Relés en sistemas de control relacionados con la seguridad
Hay no menos de siete formas para que incluso un transistor simple falle. Esto significa que el monitoreo de todos los componentes electrónicos que pueden estar defectuosos en una salida de conmutación electrónica segura requiere un esfuerzo considerable y el uso de elementos, como una unidad a prueba de fallas con cronómetro y microcontroladores (Fig. 1). En comparación, los diagnósticos para una salida de relé segura no implican más que el monitoreo de la apertura de contactos. Los relés con contactos forzados ya tienen integrado este mecanismo de diagnóstico; devuelven el resultado para su posterior procesamiento a través de un contacto de monitoreo aislado eléctricamente.
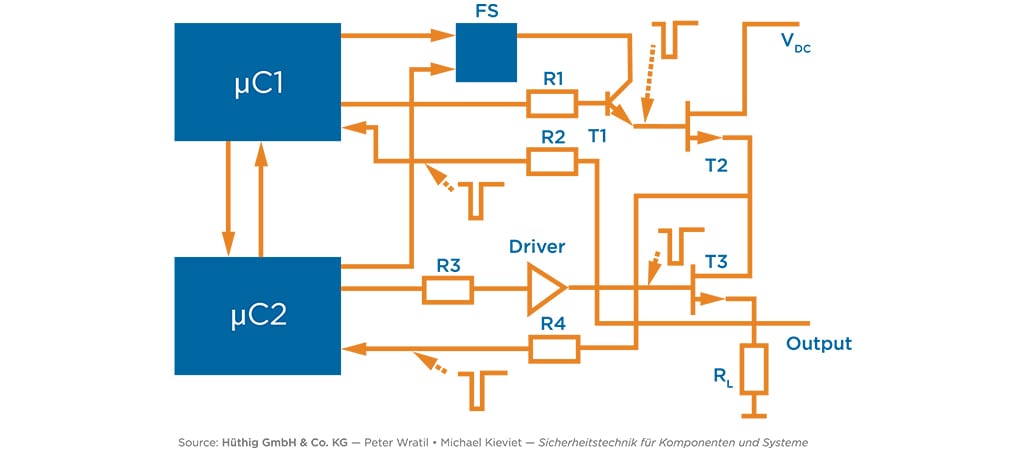
Por lo tanto, no es de extrañar que los relés sean la primera opción de los expertos en seguridad cuando se utilizan circuitos simples para desarrollar salidas seguras, incluso para altos voltajes. Las salidas de control que se basan en el contacto también exhiben una mayor capacidad inherente de carga de corriente y resistencia a los voltajes máximos que las salidas electrónicas; pero al diseñar una salida segura es importante tener en cuenta que, a lo largo de su vida útil, los relés tienen una tasa de fallas cada vez mayor debido al desgaste.
Tipos de fallas del relé
La Fig. 2 muestra una "curva de bañera" para un relé de tres contactos, en la que se muestra con claridad dos secciones exponenciales, correspondientes a fallas tempranas y fallas de desgaste, y una sección central con una tasa más o menos constante de fallas aleatorias.
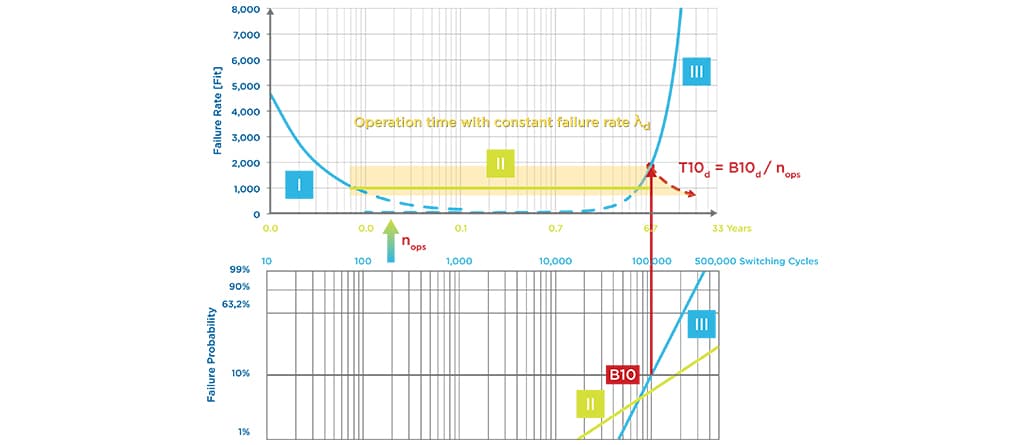
Estas fallas aleatorias no son causadas por el desgaste y, por lo tanto, son independientes de los ciclos de conmutación. Al igual que los componentes electrónicos, los relés exhiben fallas que se distribuyen de manera uniforme a lo largo del tiempo. Estos incluyen, por ejemplo, corrosión de contactos y otras piezas metálicas, deformación inducida por el medioambiente de piezas de plástico, fallas en el proceso de fabricación e incumplimiento de la tolerancia.
