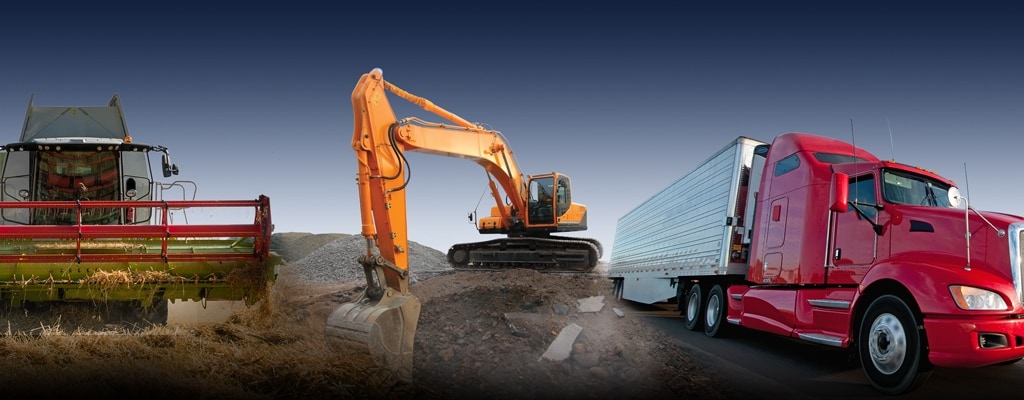
Tendencia
Datos a alta velocidad en entornos hostiles
Para una transmisión de datos a alta velocidad en vehículos comerciales, los diseñadores deben considerar cuidadosamente los componentes, su ubicación y el impacto de las condiciones ambientales en la etapa inicial de diseño. Lee nuestro informe para obtener más información.
AUTOR
Christian Manko, gerente de productos de conectividad de datos, TE Connectivity
Avances tecnológicos
Los clientes exigen una funcionalidad que automatice o mejore las tareas operativas para aumentar la productividad y la seguridad del conductor. y, en muchos casos, también reduce el costo total de propiedad. Características como el frenado y la dirección adaptativos automáticos, el diagnóstico a bordo, la comunicación de vehículo a vehículo (V2V) y de vehículo a infraestructura (V2I), y las cámaras que brindan al conductor una visión de 360º de su entorno se están convirtiendo en requisitos básicos del cliente.
Estas características requieren la transmisión de grandes cantidades de datos a altas velocidades. A medida que los ingenieros diseñan nuevos modelos para satisfacer las exigencias de los clientes, el desafío es garantizar la integridad de la señal y la transmisión de datos en el difícil entorno de las industrias de camiones y vehículos todoterreno.
Aplicación de Ethernet en una arquitectura mixta
Para gestionar el aumento de las demandas de datos y la conectividad a alta velocidad, se necesita una infraestructura de red sofisticada. Las arquitecturas de bus CAN, que normalmente gestionan velocidades de hasta 500 Kbps, han sido la columna vertebral incondicional de la mayoría de las redes de comunicación de vehículos de alto rendimiento durante algunas décadas. Sin embargo, el ancho de banda de datos requerido para una funcionalidad avanzada del vehículo y las funciones automatizadas para brindar seguridad y productividad es demasiado grande como para que solo la CAN lo proporcione.
El protocolo Ethernet de un solo par (100BASE-T1 a 100 Mb/s o 1000BASE-T1 a 1 Gb/s) proporciona la capacidad de transmitir datos a altas velocidades. El uso de redes y conectores Ethernet permite a los diseñadores del OEM integrar sin problemas más dispositivos en la red y acelerar la conectividad de datos en sus vehículos. Sin embargo, como topología de punto a punto, Ethernet cambia la arquitectura eléctrica y electrónica (E/E) del vehículo. A medida que los OEM decidan agregar más funciones y dispositivos, los diseñadores también deberán tener en cuenta los conmutadores Ethernet para dirigir la señal y las puertas de enlace para establecer una comunicación entre Ethernet y CAN.
