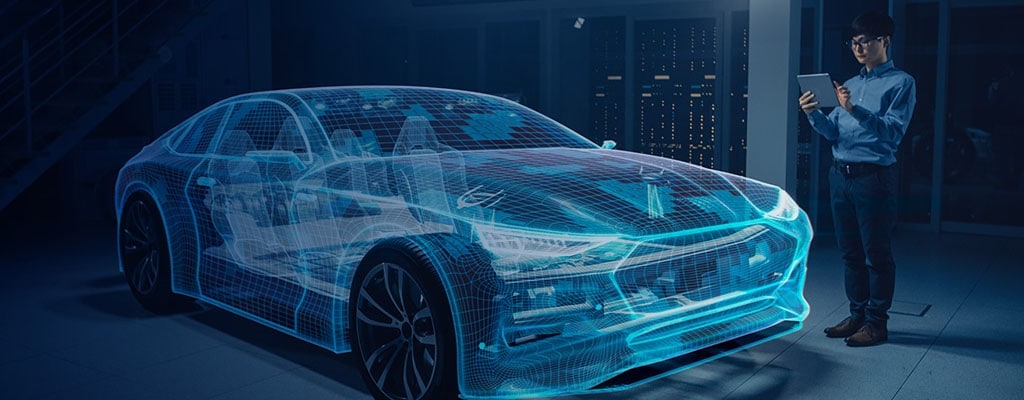
Tendencia
Resistente a temperaturas extremas
Las interconexiones ofrecen nuevos niveles de ahorro de peso para las aplicaciones de los deportes de motor. Por Paul Webb, director de ventas y marketing, deportes de motor
La reducción de peso es fundamental para la ventaja competitiva en las carreras de Fórmula 1 y otros deportes de motor. Unos pocos gramos ahorrados aquí y unos pocos más ahorrados allá pueden sumar ahorros significativos en general. También estamos viendo un movimiento hacia el embalaje de alta densidad de las piezas electrónicas. A medida que aumenta el contenido electrónico de los automóviles, el impulso natural es miniaturizar el embalaje para obtener la máxima eficiencia en el uso del espacio. Los arneses de cableado y los sistemas de interconexión ofrecen oportunidades para reducir el peso y el tamaño. El primer requisito para los conectores y el cable es un diseño resistente que pueda soportar temperaturas extremas, vibraciones y la exposición a fluidos en general y al limpiador de frenos en especial.
Evolución de los conectores
La evolución de los conectores de la serie DEUTSCH AS de TE Connectivity (TE) demuestra la miniaturización de los conectores. Los conectores más pequeños suelen pesar menos, por lo que se prestó atención al desarrollo de conectores de mayor densidad. Las cubiertas de acero inoxidable dieron paso al aluminio ligero, con un compuesto mucho más liviano. Elementos como los anillos de acoplamiento se hicieron más pequeños. A medida que los conectores se reducen, también hay que prestar atención a las cuestiones de utilidad, como el rediseño de las moletas para que un técnico con guantes pueda conectar y desconectar los conectores con rapidez y precisión. Los conectores de cubierta compuesta ofrecen un método atractivo para reducir el peso. Cuando la industria consideró por primera vez los conectores compuestos, no cumplieron las expectativas de rendimiento resistente en el mercado de los deportes de motor. En especial, los materiales compuestos no resistieron la exposición al limpiador de frenos. Como resultado, los diseñadores dejaron de usarlos. Los materiales compuestos están evolucionando. Estos han mejorado notablemente y la próxima generación pronto atenderá completamente las necesidades de las carreras de automóviles. Los materiales compuestos merecen una nueva evaluación de sus capacidades para ahorrar peso y cubrir las necesidades mecánicas y medioambientales de los deportes de motor.
