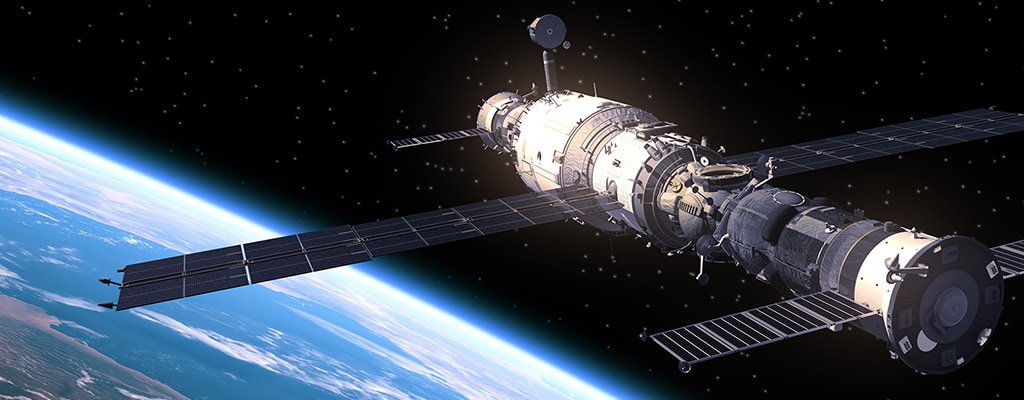
Carcasas posteriores de grado espacial para conectores Micro-D y D-sub
Al elegir carcasas posteriores para aplicaciones espaciales, la protección contra la tensión y el blindaje EMI/RFI son algunas de las características de rendimiento necesarias para soportar condiciones difíciles.
Encontrar las carcasas posteriores adecuadas
Cuando los diseñadores evalúan la capacidad de una carcasa posterior para proteger las terminaciones de conector a cable y cable, vale la pena considerar soluciones económicas y de alta calidad que puedan manejar múltiples desafíos. Las funciones clave proporcionadas por las carcasas posteriores incluyen una protección contra la tensión en la parte posterior de la carcasa (donde los contactos se conectan a cables o alambres), blindaje contra interferencia electromagnética (EMI) y protección del medio ambiente.
Las propiedades de los materiales de las carcasas posteriores de aleación de aluminio o compuestos termoplásticos deben presentar características de acoplamiento resistentes, livianas y precisas. El rendimiento físico debe incluir la capacidad de soportar golpes, vibraciones, temperaturas y corrosión. El manejo de estos desafíos es especialmente crítico cuando los sistemas electrónicos están sujetos a velocidades supersónicas y altas fuerzas gravitacionales (g).
Las carcasas posteriores Micro-D y D-subminiatura de TE Connectivity (TE) para aplicaciones espaciales satisfacen las demandas funcionales, de material y de rendimiento, cuando la calidad y la asequibilidad son importantes.
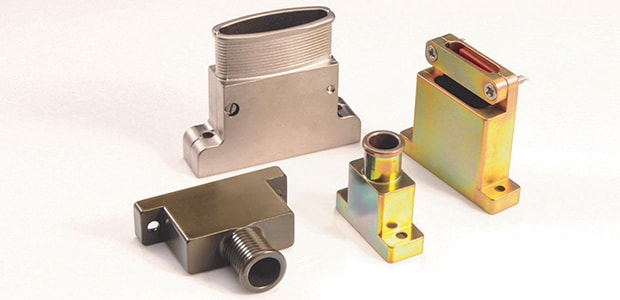
Cumplir con los desafíos funcionales clave del uso de carcasas posteriores de conectores D-sub y Micro-D
La evolución de los conectores tipo D ha pasado de los conectores D-Subminiatura (D-sub) desarrollados en la década de 1950 a diseños más compactos microminiatura D (Micro-D) introducidos a principios de la década de 1970 a las versiones D-sub y Micro-D de alto rendimiento de hoy en día que aprovechan la avanzada tecnología de carcasa posterior rectangular para aplicaciones de grado espacial.
