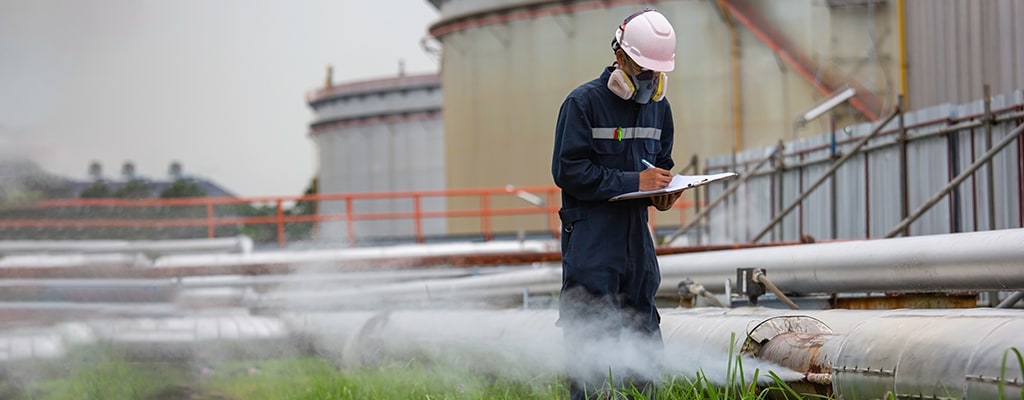
Industrias
Detección y monitoreo de la CUI en la industria del petróleo y gas
La CUI representa un reto importante en varios sectores, en particular para las industrias petroquímica y la del petróleo y gas. Este problema generalizado, que permanece oculto bajo capas de aislamiento, a menudo pasa desapercibido hasta que se realiza el mantenimiento de rutina. Si se pasa por alto, puede poner en riesgo la seguridad y ocasionar daños al medio ambiente, interrupciones operativas, pérdidas financieras, incumplimientos normativos, reducir la vida útil de los activos y aumentar los problemas de mantenimiento, lo que en última instancia representa un grave riesgo de lesiones o, incluso, de pérdida de vidas. Algunos informes sugieren que la CUI es responsable de entre el 40 % y el 60 % de los costos de reparación de tuberías (Dey, s. f.), lo que equivale a cientos de miles de millones de dólares en gastos anuales en la industria.
En este informe técnico se aborda el problema persistente de la CUI, se exploran avanzadas tecnologías de sensores y técnicas de monitoreo que son fundamentales para la detección temprana y el monitoreo continuo de la CUI, lo que, a su vez, hace posible mitigar posibles riesgos de manera proactiva, preservar la integridad de los activos y facilitar las operaciones de manera continua y segura en la industria del petróleo y gas.

Descripción general de la CUI
La CUI es la corrosión externa que por lo general ocurre en equipos aislados hechos de aceros al carbono o de baja aleación, como las tuberías. Para que este tipo de corrosión ocurra, son necesarias dos condiciones:
- La presencia de agua
- La disponibilidad de oxígeno
La CUI es más frecuente en plantas de procesamiento y refinerías que operan bajo temperaturas variables, lo que contribuye de manera significativa al proceso de corrosión. Además, la exposición del sistema a los productos corrosivos que están en contacto con la superficie de la tubería también actúa como fuente de corrosión.
Por lo general, la tubería que se encuentra en el centro del aislamiento está hecha de acero, y el aislamiento se compone de materiales o combinaciones de materiales que envuelven la tubería para reducir de manera significativa la transferencia de energía térmica. Esta reducción efectiva en la pérdida de energía contribuye a un considerable ahorro de costos.
Tuberías con aislamiento térmico y en frío
El aislamiento térmico evita la transferencia de energía del fluido calentado. La función principal de este aislamiento es conservar el calor. También protege a los operarios de las superficies calientes. Entre los materiales aislantes térmicos que más se utilizan se encuentran la lana mineral y la de vidrio, y el silicato de calcio.
Por otra parte, el aislamiento en frío reduce la transferencia de calor desde el exterior hacia la tubería y también limita la condensación. Entre los materiales para aislamiento en frío que más se utilizan se encuentran la espuma de poliuretano o la de caucho.