Para optimizar el espacio, el peso y el rendimiento en condiciones difíciles, los diseñadores deben considerar en las primeras etapas de diseño cómo integrarán Ethernet donde sea necesario para ofrecer funcionalidades avanzadas. Deben tomarse decisiones como la cantidad de cables que se deben colocar dentro del vehículo y dónde colocarlos, dónde colocar los conmutadores Ethernet y si este debe estar en una unidad de control electrónico (ECU) existente o en una nueva ECU dedicada en cada característica que requiera Ethernet. Esto es crucial para evitar o mitigar problemas con interferencias electromagnéticas (EMI) u otras interrupciones mecánicas.
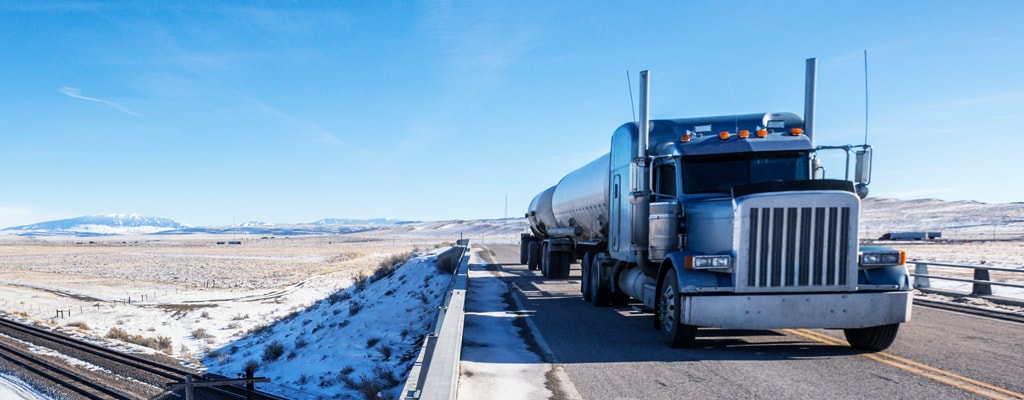
Por ejemplo, Las cámaras de 360º en un vehículo de alto rendimiento transmiten datos a alta velocidad desde el exterior del vehículo a la pantalla en la cabina para que el conductor los vea. Hay cuatro cámaras (una de cada lado del vehículo) que envían señales a una ECU. Los diseñadores deben planificar dónde colocar un interruptor para combinar los datos de las cuatro cámaras y enviar esos datos en una señal a la ECU. El interruptor puede estar en el vehículo o en una de las cámaras, que tendría cuatro puertos para ingresar datos de las otras tres cámaras y luego enviarlos. Otra opción es integrar el interruptor en el monitor de visualización de video.
Con funciones automatizadas activas, como el frenado adaptativo automático y otros sistemas avanzados de asistencia al conductor (ADAS) que incluyen una matriz de varios sensores, aún más, se deben evaluar más aspectos al principio además del diseño. Cada sensor tendrá un enlace de comunicación dedicado a una ECU. Cuantos más sensores tenga el vehículo, más cables y enlaces de comunicación se necesitan. Un vehículo de alto rendimiento autónomo del futuro necesitaría una amplia gama de sensores para aproximadamente 16 radares, 10 lidares y 10 cámaras alrededor del vehículo. Eso significa más de 30 cables y enlaces que deben ser resistentes a EMI y que se deben enrutar de manera inteligente teniendo en cuenta el espacio, el peso y la EMI para mantener la integridad de la señal dentro y fuera del chasis y a medida que los enlaces entran en una ECU. Más datos significan más necesidades de ancho de banda, y eso significa conectores y cables que también pueden gestionar más velocidad.