La norma IEC EN 61709 (SN 29500) proporciona fórmulas que se pueden utilizar para determinar una tasa de fallas constante sobre la base de fallos reales en el campo. Las partes exponenciales de la curva de la bañera que muestran fallas tempranas y las causadas por el desgaste quedan fuera de las casos registrados: solo se consideran las fallas que ocurren después de los primeros 5000 ciclos de conmutación y hasta un máximo del 10 % de la vida útil de la unidad. Sobre esta base, la tasa de fallas establecida de un relé de contacto forzado (forced-contact relay, R-FC) de 3 polos en una aplicación típica es de 1000 FIT1, lo cual es totalmente realista. Esto predice que después de 20 años alrededor del 16 % de los relés habrán fallado.
Las tasas de fallas que se obtienen de acuerdo con la norma IEC EN 61709 se utilizan para cálculos en los que los relés conmutan con poca frecuencia y es muy poco probable que el final de su vida útil sea por el desgaste de la conmutación.
Las fallas de desgaste son fallas sistemáticas conocidas que se generan por la erosión de los contactos durante las operaciones de conmutación. Por lo tanto, su tasa de fallas se determina a partir de la vida útil de conmutación de los relés a una carga específica. Este valor se escala al eje de tiempo sobre la base de la frecuencia de conmutación asumida NO por hora para la aplicación. Dentro del tiempo de funcionamiento T10d, la tasa de falla λd se considera constante.

La vida útil B10, que se determina de acuerdo con la norma IEC 61810-2, es el número de ciclos de conmutación en los que el 10 % de todos los relés habrán fallado. Debido a que los cálculos de seguridad para los circuitos de seguridad solo tienen en cuenta las fallas peligrosas (contactos que no se abren), B10d (donde d = peligroso) puede ser mayor que B10 por un factor de hasta 10.
Relés en circuitos de seguridad
La probabilidad de falla en un solo relé suele ser demasiado alta para protegerse contra un riesgo. Los circuitos de relé para diversas categorías de riesgo son conocidos2 y pueden verificarse como subsistemas con componentes bastante simples, como se describe en EN/IEC 62061, sección 6.7.3.3. Las arquitecturas básicas de los subsistemas descritas en la sección 6.7.8 de esta norma muestran cómo las tasas de fallas pueden reducirse de manera gradual mediante redundancia (tolerancia a fallas de hardware) y diagnósticos.
La tolerancia a las fallas de hardware se determina subdividiéndolas en fallas seguras e inseguras (fracción de falla segura, SFF). En el caso de los relés, esta subdivisión se puede definir entre fallas seguras sin cierre y fallas inseguras sin apertura, y determinada por el análisis de modo y efectos de falla (FMEA) y la experiencia de campo. Esto significa que los relés corresponden a los subsistemas de tipo A definidos en la norma IEC 61508-2. En general, se supone que el SFF de un relé no monitoreado alcanzará un máximo del 95 % si se le proporciona un fusible interno clasificado a dos tercios de la corriente de contacto.
Una tolerancia a fallas de hardware de 1 permite evitar el efecto de un solo contacto soldado, ya que tiene dos relés conectados en serie. En caso de falla, el relé redundante equivalente aislará la carga.