Conocer la composición y la función de los materiales de aislamiento, tanto térmico como en frío, es esencial para entender el papel que cumplen en el complejo problema de la CUI. Si bien la función principal del aislamiento es controlar la transferencia de energía, cuando determinadas condiciones ambientales y operativas están presentes, se crea un entorno propicio para la corrosión de manera involuntaria.
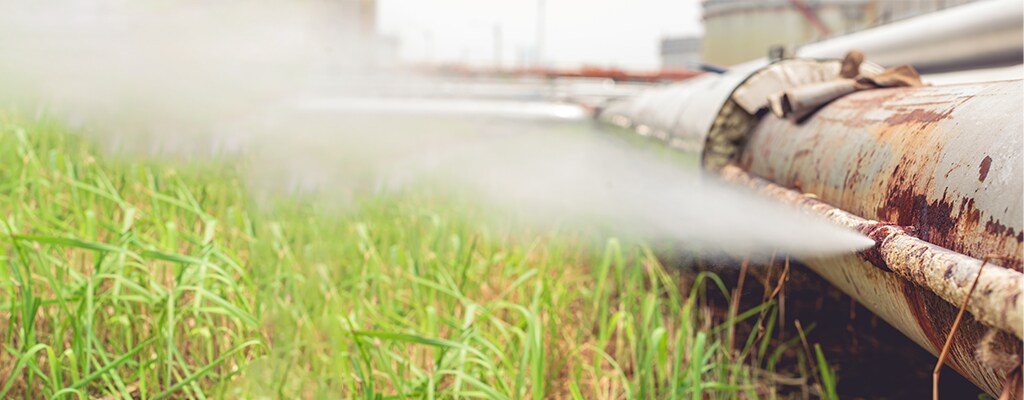
Condiciones medio ambientales corrosivas que afectan el aislamiento de las tuberías.
Detección tradicional de la CUI
Son varios los factores que interactúan para dar lugar a la CUI. La interacción de estos elementos es una compleja red de causalidades que agrava el problema, lo que dificulta detectarlo y manejarlo. Analicemos en detalle la interrelación de estos factores y veamos cómo sus sofisticadas interacciones sustentan el desarrollo de la CUI.
En primer lugar, las condiciones ambientales causan la CUI en gran medida. La humedad, las variaciones de temperatura y la exposición a la niebla salina o a contaminantes industriales pueden aumentar la probabilidad de que agua penetre el aislamiento, lo que antecede a la CUI. Estas condiciones, junto con la temperatura de funcionamiento del equipo, a menudo crean las condiciones perfectas para la corrosión.
Otro factor crítico es la calidad y el tipo de aislamiento. Como se señaló anteriormente, los materiales aislantes varían en gran medida, y su eficacia y su propensión a retener agua pueden contribuir a la CUI. Por ejemplo, los aislamientos porosos (hidrófilos) o las celdas cerradas (hidrófobos) contribuyen a la CUI de diferentes maneras.
Las propiedades de los materiales de los equipos aislados, en particular, la resistencia a la corrosión, desempeñan un papel clave en la CUI. Los aceros al carbono y de baja aleación son propensos a oxidarse cuando se exponen a la humedad, un proceso que se agrava con temperaturas altas.
Además, las prácticas operativas son un factor determinante. Por ejemplo, los equipos que alternan con frecuencia entre temperaturas altas y bajas, pueden generar condensación dentro del aislamiento, lo que crea una condición ideal para la corrosión. La manera en que se lleva a cabo el mantenimiento también incide de manera significativa en la aparición de la CUI. Si el aislamiento permanece dañado o si la intrusión de humedad no se soluciona con rapidez, el riesgo aumenta.
Comprender estas sofisticadas interacciones es esencial para formular estrategias efectivas que permitan prevenir y mitigar la CUI. Antes de discutir estas estrategias y su eficacia, analicemos de fondo un caso típico del fenómeno de la CUI: la construcción de tuberías con aislamiento térmico. Para asegurar el aislamiento y protegerlo de las condiciones climáticas externas, se coloca una cubierta metálica, a menudo denominada revestimiento, alrededor del aislamiento, que se mantiene en su lugar con bandas metálicas. Esta cubierta está diseñada para envolver el aislamiento y, como resultado, se crean juntas longitudinales o radiales.