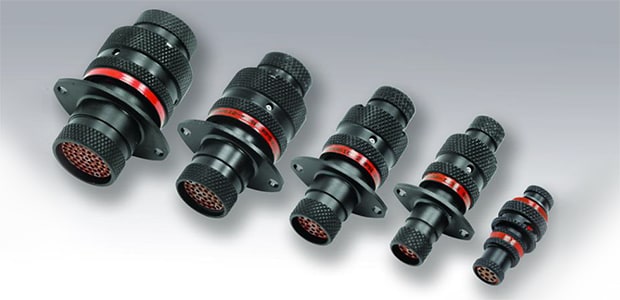
Normalmente, los materiales compuestos han reducido el peso de los conectores en un 40 % aproximadamente. Al optimizar el material de refuerzo e introducir la espuma en las matrices de polímero, se puede alcanzar un ahorro adicional del 10 % al 20 %. Tanto el material de la fibra como la longitud de las fibras de refuerzo desempeñan un papel importante para determinar la resistencia de la pieza acabada. Los materiales de mayor resistencia pueden significar una reducción en el grosor de las paredes y, por lo tanto, un peso menor. Introducir agentes espumantes o microesferas en un material compuesto de polímero, aunque se dificulta a medida que aumenta el volumen de la fibra de refuerzo, es posible hoy en día. Los cables de pared delgada de alto rendimiento ya son el estándar para las carreras de automóviles. Un cable típico, como el cable SPEC 55 de TE, utiliza un aislamiento y una cubierta reticulada de ETFE que ofrece rangos de temperatura de hasta 150 °C o 200 °C y una excelente resistencia a los fluidos. La construcción de paredes finas permite reducir el peso sin comprometer el rendimiento. Si bien, tanto la industria del automóvil comercial y como el ejército han comenzando a utilizar hilos y cables de aluminio para ahorrar peso, todavía no encuentran un uso generalizado en los deportes de motor.
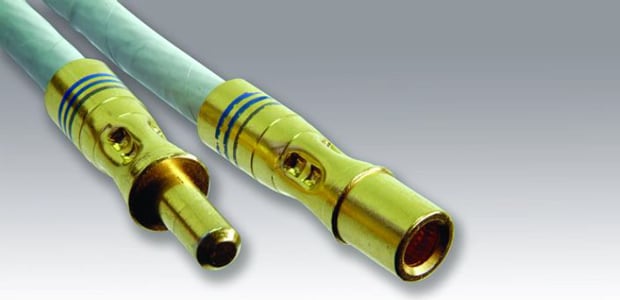
El cable de aluminio se considera difícil de manejar. Su radio de curvatura no es tan ajustado como el del cobre, además resulta preocupante la fiabilidad de la conexión debido al flujo frío. Sin embargo, hay contactos disponibles que contrarrestan el flujo frío para formar una conexión confiable y hermética. El aluminio tiene solo el 60 % de la conductividad del cobre, por lo que se necesita un conductor más grande para conseguir la misma capacidad de conducción de corriente. Incluso, teniendo en cuenta esto, el aluminio pesará aproximadamente la mitad.
Ruido eléctrico
Cómo abordar la EMI: tres enfoques
Si bien la protección se ha utilizado con moderación en los vehículos de carreras, la tecnología más reciente está creando nuevos niveles de ruido eléctrico que deben solucionarse. Los sistemas de recuperación de energía de alta corriente, por ejemplo, son una fuente de interferencia electromagnética (EMI).
1
Separación
Aumentar la separación entre la fuente EMI y los cables y los productos electrónicos susceptibles. Con el espacio limitado de un carro, este enfoque es poco práctico en la mayoría de los casos.
2
Apantallamiento
Dado que la protección añade peso, con frecuencia se utiliza en función de las necesidades en lugar de estandarizar los cables protegidos. Esto se puede lograr deslizando un cable trenzado de cobre sobre el cable y conectando en la carcasa posterior de un conector. La trenza forma un camino de baja impedancia a tierra para la EMI. TE ha presentado recientemente un sistema de trenzado ligero que ofrece un ahorro de peso de hasta el 50 % respecto al trenzado tradicional.