La probabilidad PFD(t) (Probabilidad de falla sobre demanda) de la falla peligrosa simultánea de dos relés conectados en serie se reduce de manera significativa, incluso sin necesidad de diagnósticos. Pero, en gran medida, cualquier falla de este tipo se deberá a fallas con una causa común (CCD):
PFD(t) = (λD Relé1 * t ) * (λD Relé2 * t) + Relés CCD1+2 * t
Una causa tan común afecta a ambos relés por igual, lo que hace que la redundancia sea ineficaz. En la Tabla F.1 de la norma EN/IEC 62061 se proporcionan los criterios para determinar la tasa de fallas con una causa común. Los factores que tienen efectos idénticos en los relés redundantes pueden ser térmicos, magnéticos, eléctricos o mecánicos, como la temperatura ambiente o los campos magnéticos y, en particular para los relés polarizados, las sobrecorrientes o la sobrecarga mecánica.
La proporción de fallas peligrosas se puede reducir aún más con diagnósticos adecuados, ya que cierto porcentaje de las fallas se pueden detectar mediante monitoreo (Fig. 3). En el cuadro A.1 de la norma IEC 61508-2 se describen los niveles de requisitos para detectar las causas de las fallas. Aquí, los contactos forzados ofrecen la cobertura de diagnóstico más alta posible, es decir, el 99 %.
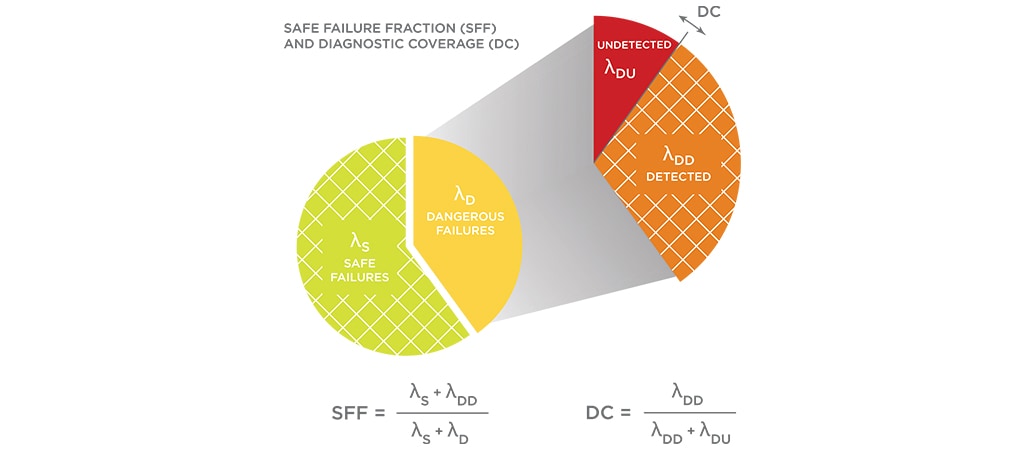
Relés con contactos forzados (R-FC)
Los R-FC garantizan que un segundo contacto antivalente se cierre solo cuando el espacio de contacto sea más ancho que 0,5 mm. Además de esto, los R-FC no proporcionan más seguridad que un relé elemental. De hecho, como todos los relés, pueden presentar desperfectos debido a fallas o porque llegan al final de su vida útil. Sin embargo, la evaluación de las señales del contacto de monitoreo permite realizar diagnósticos automáticos para cada ciclo de conmutación. En este caso, el circuito de seguridad puede impedir un reinicio.
La norma IEC 61810-3 (EN 50205) describe cómo diseñar y probar relés forzados de tal manera que no se pierda la antivalencia de los contactos normalmente abiertos y normalmente cerrados, incluso en caso de una falla. Aquí, los contactos se conectan de manera mecánica a través de un actuador y tienen la dimensión suficiente como para que no se rompan. En situaciones en las que no es posible tal sobredimensionamiento, como en los puntos de flexión de los resortes, los posibles fragmentos están asegurados para que no generen un cortocircuito en el contacto antivalente.