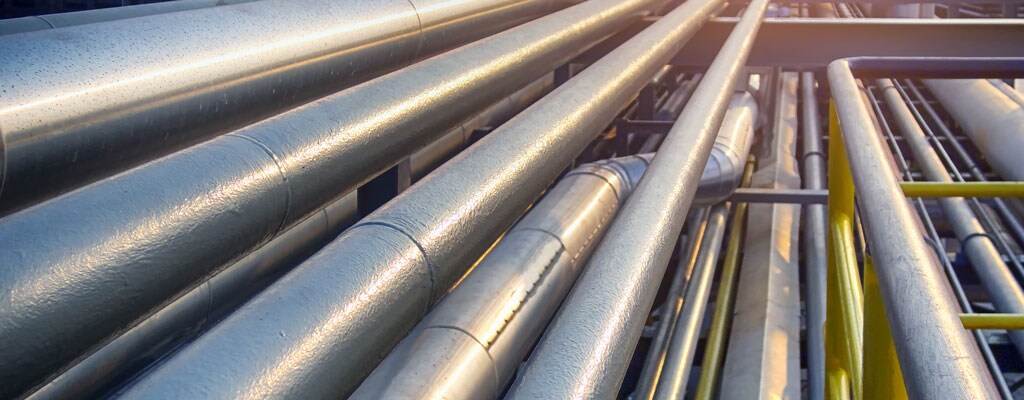
Tubería aislada con revestimiento metálico.
Si bien es una causa común, la lluvia no es la única fuente de agua que puede provocar una CUI. El agua también puede provenir de torres de enfriamiento, vapor y diferentes procesos que pueden ocasionar derrames de líquidos. La intrusión de agua puede ocurrir si el revestimiento está dañado, si los sellos están rotos o si actúan fuerzas externas, como impactos, caídas de objetos, el contacto con objetos afilados o personas que caminan sobre la tubería. Una vez que existe un punto de ingreso de agua, no siempre se percibe de inmediato, pero, en caso de lluvia, la intrusión de agua es inevitable.
La interacción entre el agua y el material aislante puede variar en función de la naturaleza del material. Como se mencionó anteriormente, si el material aislante es hidrófobo (una celda cerrada que no permite la absorción de agua), el agua fluirá y permanecerá entre el aislamiento y la tubería. Esta agua no siempre se evapora por completo y puede estancarse.
Por el contrario, si el material aislante es hidrófilo (capaz de absorber la humedad como una esponja), el agua creará una conducción térmica a través de la esponja y el impulso térmico irá desde la tubería al revestimiento, lo que dará lugar a un ciclo de evaporación y condensación que, a su vez, provocará un aumento de la concentración de sal en la piel de la tubería a medida que el agua se evapore. Esta sal, junto con otros componentes naturales de este tipo de material aislante, puede degradar la protección de las tuberías y producir corrosión y fisuras, conocidas como grietas por corrosión bajo tensión por cloruros (CSCC) debajo del aislamiento.
La presencia de contaminantes, principalmente cloruros y sulfatos, es común debajo del aislamiento. Estos pueden filtrarse desde los materiales aislantes o provenir de fuentes externas. Sus soluciones acuosas, que poseen una gran conductividad eléctrica, pueden facilitar el proceso de corrosión.
La temperatura también juega un papel crucial. En mayor parte, se acepta (o diferentes fuentes lo indican) que el acero al carbono que funciona dentro del rango de temperatura de -4 °C (25 °F) a 149 °C (300 °F) tiene el mayor riesgo de CUI. Los equipos que funcionan de manera continua por debajo de los -4 °C (25 °F) tienden a permanecer libres de corrosión. Los equipos que funcionan bajo temperaturas mayores a los 149 °C (300 °F), que superan el punto de ebullición del agua, experimentan una corrosión baja ya que la superficie del acero al carbono se mantiene seca.
