Los sensores mejoran nuestra capacidad de observar e informar sobre el mundo que nos rodea. Lo que ve un sensor puede ser la diferencia entre lo que se imagina y lo que es posible.
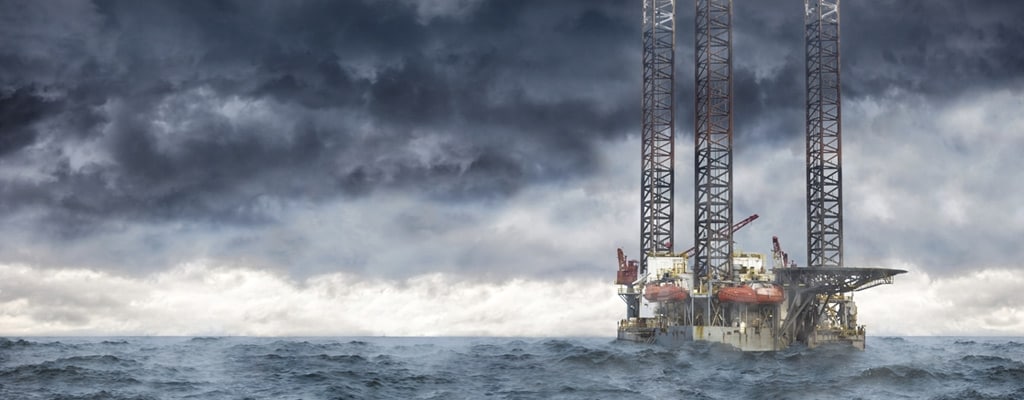
Informe técnico
Confiabilidad extrema
La construcción de transmisores que funcionan cuando las temperaturas son extremas comienza con el desarrollo de un sensor diseñado para soportar los entornos más hostiles.
El entorno operativo juega un papel importante en el funcionamiento continuo y la precisión de los transmisores de presión. Si no se especifica adecuadamente para manejar condiciones ambientales como lugares subárticos y líquidos congelados, los transmisores de presión pueden fallar prematuramente y causar fallas catastróficas en el equipo. Si bien las hojas de especificaciones del transmisor de presión proporcionan información sobre el rendimiento del sensor en condiciones ambientales, las lecturas esperadas en un rango de temperatura determinado, así como varios términos y acrónimos que aclaran cómo funcionará el transmisor de presión en diferentes condiciones, una comprensión más profunda de la construcción del transmisor ayudará a definir cómo funcionará el sensor en entornos extremos, particularmente en temperaturas frías.
Descubre nuestro transductor de presión hidráulica M9100, que mide las presiones de fluidos de hasta 700 bar en condiciones extremas.
Los transmisores de presión suelen utilizar algún tipo de galgas extensométricas montadas en un diafragma para medir la presión. Estos medidores se pueden aplicar con pegamento, deposición de película delgada, encapsulados en aceite o montados a través de un proceso de cocción de vidrio. A medida que el diafragma se desvía, los valores de resistencia cambian. En todos los casos, los efectos de la temperatura también pueden cambiar la resistencia de esta señal de salida, lo que causa errores en el sensor.
La capacidad de supervivencia del sensor se puede probar en climas fríos. Las temperaturas inferiores a -20 °C (-4 °F) pueden hacer que los sensores llenos de aceite se gelifiquen y se endurezcan. Con la tecnología cerámica, la junta tórica entre el puerto mecanizado y el diafragma puede endurecerse y volverse quebradiza. Esto compromete la integridad del elemento de detección y crea una posible ruta de fuga. Para evitar que el sensor alcance por debajo de su rango de temperatura de funcionamiento, su ubicación y entorno deben modificarse. Las cajas o habitaciones calentadas se pueden usar para proteger el sensor, así como para evitar que la temperatura en el sensor alcance temperaturas de congelación. En ubicaciones remotas, la energía puede no estar fácilmente disponible para la instrumentación que opera desde la energía solar. Por lo tanto, la capacidad de calentar el sensor es limitada o no está disponible. Por ejemplo, los equipos de pozos en Alaska, Alberta, Columbia Británica, Saskatchewan y Dakota del Norte pueden experimentar temperaturas tan frías como -50 °C (-60 °F) donde los sensores se instalan al aire libre directamente en las tuberías para monitorear la presión hidráulica, de la carcasa y de los tubos desde el cabezal del pozo.