Al igual que los relés electromecánicos (EMR), debe seleccionar las dimensiones de los relés con contactos forzados para que se adapten al circuito de control, el circuito de contacto y a las condiciones ambientales. En este sentido, los relés con contactos forzados no son diferentes de cualquier otro EMR. Al dimensionar, por ejemplo, el voltaje de la unidad o determinar la vida útil esperada o la resistencia al impacto, se puede consultar una amplia documentación y notas3 de aplicación.
Han surgido una serie de preguntas específicas que corresponden especialmente a los R-FC, en lo que respecta a los campos típicos de uso o a evitar las fallas de causa común.
Determinar parámetros eléctricos y mecánicos
Para obtener una disposición compacta de circuitos de seguridad operados por relés, suelen utilizarse "módulos de relés de seguridad" en carcasas estrechas que están diseñadas para su montaje en un riel DIN. La temperatura ambiente máxima para los relés que se establece en la norma IEC 61810-1 no se puede utilizar aquí, ya que las distancias a la pared de la carcasa y la proximidad de otras fuentes de calor hacen imposible determinar de manera estandarizada la temperatura ambiente en las cercanías de los relés. Por lo tanto, las temperaturas de los relés se deben medir directamente en las peores condiciones.
Esto se hace con módulos de relé ensamblados, utilizando la tensión de alimentación máxima con la mayor cantidad posible de componentes activados; la temperatura se mide directamente en los puntos calientes en la superficie del relé, mientras que las temperaturas de la bobina se determinan a partir de la resistencia del cable. Los valores límite para la carga de temperatura son proporcionados por el fabricante del relé, y las notas de aplicación ayudarán a llevar a cabo estas mediciones.
Además del aspecto funcional al configurar el controlador, la temperatura también juega un papel importante en la seguridad que no debe pasarse por alto. En otras palabras, ¿qué sucede si la temperatura supera el rango especificado por el fabricante? ¿Qué podría dar lugar a tal desviación, y podría la misma causa afectar a los relés redundantes al mismo tiempo? Dado que los fabricantes no prueban el efecto de las desviaciones de temperatura fuera del rango especificado, debemos suponer que se produciría una falla crítica. Por esta razón, la evaluación de seguridad del dispositivo debe incluir el cumplimiento del rango de temperatura estipulado.
Otra rango que especifica el fabricante es el de la resistencia al impacto y a las vibraciones. Si los componentes, PCB o dispositivos caen sobre una superficie sólida, pueden exponerse a cargas superiores al máximo permitido. El daño a menudo no es visible desde el exterior, pero las partes pueden desalinearse o pueden astillarse, lo que reduce la distancia de contacto o, incluso, puede atascar el relé por completo. Por lo tanto, debe existir una gestión de calidad adecuada, con las medidas correspondientes para detectar impactos excesivos y garantizar que las cargas mecánicas que se encuentran durante el procesamiento, el transporte y la operación estén dentro del rango especificado.
Conclusión y perspectivas
Los relés con contactos forzados que se usan en aplicaciones de seguridad en ascensores, ingeniería ferroviaria, ingeniería mecánica y automatización están disponibles en versiones de dos a diez contactos. Los usuarios esperan una mayor miniaturización y soluciones rentables que se puedan utilizar para cubrir riesgos leves. Los sensores integrados no solo podrían promover la miniaturización y la confiabilidad, sino que también podrían permitir funciones adicionales.
Según la norma, la delimitación requerida del rango de aplicación de un relé antes de que se produzcan las fallas de desgaste peligroso (B10d) ahora se lleva a cabo utilizando valores previstos para el tiempo de operación esperado, la carga de contacto y la frecuencia de conmutación.
Sin embargo, desde el punto de vista del usuario, sin duda sería útil poder reconocer un aumento en la tendencia del relé a quedar soldado o atascado en condiciones de campo.
En resumen, cuando los componentes se consideran, en especial, subsistemas y se unen diferentes tecnologías, podemos prever posibles aplicaciones adicionales que surgen para los relés en el campo de la tecnología de seguridad. La estandarización para la seguridad funcional deja mucho espacio para nuevas soluciones.