Comprender la interacción entre los materiales aislantes, la entrada de agua, los contaminantes y las variaciones de temperatura es fundamental para entender cómo se origina la CUI. Sin embargo, este conocimiento no es suficiente si no se tienen en cuenta las posibles consecuencias de no mitigar este problema. Las ramificaciones van más allá de la corrosión en sí y afectan no solo al aspecto financiero de la industria del petróleo y gas, sino también a los relacionados con la salud, la seguridad y el medio ambiente.
Los efectos de la CUI se asemejan a las de la corrosión en general. La corrosión puede producir grietas que, con el tiempo, pueden provocar fracturas y fugas de productos petrolíferos en las tuberías. Esto no solo representa una amenaza grave para el medio ambiente debido a la posible contaminación, sino que también genera riesgos de salud para quienes viven cerca del lugar de la fuga. Además, el riesgo de incendios y explosiones agrava una situación que ya de por sí es crítica.
Estos daños no solo son peligrosos, sino también costosos. La reparación puede representar tanto una carga financiera, en términos de gastos de capital y operativos (CAPEX y OPEX), como una situación peligrosa para los técnicos que la realizan. En las siguientes secciones, exploraremos las estrategias para prevenir y mitigar la CUI a fin de controlar estos riesgos de manera efectiva.
Descubrir la CUI es todo un reto puesto que se encuentra debajo del aislamiento y a menudo sale a la luz cuando ya es demasiado tarde. Los métodos tradicionales para detectar la CUI van desde técnicas sencillas a avanzadas, y todas están destinadas a descubrir la corrosión antes de que cause daños serios.
El método más frecuente y directo para inspeccionar la CUI consiste en cortar partes del aislamiento para llevar a cabo pruebas no destructivas o inspecciones visuales.
Los siguientes métodos, con sus respectivas ventajas y desventajas, se suelen emplear para detectar la CUI:
- Inspección visual: el primer método, y el más sencillo, consiste en retirar el aislamiento, verificar el estado de la superficie de la tubería y volver a colocar el aislamiento. Los estudios indican que la mayoría de las veces no se encuentra CUI después de retirar el aislamiento. Otros retos pueden ser el riesgo asociado a la manipulación del aislamiento en presencia de amianto o el impacto del aislamiento térmico si la tubería está en funcionamiento.
- Inspección sin retirar el aislamiento: esta técnica reduce de manera considerable el costo de las inspecciones, ya que no es necesario retirar y volver a colocar el aislamiento. Por lo general, este método utiliza las pruebas no destructivas (NDE).
- Pruebas no destructivas (NDE): las NDE abarcan varias técnicas de inspección no invasivas que se utilizan para evaluar las propiedades de los materiales, de los componentes o de la totalidad de los componentes del proceso. La corriente de Foucault pulsada (PEC) y la radiografía digital son dos de los métodos que se emplean para realizar inspecciones de CUI. Por lo general, ningún método se utiliza de manera aislada, sino en conjunto para obtener resultados óptimos.
- Corriente de Foucault pulsada (PEC): los equipos de PEC funcionan por electromagnetismo y determinan de manera efectiva el espesor promedio de la pared de la tubería a través del aislamiento. Esto hace posible la detectar y localizar la CUI. La principal ventaja de la PEC es que determina la reducción del espesor general de las paredes de los objetos aislados sin retirar el aislamiento ni procesar la superficie del objeto.
- Ondas guiadas (GW): es una tecnología alternativa para evaluar la CUI en tuberías largas. Utiliza ondas ultrasónicas guiadas de baja frecuencia que se propagan a lo largo de la tubería. Puede detectar la corrosión tanto interna como externa, pero el sensor de onda guiada debe estar en contacto directo con la tubería, por lo que es necesario retirar parte del aislamiento para instalar el sensor.
- Radiografía digital en tiempo real: los rayos X se descargan en un lado de la tubería aislada, atraviesan la tubería, el revestimiento y el aislamiento, y un sensor los recibe en el lado opuesto. Los rayos que recibe el sensor se convierten en imágenes en tiempo real y ponen de manifiesto anomalías, como la corrosión interna o externa o los defectos en la tubería. Con este método no se retira el revestimiento y proporciona información en tiempo real.