Hoy en día, los conectores para rack y panel pueden utilizar carcasas posteriores de TE D-sub altamente especializadas para el acoplamiento conforme con MIL-DTL-24308 y carcasas posteriores Micro-D para el acoplamiento compatible con MIL-DTL-83513 en factores de forma compactos y rectangulares. Al igual que los diseños circulares estándar, las carcasas posteriores rectangulares ofrecen ventajas funcionales clave, que incluyen:
Incorporación de la protección contra la tensión
La protección contra la tensión admite cables y alambres para ayudar a evitar la flexión o flexión excesiva. Esto se puede lograr con una funda termocontraíble, una abrazadera de cable o un poste de amarre, según las preferencias del cliente y los requisitos de prueba. Las abrazaderas de cable ayudan a evitar que los cables tiren de los contactos y que se produzcan daños mecánicos generales en la conexión. Las abrazaderas de los cables de la barra de asiento están integradas en la carcasa posterior para simplificar la instalación. Sin embargo, las carcasas posteriores de protección contra la tensión no proporcionan ninguna EMI o protección ambiental y deben usarse solo en ambientes limpios y secos.
Prevención de la interferencia electromagnética (EMI)
EMI, también conocida como interferencia de radiofrecuencia (RFI) cuando está en el espectro de radiofrecuencia, puede afectar un circuito eléctrico por inducción electromagnética, acoplamiento electrostático o conducción. Para ayudar a evitar los efectos de la EMI, el blindaje de compatibilidad electromagnética (EMC) puede emplear un blindaje trenzado debidamente conectado a tierra o una pantalla terminada en la carcasa posterior. Para asegurar el blindaje/pantalla, se puede utilizar una banda estándar o microbanda.
Los métodos adicionales para preservar la integridad de las piezas incluyen:
Protección contra los contaminantes externos
Para proteger las carcasas posteriores del medio ambiente, todo el conjunto debe sellarse con una funda termocontraíble. La funda en sí debe estar sellada adecuadamente con un compuesto de encapsulación o un adhesivo para ayudar a evitar que el agua u otros fluidos entren en el cableado. Otra solución es proporcionar una cubierta protectora en la parte posterior de un conector que se utiliza como un dispositivo independiente.
Conexión a tierra del sistema
La conexión de una pantalla en la carcasa posterior conectará a tierra el sistema. La conexión más básica del blindaje del cable comprende la conexión de toda la circunferencia del blindaje del cable a la carcasa posterior. Luego debe conectarse al gabinete y, en última instancia, al fuselaje para ayudar a garantizar un sistema cerrado sin un bucle de tierra. El uso de una carcasa posterior para la conexión a tierra es particularmente valioso en situaciones en las que no se permite la conexión a tierra a través de un pin.
Enfrentando los desafíos materiales de las carcasas posteriores de grado espacial
Las carcasas posteriores en aplicaciones con clasificación de espacio requieren un procesamiento de materiales especializado e interfaces de acoplamiento precisas. Para las carcasas posteriores metálicas, el material base y el revestimiento deben combinarse para evitar la corrosión galvánica entre metales diferentes. Para las carcasas posteriores termoplásticas compuestas, el material no metálico no se corroe, pesa menos que el metal y puede soportar mejor los entornos hostiles.
Las carcasas posteriores en cualquiera de los materiales están disponibles en versiones de copa de soldadura, precableada y placa de circuito impreso (PCB).
- Las carcasas posteriores de aluminio están hechas de aleación de aluminio mecanizada ligera y resistente que emplean accesorios de acero inoxidable. El recubrimiento generalmente se realiza con níquel químico, que proporciona un acabado conductor de baja resistencia apropiado para aplicaciones no ambientales. El baño de oro ofrece una excelente resistencia a la corrosión y la radiación del espacio. Debido a que el recubrimiento de cadmio se sublima en el vacío, no es aceptable en aplicaciones donde la desgasificación es un problema.
- Las carcasas posteriores termoplásticas compuestas están hechas de materiales termoplásticos compuestos resistentes a productos químicos que reducen significativamente el peso del sistema de interconexión y manejan la niebla de SO2 mejor que la metálica. Debido a que las carcasas compuestas son transparentes a EMI, se utiliza un niquelado químico para el blindaje EMI.
El acoplamiento de precisión ayuda a garantizar la integridad eléctrica de una interconexión al eliminar la discontinuidad en los diámetros entre pares. Las carcasas posteriores mecanizadas con precisión permiten no solo un acoplamiento preciso entre interfaces, sino también una fuerte fuerza de retención de acoplamiento. Para una fácil instalación sobre cables conectados, las carcasas posteriores divididas pueden encajar sobre el conector sin un componente de clip ferromagnético y emplean cierres de rosca para acoplar conectores. (Las carcasas posteriores de una sola pieza, por el contrario, deben colocarse en el haz de cables antes de que se completen las terminaciones de cable a conector). Las carcasas posteriores que requieren una plataforma para correas de banda pueden utilizar una microbanda de bajo perfil que acomoda anchos de banda estrechos que ahorran espacio.