Relés en sistemas de control relacionados con la seguridad
Hay no menos de siete formas para que incluso un transistor simple falle. Esto significa que el monitoreo de todos los componentes electrónicos que pueden estar defectuosos en una salida de conmutación electrónica segura requiere un esfuerzo considerable y el uso de elementos, como una unidad a prueba de fallas con cronómetro y microcontroladores (Fig. 1). En comparación, los diagnósticos para una salida de relé segura no implican más que el monitoreo de la apertura de contactos. Los relés con contactos forzados ya tienen integrado este mecanismo de diagnóstico; devuelven el resultado para su posterior procesamiento a través de un contacto de monitoreo aislado eléctricamente.
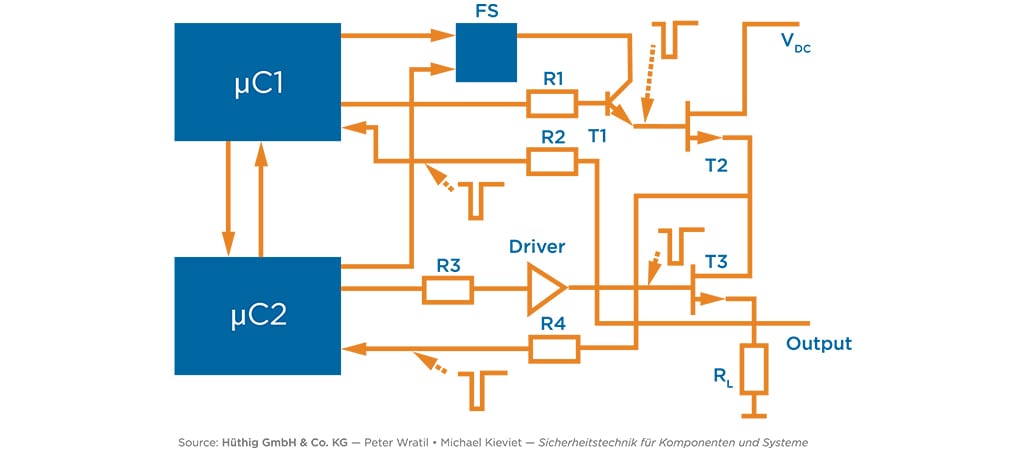
Por lo tanto, no es de extrañar que los relés sean la primera opción de los expertos en seguridad cuando se utilizan circuitos simples para desarrollar salidas seguras, incluso para altos voltajes. Las salidas de control que se basan en el contacto también exhiben una mayor capacidad inherente de carga de corriente y resistencia a los voltajes máximos que las salidas electrónicas; pero al diseñar una salida segura es importante tener en cuenta que, a lo largo de su vida útil, los relés tienen una tasa de fallas cada vez mayor debido al desgaste.
Tipos de fallas del relé
La Fig. 2 muestra una "curva de bañera" para un relé de tres contactos, en la que se muestra con claridad dos secciones exponenciales, correspondientes a fallas tempranas y fallas de desgaste, y una sección central con una tasa más o menos constante de fallas aleatorias.
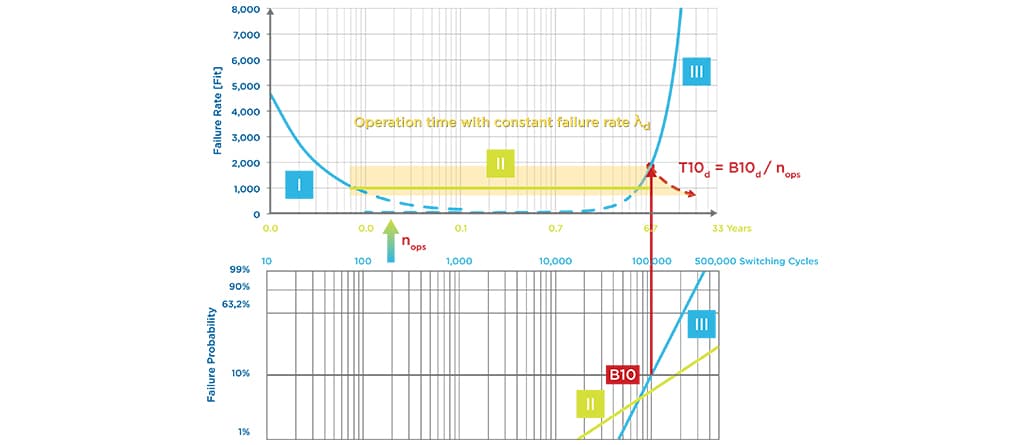
Estas fallas aleatorias no son causadas por el desgaste y, por lo tanto, son independientes de los ciclos de conmutación. Al igual que los componentes electrónicos, los relés exhiben fallas que se distribuyen de manera uniforme a lo largo del tiempo. Estos incluyen, por ejemplo, corrosión de contactos y otras piezas metálicas, deformación inducida por el medioambiente de piezas de plástico, fallas en el proceso de fabricación e incumplimiento de la tolerancia.