- Termografía: se utiliza en la industria petroquímica. Proporciona una imagen térmica de un objeto y detecta pérdidas de energía que, por ejemplo, pueden ser el resultado de defectos de aislamiento, entrada de agua o fugas de gases o líquidos que afectan la temperatura de la tubería aislada.
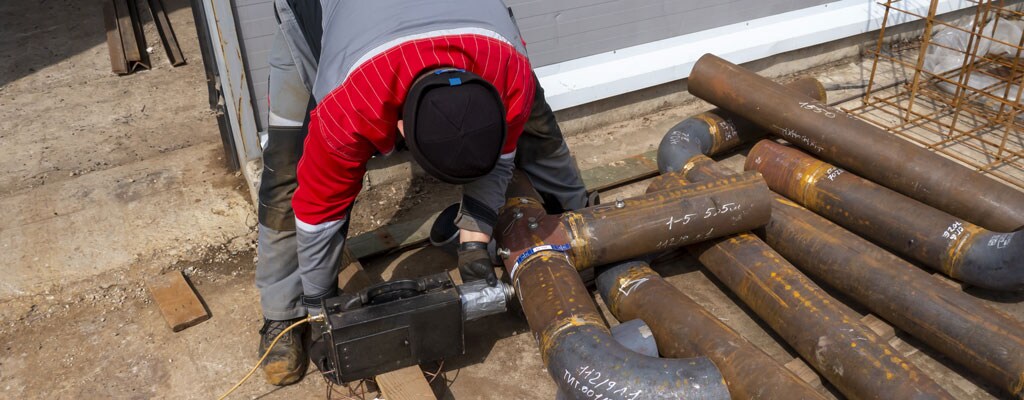
Un especialista instala un aparato de rayos X para realizar pruebas no destructivas en las uniones soldadas.
Si bien cada uno de los métodos descritos tiene puntos fuertes, todos comparten limitaciones inherentes que pueden hacerlos poco efectivos para detectar la CUI. Las inspecciones visuales, si bien son sencillas, solo ponen de manifiesto las condiciones de la superficie, con la posibilidad de pasar por alto la corrosión que yace más profundo. Además, retirar y volver a colocar el aislamiento durante estas inspecciones agrega costos sustanciales y retos logísticos, como el manejo del asbesto (Texas Nondestructive Testing Academy & Level III Services, s. f.)
Los métodos de NDE, que evaluan las propiedades de los materiales sin dañar el aislamiento, están limitados por su propia naturaleza. Por ejemplo, los sistemas PEC brindan información valiosa sobre la reducción del espesor de las paredes, pero es posible que no detecten con precisión la corrosión en una zona específica o las picaduras pequeñas (Texas Nondestructive Testing Academy & Level III Services, s. f.)
La tecnología de ondas guiadas requiere retirar el aislamiento en puntos específicos, por lo que es posible que no se detecte la corrosión en otros lugares. Además, factores como los recubrimientos de alta pérdida o los reflejos de señal provenientes de elementos como soldaduras y abrazaderas pueden afectar la atenuación de la señal, lo que limita la longitud de las tuberías que se puede inspeccionar (Chukwuemeka et al., 2021).
La radiografía digital en tiempo real proporciona imágenes de posibles anomalías debajo del aislamiento, pero puede carecer de la sensibilidad para detectar la corrosión desde su etapa inicial. Además, solo se utiliza en la densidad de los materiales y es posible que en ciertos de ellos no se detecte la corrosión de manera efectiva (Nanan, 2020).
La termografía y las pruebas visuales, si bien son efectivas para identificar posibles riesgos de CUI debidos a daños en la impermeabilización o el revestimiento, solo realizan un análisis superficial y pueden pasar por alto la corrosión oculta a mayor profundidad debajo del aislamiento (Fujifilm, 2022).
En esencia, el principal reto consiste en que estos métodos no proporcionar una evaluación completa y exhaustiva de la corrosión oculta, sobre todo cuando se encuentra en una zona específica o en sus etapas iniciales. Con las limitaciones de cada método existe la posibilidad de que considerables áreas no se revisen, lo que podría pasar por alto la CUI que crece debajo el aislamiento.