El inmenso tamaño de los vehículos industriales y comerciales presenta un desafío para mantener la integridad de la señal y transmitir datos de manera confiable. Para transmitir una señal Ethernet en automóviles, el estándar Ethernet especifica requisitos técnicos de hasta 15 m (49 ft). Pero en camiones, autobuses y vehículos todo terreno, debe mantenerse la integridad de la señal durante longitudes más largas, de hasta 40 m (131 ft), mientras soporta fuertes vibraciones, temperaturas extremas e impactos, grandes cantidades de polvo, entre otros.
El estándar Ethernet actualmente especifica hasta cuatro conexiones en línea a lo largo de esos 40 metros; los diseñadores deben evaluar cuánto tiempo puede durar cada segmento para mantener una integridad óptima de la señal. Los factores que afectan esto podrían estar expuestos a elementos externos o a altas temperaturas, colocación cerca de una antena u otro componente que podría causar EMI. El enrutamiento es un elemento clave del diseño y toda la capa física debe escalarse para lograr el rendimiento esperado.
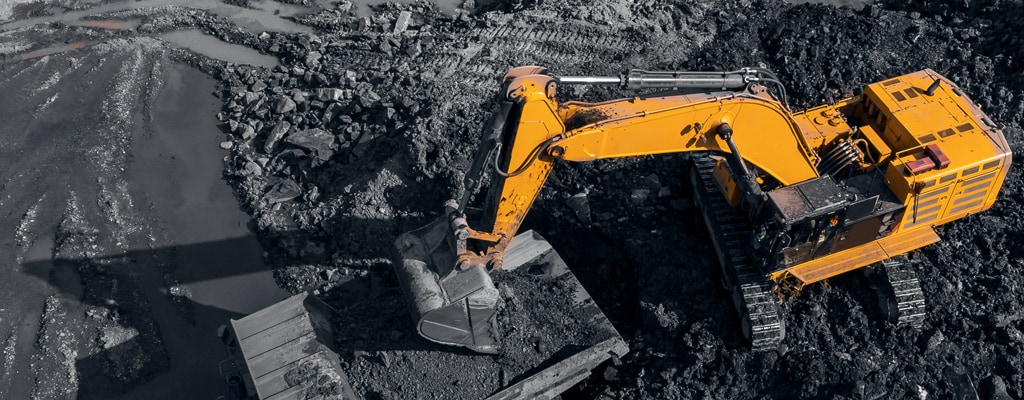
Compra nuestras soluciones para vehículos conectados de alto rendimiento
Elegir los componentes adecuados
“Al diseñar una arquitectura mixta con CAN y Ethernet, los ingenieros deben pensar en toda la infraestructura de conectividad de antemano en términos de qué funciones avanzadas y con mucha carga de datos incorporarán”. explica Abbas Alwishah, gerente de ingeniería de conectividad de datos de TE Connectivity. “Cuanto más avanzada sea la tecnología, más importante será la colaboración entre los OEM y los proveedores. Si un cliente me dice que necesita una cámara de alta definición o un sistema de detección de proximidad que funcione con una latencia muy baja, puedo explicarle todos los componentes individuales necesarios para esa función o sistema (sensores, conectores, conjuntos de cables, antenas, procesadores, pantallas, etc.) y hacer recomendaciones sobre la topología para optimizar el rendimiento, el espacio, el peso y los costos”.
Elegir componentes compatibles con Ethernet que puedan soportar condiciones adversas es clave para una transmisión de datos confiable en vehículos de alto rendimiento de larga duración. Se pueden usar los conectores Ethernet automotrices (aquellos diseñados originalmente para vehículos de pasajeros) en la cabina o en otras áreas del vehículo que no estén expuestas a impactos extremos, temperaturas extremas u otras condiciones, donde no se necesitan conectores más resistentes ni cables de mayor longitud. Un cable de par trenzado sin blindaje de alta calidad es adecuado para Ethernet en la mayoría de las áreas del vehículo, y los cables de par trenzado blindados solo se utilizarán cuando sea necesario. Las elecciones del diseñador también ayudarán a controlar los costos y ahorrar espacio y peso.