La norma IEC EN 61709 (SN 29500) proporciona fórmulas que se pueden utilizar para determinar una tasa de fallas constante sobre la base de fallos reales en el campo. Las partes exponenciales de la curva de la bañera que muestran fallas tempranas y las causadas por el desgaste quedan fuera de las casos registrados: solo se consideran las fallas que ocurren después de los primeros 5000 ciclos de conmutación y hasta un máximo del 10 % de la vida útil de la unidad. Sobre esta base, la tasa de fallas establecida de un relé de contacto forzado (forced-contact relay, R-FC) de 3 polos en una aplicación típica es de 1000 FIT1, lo cual es totalmente realista. Esto predice que después de 20 años alrededor del 16 % de los relés habrán fallado.
Las tasas de fallas que se obtienen de acuerdo con la norma IEC EN 61709 se utilizan para cálculos en los que los relés conmutan con poca frecuencia y es muy poco probable que el final de su vida útil sea por el desgaste de la conmutación.
Las fallas de desgaste son fallas sistemáticas conocidas que se generan por la erosión de los contactos durante las operaciones de conmutación. Por lo tanto, su tasa de fallas se determina a partir de la vida útil de conmutación de los relés a una carga específica. Este valor se escala al eje de tiempo sobre la base de la frecuencia de conmutación asumida NO por hora para la aplicación. Dentro del tiempo de funcionamiento T10d, la tasa de falla λd se considera constante.

La vida útil B10, que se determina de acuerdo con la norma IEC 61810-2, es el número de ciclos de conmutación en los que el 10 % de todos los relés habrán fallado. Debido a que los cálculos de seguridad para los circuitos de seguridad solo tienen en cuenta las fallas peligrosas (contactos que no se abren), B10d (donde d = peligroso) puede ser mayor que B10 por un factor de hasta 10.
Relés en circuitos de seguridad
La probabilidad de falla en un solo relé suele ser demasiado alta para protegerse contra un riesgo. Los circuitos de relé para diversas categorías de riesgo son conocidos2 y pueden verificarse como subsistemas con componentes bastante simples, como se describe en EN/IEC 62061, sección 6.7.3.3. Las arquitecturas básicas de los subsistemas descritas en la sección 6.7.8 de esta norma muestran cómo las tasas de fallas pueden reducirse de manera gradual mediante redundancia (tolerancia a fallas de hardware) y diagnósticos.
La tolerancia a las fallas de hardware se determina subdividiéndolas en fallas seguras e inseguras (fracción de falla segura, SFF). En el caso de los relés, esta subdivisión se puede definir entre fallas seguras sin cierre y fallas inseguras sin apertura, y determinada por el análisis de modo y efectos de falla (FMEA) y la experiencia de campo. Esto significa que los relés corresponden a los subsistemas de tipo A definidos en la norma IEC 61508-2. En general, se supone que el SFF de un relé no monitoreado alcanzará un máximo del 95 % si se le proporciona un fusible interno clasificado a dos tercios de la corriente de contacto.
Una tolerancia a fallas de hardware de 1 permite evitar el efecto de un solo contacto soldado, ya que tiene dos relés conectados en serie. En caso de falla, el relé redundante equivalente aislará la carga.