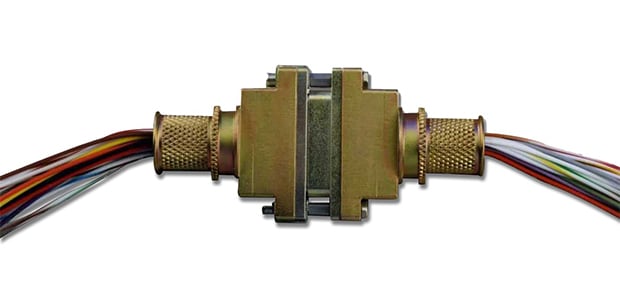
Enfrentando los desafíos de rendimiento de las carcasas posteriores de grado espacial
Durante el lanzamiento, el vuelo y la órbita, las carcasas posteriores utilizadas en las interconexiones a bordo de las naves espaciales están sujetas a condiciones extremas que requieren características de rendimiento críticas.
Protección a golpes y vibraciones
Las características específicas de la carcasa posterior desempeñan un papel fundamental en el mantenimiento de la continuidad eléctrica al reducir el estrés y la tensión durante las sacudidas violentas y las fuerzas G extremas. Las características de la carcasa posterior D-sub y Micro-D de TE están diseñadas para cumplir con los requisitos del cliente adecuados para la aplicación, no con las especificaciones genéricas.
* Consejo para el éxito: Cuando se requiere blindaje EMI, el diseñador puede usar la conexión de microbanda para ese propósito, además de disfrutar de una medida de protección contra la eliminación inadvertida debido a vibraciones y golpes. La tuerca de bloqueo de autoacoplamiento proporciona una protección mecánica mejorada contra el aflojamiento bajo vibración.
La incorporación de postes de amarre en las carcasas posteriores con bandas puede lograr la protección contra la tensión de trabajo ligero. Los postes de amarre son opcionales en las carcasas posteriores Micro-D con bandas porque los cables generalmente se encapsulan en su lugar y la trenza de la pantalla agrega suficiente protección contra la tensión. La encapsulación solo proporciona cierta protección contra la tensión, ya que la resina epoxi u otro material utilizado para llenar el espacio en la parte posterior de un conector se endurecerá en un sólido, ofreciendo un grado de fuerza de retención para soportar los contactos en la carcasa.
Los puntos de entrada de cables también son vulnerables a las vibraciones. Las entradas de cable de forma elíptica se pueden emplear para reducir los ángulos de contacto para minimizar las áreas de desgaste en comparación con las entradas de cable redondas. Sin embargo, la fuerza desigual alrededor de las bandas en las entradas de cable de forma elíptica causa problemas, ya que el radio más grande tiende a permitir que el trenzado se salga. El procesamiento adecuado puede mitigar este problema, pero este tipo de entrada no se recomienda en condiciones de alta vibración.
Tolerancia de temperatura
Tanto si se trata de picos de temperatura muy elevados, como de mínimos, o de ciclos entre temperaturas altas y bajas, el calor y el frío extremos someten a los materiales (metales, vidrio y polímeros) a tensiones que pueden provocar grietas y fatiga. También pueden distorsionar los conjuntos y romper los sellos debido a diferentes coeficientes de expansión térmica.
En general, las carcasas posteriores de TE están certificadas según el rango de prueba de ciclo de temperatura MIL-STD-883 de -55 °C a 125 °C. Sin embargo, hay materiales y revestimientos especializados disponibles para manejar el frío criogénico del espacio y para la electrónica de mayor temperatura (Figura 1).
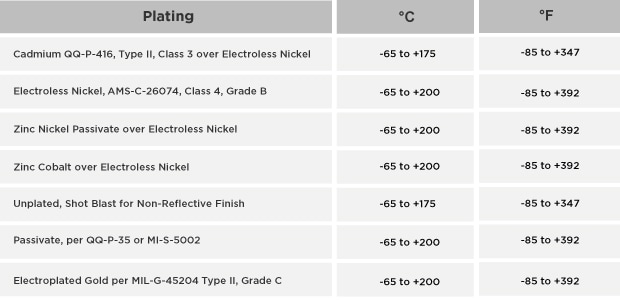
Control de desgasificación
La desgasificación ocurre cuando los gases atrapados en materiales no metálicos, como los polímeros utilizados en insertos de conectores, sellos, adhesivos o materiales de encapsulación, se liberan en el vacío del espacio o por altas temperaturas. Los gases liberados pueden condensarse y contaminar superficies sensibles, lo que, a la larga, degrada el rendimiento de los sensores de dispositivos acoplados de carga (CCD) en satélites, radiadores térmicos o celdas solares.