Sensores para la detección de la CUI
A partir de la transformación digital de la industria, la rápida proliferación de dispositivos de Internet de las cosas (IoT) y de sistemas conectados sentó las bases para desarrollar tecnologías innovadoras para detectar CUI, en particular, a través de sensores inalámbricos que se alimentan con baterías. En gran medida, la aceleración de esta revolución tecnológica se da cuando surgen los sensores inalámbricos que se alimentan por baterías, que aprovechan los avances de la electrónica de baja potencia, y se introducen los protocolos de comunicación inalámbrica que son aptos para baterías, como LoRaWAN, NB‑IoT, LTE M y Bluetooth.
Se están evaluando varios principios de detección, como los sensores de humedad y de temperatura entre la tubería y el revestimiento exterior, o dentro o alrededor del material aislante, por ejemplo, la fibra óptica o el radar guiado electromagnético (EMGR). Sin embargo, existen algunos retos, como las dificultades asociadas al reacondicionamiento con fibra óptica de las infraestructuras existentes o la integración de alambres (cables) de sacrificio en el aislamiento.
Estos cables de sacrificio se utilizan junto con el EMGR, en el que el cable se corroe como indicador previo de la CUI, a la vez que un cable no corrosivo transmite señales a un módulo inalámbrico que está fuera del revestimiento. Esta incorporación hace posible una conexión óptima entre los métodos de detección innovadores y las limitaciones prácticas de su implementación, lo que refleja las complejidades inherentes a la fusión de las nuevas tecnologías con las infraestructuras existentes.
TE Connectivity se destaca por superar estos retos gracias a su experiencia única en sensores, en particular, por su tecnología central de detección capacitiva de humedad relativa y sus transmisores inalámbricos. Estos sensores, que se colocan de manera estratégica en tuberías aisladas, hacen posible realizar un mapeo efectivo de infraestructuras enteras. Pueden detectar la entrada de agua y, mediante análisis inteligentes, simplifican la identificación de las áreas que requieren una evaluación más exhaustiva de la CUI por medio de pruebas no destructivas (NDE). En la sección de casos prácticos se analiza con más detalle cómo se aplica esta tecnología en la vida real.
Los esfuerzos de colaboración en la industria ofrecen vías para mejorar el monitoreo en tiempo real. Sin embargo, estas soluciones son más eficientes cuando se combinan con las avanzadas tecnologías de los sensores de TE Connectivity.
A menudo, el enfoque tradicional requiere inspecciones costosas que consumen muchos recursos. No obstante, con los sensores de TE Connectivity este proceso se hace más eficiente y utiliza menos recursos, lo que ahorra tiempo y dinero. En más del 90 % de las inspecciones visuales, que se realizan después de retirar el revestimiento, no se detecta corrosión. De esta manera, las inspecciones que se llevan a cabo con nuestra tecnología avanzada de sensores conllevan un importante ahorro de costos.
Las empresas podrían tener sus propias estrategias para realizar inspecciones basadas en riesgos. Es probable que en las instalaciones eléctricas críticas se continúen utilizando los métodos de mantenimiento periódico y de NDE, pero, en el caso de instalaciones menos críticas, se podrían reducir sustancialmente los costos de mantenimiento si se les equipa con
los sensores inalámbricos y remotos de TE Connectivity.
El objetivo sigue siendo diseñar y ofrecer un sensor robusto, preciso, rentable y duradero que sea capaz de monitorear todas las tuberías y las superficies con aislamiento en las refinerías. Los sensores de TE Connectivity, que ya cumplen con estos criterios, también cuentan con la certificación ATEX FCE, lo que garantiza su funcionamiento en entornos potencialmente peligrosos.
Avances en la tecnología de sensores y sus ventajas
Con tecnologías como LoRaWAN, los sensores transmiten información desde distancias que van de unos pocos metros a varios kilómetros. Al trabajar en conjunto con puertas de enlace, análisis avanzados, estrategias de manejo con enfoque en la CUI y conocimientos especializados sobre corrosión, los operarios y las empresas de mantenimiento pueden detectar la corrosión de forma proactiva. Esto hace posible intervenir de manera rápida y específica para reparar áreas en las que se produce corrosión, con lo que se ahorra tiempo y dinero, a la vez que se mejora la seguridad y la durabilidad de la infraestructura.