Los conectores MATEnet modulares y escalables desarrollados por TE para Ethernet automotriz, por ejemplo, también se pueden usar en vehículos de alto rendimiento para aplicaciones que requieren volúmenes de datos de tamaño medio a grande y bajas latencias, como diagnósticos a bordo (tecnologías V2X), telemática, infoentretenimiento en el tablero, ADAS y mucho más. Los conectores pueden transmitir datos a 100 Mb/s a 1 Gb/s (de conformidad con IEEE 100BASE-T1/1000BASE-T1) y se pueden utilizar con cables de par trenzado sin blindaje o blindados.
Los componentes del chasis requieren algo más que resistencia. Deben ofrecer confiabilidad mecánica, capacidades de reparación, soportar temperaturas extremas y funcionar con eficiencia con canales más largos. Cuando las frecuencias son más altas, la calidad y el diseño de los cables y conectores pueden repercutir en el rendimiento del canal, lo cual repercute en el rendimiento del sistema y, en consecuencia, en el rendimiento de la aplicación. Especialmente para los componentes en el chasis, los ingenieros deben optar por cables y conectores específicamente diseñados para transmisiones de datos a altas velocidades en entornos hostiles.
“Cuando se intentan abordar las necesidades de resistencia mecánica, algunos ingenieros pueden pensar instintivamente en agregar una carcasa más grande y sólida, pero la incorporación de paredes más gruesas afecta negativamente el rendimiento del sistema eléctrico”, afirma Mark Brubaker, gerente de productos de conectividad de datos de TE. “Es importante observar lo que históricamente ha funcionado, pero también se debe comprender más esta nueva generación de necesidades eléctricas para la transmisión de datos a altas velocidades y probar el rendimiento de las conexiones en las frecuencias más altas involucradas”.
Desde el principio se deben considerar la elección del producto y su colocación cuando se diseñan funcionalidades avanzadas y automatizadas para las que se requiere una transmisión de datos a altas velocidades. Cuando se agrega Ethernet a arquitecturas de vehículos de alto rendimiento, los diseñadores deben considerar y planificar aspectos para las complejidades involucradas con antelación y en profundidad antes de equilibrar con éxito la confiabilidad y la resistencia mecánica con los requisitos eléctricos para datos a altas velocidades y canales más largos, además de las cuestiones de capacidad de mantenimiento.
Para obtener más información sobre nuestras soluciones para vehículos conectados
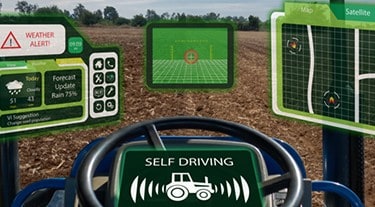
Conducción autónoma
Soluciones de Ethernet
Obtén más información sobre los requisitos de conectividad para promover una conducción autónoma de vehículos comerciales e industriales.
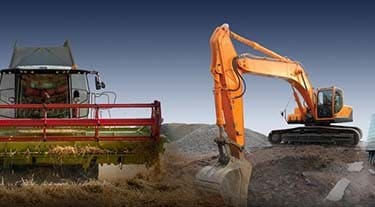
Conectividad de datos
Soluciones para vehículos de alto rendimiento
Descubre por qué los ingenieros de diseño deben considerar la incorporación de sistemas Ethernet en sus vehículos y maquinarias industriales y comerciales para satisfacer las necesidades de los futuros clientes.
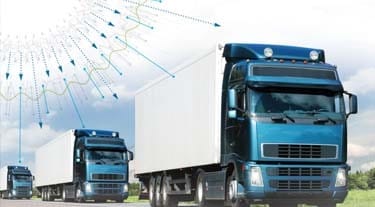
Conectividad de Ethernet
Requisitos para vehículos de alto rendimiento
Descubre las consideraciones que tenemos en cuenta para diseñar conectores Ethernet para vehículos de alto rendimiento.
Publicado originalmente en Truck & Off-Highway Engineering