Operación de impactos de congelación
La congelación de los medios de proceso es un resultado indirecto de los climas fríos. En ciertas aplicaciones de perforación de gas natural, el agua se puede encontrar en las mismas tuberías que el gas. Cuando el sistema se apaga y la temperatura cae por debajo del punto de congelación, el agua dentro de la tubería puede congelarse y expandirse, lo que causa una sobrecarga en el sensor de presión durante un período prolongado de tiempo. La expansión puede reflejar un pico de presión de 500 PSI (35 bar) a 1.000 PSI (70 bar) de presión. Para un sistema de 100 PSI, la presión puede aumentar a 1500 PSI (100 bar). Para muchas tecnologías de sensores, esta tensión en un diafragma de presión más baja causará una falla del medidor de tensión o la ruptura del diafragma. Para proteger contra la falla del sensor, el aumento de presión debe estar sostenido por el elemento de detección durante un período de tiempo sin afectar la precisión del sensor después de la descongelación. El diseño especial de la cavidad, así como la capacidad de presión de prueba especial y la calibración son las mejores maneras de garantizar que el sensor no fallará por la congelación de los medios en la cavidad.
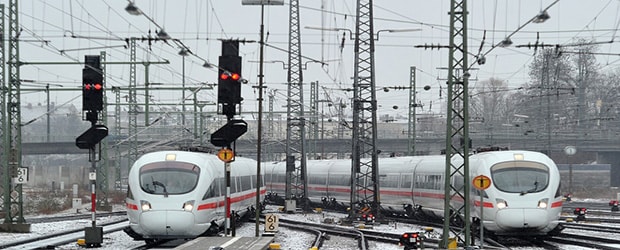
Compensación de la temperatura
Con el fin de compensar los cambios de temperatura eléctricamente, el transmisor de presión fabrica sensores de prueba sobre la presión y la temperatura para ajustar los efectos de la temperatura. Debido a que cada sensor y galga extensométrica son únicos, la mejor práctica consiste en probar cada sensor individual por sus propiedades específicas. El método tradicional es recortar o reducir la señal de salida en bruto mediante resistencias para optimizar el rendimiento en el rango de temperatura probado. El sensor, entonces, usaría un conjunto de placa de circuito que amplifica la señal de milivoltios a la señal de salida requerida (p. ej. 4-20mA). Ciertos transmisores de presión ofrecerán la opción de ajustar el cero y el intervalo. Esta función es comúnmente necesaria para las señales de salida a la deriva después de la fatiga del diafragma. A medida que el costo y el tamaño de la electrónica digital han disminuido, ha habido un aumento en el uso de la compensación digital a través del uso de un ASIC (Circuito integrado de aplicación específica). En casos de baja temperatura, el ASIC se programa a medida que el sensor de presión se prueba sobre la temperatura, con algunos diseños que corrigen la no linealidad o las desviaciones de la señal de salida ideal. La temperatura del ASIC se puede compensar en los medidores con un sensor de temperatura como un termistor o en el propio ASIC. La principal diferencia es la temperatura del medio. Si se compensa en función de la temperatura ASIC, la lectura de la temperatura no es tan precisa debido a su proximidad al medio. En climas fríos, el ASIC podría estar leyendo cerca de la temperatura ambiente, mientras que el medio podría ser un líquido o gas caliente. La medición de la temperatura de los medidores produce la respuesta más rápida y la compensación dinámica, lo que optimiza el rendimiento.
Otro avance de fabricación relacionado con los transmisores de presión es la capacidad de ofrecer una señal de salida de temperatura independiente. Los integradores de sistemas ahora pueden monitorear de cerca los cambios en la temperatura del medio desde un solo dispositivo, lo que reduce el costo de instalación y el costo del sensor adicional. En la imagen de la izquierda, observarás un elemento de detección de acero inoxidable de una sola pieza que está mecanizado para que no haya soldaduras ni juntas tóricas internas. Dado que no hay soldaduras o juntas en este diseño, el valor de fatiga es mucho menor en una temperatura de funcionamiento amplia. Construidos con diafragmas muy gruesos y galgas extensométricas de silicio de última generación, estos transmisores de presión a prueba de explosiones ofrecen resultados repetibles incluso en los entornos hostiles de perforación de pozos profundos, como se muestra en la imagen de la derecha. La adición de Alloy 718, 17-4 PH, Alloy C-276 y 316 L SS wetted parts, extiende aún más el uso de estos transmisores de presión en el procesamiento de petróleo pesado y alta sulfuración.
RESUMEN
Al igual que con el diseño de todo el sistema, comprender los detalles permitirá una mejor toma de decisiones. Si bien los transmisores de presión se ven similares en su empaque y tamaño, la forma en que se mide la presión desde un punto de apoyo mecánico y eléctrico puede ser extremadamente diferente. Los materiales que se utilizan también pueden variar, por lo que requieren un análisis más detallado. Trabaje con su fabricante de transmisores de presión para encontrar un diseño adecuado a sus necesidades.