La integración de estos sistemas ofrece grandes ventajas para el manejo proactivo de la CUI. En los últimos años, se han llevado a cabo numerosas simulaciones y experimentos en laboratorio con sensores de humedad en los que se han obtenido resultados prometedores, lo que demuestra que medir la humedad y la temperatura podría ser efectivo para detectar la CUI antes de que ocurra. Estos avances no serían posibles sin nuestra tecnología de sensores, de la que estamos muy orgullosos. Sin embargo, dichos avances no se limitan al laboratorio, sino que se aplican de manera práctica mediante instancias de colaboración estratégicas y sólidas, como veremos más adelante.
Caso práctico de KAEFER
Estamos conscientes de los graves temas de preocupación de la industria
En los últimos años, KAEFER Group, líder en soluciones de servicios integradas e industriales, ha entrevistado a una amplia gama de empresas de gas y petróleo en todo el mundo. De allí surgió un punto en común: todas mencionaron que la CUI es una de sus prioridades principales. El tema de preocupación no era solo técnico, sino que tenía consecuencias de largo alcance, como las que se trataron con anterioridad en este informe. Fue en este contexto que empezó nuestra colaboración con KAEFER para abordar estas necesidades urgentes.
Soluciones integrales con KIT
Blu Empowered by KAEFER presentó KIT (KAEFER Integrity Technology) como un servicio integral para el manejo de la CUI. KIT pone de manifiesto la experiencia de KAEFER en el manejo eficaz de proyectos de CUI de diferentes magnitudes Desde la compleja optimización de la colocación e instalación de los sensores hasta la configuración del sistema, KIT es un paquete completo. Pero lo que aumenta su capacidad es la tecnología de sensores de TE Connectivity.
La sinergia entre los servicios integrados de KAEFER y las avanzadas soluciones de detección de TE Connectivity son la base de esta innovadora colaboración. La tecnología de los sensores inalámbricos de TE Connectivity, que integra una batería de larga duración y tolera entornos difíciles, es un importante avance en la detección de la CUI. Certificados de acuerdo con los más altos estándares de seguridad, estos sensores inalámbricos hacen posible la comunicación a grandes distancias mediante protocolos avanzados como LoRaWAN y están equipados con la tecnología de Bluetooth de bajo consumo de energía para una configuración versátil.
Además, la incorporación de tiempos de medición personalizables y el manejo inteligente de eventos de umbral son un ejemplo del enfoque vanguardista de esta colaboración y mejoran la confiabilidad y la precisión de los datos a la vez que optimizan la duración de la batería. Con los sensores que adaptan la medición y transmisión de forma autónoma con base en límites configurados y las notificaciones automáticas para el manejo de la batería, se logra una gran eficiencia.
Los elementos de detección de esta tecnología se diseñan con mucho cuidado y, a menudo, hacen uso de las tecnologías ASIC (circuitos integrados para aplicaciones específicas) y los sensores de humedad MEMS (sistemas microelectromecánicos), que se utilizan de manera considerable en la industria automotriz, la de maquinaria de obra y la de camiones. Cabe destacar que esta aplicación interindustrial subraya el potencial de ampliar la capacidad a gran escala a sectores como el del petróleo y gas, y a la vez lograr los niveles de calidad que exigen las industrias como la automotriz y ser el pilar para la adquisición efectiva de datos y el monitoreo en tiempo real.
La técnica sofisticada de KIT
El sistema de monitoreo de la CUI de KIT es totalmente digital. Si bien es cierto que se requiere una inspección tradicional de las áreas problemáticas identificadas, existe la posibilidad de que las actividades de campo se automaticen, lo que reducirá la intervención humana y, por tanto, mitigará los riesgos. Además, el sistema está en continuo desarrollo y se espera que incluya servicio de asesoría e, incluso, instalación robótica y autónoma mediante la tecnología de sensores inalámbricos de batería de TE Connectivity.
Para visualizar la información, KIT cuenta con opciones como tableros modernos o gemelos digitales. Estas se enriquecen aún más con análisis sofisticados que ayudan a predecir la CUI y recomiendan acciones de mantenimiento.