3
Fibra óptica
Esto es por naturaleza inmune a la EMI. Además, los cables de fibra óptica son considerablemente más ligeros que los cables de cobre. Tanto las fibras ópticas de vidrio como las de plástico son candidatas para su aplicación en los deportes de motor. Las fibras de vidrio tienen las ventajas de un mayor ancho de banda y un mayor rango de temperatura de funcionamiento, con algunas fibras especiales de hasta 700 °C. La desventaja es que son más difíciles de manejar. Si bien los cables de fibra de vidrio son resistentes y están disponibles en versiones reforzadas, hay que tener cierto cuidado a la hora de enrutarlos y respetar los radios de curvatura. La construcción del cable puede superar muchos de estos inconvenientes para permitir que el cable de fibras de vidrio pueda soportar los rigores de la construcción, el mantenimiento y las carreras de un carro. Las fibras ópticas de plástico son menos costosas tanto en el propio cable como en los transceptores electrónicos asociados. Son más indulgentes con el abuso mecánico y la curvatura ajustada, además se utilizan más en las redes automóviles comerciales en la actualidad. El principal inconveniente es el rango de temperatura, ya que el cable POF estándar está limitado a 85 °C y las versiones para altas temperaturas llegan hasta los 125 °C.
Soluciones integradas
Si los conectores de material compuesto merecen una nueva apariencia, también lo merecen las cajas de material compuesto como una alternativa viable al aluminio para alojar unidades de control electrónico y otros sistemas. La atracción inicial de las cajas de materiales compuestos es el ahorro de peso, una caja compuesta de sulfuro de polifenileno lleno de carbono puede ser 40 % más ligero que una de aluminio. Los materiales compuestos son fuertes y pueden adaptarse para proporcionar una resistencia a la tracción excepcional, a la fuerza extensible, a la flexión, etc. Pueden ser más resistentes que sus contrapartes de aluminio porque no se abollan ni deforman fácilmente. La sustitución de las cajas metálicas por materiales compuestos ofrece todas las ventajas mecánicas y eléctricas del metal, pero con las ventajas añadidas de un menor peso, resistencia a la corrosión y menores costos.
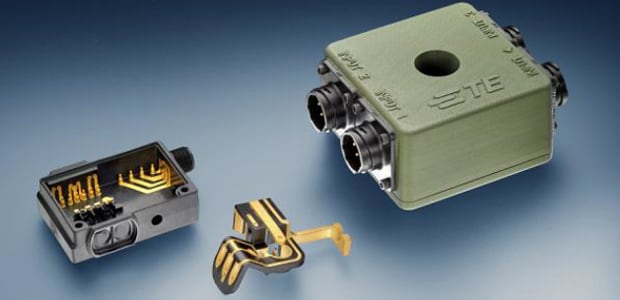
Las nuevas capacidades y las nuevas formulaciones de materiales te ofrecen más opciones. Los rellenos, que van desde la fibra de carbono tradicional hasta las microesferas y los nanotubos de carbono, permiten personalizar la caja para lograr el mejor equilibrio entre el peso y el rendimiento eléctrico, mecánico y medioambiental. El modelo avanzado permite crear separadores, carcasas de conectores integradas, particiones y otras características tridimensionales. La metalización selectiva permite que las trazas de circuitos, la protección e incluso las antenas incorporadas se integren de manera rentable en la caja. El modelado tridimensional y la metalización selectiva proporcionan un ahorro de peso adicional que va más allá de las ventajas básicas de los materiales compuestos.
Conclusión
La tecnología de interconexión continúa avanzando a fin de ofrecer nuevos niveles de ahorro de peso para aplicaciones de los deportes de motor. Más importante aún, lo que es viejo vuelve a ser nuevo. Las tecnologías que se consideraban deficientes en uno u otro aspecto han evolucionado. No confíes en la sabiduría convencional de ayer. Los conectores y las cajas de materiales compuestos, la fibra óptica, el trenzado blindado y el cable de aluminio merecen una nueva evaluación. Una de las ventajas de trabajar en TE es que adoptamos un enfoque de las interconexiones en el nivel de sistema. Un par de gramos agregados aquí pueden ahorrar kilogramos en otros lugares. Es el producto final el que gana la carrera, no los componentes individuales.