La probabilidad PFD(t) (Probabilidad de falla sobre demanda) de la falla peligrosa simultánea de dos relés conectados en serie se reduce de manera significativa, incluso sin necesidad de diagnósticos. Pero, en gran medida, cualquier falla de este tipo se deberá a fallas con una causa común (CCD):
PFD(t) = (λD Relé1 * t ) * (λD Relé2 * t) + Relés CCD1+2 * t
Una causa tan común afecta a ambos relés por igual, lo que hace que la redundancia sea ineficaz. En la Tabla F.1 de la norma EN/IEC 62061 se proporcionan los criterios para determinar la tasa de fallas con una causa común. Los factores que tienen efectos idénticos en los relés redundantes pueden ser térmicos, magnéticos, eléctricos o mecánicos, como la temperatura ambiente o los campos magnéticos y, en particular para los relés polarizados, las sobrecorrientes o la sobrecarga mecánica.
La proporción de fallas peligrosas se puede reducir aún más con diagnósticos adecuados, ya que cierto porcentaje de las fallas se pueden detectar mediante monitoreo (Fig. 3). En el cuadro A.1 de la norma IEC 61508-2 se describen los niveles de requisitos para detectar las causas de las fallas. Aquí, los contactos forzados ofrecen la cobertura de diagnóstico más alta posible, es decir, el 99 %.
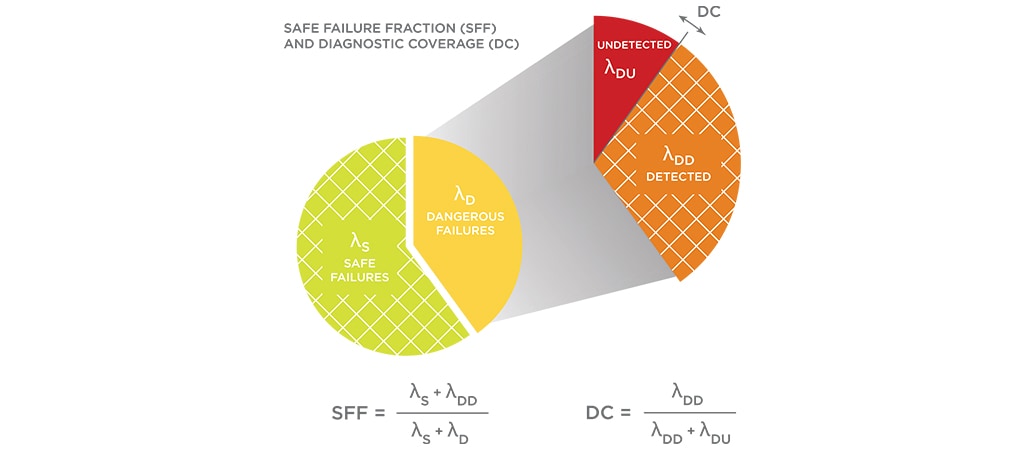
Relés con contactos forzados (R-FC)
Los R-FC garantizan que un segundo contacto antivalente se cierre solo cuando el espacio de contacto sea más ancho que 0,5 mm. Además de esto, los R-FC no proporcionan más seguridad que un relé elemental. De hecho, como todos los relés, pueden presentar desperfectos debido a fallas o porque llegan al final de su vida útil. Sin embargo, la evaluación de las señales del contacto de monitoreo permite realizar diagnósticos automáticos para cada ciclo de conmutación. En este caso, el circuito de seguridad puede impedir un reinicio.
La norma IEC 61810-3 (EN 50205) describe cómo diseñar y probar relés forzados de tal manera que no se pierda la antivalencia de los contactos normalmente abiertos y normalmente cerrados, incluso en caso de una falla. Aquí, los contactos se conectan de manera mecánica a través de un actuador y tienen la dimensión suficiente como para que no se rompan. En situaciones en las que no es posible tal sobredimensionamiento, como en los puntos de flexión de los resortes, los posibles fragmentos están asegurados para que no generen un cortocircuito en el contacto antivalente.