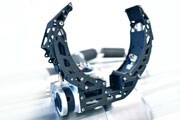
MonkeyBot para instalación robótica de sensores
Integrar la tecnología de sensores de TE Connectivity en KIT da como resultado una tecnología sofisticada y ventajas concretas. Los casos prácticos demuestran que se logran ahorros considerables en los costos de mantenimiento y mejoras en la integridad de la planta. En última instancia, todo esto constituye un mayor valor para el cliente, algo que tanto KAEFER como TE Connectivity se esfuerzan por lograr.
Conclusión
Al hacer frente al reto generalizado de la CUI, un dilema que tiene ramificaciones considerables en la eficiencia operativa, la seguridad del medio ambiente y el bienestar de la comunidad, no se puede subestimar el papel que juegan las tecnologías avanzadas. En este informe técnico se ilustraron las enormes repercusiones de la corrosión en el sector del gas y petróleo, que afectan no solo a los resultados financieros, es decir, los gastos de capital y operativos (CAPEX y OPEX), sino también a los factores de salud, seguridad y medio ambiente (HSE).
Con nuestra colaboración con KAEFER como trasfondo, se reconoce la urgente necesidad en la industria de contar con soluciones sólidas para la CUI. KIT, de KAEFER, integra la tecnología innovadora de los sensores de TE Connectivity y cuenta con un servicio completo para la CUI. Este trabajo en colaboración ejemplifica un enfoque interdisciplinario para resolver problemas y une diversas experiencias en un ecosistema que está comprometido con superar los complejos retos de la detección y el manejo de la CUI. La implementación a gran escala de nuestros sensores inalámbricos de batería no es un simple logro tecnológico, sino un impacto transformador en la industria. La posibilidad de reducir tanto el mantenimiento periódico como las inspecciones visuales innecesarias mejora la seguridad y ahorra dinero de manera considerable.
La digitalización en las instalaciones, como el desarrollo de gemelos digitales, hace posible avanzar en precisión y predictibilidad. Nuestros sensores, que cuentan con el respaldo de sólidas herramientas de análisis, se alinean con los sistemas y los estándares actuales, lo que refleja nuestro compromiso de estar a la vanguardia en los avances en la detección y prevención de la CUI. Asimismo, pone de relieve nuestro compromiso con la evolución continua de la tecnología de sensores y con las instancias de colaboración en la industria que hacen posible estos avances.
De cara al futuro, el objetivo de TE Connectivity sigue siendo claro: ser pioneros en soluciones más seguras y sostenibles con el uso de tecnologías de vanguardia. Con las herramientas para visualizar la información, que utilizan nuestros sensores inalámbricos inteligentes, se obtiene una visión completa de las condiciones de las instalaciones, lo que hace posible pasar de un mantenimiento generalizado que se basa en riesgos a un método más puntual que se basa en información.

Los sensores inalámbricos de TE Connectivity en la actualidad se utilizan en aplicaciones de monitoreo de condiciones que hacen posible el mantenimiento predictivo de activos rotativos y de las bocas de pozos de petróleo y gas.
Se dispone de una plataforma inteligente y completa que incluye sensores de vibración piezoeléctricos simples y triaxiales con un rango de frecuencia de hasta 15 KHz (FFT y procesamiento de señales integrados); sensores de temperatura que se pueden colocar en tuberías y son capaces de tolerar temperaturas externas de hasta 260 °C, y sensores de presión que pueden medir la presión absoluta o relativa.
Estos sensores inteligentes se pueden configurar por completo con TE Sensor Toolbox o con la aplicación TE SensorConnect (en un teléfono inteligente) que se encuentra disponible en la App Store de Apple o en la Play Store de Google. Al avanzar hacia el futuro, confiamos en que nuestro liderazgo en soluciones de monitoreo de la CUI está a la vanguardia de la transformación de la industria y representa un nuevo paradigma de eficiencia y seguridad.
Al combinar la tecnología avanzada con una experiencia sólida y las instancias de colaboración, no solo hacemos frente a los retos de la actualidad, sino que damos forma a las soluciones del futuro.