Pruebas ASTM E595-77/84/90 de la NASA y el MIL-W-22759 (M22759) | La especificación SAE AS22759 cubre el rendimiento de un material cuando se expone a altas temperaturas o al vacío. Los materiales considerados materiales de baja desgasificación cumplen con los requisitos de una pérdida de masa total de 1.00 % o menos y un material condensable volátil recolectado (CVCM) de 0.10 % o menos.
* Consejo para el éxito: Los conectores y carcasas posteriores Micro-D de grado espacial deben cumplir con los requisitos MIL-DTL-83513 para la desgasificación de material en un entorno de vacío.
Resistencia ultravioleta
En el espacio, no hay atmósfera para proteger los materiales de los efectos de los rayos X, gamma y radiación cósmica. La degradación ultravioleta (UV) influye negativamente en las propiedades materiales de los componentes electrónicos, e incluso puede cambiar la composición molecular de los materiales. Lo hace eliminando los átomos de oxígeno de las sustancias que contienen oxígeno. Como resultado, los subsistemas de control térmico pueden no funcionar correctamente, la óptica puede degradarse y los paneles solares pueden volverse menos eficientes.
En las altitudes de la órbita terrestre baja (LEO) entre 200 km y 700 km, la excitación UV de las moléculas de O2 restantes en la franja de la atmósfera forma oxígeno monatómico. La corrosión del oxígeno atómico (ATOX) ocurre cuando estas moléculas de oxígeno monoatómico altamente reactivas erosionan el aluminio y los plásticos. Una solución es emplear materiales con bajo potencial galvánico, como polímeros de grado espacial, compuestos termoplásticos y vidrio (fibra óptica).
Se pueden utilizar chapas y revestimientos con aleaciones para evitar la formación de una celda electrolítica. El baño de oro resiste la corrosión ATOX porque el oro es un metal noble que normalmente resiste la oxidación. Los revestimientos de dióxido de silicio pueden proteger los polímeros de la corrosión ATOX porque el SiO2 ya está completamente oxidado. En términos más generales, los satélites LEO pueden utilizar blindaje UV especial para sus sistemas electrónicos para minimizar la degradación UV y proteger los componentes.
Más capacidades para interconexiones de grado espacial
Hoy en día, los desafíos para las interconexiones en aplicaciones espaciales se están expandiendo, ya que el tamaño y el peso de los componentes y paquetes deben disminuir. TE ofrece una amplia gama de productos compatibles con la NASA y MIL-SPEC, junto con conectores, cables y capacidades completas de aprovechamiento, para ayudar a satisfacer la mayoría de las necesidades de comunicaciones de datos, video, ópticas y de control en la industria aeroespacial.
Las carcasas posteriores de grado espacial de TE están diseñadas para soportar las condiciones más rigurosas mientras mantienen un acoplamiento preciso. No importa el desafío, cuente con nuestra experiencia técnica, ingeniería de diseño y capacidades de fabricación para respaldar su misión, desde el lanzamiento hasta la intercepción o el despliegue.
Puntos clave
- Seleccionar la carcasa posterior adecuada para aplicaciones espaciales es vital para el éxito de cualquier misión.
- Los desafíos funcionales clave incluyen protección contra la tensión, interferencia electromagnética (EMI), sellar irritantes ambientales y garantizar que el sistema esté correctamente conectado a tierra.
- Los materiales utilizados en las carcasas posteriores para aplicaciones con clasificación espacial deben ser resistentes a la corrosión y capaces de soportar entornos hostiles.
- Algunas de las condiciones extremas que plantean desafíos de rendimiento incluyen choques y vibraciones, temperaturas extremas y cambio de temperatura, desgasificación y exposición a rayos fuertes fuera de la atmósfera de la Tierra.
- Mirando hacia el futuro de las interconexiones para aplicaciones espaciales, las piezas deben optimizarse para el tamaño y el peso.