Al igual que los relés electromecánicos (EMR), debe seleccionar las dimensiones de los relés con contactos forzados para que se adapten al circuito de control, el circuito de contacto y a las condiciones ambientales. En este sentido, los relés con contactos forzados no son diferentes de cualquier otro EMR. Al dimensionar, por ejemplo, el voltaje de la unidad o determinar la vida útil esperada o la resistencia al impacto, se puede consultar una amplia documentación y notas3 de aplicación.
Han surgido una serie de preguntas específicas que corresponden especialmente a los R-FC, en lo que respecta a los campos típicos de uso o a evitar las fallas de causa común.
Determinar parámetros eléctricos y mecánicos
Para obtener una disposición compacta de circuitos de seguridad operados por relés, suelen utilizarse "módulos de relés de seguridad" en carcasas estrechas que están diseñadas para su montaje en un riel DIN. La temperatura ambiente máxima para los relés que se establece en la norma IEC 61810-1 no se puede utilizar aquí, ya que las distancias a la pared de la carcasa y la proximidad de otras fuentes de calor hacen imposible determinar de manera estandarizada la temperatura ambiente en las cercanías de los relés. Por lo tanto, las temperaturas de los relés se deben medir directamente en las peores condiciones.
Esto se hace con módulos de relé ensamblados, utilizando la tensión de alimentación máxima con la mayor cantidad posible de componentes activados; la temperatura se mide directamente en los puntos calientes en la superficie del relé, mientras que las temperaturas de la bobina se determinan a partir de la resistencia del cable. Los valores límite para la carga de temperatura son proporcionados por el fabricante del relé, y las notas de aplicación ayudarán a llevar a cabo estas mediciones.
Además del aspecto funcional al configurar el controlador, la temperatura también juega un papel importante en la seguridad que no debe pasarse por alto. En otras palabras, ¿qué sucede si la temperatura supera el rango especificado por el fabricante? ¿Qué podría dar lugar a tal desviación, y podría la misma causa afectar a los relés redundantes al mismo tiempo? Dado que los fabricantes no prueban el efecto de las desviaciones de temperatura fuera del rango especificado, debemos suponer que se produciría una falla crítica. Por esta razón, la evaluación de seguridad del dispositivo debe incluir el cumplimiento del rango de temperatura estipulado.
Otra rango que especifica el fabricante es el de la resistencia al impacto y a las vibraciones. Si los componentes, PCB o dispositivos caen sobre una superficie sólida, pueden exponerse a cargas superiores al máximo permitido. El daño a menudo no es visible desde el exterior, pero las partes pueden desalinearse o pueden astillarse, lo que reduce la distancia de contacto o, incluso, puede atascar el relé por completo. Por lo tanto, debe existir una gestión de calidad adecuada, con las medidas correspondientes para detectar impactos excesivos y garantizar que las cargas mecánicas que se encuentran durante el procesamiento, el transporte y la operación estén dentro del rango especificado.
Conclusión y perspectivas
Los relés con contactos forzados que se usan en aplicaciones de seguridad en ascensores, ingeniería ferroviaria, ingeniería mecánica y automatización están disponibles en versiones de dos a diez contactos. Los usuarios esperan una mayor miniaturización y soluciones rentables que se puedan utilizar para cubrir riesgos leves. Los sensores integrados no solo podrían promover la miniaturización y la confiabilidad, sino que también podrían permitir funciones adicionales.
Según la norma, la delimitación requerida del rango de aplicación de un relé antes de que se produzcan las fallas de desgaste peligroso (B10d) ahora se lleva a cabo utilizando valores previstos para el tiempo de operación esperado, la carga de contacto y la frecuencia de conmutación.
Sin embargo, desde el punto de vista del usuario, sin duda sería útil poder reconocer un aumento en la tendencia del relé a quedar soldado o atascado en condiciones de campo.
En resumen, cuando los componentes se consideran, en especial, subsistemas y se unen diferentes tecnologías, podemos prever posibles aplicaciones adicionales que surgen para los relés en el campo de la tecnología de seguridad. La estandarización para la seguridad funcional deja mucho espacio para nuevas soluciones.